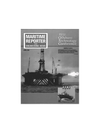
Flexible Power Solutions*
On many vessel types the required propulsion power varies greatly during a single voyage. Remarkable differences in load, trim or cruising speed are the cause.
Many shipowners have noted that conventional single-engine solutions do not provide the flexibility required for such wide fluctuations.
The effects are even greater for ships where the original trial speed was far above the actual requirement.
Trial speeds and thus the installed main engine outputs are purposely selected to be too high.
This is done to make the ship more interesting on the second-hand market, while the actual traffic where the vessel is used moves at much lower speeds.
Multi-engine solutions are often chosen for many ship types. This permits generation of propulsion power required in any operating mode at engine loadings close to the optimum fuel consumption loadings.
.
The most spectacular example is the passenger ferries, where the usual layout is two propeller shafts and four main engines. There are also examples where as many as four engines are served by a single gearbox.
For a typical passenger ferry with a four-engine, twin-screw installation, the installed outputs can exceed 45,000 bhp. The reasons why passenger ship operators select multi- engine configurations are obvious: availability; flexibility; and compactness.
Another way to achieve flexibility is to install a diesel-electric solution, where the propulsion power comes from a common "power station." The power station normally consists of from two to even nine engines and since this power station feeds both the electrical equipment as well as the propulsion motors, it is easy to install an electronic performance control that starts and stops engines based on the actual power requirement.
In this way, the engine loadings are always on or close to the optimum fuel consumption point.
A twin-engine installation would be normal for a single-screw vessel.
In some cases the optimum is that both engines are the same size. In other cases, it is better to use a "father- and-son" installation, which is a machinery arrangement where the main propulsion is handled with a multi-engine arrangement consisting of a larger engine (father) and a smaller engine ( son). The engines are connected to a common gearbox and drive a single controllable pitch propeller.
The father-and-son solution is usually very efficient for ships with a varying speed or loading profile.
By selecting the sizes of main engines wisely and by installing suitable shaft generator arrangements, remarkable savings in both capital expenditure and operating costs can be achieved.
Further savings can be made when onboard electricity is generated with the main engines. Due to the CPP installation, the configuration does not require expensive constant speed gears for a shaft generator.
The cost and complexity of such devices are normally much more than what would be anticipated in the initial stage.
In conclusion, the use of multiengine installations has proven a useful alternative to conventional slow-speed engine installations. The flexibility needed to run at any speeds and loading conditions is highly appreciated by owners already using the system.
The availability of the system is increased, since the ship is maneuverable at all times, even if one of the main engines is being overhauled.
The economy of this system results not only from lower operating costs, but also from low capital expenditure and space savings.
For free literature on diesel engines from Wartsila, Circle 62 on Reader Service Card *Editor's Note—Excerpted from a paper by Kenneth J. Jofs, president, Wartsila Diesel do Brasil Ltda.
Other stories from April 1991 issue
Content
- Halter Marine Christens Second Of Two Navy Survey Ships page: 8
- Literature Available On COMSAT's SatCom Services page: 9
- New IMO Quabbin Package Improves Turbine Performance page: 9
- Balehi Marine Delivers Second Of Two GM-Powered Towboats For Conoco Oil Company page: 10
- Winninghoff Boats Introduces Versatile Workboat Design— Literature Available page: 11
- Wide Range Of Vessels Using Hamilton Water Jets Detailed In Free Literature page: 11
- Allied Shipbuilders Deliver New Caterpillar-Powered Z-Drive Ship-Assist Tug page: 12
- Saab Marine Reports Orders Received In Excess Of $35 Million page: 14
- World Bulk Fleet Expected To Increase Moderately For Next Few Years page: 16
- Lexair Introduces New Three-Way Poppet Type Control Valve page: 16
- Exxon Celebrates Grand Opening Of Port Allen Lubricants Plant page: 17
