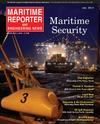
Eliminating Waste Water Discharge
A New Approach to CWA/NPDES Requirements
Environmental professionals in industry are tasked with the unenviable responsibility of managing the delicate balance between compliance with ever-increasing and at times mind-numbingly complex and stringent regulations and maximization of production efforts. Consequently, Environmental Compliance Officers are perpetually on the hunt for alternatives to costly process controls and best management practices designed to mitigate potential negative impact. Requirements of the Clean Water Act and associated National Pollutant Discharge Elimination System serve to illustrate how daunting the proposition of this balance can be and further present the need for constantly evolving technology in the quest for cost-effective options. In fact, effluent limits on process water discharges in permits issued under the latter have historically proven to be so rigid as to hamper even basic industrial processes to the extent that any type of traditional engineering controls have been rendered ineffective. Subsequently, these limits have been both scientifically and legally challenged, albeit to no avail. In the course of the settlement of a civil action brought by EPA involving, among other issues, its process effluent, a shipyard in Hawaii has developed new technology that is generating a paradigm shift where the approach to waste water discharge is concerned in this context.
Marisco, Ltd. is Hawaii’s largest privately owned shipyard, employing upwards of 125 workers during peak production cycles at Barber’s Point Harbor and at Pearl Harbor, both on the island of Oahu. For much of the last decade, reported concentrations of constituents of concern in dry dock effluent generated at the main facility, most notably both copper and zinc which can be found in anti-foulant paint systems applied to vessel hulls, have proven problematic for the company in consideration of limits imposed by its NPDES permit. This condition has been particularly puzzling to the environmental staff within the organization given both the level to which engineering controls have historically been applied and in light of the results of sediment characterization and ambient water quality studies conducted by Marisco that seem to indicate no presence of any negative impact from its industrial activity. Nevertheless, based in part on the content of its monthly discharge monitoring reports, Marisco has been the object of two actions filed by both the state and by EPA. The most recent of these, the result of a compliance evaluation conducted in December of 2008, was just settled last week.
During settlement negotiations, Marisco attempted to explain apparent copper and zinc concentrations as the result of flawed sampling protocol that had been recommended by the state, citing it as too narrowly defined to allow for representative sample procurement. The company consulted with professionals from URS in the design of a new sampling and analysis plan. The resulting concentrations, while considerably lower than those obtained under the states plan, still did not attain permit limits. Although it seemed obvious at the time that paint overspray was the likely source of the problem, company officials were unable to identify at what stage of application any breach of containment might be occurring and therefore where BMPs needed to be modified. Further, the notion that studies had failed to identify significant levels of any pollutant reaching the harbor was still perplexing. The fact remained, though, that there were readings indicating levels present in effluent that appeared to violate permit conditions and that Marisco could not continue to operate under these circumstances. It was time to research and develop an alternative.
In a concerted effort to rise to the challenge and in one to foster effective collaboration between regulatory authority and the regulated community that is at the core of the National Environmental Policy Act, Marisco consulted further with URS and with EPA to develop a system that would eliminate its discharge entirely. This system is composed of two major components. The first of these involves a three-stage dry dock deck fresh water wash down. The second is the collection of residual water into a closed-loop process called the Portable Passive Precipitation Filtration System or 3PF, capable of treatment to below permit standards and then retention for re-use in the process. Given this proposal, EPA granted conceptual approval and allowed a period of time for design and development which is still underway, but to date results of testing both the efficacy of the deck wash down and of the filtration processes have been very encouraging, and the original design of the filtration unit has received an honors award for excellence in engineering from the American Council of Engineering Companies Hawaii. EPA has indicated that after the current phase of system optimization that the agency will consider a request for permit modification eliminating the requirement for effluent sampling.
Concept Development
The intent was that the conceptual design should address the following:
• Treatment efficiency to ensure compliance with current NPDES limits for discharge.
• Development to target pollutant such as copper, zinc and TSS.
• Filtration at a rate that ensures thorough removal.
• Consideration of site restraints requiring the need for portability.
• Examination of construction, operational and maintenance costs.
Shipyards and their dry docks are industrial areas characterized by activities such as abrasive blasting, metal cutting and painting operations. Dry dock effluent and general shipyard storm water discharges can therefore be thought of as potential pathways for relatively high concentrations of metals, intermediate concentrations of solids and low concentrations of oil and grease. The first line of defense in keeping such potential pollutants from reaching receiving waters is the implementation of BMPs which apply operational improvements and source control technology to prevent discharges from attracting blast grit, paint chips, oil, and other potentially contaminating materials. As discussed earlier, Marisco developed a BMP suite for such control, but those alone proved insufficient to allow the shipyard to meet effluent criteria for direct discharge to surface waters as even hard to capture fine particles of dust can contain concentrations of pollutants.
URS began its research with a review of the testing results from dry dock effluent analysis primarily for copper and zinc. Copper concentrations were found in a range of 9 to 630 µg/L with an approximate average of 400 µg/L. In the case of zinc, effective concentrations were observed in the range of 11.4 to 390 µg/L with an average of 190 µg/L. The design criteria for the treatment system were therefore set to address a constituent concentration of 500 µg/L for copper and 250 µg/L for zinc.
There is a variety of technologies for removing metals from process waters. Those include chemical precipitation, electrocoagulation and sedimentation. Effectiveness for all is dependent on the media used as well as flow chacteristics through that media. For example, sand can be quite effective in the removal of particulates but is not at all effective for metals in dissolved phase. Organic-based filtration can provide enhanced treatment of dissolved metals by adsorption but is more effective on some chemical constituents more than others. The results of technology review conducted by URS indicated the need for a combination portable treatment structure to be used for full-range effective treatment of all constituents.
