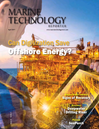
Revolutionizing Deepwater Drilling Riser Buoyancy
By Collin Gaskill
Software analysis and vortex-induced vibration (VIV) for access in extreme conditions
The ability of advanced software analysis capabilities to produce high performance, robust and dependable solutions is revolutionizing deep water drilling and production. By increasing the performance of products before they even enter the water, companies using software analysis capabilities are able to provide the solutions needed to combat the increasing harsh environments presented by the offshore world.
Maximizing Efficiencies
As exploration of offshore oil and gas continues to move into deeper waters, the demands for drilling operations to be performed faster and more efficiently, providing cost savings and safer well completions, persists.
As companies move to water depths past 12,000 feet the technology they use has evolved. Extensive engineering design work is now performed using specialized software to produce local and global finite element (FE) and computational fluid dynamics (CFD) analysis to develop optimum designs. The ability to model equipment and system responses to environmental forces helps advance product development and design opportunities to maximize operational efficiency, resulting in cost savings, increased service life and multi-functional designs.
Companies with in-house analysis teams can simulate offshore drilling and production operations, offering customers solutions considering a fully coupled vessel to well approach. These riser studies can specifically be used to assist clients in defining operational methodologies and structural system limitations for offshore drilling and production operations.
Drilling Deeper
Offshore oil and gas exploration requires drilling vessels to deploy thousands of feet of steel drilling riser through the water column to safely and effectively drill offshore production wells. Drilling campaigns in deep and ultra-deepwater locations can see millions of pounds of riser and equipment deployed and suspended from the drilling vessel required to be kept in tension to avoid buckling failure. For decades, the offshore drilling industry has utilized drilling riser buoyancy modules (DRBMs) to reduce the overall riser weight and required top tension. DRBMs are highly effective at adding necessary uplift to drilling risers however, the associated drawback is increased overall outer diameters which subsequently increase the magnitude of loading experienced by the riser due to hydrodynamic forces.
Increased hydrodynamic diameters reduce the magnitude of environments that drilling vessels can safely operate. Additionally, consequences from the phenomenon of riser vortex induced vibration (VIV) developing from a complex interaction between the riser structure and the flow field around the riser coupled with the occurrence of drag is amplified for larger structural diameters. These forces induce periodic oscillations or vibrations of the riser, which transmit large amounts of dynamic strain from the riser system to subsea equipment. With exploration extending into deeper waters and locations with onerous environmental conditions occurring year around, the offshore drilling market requires solutions that allow for large magnitudes of buoyancy uplift without the penalty of increased drag and VIV forces.
Multifunctional Designs
A new multifunctional buoyancy solution has recently been developed to integrate drag reduction and VIV mitigation into DRBM equipment, reducing the necessity for auxiliary suppression equipment and alleviating complicated and time intensive riser running and retrieval procedures.
Inverted helical straking of drilling riser buoyancy modules allows for in-line drag reduction and VIV suppression of drilling riser systems through the use of a tri-helical groove design molded into the outer profile of the buoyancy modules. The origins of the design stem from external helical strake designs, which have been used in the offshore industry since the late 1970s to suppress VIV of slender structures. However, the inverted strake design, unlike its externally protruding predecessor, does not increase the overall hydrodynamic diameter of drill riser buoyancy modules and therefore VIV suppression comes without the undesirable penalty of increased in-line drag.
Obtainable VIV mitigation properties of the inverted tri-helical buoyancy design with the elimination of required auxiliary equipment simplifies and increases the running and retrieval times of the riser compared to traditional suppression technology. Numerous locations across the globe are subject to the sudden onset of onerous weather, requiring drilling vessels to be able to respond quickly in order to transit out of forecasted storm paths. If these fields are subjected to high current or VIV inducing metocean conditions, as many of them are, operators may opt out of drilling in these locations at certain points of the year or entirely, as retrieval of the riser and vessel transiting speeds are not adequate with the increases in joint handling time associated with auxiliary VIV mitigation equipment. With the adaptation of the strake design to an inverted tri-helical groove, incorporated into the buoyancy itself, suppression of riser VIV and reduction of riser drag is obtainable without an increase in riser retrieval time, offering a solution for well sites with volatile environmental conditions.
