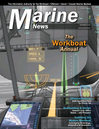
From Across the Big Pond
By Kathy A. Smith
With familiar faces, new partnerships and Houston office, Damen widens its North American profile with a flurry of new work orders.
With a flourish and a flurry of new business, Damen’s new U.S.-based office officially opened in Houston, Texas on July 1, 2016. Registered as Damen Area Support North America BV Co., it has been established to provide a local presence and work hand-in-hand with the North American market, offering a full range of ready built, standard and custom design vessels as well as the products and services of Damen Shipyards group ‘License to Build’ program. In addition, the new office also represents the ship repair and conversion side of the group. It would not be overstating the obvious to say that Jan van Hogerwou, Damen’s General Manager of New Construction (North America) hit the ground running and hasn’t stopped since.
Fast Start in a Slow Market
In its first three months of operation, the new entity secured contracts for 27 new tugs that are planned or under construction for several different customers, most notably a total of 13 heavy duty mooring assist and escort tugs for two oil projects, an impressive feat coming during a depressed gas market, and a boon for the leader whose proven tug design niche continues to grow.
For example, Edison Chouest Offshore (ECO), has teamed up with Damen to build a total of 13 heavy duty mooring assistance and escort tugs. These will be deployed on two major maritime projects for which ECO has recently won contracts, based in part on the use of well-proven Damen tug designs. The vessels will be built using ECO’s network of five shipyards and Damen’s support and expertise.
The first of these is a contract that ECO won earlier this year with a new Corpus Christi based LNG export terminal. The agreement is for the supply of four escort tugs with a bollard pull of 80 tonnes, to operate at this new LNG terminal in Texas, which is currently under construction. The Damen tugs will be of the well proven escort / mooring ASD 3212 design.
More recently, ECO won a high profile, long term contract in Alaska. ECO is taking over the ship escort duties out of Valdez, Prince William Sound, from July 2018, for which it will require nine, high-powered escort tugs. For this environmentally-sensitive project, Damen and ECO will work together to deliver four more ASD 3212 tugs with a bollard pull of 70 tons each and five of the most powerful ASD tugs ever built; the ASD 4517 with a bollard pull of 150+ tons, is a joint Damen and ECO developed escort tug specifically designed for the sometimes challenging weather conditions in the Prince William Sound.
Future operations from the new tugs in this environmentally-sensitive region have some local residents and stakeholders concerned that the high standards of previous work will continue to be carried out. Addressing those worries, ECO responded by building safe, Tier 4, technologically-advanced vessels for this demanding work.
Jan van Hogerwou, GM New Construction Damen Area Support North America at the Houston office explains, “In terms of Edison Chouest, we are providing our designs and our knowhow and our engineering capacity. We have engineers that are presently working at Edison Chouest. We have our research team in the Netherlands that is doing all kinds of tow and escort predictions and calculations, so we’re a true partner on these projects with Edison Chouest.”
“Chouest was pleased to have this opportunity to take Damen’s proven hull design and helped create a new, state of the art escort design representing the most powerful ASD tug ever designed or built” said Gary Chouest, President/CEO of Edison Chouest Offshore.
Market Penetration 101
According to van Hogerwou, 95 percent of standard vessels start the production cycle without an owner, and at 50 percent of the cycle, 80 percent of the tugs are sold. “That is a business model that no one in the world of shipbuilding has copied so far,” he says. “And it’s very difficult to copy because that’s a portfolio that takes decades to build up.” That’s because Damen, the global shipbuilder, has more than 30 yards all over the world and has over time arguably mastered the art of series-build spec tonnage which can then be modified and customized for multiple mission sets.
Helping customers keep construction costs down is one of Damen’s market differentiators. “If you do a first of a series shipbuilding, and that’s for any shipyard in the world, the first of the series is usually a ship that will cost the shipyard money because it’s a big learning curve in how to build that ship,” he says. “We’ve already done that. We send our planners and then our construction supervisors to these yards and they’ll stay there for the entire production cycle of the ship to help our customers, our shipyards and our partner yards in building these ships as economically and efficiently as possible.” On this side of the pond, especially in the Jones Act trades, Damen isn’t here to compete with shipbuilders. They’re here to help.
