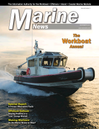
Connecting Boatbuilders to the New Gold Standard
By Joseph Keefe
Victaulic’s forward-thinking vertical integration remains, at the same time, solidly connected to a rich and varied past.
It is still common to hear waterfront stakeholders refer to alternative pipe connection systems as temporary or simply as ‘a new development.’ While none of that could be further from the truth, the education of the marine community as to the merits of these products as an alternative to traditional flanges continues. These products – like Victaulic’s market offerings – are indeed mainstream parts of the marine sector, their use limited only by the imagination of designers, builders and operators who constantly find new applications to improve their bottom line.
Historical Primer: Always Functional, Anything but ‘New’
Since the 1920s, Victaulic couplings have demonstrated their value in countless maritime applications. As early as the late 1920’s, Victaulic had the sanction of Lloyds’ Register and Bureau Veritas. Back then, boatbuilders first used the product for water supply and sanitation because of their flexibility, reliability, tolerance for vibration, safety, ease of access and ability to accommodate expansion and contraction. That hasn’t changed. Later, during WWII, Victaulic couplings were installed in thousands of piping systems of merchant and navy ships in expanded roles that included solutions for bilge, ballast, freshwater, saltwater, sanitary and deck drains, fuel oil fittings and transfer, fire mains, cargo systems and more.
It was during the war that the ease and quickness of installation became just as valuable as the versatility of the product itself. The need to quickly mass produce a fleet of ships to counter overseas threats required efficient assembly and manufacturing in all phases of shipbuilding. Victaulic’s pipe coupling systems became an integral part of that successful effort.
In 1975, Victaulic continued its expansion as it purchased NJ-based Apex Galvanizing Corporation. The move enabled the firm to provide galvanized pipe, couplings and fittings used in many applications to withstand the corrosive, rust-causing effects of condensation. For example, Apex galvanized brackets and support stands were used in the USS Michigan Trident series of ballistic missile submarine for the US Navy. Beyond that, Victaulic’s method of pipe joining has today penetrated many aspects of commercial vessel newbuilding and repair alike.
The Rule, Not the Exception
Long thought to be a ‘temporary’ solution to permanent piping tasks, the alternative to traditional flanged piping is fast becoming, instead, the marine standard. That’s because there is no aspect of piping that can’t benefit from the use of Victaulic hardware.
Myriad piping materials are used on the waterfront. In addition to Carbon Steel Pipe, Galvanized piping, Stainless Steel Pipe, Aluminum Pipe, and CPVC are growing in popularity. These materials require special skill sets and preparation if ‘traditional’ piping methods are followed. With Victaulic grooved products, the skill sets are modest and nearly identical for any of these piping materials. ‘Traditional’ piping methods (such as welding) can take years of experience to become efficient and productive. With Victaulic grooved products, the learning curve is shortened to a matter of days.
Piping repairs or alterations in confined spaces – like the coming ballast water treatment tsunami – often involve work in confined, hazardous areas. In these instances, welding can include risk of fire, poor ventilation, poor access to all sides of the piping to insure complete weld passes are completed, and difficulty in “fitting” pipe and fittings around existing piping or electrical lines. And, for those engineers who still insist on using traditional flanges, the much smaller physical footprint of an easily rotated Victaulic joint can (and should) change their minds as they try to thread that BWTS system through an already crowded pumproom. Victaulic piping products address all of these issues, and more.
It is important to define what Victaulic is, and what it is not. No solution is the ‘be all-end all’ for all projects. For example, Victaulic is not – as yet – approved for use in hydraulic lines, starter air, and a few other applications. Separately, Victaulic’s in-house robust pressure testing and QA schemes are impressive. That said, and with respect to allowable working pressure, Victaulic ABS type approvals limit systems to 16 bar or 232 psi. It’s also important to note that Victaulic Style 77 couplings are rated up to 1,000 psi for everyday applications. That’s a big safety factor for any vessel.
When one considers that the standard charter party language for a tanker voyage agreement specifies 100 psi or about 7 bar at the discharge manifold, it’s obvious that there isn’t too much the average vessel can’t depend on Victaulic couplings to address. The list of Victaulic’s approved services and applications is, conversely, simply voluminous. And, Victaulic manufactures solutions ranging from ¾” and up past 12’ (feet) in diameter. It isn’t uncommon to see Victaulic applications used for 20” ballast lines – much larger ranges than most of its ‘alternative’ piping connection competitors.
