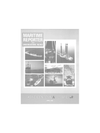
POSITION/LIMIT SENSING SOLUTIONS IN HARSH ENVIRONMENTS
Salt water is one of the toughest environments when it comes to exposed machinery. Common untreated metals are eroded in a matter of months and expensive equipment can become useless in half that time.
One particularly vulnerable part of such equipment can be positioned sensing or limit detection devices.
These devices protect the equipment from overtravel conditions and prevent damage to the equipment or personnel. However, these devices are particularly vulnerable to harsh environmental conditions and can become non-functional, creating a hazard to both man and machinery. Recently, electronic proximity sensors specifically designed for the marine environment that address such problems have come on the market.
This article briefly looks at the currently available sensing techniques, their strengths and weaknesses, and presents several case studies where operators are now using the new ruggedized electronic sensors to solve some particularly demanding application problems.
Types of Sensing Devices Basically there are two main categories of sensing devices: contacting and non-contacting.
In the contacting category are primarily mechanical limit switches.
These switches contain contact closures within a sealed container and have external actuating arms or plungers that contact a moving element of the monitored equipment.
When the moving element exceeds a set limit or position, the switch interrupts the power circuit or sets an alarm indicating an unusual condition.
Because of wear factors and other physical changes, these switches require regular maintenance.
Non-contacting sensing devices, on the other hand, make no contact with the moving element and have no moving parts. All sensing is done electronically using techniques such as metal sensing, magnet sensing, optical path interruption, and detection of changes in capacitance.
The devices, commonly known as electronic proximity switches, require much less maintenance than contacting devices and last considerably longer.
In summary, the choice is between mechanical switches and electronic proximity switches to solve position/limit sensing needs.
Strengths and Weaknesses In considering the strengths and weaknesses of the two categories of switches, it is important to evaluate these products in the context of environmental and cost factors.
When using these devices in an application that is exposed to the marine environment, there are several factors to consider, particularly when the application is exposed to green water. First is the question of watertight integrity for the switching elements and, second, the materials used in the construction of the device itself. Unless a switching device has been built specifically for the marine environment, either of these factors can render a switch useless in a very short period of time, causing costly downtime and excessive maintenance/replacement expenditures.
Mechanical limit switches, because of their intrusive mechanical coupling, are inherently weak in these areas resulting in early contact corrosion failures. Proximity switches are particularly strong in these areas because of the lack of mechanical coupling, and because typically, they are potted in an epoxy resin which protects the internal switching elements and electronics.
Other important considerations are mechanical shock and vibration when choosing a sensing solution.
Again, proximity switches excel in this area because of their one piece epoxy impregnated design. Unlike mechanical switches, the contact closure in these solid state switches will not vibrate out of adjustment and wear out as a function of the number of operational cycles. They are typically capable of many millions of cycles rather than the finite number of contact closures that are characteristic of mechanical devices.
Another consideration for proximity switches is the question of RFI/EMI (Radio Frequency Immunity/ Electro-Magnetic Immunity).
Our environment is jammed with static and interference, radio signals, TV signals, and radar trans- missions. Electronic devices, if not properly protected, are susceptible to interference from these conditions.
Mechanical switches are virtually unaffected by such signals.
Industrial grade proximity switches are protected to a small degree, but are not designed to operate in strongly radiating fields such as radio transmitters and radar. However, properly constructed proximity switches designed to operate in these strongly radiating fields will perform similarly to the mechanical switches. These proximity switches are designed to meet MIL-STD 461 for stringent military applications.
Are there differences in cost among the choices available for position/ limit sensing applications.
Yes, there are, although the true cost of a particular product may not be obvious from acquisition cost alone.
On the low end of the scale, industrial grade proximity switches and mechanical switches are available for less than $100. However, these units will not survive harsh environments very well and, in the case of the industrial grade proximity switch, will not perform well in RFI/EMI environments. Higher grade mechanical switches that will better survive the harsh marine environment are available in the $100- 300 range. In the $300-450 range are top-of-the-line proximity switches designed specifically to withstand the rigors of the marine environment.
Acquisition cost does not tell the whole story, however. In a tough environment, long term operational costs should be considered as well.
