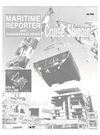
Industry-Wide Interoperability Investment Paying Off
The Integrated Shipbuilding Environment (ISE) project sponsored by the National Shipbuilding Research Program is a three-year effort to develop and deploy an industry-wide architecture for computer interoperability. ISE is targeting cost and cycle time reduction for both Navy and commercial customers by providing real-time digital connectivity between shipbuilders and their suppliers. ISE also targets the total ownership costs during the 40-year life of a ship in that it provides access to configuration data during the life of a ship or ship class - regardless of computer system upgrades.
The expected benefits of this project are very high. For each shipyard, conservative benefits are a 15 percent reduction in pre-contract labor, six percent reduction in production labor and a two percent reduction in material costs.
Business Case The ISE business case is simple: radically reduce the costly, time-consuming and error-prone manual re-entry of complex 3-D design information through reliable and efficient digital data transfer of: • Part information from vendor electronic libraries into shipyard parts libraries, 3-D design data from CAD files to the sophisticated computer analysis and simulation tools used to validate the design of each ship system, and • 3-D design data between diverse CAD systems and versions at shipyards specializing in defense work, commercially oriented U.S. yards, and marine suppliers. This capability is significant because second tier shipyards and marine suppliers rarely use the sophisticated high-end CAD tools used by U.S.
yards supporting DoD programs, and because even a single vendor's CAD product installations at different facilities routinely result in interoperability issues. The patchwork solutions currently used to address this increasingly significant cost driver include time consuming and very expensive modification of direct point-to-point translators every time a new version of a CAD system is implemented at any point in the supply chain, or among co-design or co-production partners — a frequent occurrence.
ISE's end goal is a cost effective, integrated, and functional information system that will provide toolsets for realtime collaboration and information sharing among shipyards, suppliers, owner/operators, and regulators.
Toolset capabilities include: • Direct download of piping and structural parts data from vendor electronic catalogs into shipyard digital parts libraries; • Export of detailed CAD data to (a) analysis tools, (b) simulation programs, and (c) ship classification software; and.
• Electronic exchange of molded form data (complex geometric shapes of steel hull plating) between four different shipbuilding CAD systems.
These capabilities flow from adherence to international standards for data structures — a practice adopted across most manufacturing industries worldwide.
Typically during the life cycle of a ship or ship class, the Navy, shipbuilders and/or suppliers will face one or more Computer-Aided Design (CAD), Computer- Aided Manufacturing (CAM), Enterprise Resource Planning (ERP), and or Product Data Management (PDM) system transitions. The consensus ISE standards and protocols being developed enable new systems to access the data from previous systems and enable new versions of existing systems to access data from all previous versions — a capability whose absence in current systems is costly.
ISE's key asset is the critical mass of committed stakeholders — an empowered team with representatives from U.S. shipyards, CAD/CAM vendors, regulatory bodies and software vendors.
The team has developed and approved an architecture for interoperability that includes agreement on information requirements and data exchange standards and protocols. The ISE architecture uses readily available Internet technologies as well as data exchange standards being developed in conjunction with the International Standards Organization (ISO).
Progress, Implementations and Early Results Shipyards are already using ISE tools in warship production on the submarine and Carrier programs. These tools enable shipyards to select digital tools (simulation, analysis, ERP, CAD, PDM.
etc.) best suited to their business, yet fully participate in co-design and coproduction arrangements that rely on other information systems to design, build and maintain war ships. Highlights of the project's on-budget, onschedule successes include: • Development/agreement of industry- wide interoperability architecture • Publication of hundreds of use cases defining requirements for information sharing at many shipyards • Development of common data element definitions and common taxonomy for transferring data between parts libraries and supplier catalogs • Development, demonstration and distribution of tool sets for inter-organizational sharing of piping system information.
including: parts catalog information, system diagrams and simulation engines, and detailed design and analysis systems. Available, proven tools are a mix of open source software available on the project's website and commercially available tools in the product lines of collaborative design, co-production, integrated supply chain, and standardized parts.
The project recently completed the second of three years with a highly successful demonstration of capabilities.
The April 4 demonstration showcased the impressive "eShipDesign" capabilities of the consensus architecture, standards, protocols, and toolsets developed to date. The following capabilities were demonstrated: • Direct download of piping and structural parts data from vendor electronic catalogs into shipyard digital parts libraries.
• Export of detailed CAD data to analysis tools, such as Anteon's Proteus Flagship Suite, simulation programs such as SIMSMART. and ship classification software such as the ABS Safe Hull program.
• Successful electronic exchange of molded form data (complex geometric shapes of steel hull plating) between four different CAD systems (Dassault's CATIA, Sener's FORAN, KCS' TRIBON and Intergraph's GSCAD).
Examples of estimated savings are: Cost to link two IPDE (Integrated Product Development Environment) systems for co-design or co-production is estimated to be $30 million. If there are three programs over the next 10 years that use an IPDE, the total cost would be $90 million. It has been estimated that the ISE developed tools will save 40 percent or $36 million.
• A top down projection of savings for the design process for Navy programs is $188 million over 10 years (see chart, previous page).
Circle 1 on Reader Service C a rd w w w . m a r i t i m e r e p o r t e r i n f o . c om Any queries regarding this article may be directed to the Program Administrator (Advanced Technology Institute): Tel: 843- 760-3331; Email: [email protected]
Read Industry-Wide Interoperability Investment Paying Off in Pdf, Flash or Html5 edition of July 2002 Maritime Reporter
Other stories from July 2002 issue
Content
- Zodiac Debuts Bulletproof System For CRRC page: 5
- Historic $17 Billion Order Placed page: 6
- USCG Proposes New Changes in Vessel Arrival/Departure Procedures page: 9
- NASSCO Celebrates Keel Laying of Trailerships page: 11
- Industry-Wide Interoperability Investment Paying Off page: 12
- Tribon M2 Aim: Better Ships at a Lower Cost page: 14
- Total CAD/CAM Solution for Ship Design and Building page: 15
- Juniper Industries Keeps the Water Out page: 17
- Molding the five-deck Trailership page: 18
- IZAR Gijon Delivers Dredger page: 19
- Estonians Raise the Ferry Stakes page: 19
- Transportation Secretary Announces $92.3M in Port Security Grants page: 21
- USS Shoup Commissioned page: 23
- U.K. Royal Navy Increases Overhaul Efficiency of HP Air Cylinders page: 24
- DD(X) Dispute: BIW Files Protest page: 25
- Technological Wonder, No Matter How You SLICE It page: 26
- GALILEO: 2008 or Bust? page: 28
- Forget the Dog, MTN Delivers the News Onboard Residensea page: 29
- SeaWave Aims to Drive Down Communication Costs page: 29
- Iridium Aggressively Pursues New Outlets page: 30
- Fincantieri Stays Strong page: 32
- Fincantieri Predicts Clear Vista For HAL page: 32
- Rodriquez Cantieri Navali: Fast Company page: 33
- SEA RIDER Infiltrates Small Craft Propulsion Market page: 34
- ACG Makes Solid Inroads page: 35
- SubSea Solutions Alliance Provides Quick Fix - Underwater page: 36
- Classic Vessel's Demise Lead to New Found Hobby page: 38
- STAR Center Provides 360-Degree Field of View page: 41
- MAN B&W 48/60B Engine page: 42
- Titan Pulls One Off for Marine Response Alliance page: 54