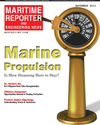
Apprenticeship Training & Academic Degree: The Pathway to Success
Edward Lundquist talks to welder and apprentice instructor Ashley Wilber at BAE Systems Ship Repair’s Norfolk shipyard.
Tell me how you came to be a welder here at BAE Systems Ship Repair.
I have been here at BAE Systems going on seven years now. I was just doing odd jobs out of high school – Hardee’s, driving jobs like delivering pizzas – anything that was making money. I have a cousin, who at the time was an electrician apprentice, and he was telling me about the shipyard. I’d never heard of a shipyard even though I drove past it all the time. I would always look to see if the Disney boat was in the dry dock. I’d say, “Hey, that’s Mickey Mouse. What is it doing in there?” I just never knew what it was.
My cousin told me about the apprenticeship program, and how it was a good opportunity—you go to school, work and get a paycheck. It sounded like something to look into, so I began to research each trade to see what was in high demand and who was hiring for that trade at that time. If things didn’t work out at the shipyard, would I be able to find work? I applied and was accepted. I decided that welding was what I really wanted to do. I was selected, went through my four years, and graduated from with my Associate’s Degree in Maritime Technologies from Tidewater Community College as valedictorian. I was also Virginia Ship Repair Association (VSRA) Junior Tradesman of the Year for the area.
My instructor was my mentor. He was very knowledgeable, and I really looked up to him. Working with him, I was trained and certified as an aluminum welder, and assigned to do 5 XXX critical welding on the cruisers. I became a crew leader directly after graduation. After a couple of months of being a crew leader, I was designated “STRIPES,” which is a supervisor lead person; and a couple of months into that, I was working on the LHDs – the big deck amphibious ships – doing aluminum foundations. The company sent me to Hawaii for five and a half months to help with the removal and replacement of uptakes on the USS Port Royal and USS Chosin. I was a welder on the Port Royal, then a supervisor on the Chosin, and led the crew out there. We finished a couple months ahead of schedule; I was very proud of how that job came out. When I returned to the yard in Norfolk, I wanted to see what it was like on the other side of the “green line.” In the shipyard, there’s a green line literally painted on the ground. On one side is the production area where you have to wear all of your safety and personal protective equipment. The other side is the offices, and guys that get us the work out here on these ships.
So you took an office job?
I applied to be a contract estimator, and got a position estimating on government contracts. A lot of times, as you get into the availability, a job will grow, and requires additional funding. I would estimate it, and negotiate a reasonable price with the customer to fix that certain item. But after about nine months I realized that I still wanted to weld, and be a part of the weld shop. The desk was not for me. Sadly, my mentor passed away and his position became open. My instructor motivated me, pushed me through and showed me some good skills that I felt I could pass on to the up and coming apprentices. I talked to the head of the shop and told him I really wanted to be an apprentice instructor. I was chosen for the position. Now I’m an apprentice instructor and a craft supervisor. My first priority is the apprentices, but I also help out with certain jobs on the ships, and maintain procedures and certifications, and I certify everyone in the yard who is qualified to weld—subcontractors, welders, ship fitters, and mechanics. If you are going to weld any type of material, you come through me first. We are in the process of getting new procedures and certifications so we can be able to weld different things—the more we can weld, the more work we can get.
When you are instructing apprentices, do you have anything to do with their classes at school?
I am involved as far as keeping them up on their grades, their attendance and their studies. If I get a report that a person is not doing so well, I pull them in and talk to them, and let them know about tutoring or other classes or resources that are available to them. They have core classes such as English, reading, and math. The apprentice program trains you for leadership, with public speaking classes along with Excel and PowerPoint. But when you first get into the program you also have a class called “Ships Nomenclature.” For me, since I had never been on a ship, this class was my first introduction to the shipyard. I learned how to get around on a ship, tie knots, and basic safety practices. Some people take it lightly, but it’s a very important class, and if you have never been on a ship, it’s vital.
What’s involved with the welding school, and what do you teach there?
The company made a significant investment in a new training facility. My apprentices rotate through the weld school every six months and receive different certifications each time. Mechanics that come through are given the same training and guidance as an apprentice, just in a shorter time. I train them all to do good quality work on the vessels.
Is it a case where some people pick things up faster, and others may take a little longer to get certified?
