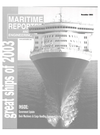
great ships of 2003
Name White Rose Builder Samsung Heavy Industries Co., Ltd.
Owner Husky Oil Operation Type FPSO For many years now, contracts for ships and floating units to operate in an offshore environment have been much-prized value-added goals at Samsung. These include not only shuttle but drill ships, floating storage and offloading units (FSOs), with their derivative production types (FPSOs), crane ships, and various types of floating and fixed platforms. Some of the more interesting ships that have been created here have included a trio of deepwater drill ships for Reading & Bates capable of working in water depths down to 3000m, the 312,500 dwt FPSO Bonga for operating off Nigeria, and the Saibos FDS, a pipelayer/crane vessel with a jib capacity of 6()0tonnes. However, today, one of the most interesting ship-shape designs currently on order at Samsung is a very special FPSO planned to operate in the White Rose field off the eastern coast of Newfoundland, Canada. This is a particularly hazardous and inhospitable area of the world, known both for storms, but more importantly it is also in an iceberg zone. The most recent new production unit to be stationed there was the Terra Nova FPSO, designed by Halliburton Brown & Root, and completed by Daewoo in 1999, and the operator of the new ship. Husky Oil, was seeking a somewhat similar concept, which was based in 'virtual drill-ship' lines using five azimuthing thrusters to maintain position. However, Samsung's design team proposed a different solution altogether, which it claims is more cost-effective.
This is extrapolated from a successful shuttle tanker hull conceived by the yard for several Norwegian owners, including Ugland, and employing twin conventional CP propellers, allied to a submerged turret loading arrangement.
Lengthy discussions took place with the owner which was prepared to pay extra for good safety features, while the hull itself was model tested at the Oceanic Consulting basin in St John's, Newfoundland.
Including slop tanks of 5800 cu. m., the total storage capacity will be 148,000 cu. m., and the bottoms of these tanks, along with the water ballast tanks and external shell will be protected by sacrificial anodes with a 10-year lifespan. For offloading processed oil to a shuttle tanker over a stern line, three 4,000 cu. m./hr. cargo pumps will be installed.
One of the most important requirements of a floating unit in this part of the world is an ability to move off-station as fast as possible in the event of any iceberg threat. If this becomes necessary, the submerged turret mooring system will be disconnected, together with the associated oil loading lines, and the twin 10,600 bhp (MCR) mediumspeed diesel engines (burning diesel oil) will give the ship a service speed of 12 knots (at 90% MCR.
including 15% power margin and a design draft of 18 m). For normal ship's services, electrical power will be provided by a pair of 2,250 kW dieselalternators.
Name Adebaran Star Builder Daewoo Shipbuilding Owner Vela International Type Aframax Product Carrier Aldebaran Star is an Aframax product carrier constructed by DSME, Okpo shipyard for Vela International Marine Ltd. under the survey of Lloyd's Register of Shipping. The vessel was designed with three (3) longitudinal bulkheads including one (1) centerline bulkhead and transverse bulkheads to have six (6) pairs of cargo tanks fully coated with pure epoxy, two slop tanks, one retention tank with mopping-up system and wing and double bottom water ballast tanks for water ballast.
The vessel has designed and built to meet the classification notations of : + 100A1, "Double Hull Oil Tanker", ESP, ShipRight(SDA, FDA, CM), LI, +LMC, UMS, NAV1, IBS, ICS, *IWS, SPM with the descriptive notes of "PL, SBT. ETA. COW, ShipRight (PCWBT, SERS, SCM)".
The Vessel has a continuous upper deck without forecastle, a raked stem with bulbous bow, a transom stern, a semi-balanced rudder and a fixed pitch propeller directly driven by a B&W5S70MC engine with MCR output of 19,100 PS at 91 rpm.
Design fatigue life of 25 years was applied for the longitudinal stiffener's end corrections to transverse webs/bulkheads in cargo area according to the requirement of LR FDA level II and all main longitudinal material in cargo area were suitably scarfed fore and after to ensure that all loads are transferred effectively.
