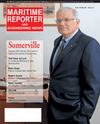
Page 41: of Maritime Reporter Magazine (October 2012)
Marine Design & Construction
Read this page in Pdf, Flash or Html5 edition of October 2012 Maritime Reporter Magazine
October 2012www.marinelink.com 41plates with replaced geometry. More in- formation about CFD that applies to mostcommercial software can be found in Ferziger and Peric (2003, 2008).There are other software tools on the market that cover most of the above- named features to a varying level of detail and a new user is advised to check all op- tions to find the best tool for particular purpose.Validation of CFD for Marine ApplicationsThe authors of this article were in-volved in several recent validation stud- ies. Results from prediction of resistance,trim and sinkage of KCS-hull were pre-sented at the Gothenburg-workshop in 2010 and will not be repeated in detailhere (see Enger et al, 2010).We only note that the trend with varying Froude-num- ber was well predicted for all three quan- tities, and that systematic grid refinement was used to demonstrate convergence to- wards a grid-independent solution. In particular, the resistance was predicted within 1% of the measured value on the finest grids (comprising around 3 million CVs) for all three hulls investigated at the workshop. Here only the results for wave profiles are given which were not pre- sented at the workshop. Results from other contributors can be seen in Work- shop Proceedings (Larson et al, 2010).Figure 1 shows predicted wave pattern around KCS-hull (KRISO ContainerShip) at Froude-number 0.26 (fixed posi- tion) and comparison between predictedand measured wave profiles along three longitudinal cuts. The simulation is per- formed in model scale with hull length of7.2786 m, draft of 0.34177 m (230 m and10.8 m in full size, respectively) and speed of 2.196 m/s. The solution domain extended to about 1.5 hull lengths behind, below and sideways and around 1 hull length above and ahead of ship. The grid had around 2 million control volumes and the computing time was about 5 hours on 8 processors. In these simula-tions wave damping with an exponential growth of resistance to vertical fluid mo- tion was applied within a zone 7 m wide along inlet, side and outletboundary. Figure 2 shows the profile of wetted hull surface. The agreement between ex- periment and simulation is rather good.This information and the distribution of pressure and shear stress along hull sur- face which simulation also provides ? in addition to velocity distribution around the hull ? allows engineers to judge per- formance of different hulls in optimiza- tion studies. Figure 3 shows the wave pattern and profiles for the DTMB-hull (David Taylor Model Basin, Hull No. 5415) at Froude-number 0.28, fixed po- sition with specified sinkage and trim. The model scale was used again for bet- ter comparison with experiments, with hull length being 5.72 m and draft 0.2477m (142 m and 6.15 m in full size, respec-tively) and speed of 2.097 m/s. The size of solution domain and wave damping zone relative to hull length as well as the number of grid points and computingtime were similar to those for the KCShull. The agreement between experiment and simulation is as satisfactory for this hull type as for the container vessel. Ac- curate prediction of free surface defor- mation (wetted hull surface, waves) is MR#10 (34-41):MR Template 10/4/2012 11:20 AM Page 41