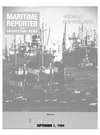
Independent Tests Show Drew Ameroid's Amergize® Cuts Fuel Consumption
—Results Available Independent laboratory tests of Amergize™ deposit modifier/combustion improver have proven a significant reduction in specific fuel consumption, carbon deposits, exhaust smoke levels, and metallic deposits in a test engine operated on a residual oil blend containing high levels of carbon residue, vanadium, sodium and sulfur. Drew Ameroid® Marine, producer of chemical products and technical services through its worldwide network, introduced Amergize earlier this year.
For the purposes of the fuel additive tests, an instrumented test engine was selected to be used with a poor burning fuel having high contaminant levels. These conditions allowed short-term testing with maximum deposit and corrosion development.
The engine was operated at conditions that would produce exhaust temperatures above vanadium-compound deposit melting points (in excess of 537 degrees C).
Three tests were completed: 1) Baseline test using neat fuel (no additive), 2) Amergize test used at concentrations of 1:250 or one liter additive to 250 liters of fuel, an overly rich ratio and 3) Amergize test used at concentrations of 1:2000 or one liter additive to 2,000 liters of fuel, within the recommended dosage range.
The engine was fully instrumented to monitor engine speed, power output and pressure and temperatures throughout the lubricating, cooling, intake and exhaust systems.
Fuel consumption rate was determined using an automated weight system which measured the amount of time required for the engine to ccr^UIne tnree pounds of fuel. Smoke density was measured by the Bosch method every two hours, and all other data was recorded every hour.
Heat exchangers, utilizing the engine cooling water as a heat source, were used to heat the fuel. A fresh charge of oil was used for each test, For the tests, a petroleum product containing asphaltenes extracted from residual fuels was used. The asphaltenes were diluted with diesel fuel to meet properties required for use in the diesel test engine. Tests on a sample obtained prior to purchase indicated a cetane number between 45 and 50, which indicated that the fuel probably did not con- tain any cracked stocks.
In the Brake Mean Effective Pressure (BMEP) measurement, showing how much engine power is produced, the engine operated most stably during the 1:250 dosage test indicated by the relatively constant, highest level carrot symbols. In the Brake Specific Fuel Consumption (BSFC) measurement, the lowest and most desirable rate is shown by the additive test symbols, and the highest, by the baseline. Smoke levels, using the BOSCH Method, giving capacity of exhaust emissions, were likewise lowest when using 1:250 additive and highest during the baseline test.
These are significant savings in fuel cost, since a specific fuel consumption decrease of only one percent covers the treatment cost. Added benefit of reduced metallic deposits and lower carbon residue increase the cost savings.
Carbon deposits, fuel consumption and smoke decreased as the quantity of Amergize increased. The results prove that combustion was more complete when using Amergize.
Metallic deposits were at a minimum when using the additive at a ratio of 1:2000. An optimum dosage, therefore, for increased combustion with reduced metallic deposits can be determined to meet specific operator needs.
For further test data and information on the Amergize deposit modifier/combustion improver, Circle 37 on Reader Service Card
Other stories from September 1984 issue
Content
- Symon Appointed New Director Of Tankers At Stolt-Nielsen page: 5
- SOFEC Awarded NavSea Contract For Offshore Mooring Terminal page: 5
- Metric Constructors Win $3.3-Million Contract page: 6
- Western Gear To Build And Sell Rademakers Epicyclic Transmissions page: 6
- I MO AB Of Sweden Offers New Products Literature page: 6
- Sperry Gets $62.8-Million Navy Contract For Frigate Combat Systems Work page: 6
- New HEET Fuel Additive Saves Time And Money By Preventive Maintenance page: 6
- Fairbanks Morse Taking Major Steps To Improve All Aspects Of Customer Services Worldwide page: 7
- Two Key Appointments Announced By Halifax Industries page: 7
- A.J. McAllister Sr. page: 8
- S.S. United States To Auction Contents Prior To Total Renovation page: 8
- Imi-Tech Offers Catalog Of Insulating Products For Marine Applications page: 8
- High-Speed Ferry For Hong Kong Owner Launched At Vosper Thornycroft Yard page: 9
- Marinette Marine Lays Keel For Second Mine Countermeasure Vessel page: 9
- Maritime Innovation — Practical Approaches '84 International Symposium page: 10
- NKK Completes World's First Offshore Steel/Concrete Drilling Platform page: 12