The vessel is capable of carrying and handing three (3) grades of oil/petroleum product simultaneously with double valve segregation and a high pressure fresh water washing system.
The vessel was equipped with a first aid fire fighting system for high-level safety of the accommodation area.
The latest navigational equipment including an integrated navigation system and ECDIS was installed on board the vessel and also a nautical information display of the integrated navigation system was installed on the bridge wing.
The engine room machinery such as generators and pumps was designed to controlled/monitored by the ship's computerized control system including a power management system.
N a m e Capricorn S t ar B u i l d e r Hyundai H e a vy I n d u s t r i e s C o . , Ltd.
O w n e r Vela I n t e r n a t i o n al T y p e VLCC C a p r i c o r n Star is t h e 3 1 7 , 0 0 0 dwt double-hull V L C C built by Hyundai Heavy I n d u s t r i e s Co., Ltd. (HHI) for Vela International Marine Ltd.
The ship was d e l i v e r e d on July 25, 2003. The s h i p has one c o n t i n u o u s f r e e b o a r d deck f r om s t em to stern with sunken d e c k - t y p e stern deck, t r a n s v e r s e b u l k h e a d s and four l o n g i t u d i n a l bulkh e a d s in w a y of t h e c a r g o space. C a p r i c o r n Star is a new type of e n e r g y - s a v i n g high grade VLCC a n d is i n c o r p o r a t i n g e n v i r o n m e n t a l f r i e n d ly d e s i g n a d o p t i n g d o u b l e h u l l e d b u n k e r t a n k s , sepa r a t e L o w s u l f u r tank, I M O a p p r o v e d incinerator, and n o n e - O z o n e d e p l e t i n g r e f r i g e r a nt C a p r i c o r n Star is d e s i g n e d to c a r r y t h r e e g r a d es of c a r g o s i m u l t a n e o u s l y , h a n d l e d by three s t e am t u r b i n e c a r g o p u m p s , each d e l i v e r i n g 5 , 5 0 0 cu.
m./hr., with one C O W p u m p of 3 , 0 0 0 cu. m./hr.
and h o u s e d in a p u m p r o om at the f o r w a r d of e n g i n e room.
The cargo and ballast control systems of the ship is computerized control and monitoring system. Cargo control and monitoring covers operation of pumps, valves, ullage measurement, inert gas systems with manual control also available.
Radar beam type level gauges have been fitted to cargo tanks, with electro pneumatic type level gauges used in the ballast tanks.
The ship has five center cargo oil tanks, five pairs of side cargo oil tanks, one pair of slop tanks and water ballast tanks surrounding cargo oil tanks.
Double bottom and double hull construction is carried throughout cargo oil tanks, with longitudinal framing.
Propulsion is supplied by a Hyundai B&W 7S80MC main engine developing an MCR of 34,650 bhp at 79 rpm, enabling the vessel to sail at a service speed of 14.6 knots at design draft at 90% MCR with 15% sea margin.
Electric power is supplied by three main diesel generators with an output of 1,500 kW at 900 rpm each, one shaft generator of 1,500kW and one 550 kW emergency generator.
Capricorn Star is. among others, equipped with the highly advanced navigation system (Integrated Navigation System) that supports integrated bridge operations of the ship such as route planning, maneuvering for collision and grounding avoidance and navigation monitoring. The Ship is classed by DNV + 1 Al, Tanker for Oil ESP, NAUTICUS (Newbuilding), E0, Wl-OC, VCS2, LCS(SID), ICM(BTs), PLUS-1, COAT-1.
Name Hellas Nautilus Builder Hyundai Heavy Industries Co., Ltd.
Owner Consolidated Marine Management Type LPG/NH3 Carrier Hellas Nautilus, a 82,000 cu. m. LPG carrier, a fully refrigerated type with a cargo space divided into four independent holds was delivered on the July 3, 2003, to CMM, GREECE by Hyundai shipyard.
The 82,000 cu. m. LPG carrier vessel has an overall length of 225.27 m, width of 36.6 m and depth of 22 m with a design draft of 11.4 m.