A study of various drydock facilities and shipyards on the West Coast of the U.S. found that they commonly use passive sedimentation, and that of facilities on the East Coast found that techniques of precipitation are most often employed there. A report from the Engineering Research Center of the University of Maryland titled “Removing Heavy Metals from Wastewater” outlined the precipitation process and cited its effectiveness. West Coast publications that advocate passive filtration agree that while the precipitate process is effective, they cite the expense associated and suggest that it is only effective to approximately 65 – 75% removal. URS’ design parameters therefore were established to incorporate both the precipitation process as well as passive filtration methods.
Assuming a reasonable value of 75% removal of heavy metals by the hydroxide precipitation process, which involves the application of caustic soda and coagulants that create metal hydroxides, it is felt that additional treatment is needed to achieve a level of non-detect in analysis of storm water or industrial effluent. Comparison of West Coast passive filtration systems indicates a low range of 25 – 42% treatment efficiency to a high range of 94.5 – 98.2%. It was obvious that site conditions and pollutant loads vary from operation to operation and from location to location. The Pacific Northwest Pollution Prevention Resource Center cites more than 100 Pacific Northwest shipyards where passive filtration is used with consistent good results in these ranges in their report “Pollution Prevention at Shipyards.” Thus, with the combination of precipitate processes and passive filtration methods, it was expected that the URS/Marisco 3PF System would have the capacity to achieve complete removal of target constituents, designed to effectively employ coagulation, precipitation, sedimentation and passive filtration to achieve State of Hawaii Department of Health regulatory levels of 2.9 µg/L for copper and 95 µg/L for zinc.
To test and evaluate the design, URS and Marisco assembled a tabletop unit. Built to scale, this model incorporated all of the components of the intended full-scale model and was constructed at Marisco’s dry dock location to receive waters from the wash down process containing copper and zinc. Marisco discontinued implementation of other BMPs during vessel maintenance to create a worst-case scenario as can be seen in the system influent levels in the compiled data below. Two testing regimes were conducted, and analysis on samples was executed by an accredited laboratory. Results indicating success in attaining non-detect levels are available for review upon request.
How it Works
One wash cycle of the dry dock generates approximately 1,500 gallons of residual wash water. The three stages then produce approximately 4,500 gallons, so the capacity of Marisco’s custom designed unit would be approximately 5,000 gallons. In general, the 3PF System is segmented, with the use of baffles into a chamber for precipitation, one for sedimentation, and a discharge chamber. System influent generated by collection from the dry dock after washing is initially treated by an oil/water gas separator energy flow diffuser to remove floatables and large particles such as paint chips or rusted metal clamps. The water then is conveyed into the first internal chamber of the system – the precipitation chamber – where a sheet flow facilitated by a perforated pvc “sprinkler” piping system spreads it out over a screen holding a bed of pH adjuster to ensure complete introduction to turn the solution caustic and to increase alkalinity to above a pH of 7.0 su. There is some immediate precipitation of heavy metals from metal hydroxides solids at this stage.
To ensure that solid metal hydroxides form, a coagulant of organic polymers is presented to aid in particle formation. A second screen located below the pH adjuster screen is coated with these coagulants. These two screens will both be required to be removed and recharged after each complete process treating approximately 4,500 gallons.
The remainder of the system hosts the sedimentation chamber and the discharge chamber. The sedimentation chamber is simply a section for the wash water to accumulate and to stagnate. Here, heavy metals still in suspension and late-forming metal hydroxides will begin a process of sedimentation. Materials that are used as attractive force to ensure sedimentation are on the base of the system.
The last stage of the portable treatment system is the discharge chamber. Again, separated by an internal baffle, the area generates a volume that has been precipitated and filtered by sedimentation that rises via capillary action to a point at this end of the vault where it can be extracted to a holding tank that will now contain clean water ready for re-use.
For effective operation, it is envisioned that the technology proposed can be applied over a three-hour period but can be optimized over a 24 hour period. There will be no harm in allowing the process to continue during non-use periods. If additional clean water is needed for the next wash cycle, the water in treatment can simply be transferred to the clean water holding tank as needed.
Additionally, it is recommended that any yard areas exposed to storm water be bermed or constructed in such a manner as to facilitate collection and introduction into the system for treatment.
From Table-Top to Prototype
To ensure that a full-scale model will respond in this manner, EPA has given Marisco fifteen months to allow for ample dry dock activity to collect supporting data. During this time, while the company does not expect any major changes to original design specifications, it is anticipated that a few minor alterations will be necessary to attain system optimization.
Stephen F. Hinton, REM, CEA, ECS, Vice President for Environmental Affairs, Marisco, Ltd. and Mark Howland, Hawaii Business Developer and Program Manager, URS, are co-designers of the 3PF System.
(As published in the July 2013 edition of Maritime Reporter & Engineering News - www.marinelink.com)
Read Eliminating Waste Water Discharge in Pdf, Flash or Html5 edition of July 2013 Maritime Reporter
Other stories from July 2013 issue
Content
- Inspired Youth page: 8
- Powering Ahead Cleanly page: 14
- Are our Ports Safe? page: 16
- LNG Fueled Vessels page: 18
- Eliminating Waste Water Discharge page: 20
- Shipping Registries and Piracy Response page: 24
- IRS to Leverage R&D for a New Dynamic Role page: 28
- Brazil Class page: 30
- Asia Pacific Spill Response OSRL Increases Capabilities page: 34
- Heinen & Hopman Complete HVAC Project page: 36
- Challenger Marine Condensing Unit page: 36
- Flexlife Completes Field Trial for Chevron page: 36
- CMA CGM Marco Polo Fitted with Marinestar page: 36
- Maintenance-free Gyro Compass page: 37