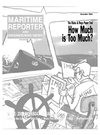
Introducing Lean Shipbuilding to U.S. Yards
Lean times call for "leaner" boats and what better to employ than Lean Shipbuilding, which is known as a proven approach that shipyards can use to improve shipbuilding efficiency. It has the advantages of reducing defects while remaining responsive to change.
How does this differ from the traditional method of shipbuilding? Broken down into three steps these components deal with: • Push vs. Pull • Batch and Queue vs. Continuous • Top Down vs. Bottom Up.
Each element builds on the others to make Lean Shipbuilding work.
Therefore, when trying to implement Lean Shipbuilding, the whole concept should be implemented rather than just a few important pieces.
The Lean Shipbuilding Model will then be introduced. This model, which helps to illustrate the key components of Lean Shipbuilding can be presented in three main categories: • Just-In-Time • Built in Quality • Operational Stability.
The success of Lean Shipbuilding, through these three categories, depends on a flexible and motivated workforce.
With an overall goal of 100 percent customer satisfaction.
Traditional v. Lean Shipbuilding Push vs. Pull Traditional shipbuilding uses push production to manufacture multiple quantities of similar products in series.
Based on a detailed schedule, similar products are manufactured one after another until the required quantity has been reached. This method, which boasts a high level of anticipation, can lead to overproduction or underproduction.
During the production process parts are pushed from one workstation to the next. When delays occur, parts and subassemblies sit idle, where they can be lost or damaged - not only tying up capital - but space as well.
Lean Shipbuilding utilizes pull production.
In a pull system, no part is made unless the customer requests it.
Here the customer can vary from the vessel owner to the mechanic installing the equipment. Because this process is demand oriented, the system is therefore highly responsive and flexible to the customer's needs. All parts are used as soon as they are completed, thus eliminating idle time between workstations.
The idle time between workstations adds no value to the part. The actual value is added at the workstation because the part is improved at each step. Each improvement makes it more valuable to the customer.
Another difference between push and pull production is raw material delivery times. In a push cycle, material is ordered and delivered well ahead of time according to a predetermined schedule. This leads to large inventories of material that may not be required for some time. Again idle material leads to higher costs in both the land required to store the material and the cost of the material, which is not recovered until the material is actually used. A pull production cycle utilizes small, more frequent.
orders and deliveries. Where a push cycle may take delivery of large amounts of material weekly or monthly, a pull cycle may take delivery of small lots several times a day. This ensures smaller lot sizes, so storage areas are not as large and materials are utilized shortly after they arrive.
Batch and Queue vs. Continuous Flow Another instance of waste encountered in traditional shipbuilding is large batch sizes. A batch is a group of parts that is produced one after another until a preselected number are produced, at which time they are pushed to the next station.
This is called batch and queue flow - batch because of the quantity of a part produced - queue because the parts wait until they are needed. Batch sizes vary depending on the process. Instead of releasing each part as it is produced, the part must wait until all other parts in its batch are competed and it is then moved as part of a batch to the next station.
Once the part is moved to the next station it is then placed in a bin until required for production, thus wasting time. This batch process also increases the lead times on newly ordered products.
A predetermined number of batches must be produced before the production line can be changed to respond to new orders. This not only adds to the amount of time required to deliver a product to the customer, but also increases the amount of time needed to implement a change order.
Lean manufacturing utilizes continuous flow. As a part is produced, it is moved to the next station, thus eliminating waiting time. It also allows the shipyard to be responsive to customer demand, delivering the right part at the right time in the right quantity. Since parts are only made when required, the production process can be changed to meet customer demand.
Continuous flow also helps to increase the quality of the final product by reducing the number of defects through product inspection by the workforce at each station, as well as decreasing damage that may occur while waiting to be used.
Any defect that might occur during continuous flow from the previous process is immediately obvious to the next operator.
The process is then stopped until the problem can be fixed, preventing defective parts from moving beyond the shop and improving total quality.