The ship is powered by a B&W 6S60MC-C main engine with an MCR output of 18,420 bhp at 105 rpm, enabling her to sail at a service speed of 16.75 knots. Electrical supply is derived from three diesel driven alternators of 1,200 kW, plus an emergency unit of 130 kW. Hellas Nautilus has a cargo space divided into four holds with wing tanks.
And each hold accommodates an independent and self-supporting prismatic cargo tank, designed for low temperature cargo of -48. Cargo tanks are insulated with 120 mm thick polyurethane foam caddied with 0.5mm aluzinc steel sheeting. The LPG carrier is able to carry two cargoes simultaneously, both of which may be refrigerated. Cargoes include anhydrous ammonia, 1,3-butadiene, butane (iso and normal), butylenes, commercial propane, propylene.
The reliquefaction plant can handle two refrigerated cargo grades simultaneously and major equipments such as cargo compressors and motors are located in compressor and motor room on main deck level.
Cargo handling is operated by eight deep well pumps, each with a capacity of 600 cu. m./hr., allowing for a discharge time of approximate 18 hours excluding stripping. Loading is accomplished in about 18 hours based on vapor return to shore.
Ship Name MSC Linzie Ship Owner Mediterranean Shipping Co. S.A.
Ship Builder Hanjin Heavy Industries & Construction Ship Type Containership MSC Linzie is the first vessel of a new vessel type developed and designed by Hanjin which adopts the new Panamax length design of 294.05 m. Apparently the design series and Hanjin's well-established reputation in this niche has proved attractive, as the company has, to date, logged orders for 24 ships of the new design.
As mentioned above, its length is the maximum for Panama canal, i.e. 294 m. So it has been designed to move flexibly both in Pacific Ocean and in Atlantic Ocean through Panama canal, which is one of the main feature that makes it popular among the operator.
This ship offers the maximum intake of 5,060TEU. It is composed of six holds and each hold is capable of holding two stacks of hi-cube containers and also equipped with cell guides exclusively for 40 ft.
containers together with fittings for the 20 ft. container, which enhances loading flexibility in hold. On deck it is even more flexible due to the loading ability of 20/40/45ft containers including separate loading facility for special cargos like dangerous cargos and 400 refrigerated FEU.
The accommodation is equipped with convenient facilities for a total of 35 person including accommodation for six Suez-canal crews Recent sea trial result has shown that it has been so comfortably designed for the crews inside that the vibration and noise level has been noticeably reduced.
HSD-built MAN B&W 9K90MC-C has been mounted and its trial speed is 23.06knots when operating at 15% sea margin (90% MCR) at the scantling draft of 13.5m.
The supply material and accessory features are arranged based on an environmentally friendly design.
The major machineries and electronic parts are the ones whose performance has been verified through plenty of testing periods for the easy operations and also has been selected among the makers familiar to the operators.
Name OOCL Shenzhen Builder Samsung Heavy Industries Co., Ltd.
Owner Orient Overseas Container Lines Type Containership Samsung has constantly contributed with suitable technologies in the ever increasing size of containership. Ten 8,063 TEU designs for Orient Overseas Container Lines are the largest liners built and delivered by the Geoje shipyard till now. The first two are now being put into service. This comprises a short accommodation block and engine room positioned approximately threequarters aft, and eight holds forward and one aft of this position, providing 15 FEU bays in way of holds I to 8, with 4 FEU bays over No. 9 hold. The forward holds are dimensioned to carry 1 x 40 ft.
containers in cell-guides of No.l hold, 2 x 40 ft. containers in cell-guides of holds 2 to 8 with four transverse panels. The aft hold with five sets of covers for No.9 F hold and otherwise four sets of covers can carry 3 x 40 ft. bays. 45ft container can be loaded directly on hatch covers every other bay form No.3 hold to No. 9 hold.
Container capacity in the holds is 3,715 TEU, with either 4,144, or 4.348 TEU carried on deck, depending on whether stacks are seven or eight tiers high. Maximum stowage on deck is 17 rows of eight tiers high, and in the holds 15 rows and nine tiers. Lashing bridges are fitted on deck between the hatches, and on deck cell guide are fitted on mooring deck. A total of 710 FEU selfcontained air-cooled type reefer containers shall be loaded 510 FEU on deck and 200 FEU in hold. Dangerous goods can be loaded in holds 1 to 8 and on deck.