Some need a little extra guidance. That’s why they come to the school. I don’t hesitate to grab my welding gear and give them a demonstration of what I expect of them.
So a welder here at BAE Systems Ship Repair doesn’t specialize as an aluminum-only welder, or a steel welder. They’re going to learn how to weld steel and aluminum.
The more certifications you have the more flexible you are. We try not to limit a welder. If we feel you’re capable of receiving a certification, we go ahead and try to give it to you. Some have a harder time grasping a concept, so we let them work with what they have and try for additional certifications at a later time. Aluminum takes more skill and patience than standard steel certifications.
Why is aluminum harder?
The testing is much stricter. For example, when they conduct NDT—nondestructive testing—they put dye penetrate on it and if it bleeds through, then it’s a bad weld. Steel is not as strict. Some ships have superstructure made out of aluminum, and with all the twisting and turning from the ship, that soft material cracks easily. Aluminum is a lightweight, soft, low strength metal. Every time you get a ship in here it’s going to have some aluminum cracking. The processes we use to weld aluminum gives you a highly concentrated heat zone to prevent distortion.
As a craftsman, what’s the difference between welding steel and welding aluminum?
With steel, you can weld, clean it and get your supervisor to do a visual test and you can walk away. Aluminum is a completely different material; and it’s inspected to a higher standard than steel. It has to be good, sound metal; look good; be clean; and stand up to the non-destructive testing process. It’s just not getting a visual inspection, they’re actually conducting test. With 5XXX aluminum, every weld pass has to be checked by a QA inspector, which takes more time to finish the job. If it is not done properly, it will show. Basically, there is no way to cover up bad welding with aluminum.
Do you use robotic welding?
We have machines—called Moggies—in the shop that we were testing and getting certified on to weld different material in different positions. We have an aluminum Moggy for our big inserts. The way it works is you set it up, set the temperature and put it on track and instead of someone sitting there taking three days to weld it by hand; you can take a few hours and get the job done right and in less time.
Do you still need a certified welder to set that up?
You have to be certified. We go through the whole process of checking every layer as if it was on the ship as a critical weld in a controlled environment passing the non-destructive testing. The yard itself is certified and we do have certified mechanics.
So that would be something that you would do in a fabrication shop before you bring it over to the ship.
Yes. We have a fabrication shop in the yard where we put together a lot of big pieces then take them to the ship to be installed.
What do you find to be the most challenging part of teaching welding?
The different people . Everyone has different personalities, and they learn at a different rate. What one person may get, others may not, so you have to spend more time with them. Sometimes an apprentice does not understand a particular certification and I have to skip over that procedure with them. I research different ways of explaining and teaching different processes. I don’t know it all and I have to do my own research. So if I have a person that’s struggling on one thing and I feel that I’m not getting through to them, then I will try to find a different way to show them that they may grasp.
What do you find most gratifying about teaching apprentices?
When they get it after I have shown them different ways of approaching it. When they pass the test, they smile and feel good about themselves—it’s like a kid at Christmas. I feel good because I helped them do something that they are proud of. I feel like I’ve had a good day if I helped at least one person.
What do you see for you in the future?
I’m not sure. I’ve already been over in the office, but I wasn’t ready to get away from the shop. I wasn’t ready to leave welding. I still go on the ships regularly and might come back over the green line, you never know. But for now, I’m happy where I’m at. Welding is my passion. If I’m not welding, I would like to help someone else learn how to weld.
Do you see a greater influx of women getting into the program?
As far as welding goes, I have seen it grow in the apprenticeship program. We’ve gone from one to two females, and now we have five. I see it continuing to grow. They say females make better welders, anyway. We have a steady hand.
I think over the years people think of welding as a man’s job, but people are now realizing that it’s a profession, a trade that anyone can aspire to. So what would you say to somebody who was thinking about becoming a tradesperson, perhaps in the ship repair, ship building industry?
Do your research. Look into it and make sure that’s what you want to do, especially working in the shipyard. You’re outside working in the elements. You might get wet, and maybe you can’t weld that day. You’re producing heat, and maybe it’s already 90 degrees out there. So you have to be prepared for it. Some people think about welding equals money. That’s all good and fine, but you have to like what you’re doing first; you have to want to learn; and you have to get good at it so you can make money. You have to have that passion. You have to get into it.
