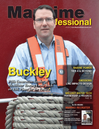
The Impact of LNG Fuel on Commercial Ship Design
The variables are many and the price of not carefully considering each and every one, costly.
Maritime industry stakeholders continue to look for new solutions to address the quickly evolving requirements for reduced emissions from vessels navigating in the coastal waters of North America and Northern Europe. At the same time, new Environmental Control Area (ECA) requirements are likely to spread to other coastal regions of the world and after 2020, the sulfur content in fuel worldwide is slated to be reduced to 0.5%.
Liquefied Natural Gas (LNG), according to many, provides the best solution to meet the ECA requirements. LNG is clean burning, easily meeting the SOx requirements in the ECA, while offering much reduced particulate matter (PM) emissions as compared to most oil fuels (one of the US EPA’s stated goals for the ECA is PM reduction). Beyond its clean burning characteristics, it has the added benefit of being lower in cost than low sulfur diesel oil or other alternate fuels under consideration, such as methanol.
While the widespread introduction of LNG as a marine fuel may be seen as a new development, LNG actually has a long history as an engine fuel on LNG Carriers (where the natural gas evaporating from the cargo tanks is consumed in the engines or boilers) and in shore-side natural gas fired engines. Nevertheless, it is important for anyone thinking about making the change to LNG to be aware that its adoption can have significant impacts on a ship’s design and operation. Those key impacts were the subject of a presentation given by Herbert Engineering at the Shipping Insight 2014 Marine LNG Symposium in Stamford, CT on September 30, 2014. It is worth summarizing those impacts, with a focus on issues related to on board LNG storage, for anyone looking to jump on board the LNG bandwagon.
Key Impacts of LNG Fuel on Ship Design
Looking at the big picture, changing to LNG fuel does not involve a major change in the basic configuration or propulsion plant design of commercial ships. The ship and engine room will basically still look the same, except for a few unusual looking tanks and a few specially colored pipes and boxes in the engine room. Industry can adapt to this new fuel, just like it did when going from wood to coal to distillate fuel to heavy fuel over the course of the past 150 years. However, more so than with previous fuels, the storage and handling issues of LNG are complex, involving as they do a fuel which is highly flammable in its gaseous state and is stored at cryogenic temperatures. These characteristics mean more planning and engineering are needed from designers and owners in the construction and operation of LNG fueled vessels than was needed for oil fueled vessels.
In comparison to oil fuels, the major impacts of LNG fuel on ship design can be summarized as follows:
LNG Fuel Storage – Many Decisions
Unlike oil fuel, which can easily be stored in hull structural tanks with only a few restrictions on possible location, there are typically few simple answers to the questions of where and how to store LNG on board, and LNG storage is not space efficient. Some of the key issues to consider include the fact that LNG Storage requires more volume than oil fuel because of its low density, but it does contain more energy (heat value) in each kilogram, partially compensating for the lower density. Specifically:
- Density: LNG (0.45 t/m3) < HFO (0.98 t/m3); Ratio about 2.18
- Heat Value: LNG (49 MJ/kg) > HFO (40.6 MJ/kg); Ratio about 0.83
- Combined LNG/HFO Volume Ratio is 1.8, meaning it required 1.8 times more LNG tank storage volume to get the same engine output as from oil fuel.
- Tank shape (frequently cylindrical) and insulation further increase the space required for LNG tanks.
- Overall, 3 to 4 times more volume onboard may be needed for LNG storage than for oil storage tanks offering the same range.
- On many ships oil fuel storage is also required as a backup in case of lack of availability of LNG – further increasing the volume on board dedicated to fuel storage and likely reducing available cargo space.
Tank Location on board is impacted by safety requirements limiting the size and location of the LNG tanks. Every cubic meter of LNG storage has a high cost so the tendency is to minimize LNG storage volume on board, reducing the vessel’s range. Selection of storage tank type depends on the vessel size, type, route and gas usage profile – no one type is best for all. Portable Containerized Tanks and IMO Type C pressure tanks offer convenience since they are built off site and easy to drop in place, but for long range and large volume, the built-in prismatic IMO Type A and B tanks or Membrane tanks provide much more volume in the same space and lower cost per cubic meter (same tanks as used on LNG Carriers). In the intermediate range of required LNG storage capacity of 1,500 to 3,000 cubic meters, tank types A, B, C, & Membrane are all practical and a detailed analysis of the costs and benefits of each should be carried out to optimize tank selection, and potentially save significant amounts of money.
