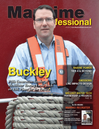
Shipbuilding’s Dilemma: Good Problems to Have.
If shipyards are the bellwether of maritime market trends, then U.S. yards should today be considered the industry’s market leaders, as well. Notwithstanding the recent (and dramatic) drop in global crude oil prices, the ongoing, so-called ‘domestic energy boom’ has left American shipyards with as many as 30 deep draft vessels on their collective backlogs. A robust inland recapitalization program is also underway with the long awaited (but still mired in red tape) subchapter M towboat rules lurking in the wings. Thousands of brown water vessels will likely need some sort of refitting to comply. On the blue water side of the ledger, ballast water treatment rules will soon transform a regulatory hassle into an estimated $80 billion bonanza for ship repair yards, some of which will be realized on this side of the pond.
It’s all good – but not if you can’t find anyone to do the work. Such is the quandary facing U.S. yards with 2015 looming large in the porthole. In this edition, we sampled a wide cross section of shipyard human resources professionals, training and education specialists and industry stakeholders who provided their unique take on the current situation, what’s coming next and how to replace (and harvest a lifetime of knowledge from) their rapidly graying workforce. It’s a work in progress. Our story starts on page 54 within our one-of-a-kind recruitment and retention feature.
Drilling down to find the source of the shipyard industry’s current largesse isn’t really all that hard. That’s because the increasingly intrusive regulatory climate facing marine operators is also forcing their hand on a number of issues; not the least of which include installation of ballast water treatment (BWT) systems and the greening of propulsion footprints. In the ballast water / invasive species game, the trends are clear: there is plenty of help out there for those who need it and I can’t think of many on either side of the equation who don’t. Moreover, the (smart) OEM BWT players are actively forming partnerships and strategic alliances. Those who don’t will likely be left behind – turn the pages to find out why.
The developing landscape for those looking to repower current tonnage or build new vessels has, in recent months, taken some interesting turns as the reality of environmental control areas (ECA) and stricter EPA Tier requirements take hold. Actually, it turns out there are more choices than you might have once thought. For example, the emergence of a Tier 4-compliant diesel engine – one that doesn’t require SCR and/or after treatment to get to the Promised Land – might be of interest. If so, the story starts on page 33.
With all of the foregoing on your mind, the approaching New Year will be here before you know it, eventually revealing what the uncertainties of a jittery oil market and a regulatory climate that awaits definitive action on many fronts will bring. Fortunately, you have Maritime Professional to guide you through the rough spots. Look for more of the same in the coming year.
(As published in the 4Q 2014 edition of Maritime Professional - www.maritimeprofessional.com)
Read Shipbuilding’s Dilemma: Good Problems to Have. in Pdf, Flash or Html5 edition of Q4 2014 Maritime Logistics Professional
Other stories from Q4 2014 issue
Content
- Shipbuilding’s Dilemma: Good Problems to Have. page: 8
- Powering Ahead with Wind Assist Technologies page: 10
- Energy Sector Volatility Affects Middle Market M&A Activity page: 16
- Maritime Crime Continues at Pace page: 20
- MarPro Profile: Margaret Kaigh Doyle page: 22
- The Impact of LNG Fuel on Commercial Ship Design page: 24
- MarPro Profile: Brian Buckley McAllister page: 30
- Marine Engine Emissions: GE Changes the Conversation page: 33
- Engine Emissions: GE Changes the Conversation page: 33
- Partnerships, Prodding Propel the Ballast Water Treatment Game page: 36
- Just in Time: ABS Ballast Water Treatment Advisory page: 42
- Maritime & Offshore Employment: Contractors, Coverage and Confusion page: 50
- Shipyard Recruitment, Training and Retention Roundtable page: 54