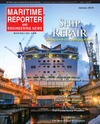
A Case for Propeller Guards & Cutters
By Matthew Bonvento & Jawara Drigo
As I was preparing for Thanksgiving dinner I put on Indiana Jones and the Last Crusade. While Indiana Jones and Doctor Elsa Schneider were being chased by the Brotherhood of the Cruciform sword through Venice and their boat was neatly shredded by the propellers of a larger vessel, it had me thinking of how much propeller technology has changed over the years. And how hopefully Indiana’s boat did not actually damage that vessel’s propeller.
Recently an article passed though my news feed about the first 3D printed propeller. This is indicative of the direction the industry is taking. With the advent of new technology, the methods of implementation will revolutionize the maritime world. However advanced we become though, certain perils are still prevalent. The methods of prevention will be dependent upon the type and size of vessel as well as the risk that is trying to be prevented.
Personnel Injury
Propeller strikes are a concern for vessels with large tonnage down to personal craft. From whales who still bear the scars of a decades old propeller strike to the unfortunate children that suffer this risk is one in which life is more at stake than property and the environment. Think of the propeller guard as a steel cage that surrounds the propeller. Propeller guards are designed mainly for vessels of a smaller tonnage down to recreational to safeguard from potential accidents that could occur such as an individual falling off the boat. Due to the strong steel structure of the propeller guard, it is effective any protecting anyone who would otherwise get cut by the propeller. There have been several cases of propeller related casualties.
One particular case occurred a in 2017 and involved a 12-year-old boy from the Centerport Yacht Club in Suffolk County, N.Y. who was killed by a propeller after accidently falling off a boat while taking a sailing lesson. This tragedy is possibly going to force a change in Suffolk County law forcing all small vessels to have propeller guards. This law may even be applicable to smaller vessels such as fishing vessels and tugs operating in Long Island. Casualties such as this drive home the importance of installing propeller guards on all types of small craft for the safety of people aboard as well as any swimmers, snorkelers or other living creatures or structures that may be near a vessel.
As effective as they are, propeller guards will not be efficient on larger vessels due to the excess weight. It would be interesting to see if propeller guards made of lighter weight material could do the same job effectively.
The Kort Nozzle is a round hydro-dynamically designed shroud that encircles the propeller. The concept of the Kort Nozzle, also known as the ducted propeller was originally developed by 20th century German engineer Ludwig Kort. Since its inception, the Kort Nozzle has been used strictly on vessels that are required to operate with high thrust at low speeds including tugs and trawlers. With the Kort Nozzle, a vessel’s speed is kept at below 10 knots. If the vessel’s speed exceeds ten knots, water flow to the propeller decreases and therefore, there will not be enough thrust generated to allow the propeller to rotate efficiently. It is not uncommon to find Kort Nozzles with nets and lines wrapped around the outside as their net guards only catch, and don’t cut fishing lines and nets.
Generally, propeller cutters are designed for the purpose of clearing any obstructions at sea that would significantly reduce the speed of vessels or render them inoperable. Propeller cutters are designed for marine growth and fishing gear, which due to their smaller diameter can easily be wound around a shaft causing significant damage, loss of time and possible environmental pollution.
The shaft mounted cutter or rotary cutter which is made of hardened stainless steel, works through a screw action which is generated once the shaft rotates. At the turning of the propeller, lines, nets and weeds are automatically drawn into the cutter blades.
The shaft mounted cutter is used for small vessels with shafts of 20mm to 255mm and cuts in both the forward and reverse directions. It is usually used on yachts, tug boats, pilot boats and super yachts and is currently installed on more than 100,000 vessels. One of the main advantages of the shaft mounted cutter is during its cutting action, there is little to no reduction in the speed of the vessel.
The mounting of such equipment is a simple process. There are a set of blades mounted around the shaft rotate with the blade cutting any line that is drawn in by the propeller suction. Requirements for shaft mounted cutters is a factor of the spacing between the strut hub and the propeller, requiring enough room between the two so as to not have the blades come in to contact on each rotation.
