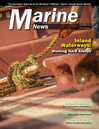
SubM Debut Now Set for February 2016
Outsourcing, E-Solutions Help Mariners “Say What You Mean, Mean What You Say, and Prove it.”
The perennial “Year of Subchapter M” has been kicked forward again, this time to February 2016. That means that the clock is now ticking loudly for those towing operations that have yet to climb onboard the safety train. Quality operators see standardized safety practices as a way of leveling the playing field, integral to maintaining the health and profitability of their fleets, and key to winning business from quality customers.
Subchapter M will be a phased-in over a period of years. It’s not as much time as you think. If you haven’t started yet, you are already running late, say industry observers, and it’s important to get it right. The obvious reason is your operation will be dead in the water if you don’t.
Get In the Game
Roughly 5,000 uninspected vessels will be affected by Subchapter M, some of which are members of the AWO, which mandates that all members within a year of joining, be certified on its own U.S. Coast Guard-approved SMS, the Responsible Carrier Program (RCP). While they wait for SubM to wend its way through the regulatory process, operators can get SMS-certified by going either with RCP and IMO’s ISM program.
ISM certification exempts holders from Subchapter M. It focuses on safety requirements and practices, and less on vessel type. RCP, by contrast, may need some tweaks to meet SubM equivalency, but was designed for the domestic towing industry. AWO will accept ISM certification from members, but only if they implement the industry-specific features of RCP. Widely seen as the driving force behind Subchapter M, AWO’s RCP program “is the gold standard” in the industry, says Helm Operations CEO Ron deBruyne. In June, the USCG gave AWO assurances that its revised program will pass muster as an alternative to SubM (with minimal tweaks likely once the rule is finalized). AWO members have until January 2016 to implement those changes or lose their RCP certification. A series of AWO explanatory workshops on the changes bring members up to speed. Once Subchapter M goes live, operators can get certified under that program, RCP or ISM, or take the USGS option, which does not currently require an SMS, but requires annual Coast Guard inspections. Each program specifies an approved source for auditing.
In 2013, citing numbers submitted to the Coast Guard by the American Bureau of Shipping (ABS) and the Towing Safety Advisory Committee (TSAC), it was estimated that the cost to install an SMS could reach $2.9 million for an average company. Smaller operators can feel overwhelmed, but it doesn’t have to be that way. Subchapter M, RCP, ISM and other SMS plans are all designed to be scalable to fit the needs of every operation, be it a one-boat outfit or a fleet of 100. It can be as simple or sophisticated as it needs to be. Having a safety compliance officer is not required, although larger operations will probably need them. Fortunately, SubM assistance abounds.
Tug and Barge Solutions
Gulf Coast Tugs does it all on paper, teaming with Tug and Barge Solutions (TBS), run by Pat Folan, a former tug owner whose partner runs a two-vessel operation. That combination allows him to both draw on that expertise and field-test his processes before taking them to clients.
TBS helps to write the TSMS plan, does an annual internal audit, and provides clients with all the manuals, forms and reports they’ll need up front, and then, based on the information received, sends a fresh batch every few months to use in the upcoming weeks. That includes daily task lists and credentials the crew has to meet, as well as reminders for regular safety meetings and schedules for fixing any nonconformities. Data collected onboard is input into those forms, given to Hebert, who checks it and sends it back to TBS every two weeks during crew changes. TBS processes and stores the data on a cloud, and provides feedback. Ken M. Hebert, President & CEO of Gulf Coast Tugs, says the time lag has never been an issue. “We’re getting it done.”
Folan packages everything needed to ensure safe operations, including an SMS, record-keeping system, 24-hour support, first aid and Hazcom manuals, training materials, vessel response and security plans, OSHA regulation guidance etc., into a bright orange, floatable, tote-able plastic box he calls The Safety Block. “I rely heavily on Pat; he’s our third-party safety guy. He is there to coach me, and tell me what I need to do. I consider him an employee of Gulf Coast,” says Hebert.
