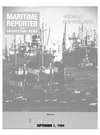
Murdock And Hunt/Leslie Use Computer To Design 'Compliant' TLP Coupling
Murdock Engineering Co., Dallas, Texas, and finite element engineering consultant Hunt/Leslie/ Associates have used a computer to design the flexible 'controlled yielding' coupling for the world's first deepwater tension leg oil platform (TLP).
The coupling is the critical connection between the platform hull and anchoring tubular lines that keeps the multimillion-dollar 53,500-ton TLP horizontal in severe North Sea weather.
The primary design requirement was to reduce the bending moment in the mooring system and protect the lines from fatigue.
The thin tubular tethering lines replace the traditional rigid platform support structure. The system is designed to operate in all weather and operating conditions.
In addition to minimizing bending moment, the final design had to support non-symmetric loads and allow angular deflection as the buoyant platform shifts with the current to create tension on one side of the coupling and compression on other, as well as vertical tension due to buoyancy.
Using axisymmetric elements in the ANSYS finite element program, Hunt/Leslie decided redesign of the segmented retainer ring—the metal ring that holds the upper backflange—would be sufficient to meet North Sea application requirements.
The Murdock flexjoint system consists of alternating laminates of metal and rubber which serve as a pressure seal and load-carrying bearing. External loading is supported by controlled compression of the seal elastomer.
The bearing design can carry an axial tension load of almost 7 million pounds in each bearing at angles to 16.6°, control lateral platform motion and prevent heave or vertical motion. In heaviest seas, the coupling will allow lateral platform movement as much as 79 feet from its neutral position.
Murdock and Hunt/Leslie used the ANSYS finite element engineering analysis computer program to evaluate stresses and displacements in the final design of the major metal flexjoint bearing structure. Hunt/Leslie found that including friction in gap elements between mating surfaces increased stress levels of a factor of 10 percent over frictionless analysis.
Using ANSY's axisymmetric elements, Hunt/Leslie was able to complete the critical final bearing design several months prior to completion of the three-story-high test structure.
For further information, Circle 28 on Reader Service Card
Other stories from September 1984 issue
Content
- Symon Appointed New Director Of Tankers At Stolt-Nielsen page: 5
- SOFEC Awarded NavSea Contract For Offshore Mooring Terminal page: 5
- Metric Constructors Win $3.3-Million Contract page: 6
- Western Gear To Build And Sell Rademakers Epicyclic Transmissions page: 6
- I MO AB Of Sweden Offers New Products Literature page: 6
- Sperry Gets $62.8-Million Navy Contract For Frigate Combat Systems Work page: 6
- New HEET Fuel Additive Saves Time And Money By Preventive Maintenance page: 6
- Fairbanks Morse Taking Major Steps To Improve All Aspects Of Customer Services Worldwide page: 7
- Two Key Appointments Announced By Halifax Industries page: 7
- A.J. McAllister Sr. page: 8
- S.S. United States To Auction Contents Prior To Total Renovation page: 8
- Imi-Tech Offers Catalog Of Insulating Products For Marine Applications page: 8
- High-Speed Ferry For Hong Kong Owner Launched At Vosper Thornycroft Yard page: 9
- Marinette Marine Lays Keel For Second Mine Countermeasure Vessel page: 9
- Maritime Innovation — Practical Approaches '84 International Symposium page: 10
- NKK Completes World's First Offshore Steel/Concrete Drilling Platform page: 12
- Manson Construction Builds Pacific Northwest's Heftiest Floating Crane page: 12
- Krupp Shipyard In Duisburg Delivers Two Harbor Tugs To Guinea page: 14
- NKK To Build Floating Offshore Production Unit For Norwegian Consortium page: 14
- Van Houten To Head New Parsons Brickershoff Marine Facilities Unit page: 14
- Lykes Gets Title XI Guarantee To Upgrade Fleet Operations page: 15
- USP&I Home Office To New York Area— Other Changes Announced page: 15
- American Marine Gets $390,000 Contract For Two Cutterhead Dredges page: 15
- MARINE SALVAGE page: 16
