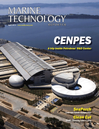
Partnerships Producing Game Changing Safety Innovations
Recent trends toward closer collaboration between operators and contractors—who after all share an interest in avoiding incidents and promoting safe operations—are a good sign for the industry. But it takes the right kind of partners to benefit from the arrangement—an operator must be willing to include its contractor partner in the early stages of engineering and risk assessment, and a contractor needs to have the expertise to advise and support the client effectively. When done well, these kinds of collaborations have the potential to deliver safer and more innovative technologies that benefit everyone. A recent subsea P&A project involving Chet Morrison Contractors and Helix ERT provides an example of an operator/contractor partnership that resulted in a win-win situation for both companies and for the industry as well.
Operator Helix ERT hired Chet Morrison Contractors to provide well plugging and abandonment and diving services on a 2012 4-well Subsea P&A project in the VR, SMI and HI fields. While thorough job planning and risk assessments were performed prior to mobilization, there are always unanticipated challenges once work begins on site. It was at the first location of the project when it was discovered that the bottom profile and specifics associated with the subsea tree would require longer jet time and unwanted risks for the Chet Morrison divers. Together the teams evaluated options, one of which was using existing subsea cutting methods--meaning more resources, time and costs. Because the team from Chet Morrison, led by Well Services Vice President Bobby Lott and Diving Operations Manager Kevin Lord, was working together to perform both work scopes, they were able to offer an alternative option they believed could provide a far better solution. The Chet Morrison team proposed a plan to use a prototype subsea abrasive cutter they developed, and Helix ERT agreed to let them try it on the project.
Chet Morrison’s prototype subsea abrasive cutter worked well, proving to be a more efficient way to cut the casing stubs while also eliminating the need for hand jetting the hard bottom. Not only did the method decrease dive time and increase productivity, but by utilizing a smaller equipment spread the operators benefited from multi-million dollar cost savings. The incident-free project was a success for both Helix ERT and Chet Morrison Contractors. “Even with my diving background and passion for diving, I would always prefer to remove a diver from the equation when technology exists that can mitigate unnecessary risk,” noted Lord, “In this instance, we were able to keep our divers out of harm’s way and save our customer avoidable costs.”
Following on the success from the Helix ERT project, Chet Morrison Contractors spent many months testing and refining the prototype to develop the new assembly, called “SHARC”—Subsea Hydraulic Abrasive Rotating Cutter. With this innovative new subsea abrasive cutting technology, they’ve eliminated the need for hand jetting and decreased the time divers spend underwater performing cuts themselves. SHARC needs only a diver or ROV to position it over the pipe opening—then operations can be managed from the surface. Another advantage is that SHARC can be deployed by Chet Morrison’s 240 foot, 4-point DSV Joanne Morrison, thus avoiding the higher cost of larger spreads. The DSV Joanne and other vessels in their fleet are also able to provide solutions for overcoming mud suction when pulling the stub (up to 150,000 pounds). While SHARC’s specs are comparable to other abrasive cutters, it is a vast improvement on existing methods. SHARC can make clean, even cuts on pipes 2 inches and larger, handle walls up to 3 inches thick, and can cut any size caisson or jacket leg from surface or subsea to depths up to 500 feet. It’s a whole new option in P&A cutting that reduces unnecessary risks for divers—and one that is the direct result of the close cooperation and communication of an operator and contractor who shared a common commitment to safe execution.
The oil and gas industry is often criticized for a perceived disregard for safety or environmental impact. The truth is that operators and contractors are constantly looking for more efficient, safer and less harmful ways to conduct business. The Chet Morrison/Helix ERT job is a useful example of how operators and contractors can work closely together to identify and solve problems, develop new solutions and produce innovations that benefit everyone. Having a single contractor partner also lowers the risk of error or miscommunication by reducing the number of different parties involved. “Because our diving and well services experts worked together as a team, we were able to ensure accurate communication and maintain our extremely demanding standards for safe operation,” said Ryan Vestal, Engineering Manager Well Services.
Another sign of this trend is the recently formed U.S./Gulf of Mexico Diving Safety Work Group (DSWG). A first-of-its-kind alliance between operators and contractors for the purpose of advancing safety in Gulf diving operations, DSWG provides a forum for operators and contractors to work together, sharing best practices and lessons learned. Chet Morrison’s Kevin Lord is an executive board member of the group, where he works closely with operators and fellow contractors to share information with each other in order to improve safety for the entire industry. Owners and contractors acting together to improve safety and reduce environmental impact may not make the front-page—but considering their impact, maybe they should.
DSV JOANNE MORRISON
The Joanne Morrison is outfitted with four-pont mooring capabilities, a moon-pool deployed four-man 1000-ft. saturation dving system and can be equipped with a work class ROV for subsea inspection.
Length 240 ft.
Width 48 ft.
Molded Depth 14 ft.
Main Deck 46 x 125 ft.
Open Deck Space 5,750 sq ft
Deck Cargo-Main Deck 225 tons
Fuel 60,000 gal.
Water 90,000 gal.
Flag USA.
Classification USCG/ABS
Crane Mantis Model 14010
70-ton Hydraulic Crane
Engines 2 x 645 EMDs C Model
Horsepower 1,500
Main Generators 2x 300 kW
Emergency Generator 375 kw
Sat Generator 275 kw
Winches 2 x SMATCO Double Drum
Wire 4x 6,000 x 1-1/4” Wire
Dynamic Positioning White Gill
Thrusters
Anchors 2 x 17,000 lbs.,
2x 15,000 lbs.
Moon-Pool Deployed 4-man 1000’
Saturation Diving System (24”d)
HRC: 4-man Hyperbaric
Rescue Chamber
Diving Station: Deep Air/Gas Surface
(As published in the April 2013 edition of Marine Technologies - www.seadiscovery.com)
Read Partnerships Producing Game Changing Safety Innovations in Pdf, Flash or Html5 edition of April 2013 Marine Technology
Other stories from April 2013 issue
Content
- Underwater Robotics National Challenge set for Indy page: 8
- Partnerships Producing Game Changing Safety Innovations page: 16
- Floating Production System Projected to Grow 40% in Five Years page: 22
- ATIVA Subsea Solutions ‘Made in Brazil’ page: 26
- Cenpes Leading Petrobras’ R&D Effort page: 32
- SailBuoy Unmanned Surface Vehicle for Ocean Monitoring page: 38
- Economics of Dyneema-based Ropes page: 42
- Quiet Efficiency: Working Together to Reduce Subsea Noise page: 44
- MacArtney Shows Sensorbots at Ocean Business page: 56