Reduced range leads to more frequent bunkering, which can be disruptive to operations and crew work time in port. Beyond this, bunkering may be needed on every round-trip voyage for a Jones Act vessel in coastwise or offshore trades (Puerto Rico, Hawaii, or Alaska).
LNG Tank Location – Protection from Damage Limits the Tank Size
LNG becomes highly flammable natural gas when exposed to ambient temperatures (such as from a leak or from damage) so LNG storage tanks are required to be away from the side and bottom of the ship to minimize potential damage from collisions and groundings. The requirements for LNG fuel storage tanks are more severe than for LNG cargo tanks on LNG carriers because of the concern that cargo ships using LNG fuel will not get the special attention that LNG carriers do, and thus will be as prone to collisions and groundings as any other ship.
According to the existing IMO Resolution (MSC285(86)) for LNG fueled vessels and the draft IGF Code (International Code of Safety for Ships Using Gases or Other Low Flash Point Fuels) slated to go into effect within the next few years, LNG storage tanks need to be away from the hull as shown in the figure by Beam/5 for the side clearance and Beam/15 for the bottom clearance (and a double bottom is necessary). However, the new IGF Code is expected to allow the creative naval architect to expand the space available for LNG storage tanks (the hatched area in the figure) up to the minimum allowed distances of 0.8 to 2.0 m from the side, depending on tank volume, by using probability based damaged stability analysis. This is one area where ship designers can directly aid the owner in getting more fuel in the same space on board.
Besides limiting tank width, the IGF Code will also limit the overall length of LNG tanks to 12% to 18% of the ship’s length for cargo vessels. The final value has been left for decision when the MEPC votes on final adoption of the IGF Code later in 2014.
Boil Off Gas – the Fuel Doesn’t Stay in the Tank
Unlike oil fuels that can stay in a tank for weeks, months, or even years, LNG because of its cryogenic nature is evaporating (referred to as Boiling Off in the LNG industry) every minute it is in the tank. As it evaporates, it builds up pressure, and if allowed to evaporate without restraint or relief, it can build up high enough pressure to damage tanks and fittings because the volume ratio of natural gas to LNG at atmospheric pressure is 600 to 1. The pressure build up from Boil Off Gas (BOG) is also a significant risk if any LNG is left in pipes, hoses, or fittings, so it is important to drain, vent or purge all LNG pipe systems when not in use. However, BOG cannot be vented to the outside atmosphere, except in an emergency after all else fails.
The best way to address the Boil Off Gas issue, and to be sure your vessel is not going to be in danger at some point, is to develop a Boil Off Gas Plan. This Plan should be started early in the design stage and consider how the BOG will be handled in all the LNG tanks and piping systems, how bunkering will take place, and how the tanks will be used in service. The plan should address all contingencies that could occur, such as what happens after the ship has just fully bunkered and the machinery plant or hull is damaged forcing the ship to stay tied up at the dock with no consumption from the main propulsion engine. Just pumping off the LNG to a shore tank or bunker vessel may not be a feasible option because a receiving tank might not be available (the vessel broke down away from the port), and venting to the atmosphere is not an option either. The proper equipment and procedures need to be implemented, such as a reliquefaction plant, a gas combustion unit, boiler with steam dump, or LNG fueled ship service generators with adequate load, even in port.
One way to consume BOG is using it in the ship’s service diesel generators (SSDG) since these can be run even with the vessel tied up in port. The below table provides a quick reference guide showing some typical BOG rates from various quantities of LNG in storage and how many kW of continuous electric load are needed to consume the BOG on a daily basis. These numbers are approximate and can vary depending on the circumstances.
Filling Limits - You Can’t Use All the Tank’s Volume
Besides the fact that LNG tanks require extra volume due to the low density of LNG and the tank’s shape and insulation, some tank volume is required to be reserved for LNG expansion and for residual LNG (heel) in the empty tank to keep it cold. The tank’s relief valve pressure drives the limit placed on the loading level. The reason for this is that LNG’s density decreases quickly as heat is absorbed, and its temperature and saturation pressure increase. The higher the temperature (and corresponding saturation pressure), the lower the density.