In August of this year, a keel laying ceremony took place at Great Lakes Shipyard for the first of ten Damen Stan Tugs 1907 ICE to be built for The Great Lakes Towing Company. The vessels (GLS Hull Numbers 6501–6510) will be built to ABS Class, and are the first tugs being built to meet the new USCG Subchapter M Regulations. It is good timing to be replenishing the fleet now because many of the upgrades that would be necessitated by Subchapter M will be easily incorporated in the new tugs, says Joe Starck, President of The Great Lakes Towing Company. The new tugs will be a modern-day version of the Towing Company’s traditional low profile ship assist tugs that have been in service across the Great Lakes for many years.
Two new harbor tugs per year will be introduced for the next five years. Damen is providing full design and engineering support. “We operate our tugs in multiples, as opposed to using a single high horsepower tug,” Starck says. As far as the newbuilds, he adds, “They will help us to not only improve the reliability of our fleet for our customers, but also allow us to expand to other ports where we currently don’t have tugs stationed.”
Starck says going with Damen was an easy choice since the two companies entered into a licensing agreement two years ago where Great Lakes Shipyard offered its customers readily available engineering packages previously produced by Damen. “Damen is providing us with what we call a U.S. variant of their European design. It’s the same exact hull form, just modified by them to meet U.S. rules and regulations with regard to tonnage and stability and any other U.S. Flag requirements necessary for our harbor towing application.” In other words: hands across the water.
Separately, four new Damen Stan 3711 tugs are being built for Young Brothers, Limited of Honolulu, Hawaii by Conrad Shipyard in Morgan City, Louisiana. The construction is being undertaken under a ‘license and materials’ agreement with Damen Shipyards Group. Young Brothers, a Saltchuck company operated by Foss Maritime, is Hawaii’s largest inter-island cargo service provider. The first vessel will be delivered in the first quarter of 2018 and the last, twelve months later.
“We are investing to serve the Hawaiian Islands for decades into the future. These new tugs are a perfect match for our higher capacity barges and will improve reliability, efficiency and on-time service,” said Young Brothers President and COO Glenn Hong in a recent statement.
The four new twin-screw tugs are 123-feet in length with a 36.5-feet beam and powered by G.E. 8L250MDC engines rated at 6,000 horsepower. Designed for high stability and maneuverability, the tug has a maximum bollard pull of 80-metric tons and a top speed of 12.5 knots.
“Damen’s approach to standardizing their design and materials is impressive and it’s a major advantage that they bring to the table,” explains René J. Leonard, VP Business Development and Engineering for Conrad Shipyard. “The number of vessels that they produce worldwide provides the company with excellent leverage in economies of scale, resulting in lower cost to the customer. Their process of shipping materials to us on an as-needed basis allows us to streamline manufacturing schedules and is extremely cost-effective,” he added.
Leonard says having Damen as a strategic partner is beneficial not only in design and construction, but also with worldwide coverage for warranty and aftermarket support for spare parts and repairs. “In this instance, with the vessel operator located in Hawaii where access to vendors and suppliers is not easy as elsewhere, Damen’s global footprint and rich history of providing these resources is a significant benefit to our customer.”
Market Differentiators
Damen’s van Hogerwou points out that most shipyards don’t have their own service and support and maintenance team in place. He explains, “We have a whole team available 24/7 that will respond to technical issues, and with our buying power and leverage, we can ensure the quickest turnaround possible.” Backing up that promise, the family-owned global shipbuilder operates 30+ yards worldwide, and more than 200 vessels have already been built or are being built to Damen designs at U.S.-based shipyards, including over 100 for the U.S. Coast Guard.
