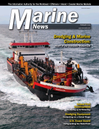
All Operators Should Follow These Lubrication Steps
By Ben Bryant and Steven Brochu
Maintaining mission-critical winches, windlasses and cranes: the four must-have lubrication steps that all operators need to keep gears going.
In the marine industry, winches, windlasses and cranes are the work horses of deck and harbor operations. They can be used to set anchors, position floating drill rigs, raise and lower sensitive scientific equipment, tow a ship, load/unload heavy cargo or even land fish. They are as vital to the mission of a vessel or a port as the main engine is to a ship. And just like engines, implementing a proper lubrication plan can lead to improved performance, reduced downtime and extended equipment life.
A common component of winches, windlasses and cranes are the open gear sets where one or more pinion gears drive a large girth gear. Proper alignment of these gears while also maintaining a high contact ratio of the tooth flanks is critical to the successful operation of this equipment.
A-B-C-D system of Gear Maintenance & Repair
Functional reliability and damage-free operation of large gear drives depend on correct lubrication. That’s because they are exposed to highly varied loads and different operating conditions during their service life, from their assembly to permanent operation under full load. To ensure optimum lubrication at all operational stages and to protect the drives from damage right from the start, a systematic lubrication method can achieve your operational objectives. Each phase of the operation uses a different type of lubricant with the letters A–B–C–D denominating the individual steps of the system:
A = priming & pre-start lubrication
B = running-in lubrication
C = operational lubrication
D = repair lubrication
Lubricants have been developed for every step; suitable not only for the respective operating phase, but also account for the type of lubrication and the method of application.
A: Priming and Prestart
Priming lubricants (type A) are products containing a high percentage of additives and are applied prior to the initial operation of gear drives. They may be used in all spur or helical girth gear drives, irrespective of the lubrication method used. Main benefits include:
- Protecting the teeth against corrosion until the drive is operated for the first time.
- During and after assembly of the drive, keeping the gears lubricated and preventing metallic contact between the tooth flanks.
- Serving as a contrast substance for a first impression of the dynamic load-carrying pattern.
- In drives with automatic spray lubrication, preventing initial scoring caused by deficient lubrication when the machine is started at its nominal speed.
B: Running-in
The initial contact ratio of a gear – even when the pinion(s) and the driven gearwheel are properly aligned – is often no higher than 50 to 60 percent. This means that when new gear drives are put into operation, there is always a danger that partial overloading of the tooth flanks may cause damage. Running-in lubricants of type B are specifically used for the running-in of new or turned gear drives. They ensure that rough surfaces are smoothed quickly and that the contact ratio of the tooth flanks is improved.
During the running-in process, and due to high pressures and point spot welding occurring during initial operation, type B lubricants contain highly effective EP additives to counteract the risk of scoring and pitting damage. The chemical etching and the EP additives smooth the tooth flanks of asperities, which creates optimum conditions to prevent pitting or other damage. This process is controlled by the amount of lubricant used and the time it is allowed to act on the component.
Beyond this, new or turned gear drives should not be operated under full load from the start, because the contact ratio often is initially too low. Instead, they should be run in according to a predetermined load/time schedule, with the transition to the next load stage only being carried out when a specific contact ratio has been reached.
C: Operational Lubrication
Type C lubricants are modern adhesive lubricants tailored to suit the operational conditions of girth gear drives and meet all extreme pressure requirements of gear drives. These lubricants are characterized by:
- excellent adhesion
- good load-carrying capacity
- maximum wear protection
- protection against scoring
- good corrosion protection
These lubricants offer the prerequisites for thin-film lubrication (e.g. base oil viscosity). Consistency, EP additives and solid lubricant content are balanced to ensure that the tooth flanks receive maximum protection even under difficult operating conditions. The transition to operational lubrication is generally made when the running-in process has been completed, i.e., when the tooth flank surface has reached its maximum smoothness and when a contact ratio of at least 80 percent has been attained.
D: Repair
Not too long ago, tooth flank damage was repaired exclusively by highly abrasive mechanical methods – often quite ineffectively. The tooth flank quality obtained often did not meet expectations in terms of functional reliability and service life of the drive. The costs were very high and the repair periods quite long. Today, tooth damage is frequently repaired by means of repair lubricants. These lubricants can repair even heavily damaged tooth flanks to such an extent that the drives can operate under acceptable conditions. In addition, repair lubrication can avoid initial damage becoming more extensive and prevent new damage.
Repair lubricants have a grease-like nature and are adapted chemically and physically to metallic surfaces subject to mechanical, chemical and corrosive wear. Thus a small amount of lubricant is required to remove just the right amount of tooth flank material within a short period of time. The material is worn off evenly at the contact points. Surface wear and, hence, damage repair can be controlled with the amount and application duration of the active compound. The amount of material removal is limited by the thickness of the hardened tooth flank surface layer.
Before starting any repair lubrication, it is of utmost importance to address the primary cause of the existing damage in order to avoid repetition. Repair lubrications are an extremely complex matter. To avoid causing inadvertent damage, this method of repair should only be carried out by trained and experienced application engineers. Nevertheless, if implemented correctly, repair lubrication is a cost-effective alternative to mechanical treatment with considerably less down time.
As Easy as A, B, C (& D)
For open gear configurations in winches, windlasses and cranes, gear alignment is the most important technical procedure for optimum operation. Furthermore, excessive wear and flank damage can be avoided if the intermeshing tooth surfaces are completely separated by a lubricant film. Proper separation, however, is almost impossible in large gear drives due to the low peripheral speed, the very high flank pressure, the relatively high flank roughness and the difficulty in setting the two axes in perfect alignment. As a consequence, large gear drives operate mostly under mixed friction conditions, which make boundary lubrication so important.
To lubricate large gear drives reliably and protect them against damage, the four-step A–B–C–D lubrication process should be implemented during installation, operation and repair to enhance the reliability and operational life of your equipment. It’s as easy as A, B, C, (& D).
The Authors
Ben Bryant is Marine Market Manager at Klüber Lubrication. A graduate of the Massachusetts Maritime Academy, he is a long-time contributor to our pages.
Steven Brochu is a Senior Application & Service Engineer at Klüber Lubrication. He graduated from the University of New Hampshire with a degree in mechanical engineering. Before joining Klüber, Mr. Brochu worked for GE Aircraft in the Fuel Control F16 Fighter Jets Engines department.
Steven Brochu is a Senior Application & Service Engineer at Klüber Lubrication. He graduated from the University of New Hampshire with a degree in mechanical engineering. Before joining Klüber, Mr. Brochu worked for GE Aircraft in the Fuel Control F16 Fighter Jets Engines department.
(As published in the February 2018 edition of Marine News)
Read All Operators Should Follow These Lubrication Steps in Pdf, Flash or Html5 edition of February 2018 Marine News
Other stories from February 2018 issue
Content
- Interview: William P. Doyle - CEO, Dredging Contractors of America page: 14
- Op/Ed: AIWA - A National Asset Worth Funding page: 18
- What Does the Jones Act Mean for Offshore Wind? page: 20
- Managing the Big Risks of Marine Construction page: 22
- All Operators Should Follow These Lubrication Steps page: 25
- Op/Ed: Safeguarding Our Marine Transportation System page: 28
- Demanding Times for DSC Dredge page: 30
- Enhancing Historic Lake Michigan Docking Facilities page: 41
- Virtual Aid to Navigation: Here Now, Here to Stay page: 45
- Marine News Boat of the Month: February 2018 page: 48
- Ports of Indiana: Building on Success page: 236