Only then can the true cost of a particular solution be measured.
On the low end of the scale, industrial grade devices have a very small initial outlay. However, the devices will not survive for any great length of time. Additional purchases must be made and the cost of labor to re-install each time figures prominently into the overall cost. Additionally, there's the cost of lost productivity and other factors/costs associated with downtime to consider.
Higher quality mechanical devices that better withstand the environment can be acquired for a slightly higher initial cost, but such devices are subject to moisture intrusion because of their mechanical coupling. They also have a limited contact life in terms of the number of cycles of operation. In fact, all mechanical switch applications have more routine maintenance and adjustment than proximity devices because of the wear factors in the switches themselves as well as the wear factors in the equipment. Although not as often as with the industrial grade devices, these higher grade mechanical switches must also be replaced regularly.
The best grade of proximity switch has a higher initial outlay but has superior environmental characteristics.
As there is no physical contact with the moving element, and solid state switching is used to dramatically increase the number of operational cycles, MTBF (Mean Time Between Failures) is very high, in excess of 125,000 operational hours. Statistically, associated replacement and labor costs are very low, downtime is minimal, routine maintenance and adjustment is nil and reliability far exceeds the other choices. Although the initial outlay is slightly higher, the overall cost savings over the life of the product will add to the operator's bottom line in terms of lower overall operational costs.
Several case studies illustrate how these high grade proximity sensing devices have been used to solve demanding problems.
Application No. 1: The U. S.
Navy uses a Bow Ramp and Stern Gate deployment system on the LST class of ships. The system allows vehicles to move from the inner decks of the ship up over the bow and onto the beach. The stern gate is a platform that is lowered from the stern of the ship to create a ramp that allows the launch of amphibious vehicles to carry troops to the beach.
The problem: The Navy was using industrial grade proximity switches for position sensing. The switches used a two piece design that had a separate amplifier and output switch. The problem was the switch did not function well in this particular environment and application.
LST's, being flat bottomed ships for convenient shallow water access, do not ride well in rough seas and therefore take a lot of green water over the bow.
The solution: The ELDEC Corporation, in conjunction with the U.
S. Navy, jointly developed a standard proximity switch specifically designed to withstand the rigors of this application and provide the kind of reliability that is required by the Armed Forces. These switches have been successfully installed on 90 % of the 20 ships in the class and have been performing very well for the past year and a half. During that time, there have been no operational failures in almost 800 switch installations.
Application No. 2: On board the Navy's carriers is a system of elevators whose primary purpose is to bring weapons/cargo to the hangar deck. In most applications these elevators move between 3 and 7 decks and have full size access hatches at most levels. System requirements are that all hatches be secured before the platform will move. An elevator controller monitors all door closures, level sensing, and speed switches for proper operation.
Previously, most of these sensors were mechanical rotary arm switches.
The problem: Flight operations on a carrier require proper fire prevention in case of emergency landing/ spilled fuel. When the threat of fire does occur, the Navy's AFFF (Aqueous Film Forming Foam) is applied to the ship's equipment and decks. Afterward, this extremely corrosive fluid is washed from the deck with seawater. This combination of seawater an AFFF then spills into the elevator shafts and escalates the corrosion/failure of the mechanical sensing devices contained in the shaft.
The solution: The Navy now has a long term program to replace these mechanical switches with highly reliable MIL qualified proximity switches. Cost projections show that program will save the U.S. Navy a significant amount of money over the long term.
Application No. 3: Crowley Maritime, a major barge towing operation, needs to monitor any slippage of the cable winch during towing operations. If the drum slips, sensing devices activate a switch closure and sound an alarm.
The problem: The port engineer was using mechanical limit switches with a lever arm extending into the structural spokes on the winch drum. Due to relatively low freeboard on seagoing tugs, a fair amount of green water comes over the gunwales in rough seas, corroding these switches. Every six months each mechanical switch had to be replaced at a cost of $125 plus electrician's labor of $35.
The solution: Crowley changed to environmentally hardened proximity switches better suited to the task. They report no failures in two years.
Conclusion The above applications all had common difficulties: harsh, hostile environments and corrosive fluids.