- Crowley Named President Of Newly Organized States Africa Line page: 18
- Simplex Gets $5.7-Million MarAd Contract To Supply Petroleum Transfer System page: 18
- General Dynamics Quincy Yard Will Build Four Containerships For USL At Cost of $341 Million page: 18
- Scripps Institution Acquires Another Research Vessel page: 18
- RDI's Satcom I Communications System Approved By INMARSAT page: 18
- American Transport Asks Title XI On $17-Million Barge Conversion Work page: 19
- Canter Named President Of At-Sea Incineration page: 19
- Coast Guard Orders Schottel Jet Thruster page: 19
- SMM '84 International Ship, Machinery, and Marine Technology Trade Fair page: 20
- Tenn-Tom Waterway Project Nearing Early Completion page: 20
- BP And Harland And Wolff Forming Joint Venture For $145-Million SWOPS Project page: 21
- Naval Ship Maintenance & Modernization/Affordability page: 22
- The "Ultimate" Compact SSB page: 23
- IBM Appoints Marine Management Systems As Authorized Dealer page: 25
- Twin City Shipyard Lays Keel For Gulf Coast Trailing Dredge page: 26
- Pearlson Begins Construction Of World's Largest Ship Transfer System page: 26
- Screw Compressors Improve Air Conditioning Reliability page: 27
- NASSCO Receives Exxon Contract For Two Alaska-Class Tankers page: 28
- Tacoma Boat Division Gets $210,000 Contract To Build Propeller Hub Assembly page: 28
- AMMCO Licensed To Market O&K Dredging Bucket And Cutting Wheels page: 32
- Westinghouse Electric Awarded $2-Million Navy Contract For Frigate Study page: 32
- John Cave Appointed Vice President For Boland & Cornelius page: 33
- Norwegian Caribbean Acquires Royal Viking Line For $240 Million page: 33
- Marinette Marine Corporation Gets $24~Million Navy Contract To Build Six Yard Patrol Craft page: 34
- New Drydock At Halifax Shipyard Operating At Close To Capacity page: 34
- Stephens-Adamson Wins Ship Unloading System Orders Worth $12 Million page: 35
- Ice-Strengthened Ship Chartered By Navy's MSC From Central Gulf Lines page: 35
- Penn Ship Awarded Navy Contract For Overhaul And Maintenance Of Frigate page: 35
- John Deere Developing Family Of Rotary Engines page: 35
- Unique High-Speed Catamaran Delivered By Nichols Brothers page: 36
- Specialized Support Vessel 'Anfitrite' Acquired By O.D.S. Italia S.P.A. page: 36
- Moss Point Awarded $3.6-Million To Build 15 Barges For U.S. Navy page: 36
- WEST GERMAN SHIPBUILDING page: 38
- CORE Canadian Offshore Resources Exposition page: 38
- Meyer Named Assistant Vice President-River Area Of National Marine Service page: 43
- New Harbor Navigation System Designed To Increase Operating Revenue And Safety page: 44
- Murdock And Hunt/Leslie Use Computer To Design 'Compliant' TLP Coupling page: 45
- Samsung Wins $45-Million Contract To Build Huge Bulker For Australian Firm page: 46
- WABCO Fluid Power Adopts Worldwide Sales And Marketing Strategy page: 46
- $79-Million Coast Guard Contract Awarded to Bollinger Shipyard page: 46
- New Busiship™ System Brochure Available From Nav-Com page: 46
- Rose Named Vice President Of Mechanical Equipment's Marine Products Group page: 47
- MSC Forms New Unit To Oversee Operations Of Fast Sealift Ships page: 47
- Independent Tests Show Drew Ameroid's Amergize® Cuts Fuel Consumption page: 47
- Sulzer RTA Engines Will Power Two Containerships Building In Germany page: 48
- MonArk Delivers Fire Boat To Memphis Fire Department page: 48
- Penn Ship Provides Emergency Repairs For Two Foreign Ships page: 48
- Smith Berger Marine Names Two East Coast Distributors page: 48
- Sperry Opens New Facility In Panama City Beach, Fla. page: 51
- AMPS Appointed As Service Facility For MaK Diesels page: 52
- Halifax Shipyard Completes Major Damage Repair Contract page: 52
- Big Towing/Supply Vessel Launched At Moss Point Marine page: 52
- Serck Evaporators Installed In USSR Fish Factory Ships page: 53
- Third USN Rescue/Salvage Ship Launched At Peterson Builders page: 54
- USS Seamless Pressure Vessels Detailed In New Catalog page: 57
- ASRY Completes $3-Mlllion Overhaul Of Mobile Offshore Jackup Drilling Rig Dana page: 57
- Todd Awarded $10-Million In Contracts By Australia For Technology Transfer page: 58
- First Oceangoing Sail-Assisted Bulker Delivered By NKK page: 63