The hatch coamings are continuous and form the major longitudinal strength member, and a double hull surrounds the cargo space to form part of a tank arrangement comprising side, bilge, and three transverse double-bottom compartments.
Two side tanks, port and starboard, are used for automatic heel adjustment, with water ballast trans- ferred by means of a heeling pump.
OOCL Shenzhen claims to be fitted with the largest-sized main engine currently available for marine use: a MAN B&W 12K98MC-C unit built in Korea by HSD. with an MCR rating of 93,120 BHP (68.520kW) at 104 rev/min. When operating at 85% full power but without the shaft generator operating, the vessel has a service speed of 25.0 knots.
Electric supply is from a 3,000 kW Taiyo shaft-driven alternator, supplemented by four Daihatsu/Taiyo 3,000 kW diesel-driven sets in an arrangement controlled by a power management system.
One Nakashima 2,500 kW bow thruster and one SR63m-type of Rudder are fitted for efficient manoeuvring.
Propulsion is by means of a six-bladed FP propeller.
Name Methane Princess Builder Daewoo Shipbuilding & Marine Engineering Co.Ltd Owner Golar LNG Ltd.
Type LNG Carrier Methane Princess is a 138,000 cu. m.
Liquefied Natural Gas (LNG) Carrier ordered by Golar LNG Ltd. and delivered by Daewoo Shipbuilding & Marine Engineering Co. Ltd. Designed for the world-wide transportation of LNG the U.K. registered and flagged vessel was delivered August 25, 2003. The vessel is designed and constructed to meet the requirement of Det Norske Veritas (DNV) with the class notation +1A1, Tanker for Liquefied Gas, Ship type 2G (0.25 bar, -163 oC, 500kg/m3), NAUTICUS (Newbuilding), EO, Wl-OC, LCS (SID).
Methane Princess has a continuous upper-deck with aft sunken deck, a raked stem with bulbous bow, a bow thruster, a semi-balanced rudder and fixed pitch propeller driven by marine steam turbine. Four (4) cargo tanks totaling 138,000 cu. m. capacity are designed as GTT membrane type ("GT No 96 E-2 system") and will keep the LNG at -163 oC, under the condition of maximum daily boil-off rate less than 0.15% of fully loaded cargo volume.
Primary/secondary barriers of 36% nickel-steel alloy (Invar, 0.7mm thickness) which have a low thermal expansion coefficient are installed in cargo tanks and plywood boxes filled with expanded perlite are used for the primary/ secondary insulation.
Through the cargo hold length, underdeck passageways are arranged port and starboard in trunk deck space and also center passageway (pipe duct) with trolley system is arranged in the double bottom.
These passages are used as pipe & cable passages and for inspection/maintenance.
Fatigue design of hull structure is based on the life time of 40 years in North Atlantic sea conditions.
A six (6) tier deckhouse located aft provided accommodation for 40 persons including Suez crews and the vibration levels in living areas are designed especially low at normal operating condition.
Cargo handling systems are designed to be capable of loading or discharging the LNG within 12 hours using eight cargo pumps with capacity of 1 . 7 0 0 cu. m./hr.
and four (4) stripping/spray pumps.
Liquefied cargo handling equipments such as two (2) sets of main cargo pumps, one set of spray/stripping pump, one set of capacitance type level gauge including back-up capacitance type top/bottom sensor and one set of float type level gauge are fitted in tripod mast construction which forms a complete assembly unit per cargo tank by incorporating all outfittings and piping in cargo tanks. Vapor cargo handling equipments such as two high duty compressors, two low duty compressors, one main vaporizer, one forcing vaporizer and two boil-off/warm-up heater are arranged in cargo machinery room which is effectively arranged so as to be readily accessible, easy operation and maintenance.
This vessel is designed to meet ship/shore compatibility of the LNG loading/unloading terminals Everett.
