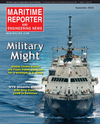
Fuels of the Future
By Wajdi Abdmessih
Chosing your fleet’s future fuel wisely
The imposition of a global 0.5% sulfur cap may be less than four years away. This clearly will eliminate residual fuel from the available fuel options unless you have fitted your vessel with a scrubber or other exhaust gas treatment technology in order to comply with MARPOL Annex VI emission regulations.
At the start of 2015, permitted sulfur levels in emission control areas (ECA) dropped from 1% m/m to 0.10% m/m. Although this was a large reduction, the switch was relatively easy to make as suppliers were capable of creating new blends from residual and distillate fuels to meet the 0.10% limit and refineries also produced new ECA compliant hybrid fuels. Indeed, given the background of falling fuel prices, many vessels simply made a switch to low sulfur distillate fuel. All these options provided an alternative way for vessels to comply with the regulations without making large investments in scrubbers or in retrofitting to use liquefied natural gas.
Looking ahead to the maximum global sulfur limit of 0.50% m/m (outside ECA zones) by 2020 or 2025 (the date will be decided in 2018 following the results of an International Maritime Organization (IMO) study), there will be no residual fuel oil that can meet the MARPOL Annex VI regulation for SOx, PM and NOx without the use of scrubbers, and therefore alternative fuel options must be considered.
Biofuel
Biofuel has become part of the alternative fuel mix of the future due to its low carbon print, and the fact that it offers a considerable reduction in greenhouse gas (GHG) and sulfur (SOx) emissions, and has a higher cetane rating than some petro-diesels, which can also improve performance.
The draft version of ISO/DIS 8217 has introduced to the distillate fuel specification new grades called DF Grades (DFA, DFZ and DFB) which include biofuel in the form of fatty acid methyl ester (FAME) with up to 7.0 % volume. It has also increased the limit for the “de minimis” definition level to 0.50% v/v instead of the previous volume of 0.10% v/v.
This is a smart way of increasing the distillate fuel supply volume by up to 7% in the market without major investment.
While adding biofuel to the mix is a positive step for the marine fuel industry, it also introduces some new quality challenges. Biofuel is known for its increased lubricity, Cetane number, and the excellent reduction in emissions of various pollutants and global warming gasses, such as CO1, CO2, hydrocarbons and particulate matter.
However, it also has some less beneficial properties.
Biofuel is hydrophilic, which means it has a great ability to absorb water. Therefore water and excessive moisture must be eliminated when using biofuel and this can be very difficult to achieve in the marine environment.
Biofuel will absorb the water if present, and this can lead to wax dropping from the fuel as well as filter plugging.
Besides the hydrophilic characteristic of the FAME, there are other major parameters in relation to biofuel that could be problematic for a marine diesel engine.
To safeguard the end user, the ISO/DSI 8217 draft has stated that the FAME used in the biofuel blending must be in compliance with the requirement of EN 14214 or ASTM D6751. The major reason for this is to ensure that some of the properties of the FAME remains within the specification, as a high level of these properties if blended with distillate may cause major problems.
These parameters are tested under the ASTM D6751 but it is not required under the ISO/DSI 8217 distillate marine fuel table (1). The parameters are detailed below (with accompanying effects):
- Free Glycerin, which has maximum of 0.02% m/m: High levels of free glycerin can cause injector deposits, as well as clogged fueling systems, and result in a buildup of free glycerin in the bottom of storage and pipe systems.
- Total Glycerin, with a maximum of 0.240 % m/m: To determine the level of glycerin in the fuel and includes the free Glycerin and the Glycerin portion of any unreacted or partially reacted oil or fat. High levels of total Glycerin (mono-, di-, and triglycerides) can cause injector deposits and may adversely affect cold weather operation and filter plugging.
- Sulfated Ash, 0.020 max % mass: Ash-forming materials may be present in biodiesel in three forms: (1) Abrasive solids, and (2) Unremoved catalysts, these two can contribute to injector, fuel pump, piston and ring wear, and also to engine deposits. (3) Soluble metallic soaps, which have little effect on wear but may contribute to filter plugging and engine deposits.
To safeguard your investment it is recommended to test the DF grades for these parameters to ensure the safe handling of the fuel onboard the vessel.
As we can see, the fuel quality issue is becoming increasingly important as more ‘problematic’ fuels enter the supply chain. This is not the result of deliberate actions but because many new fuels types are coming onto the market without a new infrastructure in place to handle and segregate what in some cases can be incompatible products or biofuel free products.
While the distillate fuel sector is experiencing many changes – and many more are to come - residual fuel is still the major element of the market, and is dependent on new developments in scrubber technology in order to survive as a key marine fuel in the next few years.
One of the most problematic parameters in residual fuel is catalytic (Cat) fines.
Cat Fines
Cat fine levels have increased in recent years across all residual fuel grades and have become the major contributors to engine damage. Other old problems still exist, but to a less extent, such as polymer contamination and poor ignition fuel. More than 60% of the high sulfur fuel has been found to contain cat fines higher than 30 mg/kg, and 12% contains more than 61 mg/kg, which exceeds the maximum specification limit for the ISO 8217:2010 RMG and RMK grades. Some 74% of the high sulfur fuels tested have cat fines level greater than 20 mg/kg. Some of the cat fines damage has been blamed on poor filtration, purification and fuel management on board the vessel. Therefore vessel managers must assess the efficiency of the fuel treatment plant in order to mitigate the risk of high cat fines by taking samples before and after purification or at the engine inlet in order to ensure that it is under the recommended level as well as taking note of cat fines particle count distribution.
You must know your vessel purifier efficiency rate as it can vary from 25% to 70%. Unless you check this, you may unintentionally introduce a high level of cat fines to the engine, thereby increasing the potential for engine wear.
Polymer contamination, although it is a relatively rare occurrence, can cause severe operational and mechanical problems. This can be avoided by testing for polymers as part of your fuel quality monitoring, which should consist of simple filtration and FTIR/microscopic analysis.
For safe operation and fuel optimization you need to know what is in your fuel, and the supplier fuel quality certificate may not actually represent what you have taken onboard the vessel.
In today’s market you cannot afford not to test your fuel.
I would also say know your engine, be open to all types of fuels, and work with your engine manufacturer, your fuel supplier and your fuel testing provider to set the parameters that will work for your specific engine and operating conditions.
Use the ISO specifications as a guideline and add what is needed to safe guard your investment. You will be surprised how much you can save, and protect the environment, by doing so.
The Author
Wajdi Abdmessih, Founder & Owner of Seahawk Services, a new name (but a long history) in the fuel testing and inspection business.
(As published in the September 2016 edition of Maritime Reporter & Engineering News)
Read Fuels of the Future in Pdf, Flash or Html5 edition of September 2016 Maritime Reporter
Other stories from September 2016 issue
Content
- Silence Your Ships page: 10
- Measuring Noise Levels of Cavitating Propellers page: 12
- What the Heck is ‘Privity’? page: 14
- Fuels of the Future page: 16
- Grand Bahama Shipyard: Investing in the Future page: 18
- Vessel Spotlight: RV Meen Shandhani page: 26
- Choke Points are Flash Points page: 28
- NYK Steams Ahead page: 34