Current IMO regulations limit LNG tanks to 98% full at the relief valve setting (its maximum allowable volume). Loading a tank with LNG at -162º C, when it is close to atmospheric pressure, is the desirable loading condition because at that condition LNG can remain in the tank for the longest period of time before heat absorption raises the tank pressure to the relief valve setting. At this initial loading condition, the LNG density will be at its highest value. Since it can’t be assumed that the ship will always be able to go to sea soon after bunkering and start consuming from all tanks at once, it is a requirement that LNG tanks be able to retain the boil off gas for a period of time up to the point the relief valve setting pressure has been reached. Before the relief valve setting is reached, gas will have to be removed and either reliquefied or consumed in accordance with the Boil Off Gas Plan.
Since the mass of LNG remains the same as the pressure is building and the LNG density is going down (raising the level in the LNG tank), the ratio of the densities between the LNG when bunkered and when at the 98% full limit determines the loading limit (the level the tank can be loaded while bunkering).
The table below lists loading limits for a range of relief valve pressures. As can be seen, the higher the relief valve pressure the lower the loading limit, but on the other hand, the higher the relief valve pressure, the longer the LNG can stay in the tank – a classic tradeoff and decision point for the owner. Besides the limit on filling, usable tank capacity is further reduced by the common practice of leaving LNG in the bottom 5% of the tank volume to continue boiling off, keeping the tank cold until the next bunkering. Cooling down an empty, warm tank before it can be refilled with LNG takes a long time and is normally avoided.
The bottom line is that usable capacity of LNG in a Type C pressure tank is only about 80% to 85% of its available volume, depending on the relief valve setting. All range calculations for the vessel should be based on the usable capacity and not the highest filling or loading limits. Owners who don’t follow this advice will be disappointed when they find out the true range of their vessel is significantly less than they expected.
Summing Up: Much to Consider
There is much to learn when considering the use of LNG as ship’s fuel, particularly those related to LNG fuel storage. Engine selection, bunkering, maintenance, operation, and training also need to be considered and each adds to the complexity of the switch to LNG fuel. Any owner looking to make a successful switch to LNG should be prepared to learn about them all. Based on today’s fast pace of adoption of LNG as a fuel, it seems many owners are saying the hard work and complexity are worth the effort to obtain the benefits from a clean burning, low cost fuel like LNG. Many who have not decided to take the full plunge to LNG are still hedging their bets by building their new vessels to be “LNG Ready,” meaning they are designed and built to easily make the switch in the future.
(As published in the 4Q 2014 edition of Maritime Professional - www.maritimeprofessional.com)
About the Author: Eugene van Rynbach is Naval Architect and Marine Engineer and Vice President of Herbert Engineering Corp. He has forty years of experience in general naval architecture and marine engineering, including time as a sea going engineer, classification society engineer, new construction supervisor, and many years working as a technical manager for former containership operator Sea-Land Service. Rynbach earned a degree in Mechanical Engineering and Naval Architecture from the University of California and a Masters Degree in Transportation Management from SUNY Maritime College.
Other stories from Q4 2014 issue
Content
- Shipbuilding’s Dilemma: Good Problems to Have. page: 8
- Powering Ahead with Wind Assist Technologies page: 10
- Energy Sector Volatility Affects Middle Market M&A Activity page: 16
- Maritime Crime Continues at Pace page: 20
- MarPro Profile: Margaret Kaigh Doyle page: 22
- The Impact of LNG Fuel on Commercial Ship Design page: 24
- MarPro Profile: Brian Buckley McAllister page: 30
- Marine Engine Emissions: GE Changes the Conversation page: 33
- Engine Emissions: GE Changes the Conversation page: 33
- Partnerships, Prodding Propel the Ballast Water Treatment Game page: 36
- Just in Time: ABS Ballast Water Treatment Advisory page: 42
- Maritime & Offshore Employment: Contractors, Coverage and Confusion page: 50
- Shipyard Recruitment, Training and Retention Roundtable page: 54