Top Down vs. Bottom Up Top Down and Bottom Up refer to the flow of suggestions to improve the production cycle. In a traditional Top Down process, improvements are initiated from managers and disseminated to the work force. This process tends to discourage valuable suggestions from the work force.
A Bottom Up managing style allows the workers to offer suggestions upward through management. This style tends to promote continuous process improvement.
which is one of the most important tenants of Lean Shipbuilding. It is so important that shipyards that have adopted Lean Shipbuilding have formed a department, made up of members of the workforce, to constantly evaluate the current processes and suggest improvements.
This not only pays dividends to the company, but also promotes workforce/ management lines of communication and trust.
The workforce also has a different perspective on production in Lean Shipbuilding. Rather than specializing in one process, the workforce is trained in many different areas of production.
This way they can be moved around as required. Individuals gain an under- Successfully implementing Lean principles in any manufacturing process is a daunting task. Given the current slump of the U.S. shipbuilding industry, the potential benefits of Lean Shipbuilding should be given serious consideration by managers, designers, and members of the workforce. Implementing Lean Shipbuilding constitutes an investment for the future of shipbuilding. With this in mind, the overarching goal of Lean Shipbuilding is 100 percent customer satisfaction through the elimination of waste. The five elements of the Lean Shipbuilding model are outlined as follows.
Just In Time The first of the five Lean Shipbuilding components, Just-In-Time (JIT), is defined as the right quantity and part, at the right time and place. JIT is essential to three areas of lean manufacturing, which will be discussed below: Onepiece or continuous flow, takt time, and the pull system.
One-piece/Continuous Flow One-piece flow involves identifying subassembly, unit, and part families that move through the same set of processes and creating assembly procedures for their production. Japanese shipbuilders who implemented lean principles such as this increased their productivity by 150 percent from 1965 to 1995 .
First, planners define hull divisions, then subdivide them into parts or blocks.
which in turn are divided into subblocks or subassemblies and so on.
Defining zones that are one-piece producible completes the zoning processes.
Intricate detail design simplifies onepiece construction along the production line. One-piece flow requires master scheduling execution for complete subassembly integration, as shown per Figures 2 and 3.
Takt Time Lean Shipbuilding processes introduce a pacing mechanism, called takt time, to help regulate production flow.
"Customer Demand Rate" essentially defines this takt time. The concept of takt time can be expressed as follows: Where: = Available time = Customer Demand Rate = Takt time Ship production requires a six-month to one-year duration. Although integrating takt time may be difficult, once in place, takt time simplifies monitoring of production-flow uniformity and forecasting of work packages. It also serves the planning department as a tool to evaluate how well the production process is going.
The Pull System Although Lean Shipbuilding discourages it. certain aspects of shipbuilding find large batch processing applicable.
When such an applicable occasion arises.
Lean Shipbuilding utilizes The Pull System as described above.
Utilizing the pull system, the accessibility and organization of "stamped" parts are increased. Periodically, a signal will indicate that personnel need to re-supply the parts in order to keep up with the production line demand. This way the production line "pulls" parts versus receiving "pushed" and unwanted parts.
Built In Quality Built-in quality represents the second component of the Lean Shipbuilding model. Built-in quality in a one-piece flow or continuous flow shipbuilding system is achieved through closely controlled accuracy. Each piece is inspected as it is passed to the next process, so inaccurate interim products will not flaw downstream processes.
Operational Stability Operational stability is vital to achieve a continuous-flow system such as Lean Shipbuilding. Standardized work and the 5Ss are two approaches that help to achieve this operational stability.
Standardized Work According to Storch (Storch. 1995), "Standardization is the principle of design-for-production that is likely to lead to significant improvements in productivity." This is also true in Lean Shipbuilding. Standardization occurs in a manufacturing process as well as design. Standardization in shipbuilding can be applied in several stages, from elementary components and assembled units to a complete ship design. Since the shipbuilding market is likely to continue to be characterized by varying and individual product requirements, a standard ship series may not be feasible.
Consequently, efforts at design standardization should be concentrated at the component, subassembly, block, and outfit unit levels. Standardization, as described here, is what will most likely lead to significant improvements for productivity. Standards achieve repeatability, and repeatability, along with continuous improvement, achieves higher efficiency.