MarineCFO
To support clients who want automation, Folan partners with Marine CFO, which offers upwards of 70 modules coverings all aspects of various maritime operations and requirements, and targets affordability and scalability for small to mid-size operators. The focus is on ease-of-use and simplicity, says Dean Shoultz, MarineCFO CTO. “Our software is scalable and configurable. Regardless of size of fleet and operation, our cloud-based system will support it. It’s just a matter of throwing switches to get simpler or more complicated.”
MarineCFO partners with TMS because, “They bring [Germanischer] Lloyd and ABS quality down to the masses,” says Shoultz. “We thought if we took their domain-level knowledge and coupled that with our technical expertise, we’d be able to add a lot of value. By digitizing their domain expertise, they took us to another level.” To whatever the degree to a client wants to automate, MarineCFO probably has the solution in its library of modules, first introduced to the marine industry in 2006. The software is Microsoft-based, utilizing Web Services, Office and SQL Server, and runs behind a corporate firewall or as a native .NET 2.0 web application.
The company offers web-based applications that feature 100% configurable and dynamic interfaces that are easy to use for inputting, collecting, processing and transmitting data. The application travels with the laptop via a roaming user profile, and has sections for the captain, maintenance engineer and electrician. The database can quickly produce any data requested by an auditor. Specific to the needs of vessels plying the inland coastal waterways, MarineCFO supports functions such as waterways management, materials and hazardous materials management and billing.
Helm Operations
Noting the adage, “say what you do, do what you say, then prove it,” Helm CEO Ron deBruyne points out that making sure safety meetings, checklists, planned maintenance and inspections are done, is a “critical piece of being compliant.”
“This is where an electronic system can assist, by keeping track of the different things and daily tasks that need to be done, by sending messages to the appropriate parties, and organizing data,” says deBruyne, whose company sells Helm CONNECT, a database-centered solution that automates tracking of compliance and preventative maintenance.
It’s important to get the buy-in of frontline staff, he says. Tell them, “Here is what you need to do today,’ then you need an escalating system of notification that lets the responsible parties know what needs to be done, and what’s not done.”
Paper systems can’t match computers for data retrieval. They generate “thousands of pieces of paper you have to deal with – if one piece goes missing there is no way to get it back. Electronic systems have the ability to sort, filter and summarize all those thousands of piece of data any way the auditor wants.” The typical two-week delay in processing paper reports is another problem if the boat is not doing what it is supposed to do, warns deBruyne.
“Paper is passive, it can only record what people have noticed; electronic is active. You can just “set it and forget it’.” Helm CONNECT was developed to address all these issues, with a focus on simplicity. “We want to be the Apple of the industry. You should be able to buy a piece of software and start to use it without months of training and implementation - the hidden costs of software.”
Since CONNECT is web-based, users just need a laptop, or a tablet or smart phone, running on either Chrome or Microsoft Internet Explorer 11. The software is hosted in Amazon Web Services. Clients can set up their templates, inspections, checklists and routines themselves. “It’s all drag and drop,” says deBruyne. “To my mind, the happy medium for smaller operations is to work with an outsourced safety manager, but [use] an electronic compliance system,” says deBruyne. Helm partners with sister company Safety Management Systems, LLC (SMSLLC) to help clients build their SMS. Helm’s focus on the simplicity of the end-user experience marries well with SMS objectives for ease-of-management system understanding and ongoing implementation, says William Mahoney, SMSLLC Director of Safety Management Systems. Both companies are owned by ClassNK America. SMSLLC will jointly host a series of Subchapter M workshops with ClassNK America starting in late fall.
ClassNK America, along with other USCG-approved Classification Societies, will be the only auditors with pre-approved subM audit authority.
American Bureau of Shipping (ABS)
With the help of several other ABS units, ABS and its independent sister company ABS Group, which provides non-class services, offer a virtual one-stop shop when it comes to safety management and compliance. With presence in every major US shipyard, and over 30 locations in the U.S. staffed with over 300 surveyors and auditors, and more than 200 engineers and naval architects, ABS offers a wide range of services needed to help operators achieve and maintain compliance when Subchapter M regulations go into effect.