Analytical Modeling
Extensive engineering design work has been performed on the inverted helical groove geometry through numerical modelling in computational fluid dynamics (CFD) software packages to develop the optimum design. This effort is reflected in a solution that corresponds to a minimal loss of buoyancy uplift, due to a minimal removal of material to facilitate the inlaid groove, while still retaining vortex suppressing properties. Similar to external strakes the inverted design disrupts the continuity of fluid flow around the outer diameter of the buoyancy modules by introducing variances in the cross-sectional geometry at each new cross section along the axis of the riser. Discontinuities in external geometry profiles along the axis of the riser lead to variances in the separation point of the flow around the outer diameter of the drilling riser which disrupt the organization of forces due to vortex shedding, the driving force responsible for larger magnitudes of riser response and subsequent dynamic strain.
Three dimensional finite element models developed for use in CFD analysis help to illuminate additional benefits realized from the inverted helical design. In contrast to traditional buoyancy modules where fluid flow paths occur almost exclusively in the horizontal plane, looking down the axis of the riser, axial flows induced by the inverted helical groove introduce turbulence into the downstream wake profile of the drilling riser. Axial flow paths result in forces that act out of plane of cross flow lift forces and in-line drag forces disrupting the cyclical rotation of these forces on the downstream side of the riser.
Reducing VIV and Inline Drag
Reduction of riser motion due to VIV in the in-line and cross-flow directions can limit the amount of dynamic loading transferred to subsea equipment and conductor casing programs from the riser. Overall decreases in cyclical loading may lead to increases in the integrity and life span of critical well containment equipment. Possible benefits of the reduction of riser drag and VIV by means of reengineered drilling riser buoyancy are numerous, with the potential to enhance overall performance of drilling vessels and the economic feasibility of accessing reservoirs in increasingly challenging environments.
Drilling operability envelopes, or the connected vessel distance away from directly over wellhead that is still deemed safe to drill, are frequently limited by allowable mean and maximum flex joint rotation angles, requiring the suspension of drilling activities at higher rotations. With a decrease in the in-line drag loading and overall deflection of drilling riser systems, upper and lower flex joint rotations are reduced for certain environmental conditions and riser system configurations. This can correspond to increased time frames where rotation of the drill string within the riser annulus is permissible, without the danger of key seating the riser joints. This potentially allows offshore wells to be drilled faster as windows of time where operations are suspended due to riser deflection are diminished.
Benefits extend beyond the expansion of drill string rotation envelopes; decreased in-line drag and riser deflection can enable deployment and retrieval of the riser in higher current environments. Additionally, reductions of overall deflection along the riser can lead to a reduced possibility of clashing between the riser system and the vessel or other various deployed equipment from the auxiliary rotary or cranes. Higher vessel transiting speeds, with a riser string deployed, are also potentially achievable in certain scenarios, as maximum allowable velocities, limited by riser stresses and the potential of riser clashing, are increased. Finally, decreased riser drag can improve riser disconnect performance as horizontal excursion of the riser due to current loading is reduced after disconnect occurs.
Conclusion
By using advanced software analysis, companies can continue to revolutionize deepwater drilling and production in increasingly demanding and previously inhospitable environments. Software analysis coupled with the advancement of riser drag reduction and VIV suppression technology, provides an integrated solution to progressing drilling riser buoyancy and opens the door for resource exploration in areas previously deemed inaccessible. Extended lengths of risers in ultra-deepwater applications are more susceptible to the complications arising from higher current velocities and the necessities of increased buoyancy uplift due to the increased weight of deployed steel riser joints. The inverted helical drill riser buoyancy module design combats both of these important issues without increasing required equipment and rig operation times. Solution-specific engineering of the inverted helical module will facilitate the ability of drilling vessels around the globe to continue to deliver the energy needs of the future.
The Author
Collin Gaskill is Riser Analysis Engineer at Trelleborg Offshore.
(As published in the April 2017 edition of Marine Technology Reporter)
Read Revolutionizing Deepwater Drilling Riser Buoyancy in Pdf, Flash or Html5 edition of April 2017 Marine Technology
Other stories from April 2017 issue
Content
- Voices: Sean Halpin page: 12
- Young Innovators to Compete in Underwater Robotics page: 16
- Norway's Heavyweights & Entrepreneurs page: 22
- To Create a Sustainable Future – Digitalize Offshore Energy page: 26
- Revolutionizing Deepwater Drilling Riser Buoyancy page: 32
- Work Class ROVs page: 38