The Coast Guard piece of the puzzle is important. That’s because more than ten years ago when the Coast Guard’s ambitious multi-million dollar conversion plan to rebuild and modernize a fleet of 20-year-old 110-foot patrol craft ran aground as the rebuilt hulls began to crack – one after the other – the next newbuild plan specified just one key ingredient: the hull design had to be a proven one. The Coast Guard turned to Damen.
Damen has grown from a staff of just six in 1969 to over 10,000 employees. To date, Damen has delivered nearly 6,000 vessels; approximately 4,200 of those are tugs – the ultimate workboat by any definition. Obviously, with that track record, it’s no wonder the company is trusted worldwide due to its proven hull form(s) and the ability to quickly and competently build a series for a certain size vessel and a wide variation of hulls on spec that can be fully customized and full support services.
“We have 800 to 1,000 naval architects, engineers on our payroll,” says van Hogerwou. “They do nothing else but design ships and make specific custom requested changes to these designs. So we go from absolute 100 percent standard design vessels to 100 percent custom designed and everything in between.”
Getting off to a fast start with these new contracts, van Hogerwou is clearly very optimistic. Over time, he expects the Houston commercial office to grow in size with sales, support and technical staff, but at the same time, will stay small enough to comfortably support its market. “We’ve always been convinced that we needed to be close to our customers,” he says. “Now we’re in the same time zone. They can reach Damen literally 24/7.”
Damen designs are familiar, iconic, and widely used on this side of the pond already. The new office, opened during an unquestionably difficult market, is off to a fast start. With tugs representing Damen’s bread and butter globally, the future looks bright for Damen in North America, and the presence of its office in this market means more work for U.S. shipyards. And that can’t be a bad thing.
Damen Designs: Hands Across the Water
Damen Design - Number - Customer - Builder/Yard
Damen StanPatrol 2600 - 74 - U.S. Coast Guard - Bollinger Shipyards (1994 – 2016)
Damen StanPatrol 4708 (FRC) - 36 (of 58) - U.S. Coast Guard - Bollinger Shipyards (2011 – present)
Damen ShoalBuster 2609 - 1 - Weeks Marine - Eastern Shipyards (2005)
‘1204’ Fast Crew Supplyboat - 40 - CITGO - Horizon Shipbuilding (2013 & 2014)
‘1605’ Fast Crew Supplyboat - 25 - CITGO - Blount Boats (2013 & 2014)
‘1204’ Fast Crew Supplyboat - 15 - CITGO - Trinity Shipyards (2013 & 2014)
ASD ‘3212’ tugs - 8 - Edison Chouest - North American Shipbuilding (2016)
ASD ‘4517’ tugs - 5 - Edison Chouest - North American Shipbuilding (2016)
Stantug ‘3711’ - 4 - Young Brothers - Conrad Industries (2016)
Stantug ‘1907’ ICE - 10 - Great Lakes Towing - Great lakes Shipyards (2016)
The Author
Kathy A. Smith is a Victoria, BC-based maritime writer who has penned over 100 published trade articles.
(As published in the November 2016 edition of Marine News)
Read From Across the Big Pond in Pdf, Flash or Html5 edition of November 2016 Marine News
Other stories from November 2016 issue
Content
- [Op/Ed] WRDA: Dredging up Progress page: 20
- Catching the Electric Vision page: 22
- Workboat vs. Jet Ski: A Mysterious Collision and Its Consequences page: 26
- Clear Contractual Language: What Are You Agreeing To? page: 30
- What to Know When Welding Primer-Coated Steel page: 34
- As Operators Look for the Bottom, Gulf Gloom Persists page: 38
- All in a Day’s Walk page: 46
- From Across the Big Pond page: 54
- Repair Yard Detyens Taps into Key Niche Markets page: 60
- Ship Intelligence 101 page: 66
- Lubricants: Mitigating Risk without Sacrificing Performance page: 74
- Tech File: Vesconite Rudder Bushings page: 84
- Digital Technology Enhances Marine Communications page: 90