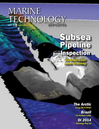
Subsea Processing Boosting and Gas Compression
Offshore drilling activity continues to migrate into deeper waters, especially with new oil and gas discoveries happening in smaller reservoirs located in deeper waters. Making these discoveries commercially viable relies on not only revenue from high oil and gas prices but also on reducing operating expenses (OPEX) and capital expenditures (CAPEX). Oil and gas producers are now looking at new technologies to produce effectively these high-pressure, complex reservoirs. Technologies such as subsea boosting and subsea gas compression allow subsea processing of hydrocarbons to change the economics of deepwater production.
Processing the hydrocarbons on the seabed has several advantages:
• Saving the multibillion dollar cost of building a new platform by providing tiebacks to shore or existing facilities
• Enhancing oil/gas recovery rates to increase the income per CAPEX dollar
• Enabling future access to reserves that are currently inaccessible due to hazards like icebergs and hurricanes
• Increasing operational safety and reducing risks
The deeper the well is, the more potential energy is required to reach the host platform at the surface. Subsea boosting increases the flowrate of the oil or gas to the surface by reducing the back pressure on the well, and therefore increases the recovery factor of the reservoir. For oil, pumping can be used, while natural gases are boosted by compression. Another technique, which can be used in combination with pumping, is to separate the water and oil/gas, injecting the water back into the reservoir to limit pressure drops in the well. This not only saves energy (of getting the water to the topside facility and down again into the well), it also saves a lot of space and weight on the heavily crowded topside facilities.
Moving processing from the platform or shorelines to the seabed creates challenges in the design and deployment of the processing equipment. A limiting factor is the weight of such equipment, especially in deep waters. Weight (and size) issues require that the equipment is designed in a modular fashion, with modules then connected together on the sea floor. For example, transformers, circuit breakers, variable-frequency drives, and the final consumers (pump or compressor) all need to be interconnected. Modularity also presents advantages in retrieving, repairing, or upgrading equipment because it is more economical to replace a module than the entire system. Where several trains of pumps or compressors are in parallel, modularity allows selective shutdown and retrieval of a module, while the other trains continue to boost hydrocarbon production, increasing the overall availability factor of the subsea station. This also eases maintenance by allowing smaller intervention vessels, which are more readily available than high payload deployment vessels and less costly to operate.
Wet-Mate Connectors Enable Modularity
A wet-mate connector is a device that allows connection of electrical conductors together. Connectors are designed for a certain current and voltage, frequency, and water depth. Their materials are corrosion resistant and designed to withstand the harsh conditions of subsea environments for their design life, typically up to 25 to 30 years.
For modularity to be achieved, power distribution must rely on wet-mate high-voltage connectors that can be mated or unmated in an unprotected underwater environment. Figure 1 shows a typical configuration suing TE Connectivity’s wet-mate connectors. In offshore applications, we distinguish between dry-mate and wet-mate connectors. Dry-mate connectors are mated topside in dry circumstances and then submerged to their rated depth. They cannot be interconnected on the sea floor. A subsea processing system will involve both dry-mate connectors within a module and wet-mate connectors for intermodule connectivity.
Typically, in a wet-mate connector, one mating half of the connector is insulated by a shuttle mechanism protecting the female contact when unmated. A mechanical spring keeps the shuttle mechanism closed, sealing the interface. During the mating operation, the shuttle is pushed in by the male pin/contact; simultaneously, a set of seals and membranes cleans/wipes the male pin and ensures no water is allowed into the mated pair. The internal oil is displaced by the pin contact. Figure 2 shows the basic operation during mating.
The design of a wet-mate connector involves pressure-balanced dielectric oil. In order to maintain insulation throughout operations and over the design life, the connector is oil filled and pressure balanced. A bladder or piston mechanism equalizes the internal pressure of the connector to the outside water pressure. This allows no differential pressure across the seals and wiping membranes, thereby achieving a very effective wiping effect on the male pin.
Application of subsea wet-mate connectors is similar to other connector applications—they are used to directly connect two modules or to connect a cable to a module.
A special type of wet-mate connector is the penetrator. The penetrator is a feed-through connector used to separate chambers or separate a chamber from the outside world. It is basically a bushing designed to accommodate pressure differentials. The inside of a sealed piece of equipment, for example, may be at a significant different pressure than the surrounding seabed. When possible, subsea modules are pressure balanced—i.e., fluid filled, with the fluid being adjusted at the same sea pressure as outside the module. This allows for thinner walls, reduced weight, and higher reliability as seals are not required to withstand differential pressures. Some modules, such as those containing electronics or other devices such as circuit breakers, cannot withstand pressure higher than atmospheric. Therefore, a penetrator is used to prevent the seawater from leaking into them. On other devices, such as pumps and compressors, which are potentially exposed to the reservoir shut-in pressures, pressure ratings can get up to 15 kpsi/1034 bars.
Penetrators are rated for withstanding pressures—5 kpsi, 10 kpsi and 15 kpsi—which linked to the reservoir pressure. This is due to the fact that the boosting unit is in contact with the hydrocarbons. In case of a shutdown, the whole reservoir pressure may apply to the penetrator. The penetrator serves an environmentally important function: An electrical failure would mean a loss of production, but a mechanical failure would release hydrocarbons into the environment.