- Manson Construction Builds Pacific Northwest's Heftiest Floating Crane page: 12
- Krupp Shipyard In Duisburg Delivers Two Harbor Tugs To Guinea page: 14
- NKK To Build Floating Offshore Production Unit For Norwegian Consortium page: 14
- Van Houten To Head New Parsons Brickershoff Marine Facilities Unit page: 14
- Lykes Gets Title XI Guarantee To Upgrade Fleet Operations page: 15
- USP&I Home Office To New York Area— Other Changes Announced page: 15
- American Marine Gets $390,000 Contract For Two Cutterhead Dredges page: 15
- MARINE SALVAGE page: 16
- Crowley Named President Of Newly Organized States Africa Line page: 18
- Simplex Gets $5.7-Million MarAd Contract To Supply Petroleum Transfer System page: 18
- General Dynamics Quincy Yard Will Build Four Containerships For USL At Cost of $341 Million page: 18
- Scripps Institution Acquires Another Research Vessel page: 18
- RDI's Satcom I Communications System Approved By INMARSAT page: 18
- American Transport Asks Title XI On $17-Million Barge Conversion Work page: 19
- Canter Named President Of At-Sea Incineration page: 19
- Coast Guard Orders Schottel Jet Thruster page: 19
- SMM '84 International Ship, Machinery, and Marine Technology Trade Fair page: 20
- Tenn-Tom Waterway Project Nearing Early Completion page: 20
- BP And Harland And Wolff Forming Joint Venture For $145-Million SWOPS Project page: 21
- Naval Ship Maintenance & Modernization/Affordability page: 22
- The "Ultimate" Compact SSB page: 23
- IBM Appoints Marine Management Systems As Authorized Dealer page: 25
- Twin City Shipyard Lays Keel For Gulf Coast Trailing Dredge page: 26
- Pearlson Begins Construction Of World's Largest Ship Transfer System page: 26
- Screw Compressors Improve Air Conditioning Reliability page: 27
- NASSCO Receives Exxon Contract For Two Alaska-Class Tankers page: 28
- Tacoma Boat Division Gets $210,000 Contract To Build Propeller Hub Assembly page: 28
- AMMCO Licensed To Market O&K Dredging Bucket And Cutting Wheels page: 32
- Westinghouse Electric Awarded $2-Million Navy Contract For Frigate Study page: 32
- John Cave Appointed Vice President For Boland & Cornelius page: 33
- Norwegian Caribbean Acquires Royal Viking Line For $240 Million page: 33
- Marinette Marine Corporation Gets $24~Million Navy Contract To Build Six Yard Patrol Craft page: 34
- New Drydock At Halifax Shipyard Operating At Close To Capacity page: 34
- Stephens-Adamson Wins Ship Unloading System Orders Worth $12 Million page: 35
- Ice-Strengthened Ship Chartered By Navy's MSC From Central Gulf Lines page: 35
- Penn Ship Awarded Navy Contract For Overhaul And Maintenance Of Frigate page: 35
- John Deere Developing Family Of Rotary Engines page: 35
- Unique High-Speed Catamaran Delivered By Nichols Brothers page: 36
- Specialized Support Vessel 'Anfitrite' Acquired By O.D.S. Italia S.P.A. page: 36
- Moss Point Awarded $3.6-Million To Build 15 Barges For U.S. Navy page: 36
- WEST GERMAN SHIPBUILDING page: 38
- CORE Canadian Offshore Resources Exposition page: 38
- Meyer Named Assistant Vice President-River Area Of National Marine Service page: 43
- New Harbor Navigation System Designed To Increase Operating Revenue And Safety page: 44
- Murdock And Hunt/Leslie Use Computer To Design 'Compliant' TLP Coupling page: 45
- Samsung Wins $45-Million Contract To Build Huge Bulker For Australian Firm page: 46
- WABCO Fluid Power Adopts Worldwide Sales And Marketing Strategy page: 46
- $79-Million Coast Guard Contract Awarded to Bollinger Shipyard page: 46
- New Busiship™ System Brochure Available From Nav-Com page: 46
- Rose Named Vice President Of Mechanical Equipment's Marine Products Group page: 47
- MSC Forms New Unit To Oversee Operations Of Fast Sealift Ships page: 47
- Independent Tests Show Drew Ameroid's Amergize® Cuts Fuel Consumption page: 47
- Sulzer RTA Engines Will Power Two Containerships Building In Germany page: 48
- MonArk Delivers Fire Boat To Memphis Fire Department page: 48
- Penn Ship Provides Emergency Repairs For Two Foreign Ships page: 48
- Smith Berger Marine Names Two East Coast Distributors page: 48
- Sperry Opens New Facility In Panama City Beach, Fla. page: 51
- AMPS Appointed As Service Facility For MaK Diesels page: 52
- Halifax Shipyard Completes Major Damage Repair Contract page: 52
- Big Towing/Supply Vessel Launched At Moss Point Marine page: 52
- Serck Evaporators Installed In USSR Fish Factory Ships page: 53
- Third USN Rescue/Salvage Ship Launched At Peterson Builders page: 54
- USS Seamless Pressure Vessels Detailed In New Catalog page: 57
- ASRY Completes $3-Mlllion Overhaul Of Mobile Offshore Jackup Drilling Rig Dana page: 57
- Todd Awarded $10-Million In Contracts By Australia For Technology Transfer page: 58
- First Oceangoing Sail-Assisted Bulker Delivered By NKK page: 63