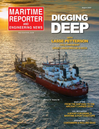
In the Shipyard: The Art of the Ship Lift
Bardex has made its name in providing solutions to move, restrain and lift heavy loads, active in the offshore oil and gas, shipbuilding and offshore wind markets. In shipyards its principal products are the Chain Type Ship Elevator, ship transfer solutions, and ship block transfer, lift and positioning systems, and Bardex installed its first shiplift in 1978 … a shiplift that is still operational today. Bardex CEO Thomas Miller shares insights on the company’s history and future.
Bardex CEO Thomas Miller, PE, has lived a maritime life, graduating from the University of California, Santa Barbara in 1982, with a bachelor’s degree in mechanical engineering and a specialization in marine structures, serving 38 years with Bardex, starting in the design department. In assessing the markets Bardex serves, he said while the split varies from year to year, “In 2019, Bardex reported 50% of revenue from shiplift and transfer products, 40% from Offshore Oil/Wind projects, and 10% from aftermarket lifecycle support.” Bardex today offers a number of system solutions designed to improve shipyard productivity.
“Our Chain Shiplift is a unique solution from that has significant benefits for yard owners,” said Miller. “We can design and supply shiplift systems ranging in capacity from 2,000 metric tons to 20,000 metric tons. We manufacture chain jacks in standard sizes of 300, 400 and 600 metric tons and we can customize these sizes if desired.”
Miller contends that, compared to Dry Docks the Shiplift & Transfer System offers a number of strategic advantages, including:
•Optimizing yard space and revenue potential
•Increasing yard flexibility in ship building and servicing
•Reduce Dry Dock CapEX and OpEX
•No confined work area constraints improving productivity and efficiency
•Lower environmental Impact; contained construction waste, reduced water contamination.
Photo: Bardex
Customize Your (Ship Lift) Ride
The design and construction of a shiplift is typically segregated into four principal activities; civil works, lift and transfer system equipment, platform fabrication, and installation/commissioning. “The most cost-effective approach is for the shipyard to act as the general contractor and issue separate contracts for each of the activities,” said Miller. “Depending on capability, some clients elect to perform some of the activities instead of contracting the work. Most shipyards are capable of fabricating the steel platform, for example, to designs provided by Bardex.” Alternatively, Bardex can provide a turnkey solution, except the civil works, which requires design and construction specialists. The civil works consists of the dredging of the area under the shiplift, installation of support piles, the concrete for the piers and yard transfer area, and utilities. “A typical project execution with Bardex providing a turnkey solution is described as follows,” said Miller. “For this example, the civil works are completed by others. The civil works order is placed on or about the same time as the shiplift system.”
- Each shipyard has a unique location, servicing vessels of various configurations and weights so the design phase starts with client specific parameters and requirements. Bardex prepares the basic system design in collaboration with the client until there is agreement on the shiplift, shipyard, and transfer system arrangement. The average duration for basic design is four months. The detail design including engineering calculations requires another four months as the client specific parameters are applied to the standard equipment design. The piping and electrical arrangement and steel platform are usually unique to the project and so these are new designs.
- Procurement of long lead items will begin within six months of order and about two months ahead of the conclusion of detail design, to save time. The total duration for the procurement phase is eight months, with many items being received in advance to allow the manufacturing to commence after four months of procurement.
- The equipment manufacture is performed at Bardex facilities in the U.S. and South Korea. Platform fabrication is subcontracted to a supplier in the vicinity of the yard to facilitate transporting of the platform to the site. If there is sufficient space at the site, the platform final welding/assembly can be performed at the site. The manufacturing phase is approximately six months. “Therefore, the equipment and platform are ready to ship 16-18 months after contract award,” said Miller. “The client should target 16 months for completion of the civil works to obtain the minimum project schedule. In other words, the civil works will be completed at the same time as the equipment and platform. It is also desirable to install the piping and electrical systems prior to delivery of the equipment.”
- The equipment and platform are installed followed by interconnection of the piping and electrical to the equipment. The duration for installation and commissioning (start-up) is four months. Acceptance testing consists of functional, synchronization, and load testing of the shiplift. Witness testing by an independent third party can be arranged or in the case where the lift is to be classed or certified, Lloyds Register of Shipping is involved.
Photo: Bardex
The Market
While the world collectively comes to grips with the ‘new normal’ courtesy of the COVID-19 pandemic, Miller said that there are a number of areas around the world that have potential for future investment in shipbuilding and facilities upgrades, some supported by government investment in the form of loans, grants and military related vessel orders.