Applications & Approvals Abound
With approvals from ABS, DNV-GL, LR, KR, RINA, CCS, the U.S. Coast Guard, BV, and more, there aren’t too many things that Victaulic can’t address. No one solution stands out as the most common application; Victaulic reports that its sales are evenly distributed across a wide spectrum of marine projects. The table depicted below is not all inclusive, but is nonetheless eye-opening.
Grooved Pipe Joining Technology 101
Victaulic’s approach to pipe joining is quite simple and equally robust.The groove is made by cold forming or machining a groove into the end of a pipe. A gasket encompassed by the coupling housing is wrapped around the two grooved pipe ends, and the key sections of the coupling housing engage the grooves. The bolts and nuts are tightened with a socket wrench or impact wrench. The advantages of using such a system are many.
Unlike a rigid coupling, a flexible coupling allows for controlled linear and angular movement, which accommodates pipeline deflection as well as thermal expansion and contraction. Through a design that allows for full rotation of the pipe and system components before tightening, Victaulic’s ease of alignment is a primary hallmark of its value. Noise and vibration attenuation is achieved by isolating the transference of vibration at each joint.
Once installed, couplings engage the pipe grooves to hold the pipes against full pressure thrust loads without the need of supplemental restraints. And, Victaulic gaskets – unlike flanged systems which are manufactured with asbestos material – have a much longer life cycle than the standard flanged gasket.
Monetizing Your Victaulic Advantage
A long time ago, someone told me: if something needs to be sold to a potential customer, then that service or product needs to be distilled down to its lowest common denominator; in other words, money. The Victaulic route, in terms of hardware alone might actually be slightly more expensive on the front end. Amortizing that nut on the backend is easy to monetize, and surprisingly, it more than pays for itself in a hurry, sometimes before the installation is even complete. Those savings come in the form of lower life-cycle costs, the elimination of hot work, reduced labor and a proven shortening of even the simplest of jobs.
Need more reason to switch? The markedly shortened training time (as compared to welding) to bring labor up to speed – especially shipboard personnel – can be a huge advantage. And, any vessel that spends less time alongside for repairs is therefore available to spend more time earning money. Finally, any vessel – your workboat, for example – that leverages the use of Victaulic across the full range of applications, from bilge to bow, boasts a lighter tonnage profile with increased physical footprint for other equipment, cargo and/or much-needed elbow room.
Vertical Integration: the Victaulic Way
Any student of boatbuilding history and operational processes knows that vertical integration – the connection of the shipyard to the steel manufacturing capability – is one primary key of shipyard economy and success. At Victaulic, their take on vertical integration involves delivering innovative pipe joining solutions that leverage a one-stop-shop approach of in-house control of all tools, material production, training, service, sales, and everything in between. Augmenting all of that is Victaulic’s Cost and Labor Analysis, Weight Analysis, Jobsite Training, and Installation Inspection that accompanies each sale.
The one-stop-shop: Is Victaulic’s unique and turnkey approach to pipe joining right for you? That depends on a lot of things, but if better design options and a measurable benchmark of Total Installed Cost Savings would benefit your bottom line, then you’ve got nothing to lose and everything to gain by trying. Since before 1920, that’s been the rule, and not the exception at Victaulic.
(As published in the November 2017 edition of Marine News)
Read Connecting Boatbuilders to the New Gold Standard in Pdf, Flash or Html5 edition of November 2017 Marine News
Other stories from November 2017 issue
Content
- Interview: Rear Adm. Mark Buzby, US Maritime Administrator page: 12
- Preparation Propels Financial Peace of Mind page: 20
- Catching a Jones Act Seaman’s 'Golden Parachute' page: 24
- Leadership and Subchapter M page: 28
- Op/Ed: Making the Mississippi River Mightier page: 34
- Op/Ed: Facts Do Matter - A Defense of the Jones Act page: 38
- Marine Fuels: Unmasking Gas page: 42
- A Sea Change for Shipbuilding page: 46
- GoM Stakeholders Energized Despite Lingering Oil Bust page: 52
- Federal Waterways Infrastructure Outlook page: 62
- Brunswick: Ramping up Quality for the Long Haul page: 70
- Marine Piping: It's Not Rocket Science page: 76
- Connecting Boatbuilders to the New Gold Standard page: 82
- Ferry Operations: A Tragedy Averted page: 86
- Connectivity for Brown Water Operations page: 90
- New Grease Extends Life, Lowers Temp of Tugboat Shaft Bearings page: 92
- The Digital Voyage: 'Onboarding' Shipping to the Digital Age page: 94