Elba Island. Cove Point. Lake Charles in USA. Point Fortin in Trinidad. Das Island in UAE. Ras Laffan in Qatar. Qalhat in Oman. Dabhol in india. Huelva.
Cartagena, Barcelona and Bilbao in Spain.
EcoElectrica in Puerto Rico and also LNG discharge terminals in Korea. Mooring arrangement, fender contact flat area, gangway landing position/support, manifold arrangement and ship/shore communication systems for the above all LNG terminals are considered sufficiently in this vessel. Air draft limitation forTobin bridge in Boston is successfully satisfied by applying the folding type antenna mast.
The main powering unit consist of the Kawasaki UA- 360 (MCR: 36,000 ps x 88 rpm) Cross compound steam turbine with high pressure turbine and low pressure turbine, double reduction gear, main condenser including astern turbine. Two (2) sets of dual fuel burning main boilers supply the steam for the main turbine, turbo generator, main feed water pump and other steam driven machinery are designed to be capable of burning of heavy fuel oil and also gas fuel by the low duty compressor through boil-off/warm-up heater for the use of boil-off gas.
The ship's Integrated Automation System (IAS) has been designed, programmed and installed by Korea Honeywell, using the Total Plant Solution (TPS) system with redundant data highway (LCN).
IAS dedicates the data acquisition for centralized process monitoring, incremental levels of distributed digital controls, history and alarm collection, reporting, communication with other process subsystems, open system provisions, control of extension alarm system and integration of extension VDU system for process/alarm monitoring.
The bridge is designed for optimum operational safety, efficiency, takes advantages of current technology and rational navigational methods. For the bridge operation under normal conditions by one person, the system comprises a modular workstation arrangement, meeting all design and equipment layout requirements in accordance with DNV notation WI-OC.
Name MV Midnight Sun Builder NASSCO Owner Totem Ocean Trailer Express Type Trailership Early this year National Steel and Shipbuilding Company (NASSC0), a wholly owned subsidiary of General Dynamics, delivered the M.V. Midnight Sun to Totem Ocean Trailer Express, Inc. (TOTE). The Midnight Sun is significant as it was the first commercial dry cargo vessel to be built in the U.S. in 10 years, and the first of two new Orca-class trailerships being built by NASSC0 for TOTE's service from Tacoma, Wash., to Anchorage, Alaska. The M.V. Midnight Sun is a 840- ft. long, 118-ft. wide (256 x 35.9-m) RoRo cargo ships capable of carrying highway trailers as large as 53 ft. (16.1 m) in length. Cargo decks are 360,000 sq. ft. and able to carry up to 600 cargo trailers and 220 autos as well as oversized freight. The ship employs twin-screw, diesel-electric propulsion that can achieve a speed of more than 24 knots. The ships' cargo can be loaded and discharged in nine hours, with the speed and efficiency of cargo handling being an important competitive advantage for TOTE. M.V. Midnight Sun and its sister ship M.V. North Star have received several prestigious awards for their environmentally sensitive features. These awards include the States/British Columbia Oil Spill Task Force Legacy Award for 2000, the Alaska Department of Environmental Conservation Commissioner's 2000 Pollution Prevention Award, and the U.S. Coast Guard's William M.
Benkert Foundation 2002 Environmental Excellence Bronze Award.
Read great ships of 2003 in Pdf, Flash or Html5 edition of December 2003 Maritime Reporter
Other stories from December 2003 issue
Content
- A More Leisurely Pace in Retirement? page: 8
- BV Backs Double-Hull Bulker Designs page: 10
- Odfjell Net Falls $20M; U.S. DOJ Fine the Cause page: 10
- New Sub Model Christened at NNS page: 12
- ISPS Code for Ship Repair Facilities? page: 13
- MX Marine Unleashes New Family of Electronics page: 14
- Container Market Pauses page: 15
- Careful ... Your TBT May Be Showing page: 17
- great ships of 2003 page: 19
- New Technology Melded to the North Atlantic Tradition Queen Mary 2 page: 24
- Techcrane Designs, Builds 125-ton Crane for Midnight Wrangler page: 34
- Global Materials Services Venezuela Takes Two page: 34