The propeller mounted cutter has a fixed blade mounted on the strut hub with other blades mounted on the propeller. During each rotation lines are cut as if with a scissor, making use of the fixed blade and rotating blades to slice the line. If aft seal rupture occurs, it can result in oil pollution and other damage to the vessel which would require expensive repairs.
In contrast to the shaft mounted cutters, the propeller mounted cutters are used in medium and large sized vessels and designed for propeller hub sizes of 300mm to 1,000mm. The propeller mounted cutters are installed on all types of commercial and naval vessels including tankers, OSVs, cruise ships and semi-submersible drilling platforms. In general, the propeller cutters serve as a huge asset to vessel owners because they save them from facing serious penalties such as towage of their vessel by the Coast Guard as well as eliminating the need to send divers down into the sea to manually cut these lines, nets and weeds or worse yet haul the vessel out of the water to conduct repairs.
Shaver cutters are line cutters that work by continuously shaving rope, line or other debris caught by the propeller. As a concept, this is a radical departure from scissor and disc designs which attempt to slice clear through line or rope at first strike.
Shavers employ fixed position vertical blades that skim closely over a cylindrical, smooth surfaced concentric rotating spool. The spool serves a number of important functions. First, line is prevented from sliding off the propeller hub and wind onto the shaft. Second, line is prevented from radial slipping. Third, to cause rotating line to press lathe-like against stationary radial cutting blades. The result is a substantial portion of line is progressively rendered harmless as it is converted to shavings. The blade angles are positively raked and rapidly remove line whenever line presses against the blade edges. With this arrangement debris has no alternative other than to be cut away.
On a typical shaver line cutter, there is at least one forward and one reverse blade, so the debris is cut no matter which direction the propeller turns. Faced with a severe propeller entanglement such as a large cluster of rogue rope, line, or net, by rotating and counter-rotating the propeller, a shaver cutter has excellent prospects of freeing the propeller. Faced with a simple entanglement involving a single floating rope or line, a skipper probably would be unaware the cutter had done its job.
Using this type of cutter, a skipper’s prospects of keeping a vessel’s propeller free of rope or line are significantly improved.
Most modern cutters do not cause a significant amount of drag or reduction in speed. In addition most can be installed as an after market add on while in the shipyard, without a significant cost.
Risks of not installing this equipment can be catastrophic. One such case involved a cruise vessel which had two azipods entangled.
This job cost upwards of $800,000 for each azipod. Unfortunately, the work did not end there. With the seal rupture there was a resultant loss of non-bio friendly lubricant in to the water, which necessitated a cleanup as well as a reporting to the coastal authorities. This whole situation could have been avoided for a price of approximately $15,000.
Although not yet in widespread use, propeller cutters can prevent significant damage and downtime to vessels. As my mentor, Captain Michael DeCharles, always says, “Pay me now, or pay me later.”
The Authors
Matthew Bonvento is the Senior Manager for Safety, Security, Regulatory, and Quality Compliance for Vanuatu Maritime Services Ltd.
Jawara Drigo is an Intern at Vanautu Maritime Services. Drigo is completing his undergraduate degree in International Transportation and Trade at SUNY Maritime College.
(As published in the January 2018 edition of Maritime Reporter & Engineering News)
Read A Case for Propeller Guards & Cutters in Pdf, Flash or Html5 edition of January 2018 Maritime Reporter
Other stories from January 2018 issue
Content
- Serious Questions Surround BWMS Testing page: 10
- Subchapter M: Top 5 Moves to Make Now page: 12
- A Case for Propeller Guards & Cutters page: 14
- Interview: Alison Nolan, GM, Boston Harbor Cruises page: 16
- Interview: Chia Yoo Soon, Chevron Marine Lubricants page: 24
- The U.S. Navy's Fundamental Problem page: 28
- Driving the Digital Ecosystem page: 32
- New Ship Repair Yard Coming to Brazil page: 36
- BAE Systems Jacksonville: Ship Repair's 'Destination of Choice' page: 39
- Vigor Adds $20 Mln Drydock page: 42
- Hendry Marine Adds New Drydock page: 44
- Caterpillar Marine’s MEO & ‘The Big Virtual Engine’ page: 49
- Triple-screw Tug for the Hudson page: 49
- Tech Talk: GHS Adds 'Seakeeping' page: 50