“We are the only company out there that offers a totality of solutions. We can do the class, the third-party inspections, set up an ISM – when we can’t do something it’s because we are try to maintain independent status and not be auditing out own work,’’ says Robert Whitney, manager, marketing and communications, ABS Americas. Combining class with an ABS certification of a vessel to the ISM code will meet subM requirements. In addition, ABS Rules have been appointed the default standard under Subchapter M for new towing vessels. Combined with third-party inspection service provided by ABS Group, owners can demonstrate compliance.
ABS Nautical Systems (NS) Fleet Management Software (FMS) has traditionally supported ISM and TSMS compliance. The NS5 Enterprise Safety Management suite provides a standardized method both on and offshore for recording and analyzing safety-related data collected across a fleet, and includes an HSQE Manager and an Internal Inspection Manager.
The NS group is developing a version of its FMS to support Subchapter M in the form of a slimmed down, simplified dashboard, which will support all subM regulations, streamline data entry and generate compliance reports, using subscription-based pricing. The group will provide SubM implementation support and training, including informational seminars to bring industry up to speed on SubChapter M requirements.
Baker, Lyman & Co., Inc.
Baker, Lyman’s software offering in the subM space is the CORSAIR Towing Vessel Record application, CORSAIR TVR v.2., which is said to be an easy-to-use, scalable TVR that meets or exceeds safety, assessment, inspection, training, recordkeeping and other documentation requirements. It provides users of Baker Lyman’s navigation, scheduling, safety, training, compliance and planned maintenance assessments with pre-formatted vessel, barge, and crew log entries, VGP permit tracking, and enhanced daily logging functions. If it can be tracked – CORSAIR tracks it – all without a sheet of paper.
The latest version has enhanced SIRE and RCP reporting capabilities, while other regulatory-required recordkeeping processes have been added, such as VGP and ballast reporting. The SQLServer-based system requires a Pentium-grade processor, Windows XP or later and 4GB RAM. It supports IE 8, Chrome 3.0, Safari 4.0 and Firefox 3.6 browsers. Baker Lyman also offers its TSMS Transition Program, and RCP-TSMS Transition Program, both of which assist tug owners in becoming Sub-Chapter M- compliant prior to the “final rule.” It also provides internal third-party safety audits of SMS.
Paper or Plastic
The classic choice of “paper or plastic” – as in computerizing some or all aspects of the program – may seem obvious, but SMS can be done on paper. Regardless of platform choice, a first good step is the Towing Vessel Bridging Program, launched in 2009 by the AWO and Coast Guard to prepare industry for the forthcoming regulations. To date, it has completed over 6,000 examinations.
From there operators should turn to their own operator’s manual and procedures, the foundation upon which the SMS is built. While generic SMS forms and consulting services can help, constructing the SMS is the one area that operators will need to fully immerse themselves and their crews in, as the plan has to reflect its specific policies and rules. For companies that don’t have the manpower or mind space to spend tracking their safety tasks and compliance, outsourcing is can be a godsend. Let’s get started!
(As published in the September 2015 edition of Marine News - http://magazines.marinelink.com/Magazines/MaritimeNews)
Read SubM Debut Now Set for February 2016 in Pdf, Flash or Html5 edition of September 2015 Marine News
Other stories from September 2015 issue
Content
- Insights: Tracy Zea, Director-Government Relations, WCI page: 12
- Spotlight: Cyber Risk Management page: 18
- Emerging Tech of Online Education and Training page: 24
- Boatbuilding Gone Bad page: 26
- New Risks Moving Crude Oil by Rail page: 28
- SubM Debut Now Set for February 2016 page: 32
- Get Started! Benefits, Advice Abound for SMS Laggards page: 38
- Marine Sanitary Devices: Size Matters page: 39