Is welding something that virtually anyone can learn, or do you need to have an aptitude for it?
If you asked me this a couple years ago, I would have said anybody can weld. When I was an apprentice, and would go out on the boat, and all around me were guys that could weld; who had passed the test; and had the experience. But now, as an apprentice instructor and seeing students come in straight from high school, or maybe different companies where they did more book work and not so much hands on welding, I see now that it’s not for everyone.
Do you ever sometimes think about what you would be doing if you hadn’t become an apprentice here?
I would probably be looking in the paper for a job, seeing who is paying the most. I don’t know. I do know I’m glad I am here at BAE Systems at this point in my career. I would not want to be anywhere else right now.
(As published in the November 2013 edition of Maritime Reporter & Engineering News - www.marinelink.com)
Read Apprenticeship Training & Academic Degree: The Pathway to Success in Pdf, Flash or Html5 edition of November 2013 Maritime Reporter
Other stories from November 2013 issue
Content
- Interview: Dr. Herbert Aly page: 12
- Knowledge is Power page: 16
- ReFRESCO: Understanding & Designing Energy Saving Devices page: 18
- Nontank VRP Regs page: 20
- The Magic Ingredients of a Healthy Safety Culture page: 24
- e-Compliance: Revolutionizing the Efficiency of Compliance for Maritime Regs page: 28
- Pull the Handle Down... page: 30
- Return of the Electric Boat page: 38
- Fast Ferry Gets a New Power Package page: 42
- Cat tackles Tier 3 and Tier 4; Completes Berg Deal page: 44
- Konrad, Cummins Propulsion Package Partnership page: 46
- Scania 13L Inline; 16L V8 for EPA Tier 3 page: 48
- The Switch: New Drive Train Tech page: 48
- John Deere Tier 3 Engine Line Up page: 49
- GE Power Conversion page: 49
- EPA’s Vessel General Permit (VGP) & You page: 50
- Are PAGS the Answer? page: 51
- Don’t Forget: Seawater is a Free EAL page: 51
- Lukoil: Cylinder Oil to Reduce Wear, Consumption page: 52
- Agip Rebrands as Eni Powers Ahead in North America page: 52
- Floating Production Systems: Market Update page: 54
- Offshore Brazil: The Libra Field & Brazil’s Pre-Salt Policy page: 56
- On Ballast Water, Time is Running Out page: 60
- Standardization for Safer Shipping of e-Navigation & Training page: 62
- Apprenticeship Training & Academic Degree: The Pathway to Success page: 64
- The Drawing Board: Innovative OSV Design from the Ground up page: 68
- Product Tanker Hijackings page: 72
- The Trinidad & Tobago Maritime Sector page: 74
- Seatorque Boost for Brazil’s Biggest Superyacht page: 76
- Raytheon Anschütz Launches New Gyro Compass page: 85
- Emsys Upgraded to Measure Mass Emissions Rates page: 85
- Thuraya SatSleeve Transforms iPhone into Satellite Phone page: 85
- Kongsberg Debuts New Drilling Rig and Ship Simulator page: 85
- Martek: “BNWAS Password Protection is Essential” page: 85
- Northrop Grumman Radars for USN page: 85
- Imtech Debuts SeaPilot 76 page: 85
- FORAN in Indonesia page: 85
- Raymarine Autopilot page: 86
- Computer Gaming & Maritime Training page: 86
- Jeppesen Updates VVOS Software page: 86
- Harris CapRock & Carnival Sign Contract page: 86
- Carlisle & Finch SmartVIEW Technology page: 86
- Thomas Gunn Unveils New Digital Chart Management System page: 86
- CM-1000 Series: Smart Fluid Handling Tech page: 87
- Paperless Navigation page: 87
- TNKC Fleet & BASS Software page: 87
- Cobham Touchscreen Navtex page: 87
- GE Dynamic Positioning System page: 87
- Ecospeed Fuel Savings Calculator page: 87
- Boatracs’ BTConnect AIS page: 87
- New Brakes from Wichita Clutch page: 88
- Home Study Programs page: 88
- New PowerShark Tool Eats through Biofouling page: 88
- VIKING Expands Training page: 88
- SUPREME Athmos Zero-Pollution Seal page: 88
- New Inertia-Engaged Turbine Air Starter page: 88