“Bardex has been successful with shipyards expanding their capacity to launch and repair the next generation of military vessels that are larger and heavier than their predecessors,” said Miller. “We understand this to be ongoing in the U.S., Australia, and South Korea amongst other countries.”
Another area ripe for growth is the megayacht repair sector. “These are the next generation of yachts that are larger and heavier than SuperYachts,” said Miller. “In order for ship repair companies to compete in this market, they need larger shiplift capacity. Even though a yard may have a drydock of sufficient capacity, yards need the ability to handle multiple vessels at any one time. For example, during the yachting off-season there is a majority of yachts being repaired and maintained. We understand there will be demand for shiplifts in the Mediterranean Sea, Florida, and the Carribean.”
Finally, Miller reckons that the IMO 2020 initiatives for retrofitting fuel scrubbers and ballast water treatment systems may lead to shipyards upgrading to a shiplift system.
Case Study
Bardex’s was recently contacted by a returning client that wanted to increase the capacity of its shiplift so they can repair larger vessels. This project was more involved than other projects because it required the removal of all the existing system including; lift equipment, structural platform, transfer system, piping and electrical as well as building and installing replacement equipment, increasing the platform capacity, reinforcing the piers, and supplying a control system based on the latest technology. The facility was commissioned in 1996 with a nominal lift capacity (NLC) of 4,300 metric tons. It consists of a 140m x 22m platform that features dual mode operation, whereby the operator may elect to use a 40 m section of the lift or the entire 140 m length. The outer 40m of platform lifts the smaller vessels reducing wear on the system and energy consumption. The client needed a new NLC of 4,970 metric tons and it was important to change the dual mode configuration to handle smaller vessels of 60 m length instead of 40 m. For the conversion Bardex supplied:
• Concrete Piers and Equipment Foundation: An independent evaluation of the piers and chain jack supporting foundation was conducted to identify areas needing repair and reinforcement. Bardex completed concrete reinforcement and replaced the foundation steel plates that support the chain jack. Two additional chain jacks and supports where added to increase the maximum distributed load (lift density) of the shiplift.
• Shiplift Equipment: Existing chain jacks were removed and replaced with new higher capacity chain jacks. Lift chains were replaced with chains of higher capacity. Larger hydraulic power units and water cooling system was installed so the speed of lift could be maintained with the larger capacity lift equipment. All piping and electrical components were replaced.
• Shiplift Structural Platform: Platform modifications were designed and fabricated by Bardex. The platform was removed from the site and transported to a quayside facility permitting better control of welding and painting. Upgrades include refurbishment and strengthening of the platform structure including cutting 20m from the 100m platform and welding it to the 40m platform, thereby achieving the 60m length. The platform was transported back to the site and reinstalled.
• Transfer System: The facility uses a rail-based transfer system. The ship shop has three repair bays that are accessed using a longitudinal transfer carriage and a pit type side transfer carriage. Bardex designed and constructed new longitudinal and lateral transfer carriages.
• Ship Shop Area Improvements: In collaboration with the client, Bardex delivered design drawings to modify the ship shop to accommodate more vessels. New features include an additional repair bay and a second Bardex side transfer carriage that can lift and transfer vessels for additional flexibility. This improvement reduces congestion in the ship shop area by providing a means to relocate smaller vessels undergoing maintenance more efficiently. Bardex provided basic design to modify the yard to add a recessed pit for installing Bardex sonar dome removal and re-installation handling equipment. This improvement will streamline repair and maintenance of these vital electronic systems.
Photos of assembly and testing of chain jacks in Bardex's CA facility.
Read In the Shipyard: The Art of the Ship Lift in Pdf, Flash or Html5 edition of August 2020 Maritime Reporter
Other stories from August 2020 issue
Content
- Training Tips for Ships #15: Using Student Exam Results to Measure OUR Performance page: 12
- Container Losses in the Rolling Seas page: 14
- Project Cargo and Heavy Lifts in the COVID-19 Environment page: 16
- Interview: Hannan Carmeli & theDOCK: Fertile Grounds for Innovation page: 18
- Interview: Tracy Zea, President & CEO, Waterways Council Inc. page: 22
- Shipping through the Pandemic: Perfect Storm or Wake up Call? page: 24
- Interview: Lasse Petterson, CEO and President, Great Lakes Dredge & Dock page: 36
- In the Shipyard: The Art of the Ship Lift page: 42
- Interview: Heavy Lifting with John DiMartino and Tandemloc page: 46
- Engineering Heavy Lifts: “Clear the Flight Deck” page: 50
- Shipping Community Beware; Sanctions Scrutiny is Stepping up a Gear page: 56