On other modules not linked to the oil flow, the penetrators are the barrier ensuring the electrical integrity of the module, preventing the modules from being flooded with water. DEUTSCH Wet-mate connectors, then, are key elements allowing cost-effective and technically feasible deployment, while penetrators are essential to preserve the integrity of the complete electrical power supply and to prevent hydrocarbon release into the environment.
Specifying Wet-Mate Connectors
A high-voltage wet-mate connector is usually specified by the following criteria:
• Voltage/Current Rating: Voltage and current handling capabilities are, of course, the basic metrics in choosing any power connector. Since power in subsea systems is usually three-phase, a connector is specified through three values, such as 18/30 (36) kV. The first number, 18 kV, is the phase-to-ground rating. The second, 30 kV, is the phase-to-phase rating. The final 36 kV is the maximum system voltage.
Some operational philosophies require the connectors to still operate when there is a ground fault on one of the three phases. In that case, the connector needs to withstand the second value (30kV in our example) and is selected accordingly.
• Frequency: Depending on the connectors and the application, the frequency can be low (50 or 60 Hz) for transmission. Higher frequencies—up to 200 Hz—are found downstream of a variable-speed drive. For some long, step-out applications, low-frequency AC transmission or DC can come into play.
• Water Depth/Pressure: Connectors must withstand not only the pressures of deepwater applications, but also other harsh conditions. Today, subsea processing must withstand depths of up to 3000 meters, and the need to withstand even deeper depths is expected in the next decade.
• Temperature Rating: Seabed temperatures are usually rather low and very stable, but the connectors and penetrators need to withstand the storage temperature which may be in direct sunlight in the very hot weather of the Gulf of Mexico or may be in the very cold winter of the Norwegian continental shelf. Penetrators must also be able to withstand the high temperatures generated by the modules (up to 90°C) or the hydrocarbons, which may be up to 200°C.
A Typical Interconnection System
Figure 3 shows a typical power-cabling system. An umbilical cable is terminated to a SUTA (subsea umbilical termination assembly), which is roughly equivalent to the wall socket in your home. From the SUTA, electrical flying leads (EFLs) bring power to the pump or other modules. To continue the home analogy, EFLs are like extension cords. A secondary jumper harness ensures connection from the EFL to the penetrator that serves as a transition at the pressurized motor enclosure.
Wet-mate connectors are highly engineered devices suitable for harsh marine environments. They are a key element of subsea equipment used in the subsea factory processing for oil & gas extraction. Wet-mate connectors provide a means of communications between the control room and the subsea equipment. They enable information retrieval from the sensors located in the well and related subsea equipment to assess the integrity of the well and related equipment optimizing reservoir production. They are more complex than standard electrical connectors because of the need to provide a sealed interface that can be maintained at subsea water pressures, carry high voltages and currents, and deliver very long operating lives. Products such as TE’s DEUTSCH line of subsea wet-mate connectors and penetrators are the result of years of offshore experience, both topside and undersea. Our product development advantage includes a close working relationship with designers and users of deepwater equipment to best match the connector to application needs, providing for subsea power distribution and subsea processing in a safe, reliable and economical manner.
(As published in the April 2014 edition of Marine Technology Reporter - www.seadiscovery.com)
Read Subsea Processing Boosting and Gas Compression in Pdf, Flash or Html5 edition of April 2014 Marine Technology
Other stories from April 2014 issue
Content
- MTR April 2014: Editor's Note page: 6
- Predator II ROV Put through its Paces @ FAU page: 8
- Imenco & High Resolution Subsea Digital Imaging page: 10
- Robotic Marine Vehicles: Meet the Anaconda-2 page: 16
- Upgraded Alvin Sub Passes Scientific Sea Trials page: 20
- STEM: SeaPerch Underwater Robotic Championships page: 24
- Subsea Processing Boosting and Gas Compression page: 28
- Offshore Oil & Gas: Brazil’s Northern Frontier page: 34
- The Future of Arctic Drilling: 90 Billion Barrels & Counting page: 38
- Underwater Laser Scanning for Subsea Pipeline Inspection page: 42
- Wave-Propelled Vessel Debuts page: 50
- Buoy Range Added to the EIVA page: 51
- New Acoustic Release from Teledyne Benthos page: 52
- Sonardyne Debuts SensorView Software page: 52
- Teledyne TSS Launches AHRS and INS Systems page: 53
- New Gyrocompass from Kongsberg page: 53
- FSI Announces new LF Bubble Gun page: 54
- TWR Delivers 6 Slocum Turbulence Gliders page: 54
- Kongsberg Makes Multiple Debuts in London at Oceanology 2014 page: 55
- Product Spotlight: FLEXUS More than an ROTV page: 56
- Insulated Wire Expands page: 57
- Tritech StarFish for Z-Boat 1800 page: 57
- Nautronix to Supply DPR System for Rig page: 57
- Lankhorst Mooring Ropes for Western Isles Development FPSO page: 58
- Seacon Expands Connector Range page: 58
- iXBlue, Septentrio Create ATLANS-C page: 58
- EdgeTech System for Polish Defense AUVs page: 59
- HYPACK Automatic Download of ENC Charts page: 59