Five Ss The 5Ss aim to achieve organization in Lean Shipbuilding. The 5Ss are: 1. Sort — Identify value added and non-value added procedures. Non-value added procedures should be eliminated.
2. Stabilize (orderliness) - "A place for everything and everything in its place." 3. Shine (cleanliness) - Inspection, which exposes abnormal and pre-failure conditions.
4. Standardize (create rules) - Maintain and monitor the first three Ss.
5. Sustain (self-discipline) - Maintaining a stabilized workplace is an ongoing process of continuous improvement.
Conclusion The American Shipbuilding industry is in need of change to become competitive in the international shipbuilding market. While some shipyards in the international market are able to dominate through relatively low labor rates, other yards can develop competitive niches through implementation of new methods such as Lean Shipbuilding.
Implementing modern manufacturing processes as well as management systems can help to shrink the competitive gap between the U.S. shipbuilders and the rest of the world. Lean shipbuilding offers both of these improvement opportunities.
Read Introducing Lean Shipbuilding to U.S. Yards in Pdf, Flash or Html5 edition of November 2003 Maritime Reporter
Other stories from November 2003 issue
Content
- EU Single-Hull Phase-Out Elicits I MO Scorn page: 10
- Costa Victoria in for a Facelift page: 11
- Sustainable Growth for Liner Shipping page: 11
- World's Biggest LNG Carrier Due in 2005 page: 12
- Shipbreaking in the Spotlight at ILO page: 14
- Signet Martime Inks Garrett Contract page: 16
- IZAR Enters Fast Ship Project page: 17
- TEN Signs Time Charter for Aframax Olympia page: 17
- Cruise Port Expenditure to Reach $300M page: 18
- At Sea with U.S. Maritime Security page: 20
- NY Navigation Channels: The Really Big Dig page: 25
- Kvichak Delivers for NY page: 28
- Vosta LMG signs U.S. contract for 18" Cutter Suction Dredge design page: 28
- Senesco Marine Christens New Drydock page: 29
- Workboat Annual 2003 • Great Boats of 2003 page: 30
- Natter Passes Command of Atlantic Fleet page: 41
- Introducing Lean Shipbuilding to U.S. Yards page: 42
- IBM PLM Offers New Shipbuilding Solutions page: 46
- Cosco Dalian Leads China Ship Repair Business page: 50
- China: Growing Influence in All Matters Maritime page: 52
- L'Orange at Marintec China 2003 page: 56
- Shiport China 2004: Set in Tune with the Shipbuilding Industry page: 57
- New Aluminum Marine Alloy Specification Developed page: 58
- InspecTech Launches Line of "Smart" Windows page: 62
- New CEO at Kvaerner Philadelphia page: 62
- Asheim Takes Helm of Hoegh Fleet page: 62
- New Potency in Electronic Control page: 68
- Research as the Building Block page: 70
- Knowledge Interchange page: 71
- Surface-Protection Symposium Set for Liibeck page: 78
- Xybernaut Gets Patent for Detecting Corrosion on Maritime Vessels page: 79
- LCS Hull Concept Tests Move Ahead page: 80
- Hypertherm Enters Laser Cutting Market page: 81
- E-Ship: The Paperless Trail page: 82
- Cradle Tweendecks Patent for Langh Ship page: 86
- Optimizing Feed Rates For Crosshead Diesels page: 88
- Benjamin Vickers: 175 Years & Counting page: 89
- Life Boats by Ernst Hatecke Make the Plunge page: 90
- Clean Seal Celebrates 25 Years page: 91
- Netherlands Vessel First With New Engine page: 92
- ONR To Evaluate SeaCoaster page: 92
- KMY Helps Breaks the Ice in Russia page: 97
- Astander Completes CSO Deep Pioneer Upgrade page: 97
- Rickmers Singapore Christened page: 97
- Transas Releases New Version of Engine Room Simulator page: 98
- Merseyside gets first UK escort tug simulator page: 98