- Textron Marine Awarded $69.1 Million Navy LCAC Order Yard Completes SES Refurbishment page: 18
- Viking Introduces New 50-Man Reversible Buoyant Apparatus page: 19
- NEI Syncrolift Wins Over $3 Million In Orders For Shiplifts, Transfer Systems page: 20
- AT&T Awarded $157 Million Contract To Build Undersea Fiber-Optic Cable —Color Brochure Available page: 20
- OTC 91 page: 23
- Balancing The National Energy Strategy page: 30
- Gulf Craft Delivers 160-Foot Aluminum Crewboat For U.S. Gulf Operator page: 35
- Southwest Marine Reports Upturn In Ship Repair And Conversion Business page: 36
- American Ship Building Awarded Navy Contract For Up To Six Ocean Surveillance Ships page: 37
- Shipbuilding Surge Predicted For 90s page: 38
- Rail/Sea Link Crossing Soviet Union Opened By Sea-Land Service page: 39
- ASNE DAY 91 'Naval Engineering In The Changing Defense Structure' page: 42
- The Iowa Class Battleships page: 50
- PMSA Study Shows Impact Of Maritime Industry On 3 West Coast States page: 51
- General Dynamics Announces Two Key Appointments page: 51
- Inventory Locator Names Jim Bross Sales Director page: 52
- Hatch & Kirk Defco Division Opens In Houston, Texas page: 52
- Innovative Tug/Barge Training Begins At Maritrans GP page: 53
- War Showed Absolute Surge Requirement For More RO/ROs page: 54
- Sperry Marine Maintains Leading Position In Competitive Marine Electronics Market page: 55
- Archway Marine Lighting Introduces New Hi-Tech Searchlight Fixture Line page: 57
- Sound Ocean Systems, SUTEC Awarded NavSea MMUROV Contract page: 58
- Amprodux Introduces New Model Level Alarm/Control Unit page: 58
- Baldt Celebrates 90th Anniversary page: 59
- Krupp Atlas Introduces New Echosounders page: 60
- Astronomical Drilling Rig Prices Anticipated Because Of Worldwide Demand page: 60
- Murphy's All-New Gage And Control Catalog Pictures Over 80 Products page: 61
- Nordic Machine Expands Line Of Anchor Winches page: 62
- ZF Extends Range Of Marine Transmissions page: 62
- TWRA Members Adjust Rates Previously Set For U.S. Exports To Far East page: 63
- Sea Recovery Offers Compact, Commercial R.O. Desalinator page: 64
- Singapore Introduces Tax Plan To Lure Foreign Shipowners page: 65
- Louisiana Officials Create Oil Spill Cleanup Tax page: 65
- Kerr Becomes U.S. Agent For Brazil's Nacional Line page: 65
- McDermott Awarded Marathon Oil Contract page: 66
- DNV Grants Quality Certificate To Wartsila page: 66
- Jered Brown Bros. Expands Manufacturing Capability By Leasing Georgia Facility page: 66
- World's Largest Seiner Delivered By AESA page: 68
- MSE Offers 28-Page, Full-Color Brochure On Shipbuilding & Services page: 69
- 50,000-GRT 'Costa Classica' Launched At Fincantieri's Marghera Yard page: 70
- Thomas B. Crowley Jr. Appointed Manager, Red & White Fleet page: 71
- Shipowners In Hong Kong Welcome Canadian Moves To Offer Tax Incentives page: 71
- Tanker Owners Alter Practices To Cope With Risks Under Pollution Act page: 72
- Gladding-Hearn Building Detroit Diesel-Powered Catamaran For California Ferry Market page: 73
- SPD Technologies Names Colangelo Executive VP page: 74
- Stolt-Nielson Names White Managing Director, Tanker Trading-Europe page: 75
- Delaval Turbine Division Appoints Kramer, Morgan To Marketing Department page: 75
- Best Effort Response To Cleaning Up Oil Spills page: 76
- Severe Vessel Shortage, Advanced Age Of Fleet Threaten Some USSR Lines page: 76
- Schepen Appointed VP, Central America/Panama Service For Crowley page: 77
- Leslie Acquires Bailey Division, CMB Industries' Navy/Marine Product Lines page: 77
- Ingalls Christens USS Essex, Second Wasp Class Assault Ship page: 78
- Western Coal Shipments Through Great Lakes Ports Could Expand Dramatically page: 79
- Norwegian Navy To Build Nine MCMVs With Composite Hulls page: 80
- Tore Steen Appointed President And CEO, West State, Inc. page: 81
- PBM Designs Patented Flush Tank Valve— Literature Available page: 81
- New $40 Million NSF Research Ship Fitted With Thordon Bearings page: 84
- Leevac Shipyards Delivers First New Supply Vessel Built In U.S. Since 1986 page: 85
- McDermott Marine Readies Four-Pile Offshore Platform For Freeport-McMoRan page: 86
- Avondale To Use Japanese Method Of Building —Gets Trade Zone Status page: 86
- Trimble Navigation Introduces Integrated GPS Receiver And Antenna In One Unit page: 87
- Flexible Power Solutions* page: 88
- Marine Inland Fabricators Launches Tow Steering Unit page: 89
- Lykes Bros. Names Two New Officers page: 91
- Marine Liability Insurance Increases Up To Threefold For Tankers Trading To US page: 92