Cost effective solutions for these difficult situations demand a durable product with reliable operation at a reasonable total expenditure.
Industrial grade proximity solutions have the lower initial cost but incur significant replacement and maintenance expenses. Higher grade mechanical solutions have the same drawbacks over the longer term.
The higher grade proximity switches are the best choice for cost effectiveness, durability, and superior reliability. For those applications where downtime and profit margins are affected by employing a less than satisfactory solution, it is imperative that the proper choice be made. In the harsh environs of the sea, it can be costly to select less than what the job demands.
For free literature on higher grade proximity sensing switches from Eldec, Circle 70 on Reader Service Car
Read POSITION/LIMIT SENSING SOLUTIONS IN HARSH ENVIRONMENTS in Pdf, Flash or Html5 edition of April 1988 Maritime Reporter
Other stories from April 1988 issue
Content
- MHI Delivers Newest Tanker For Chevron Fleet page: 5
- New Nirex Freshwater Distiller And Ice Machine From Alfa-Laval page: 6
- Repower With Cummins NTA-855-Ms Gives Pushboat A New Life page: 7
- System Expansion For WLO Radio page: 7
- Penn Ship Names Veteran Shipbuilder Grandin Vought Operations Vice President page: 7
- Krupp Atlas Elektronik Navaids page: 8
- A.S.N.E. DAY '88 A CENTENNIAL CELEBRATION page: 10
- Aeroquip Offers Free Hose Line Training Bulletin page: 19
- Woodward Governor Forms International Operations Division page: 20
- Moss Point Marine Delivers First Of Two Navy Landing Craft page: 21
- Six-Patrol-Boat 'Package' Completed By Halter Marine For Ecuadoran Navy page: 22
- Two New Low-Cost Products From Furuno: Temperature Sensor, And Net Sounder page: 22
- OTC-'88 20th ANNIVERSARY SPECIAL PREVIEW page: 24
- Astilleros Espanoles Yards Report Full Orderbooks Well Into 1989 page: 50
- New 52-Page Catalog On Lighting Offered By Aqua Signal page: 51
- Radio Holland USA Opens New Service Centers page: 51
- Halter Converts Supply Boat To Crabber/Processor In 90 Days page: 52
- POSITION/LIMIT SENSING SOLUTIONS IN HARSH ENVIRONMENTS page: 54
- Ingalls Shipbuilding Awarded $769-Million Navy Contract To Build Four Aegis Cruisers page: 56
- Riedel International Announces Key Promotions page: 56
- Halter Marine Converts Crewboat For Fisheries Patrol Service page: 57
- Skipperliner Shipyards Delivers Cummins-Powered Passenger Vessel page: 58
- Schaffran Offers Advanced, Compact Controllable Pitch Propeller page: 59
- Port of Genoa Attracts New Container Business Under Innovative Leadership page: 60
- Perkins Marketing Light Marine Engines As Power Prestige Line page: 61
- Literature Offered On Marine Cross Reference Data Base Compact Disc page: 61
- Datamarine's ^Chartlink' Adds New Dimension To Loran/Satnav Navigation page: 62
- Caterpillar Announces 1.1 -Liter Family Of Marine Diesel Engines page: 62
- Robertson-Shipmate's Multi-Station Commercial VHF Radiotelephone Now Approved For Use In U.S. page: 64
- Reiss Purchases Rexnord Defense Systems —Renamed TANO Corp. page: 65
- Free Literature Offered On Full Line Of Steering Gears From Tenf jord page: 65
- Academy Chief Elected To ASNE page: 66
- Deutz MWM Diesel Engine Series Offer Distinct Advantages For Passenger Boat Propulsion page: 66
- Seaward International Supplies Large Fleet Mooring Buoys To Navy For Use In Pacific Islands page: 69
- SASMEX '88 To Be Held April 26-28 In London page: 70
- Hyundai Heavy Industries To Build Ethylene Carriers page: 72
- MAN B&W's New 2 8 / 3 2 A Diesel: Improved Fuel Economy With Same Reliability page: 73
- Fluid Energy Launches 64-Foot Passenger Submarine page: 78