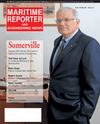
Page 40: of Maritime Reporter Magazine (October 2012)
Marine Design & Construction
Read this page in Pdf, Flash or Html5 edition of October 2012 Maritime Reporter Magazine
40Maritime Reporter & Engineering News The use of computers to solve hydrodynamics problems in shipbuilding started in early days of scientific computing ? as early as in aerodynamics and aero-space. Due to limited computing re-sources at that time, potential flow model was used in both aero- and hydrodynam- ics. However, while simulations based on Euler equations, Reynolds-averaged Navier-Stokes equations (RANSE) and most recently partially resolved Navier- Stokes equations (so-called ?large-eddy? ? LES ? or ?detached-eddy? ? DES ?simulations) have become established tools in aerodynamics, ship hydrody- namics is still predominantly simulatedusing methods based on potential flow. There are good reasons for this:The presence of free surface with its arbitrary deformation and break- ing makes the simulation difficult and commercial software that can perform coupled simulation of flow and motion of floating bodies has only recently be- come available. The computational effort for simu- lations based on Navier-Stokes equa- tions is several orders of magnitude larger than for methods based on po- tential theory. Methods based on RANSE have been used in research institutions for marineapplications for quite a while, but exten- sive use of such methods only recently become a commonplace. In addition tothe need to account for flow features which potential flow model does not cover (turbulence, viscous effects, break- ing waves etc.), the availability of inex- pensive computer clusters and easy-to-use commercial software has greatly facilitated this trend. Also, new generations of engineers are being edu-cated in computational fluid dynamics(CFD) and are thus eager to adopt thesenew simulation methods. Regular con- ferences and workshops dedicated to the use of CFD in marine engineering arealso influencing this trend (e.g. NuTTS ?Numerical Towing Tank Symposium, held every year and for the 15th time in 2012).Although some people claim that sim-ulations will replace experiments com- pletely, we believe this will not happen any time soon. One reason is that CFD still uses models that need to be validated for each new application area (like turbu- lence and two-phase flow or phase change models). Also, some simulations ? while in principle possible ? would take too long to be performed with sufficient accuracy so experiments are the more ef- ficient approach (like for maneuvering and sea-keeping problems). The combi- nation of the two approaches is the best way towards optimum products: simula- tion can be used in early design stagesand provides a wealth of information that helps understand the physics of the prob- lem, while well-designed and instru-mented experiments are needed to validate CFD tools. However, there are many problems that can be solved today with CFD very effi- ciently with a satisfactory accuracy. Below are the elow results of several re- cent validation studies, before discussing industrial applications and future trends.State-of-the-Art in Commercial CFD All results presented here were ob-tained using new-generation software STAR-CCM+ from CD-adapco. It is based on finite-volume method and can use control volumes (CVs) of arbitrary polyhedral shape. This allows handling of complex geometries and changes in CV-topology since there are no limita- tions to the number of faces one CV can have. A range of turbulence models, an interface-capturing scheme for free sur- faces, a cavitation model, moving and overlapping grids, sliding surfaces and a dynamic fluid-body interaction (DFBI)model are also available. Compressibil- ity effects in both liquid and gas phase are accounted for. The software also con- tains a CAD-modeler and repair tools sothat the body of flow domain can easily be obtained even if the ship is defined by the shell of hull surface. The computa- tional grid defining CVs is created fully automatically and the user can prescribethe size of control volumes using line, surface and volume control parameters. The whole process from CAD to solutioncan easily be automated and saved in templates so that non-experts can per- form parametric studies once the simula-tion is set up by a knowledgeable engineer. This also facilitates the use of optimization software (like FRIEND- SHIP-Framework from Germanischer Lloyd) since it can automatically vary geometry and other parameters and per- form CFD-simulations by executing tem- TECHNICAL FEATURE CAD/CAM Virtual Towing Tank State-of-the-Art and Future Trends By Boris Bucan & Marta Pedi?icBuca, BrodarskiInstitut, Zagreb, Croatia; Jaehyoung Jun, CD-adapco, Seoul, Korea; and MilovanPeric, CD-adapco, Nürnberg, Germany Fig. 1: Predicted wave pattern around KCS-hull at Froude-number 0.26 and comparison between pre- dicted (red) and measured (blue) wave profiles along three longitudinal cuts. Fig. 5:Computational grid on the surface of a patrol boat. Fig. 2: Predicted profile of wetted hull surface for the KCS at Froude-number 0.26: simulation (red line) and experiment (blue dots).Fig. 3: Predicted wave pattern around DTMB-hull at Froude-number 0.28 and comparison between pre- dicted (red) and measured (blue) wave profiles along three longitudinal cuts. MR#10 (34-41):MR Template 10/4/2012 11:01 AM Page 40