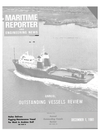
Outstanding Vessels
[...] Review — Blue Ridge cargo tanks. Each tank is fitted with a deep well cargo pump.
The 658-foot-long ship is also fitted with a cylindrical appendage- type bulbous bow to improve speed, and is powered by a GE steam turbine engine. The Blue Ridge and her sister ships incor- porate state-of-the-art equipment and meet the latest safety and environmental protection standards including double bottoms, a clean segregated ballast system, an inert gas system, a sewage treatment plant, collision avoidance radar, and a backup steering system.
The ships, ordered by Union Oil in April 1979, were built entirely without federal subsidy.
The shipbuilder is a wholly owned subsidiary of Morrison-Knudsen Company, Inc., Boise, Idaho.
The Blue Ridge hull was constructed in the f l a t - b o t t o m e d, 1,000-foot-long NASSCO building dock. L a u n c h i n g was accomplished by flooding the dock and floating out the vessel.
The name Blue Ridge is in honor of the mountain range in the Appalachians e x t e n d i n g f r om New England to Georgia. The second of the sisterships, Coast Range, was launched on January 10, 1981, and the third, Sierra Madre, was launched on May 2.
The Blue Ridge will transport products from Union Oil's refinery in Beaumont, Texas, to Atlantic and Gulf Coast ports GALLEON DIAMOND The 19,407-dwt multipurpose cargo ship Galleon Diamond was delivered to Galleon Shipping Corporation of the Philippines by the Hiroshima Works (Innoshima) of Hitachi Zosen, Japan. She is the first of three sister ships ordered from Hitachi by Galleon; one more will be constructed at the Hiroshima Works and the other was built at the Setoda Shipyard of Naikai Zosen, an affiliate of Hitachi.
Galleon Diamond is designed to carry a variety of cargoes such as containers, lumber, bulk, etc.
She will also transport tobacco, coconut products, and hemp, for which all holds have been fitted with dehumidifiers. The ship is equipped with three 16-ton cranes for general cargo, and one 50-ton, twin-type deck crane for extraheavy cargoes such as construction machinery.
The single main engine is the newly developed, long-stroke Hitachi/ B&W diesel, type 6L67- GFC, with constant-pressure turbocharging.
This f u e l - e f f i c i e n t, two-stroke engine has a maximum continuous output of 11,200 bhp at 119 rpm; maximum trial speed was 19.8 knots.
Built to American Bureau of Shipping classification, the 13,886- gt vessel has an overall length of 498.7 feet, beam of 75.8 feet, depth of 46.3 feet, and design draft (full load) of 32.5 feet.
JOHN B. WATERMAN The S / S John B. Waterman is a 23,500-dwt combination container and r o / r o ship that was built for Waterman Steamship Corp. by Sun Ship, Inc., of Chester, Pa. She is the first of two building for the owner.
The ship is intended to transport cargo along the North European trade route f r om Gulf and East Coast ports of the U.S. The 692-foot combination carrier can t r a n s p o r t t r a i l e r s and other wheeled vehicles, containers, and unitized or palletized cargo. The ship has the capacity of 762 f o r t y - foot containers.
The forward section is designed f o r containerized freight and the main deck and hatch covers are capable of r o / r o operations. The aft part is 100 percent roll-on/ roll-off. For ease in loading and unloading, the W a t e r m a n is equipped with a full slewing ramp on the stern, a self-sustaining container crane, side cargo ports, and a cargo elevator in the r o / ro holds.
The Waterman has a beam of 105.5 feet, a molded depth of 68 feet, and a draft of 33 feet. The ship is powered by a General Electric cross compound axial flow turbine engine that drives a 22-foot-diameter, six-blade propeller 110 rpm at 32,000 shp through a double reduction gear.
The vessel's design service speed is 20.9 knots.
There are two Combustion Engineering top fired single case welded wall boilers with a maximum heated steam flow of 102,751 lb hr for each boiler. The operating steam conditions are 872 PSIG, at 955 degrees F.
JOHNSON CHEMSTAR The 38,000-dwt chemical and product carrier Johnson Chemstar, the first of two technically s o p h i s t i c a t e d vessels built by Kockums Shipyard, Malmo, Sweden, was delivered this year to J.O. Odfjell Johnson A/S, Minde, Norway.
Reportedly one of the largest and most technically advanced in the world for the global shipment of chemicals, the vessel was designed to conform to all international safety and environmental regulations, both on the books and pending.
The vessel's hull was designed and built with segregated ballast tanks and double bottom. The center section contains 28 stainless- steel 316LN tanks that are classified for the transport of IMCO type II cargo. There are 10 zincsilicate-coated wing tanks that are classed for IMCO type III cargo. Each tank is equipped with its own stainless-steel piping and deep-well pumping system.
The capacity of the pumps varies from 100 m3/h to 400 m3 h, depending on the size of the tanks.
All cargo handling is controlled from a separate room in the deckhouse.
The Johnson Chemstar is powered bv two independent Lindholmen S.E.M.T. Pielstick medium- speed turbocharged diesel engines, model 12PC2-5V. Each engine is coupled via a reduction gear to a KaMeWa controllablepitch propeller—MCR: 11,500 kw, 15,800 bhp, 520 100 rpm. The epicyclic reduction gears are two Stal-Laval CPG—compact planetary gear type units.
The a u x i l i a r y machinery is powered by three V12A/126 fourstroke turbocharged V-type diesel engines from Hedemora Verkstad, Sweden. They deliver 1,074 kw at 1,200 rpm. Three ASEA alternators, type GBL 560MB, serve the auxiliary diesels, and the shaft alternators are two ASEA type GBL, producing 1,500 kva, 440 v, three-phase, 60 hz, at 1,800 rpm.
The ship is fitted with a bow thruster to improve maneuvering.
The hydraulic system — seven Frano e l e c t r o h y d r a u l i c units manufactured by Frank Mohn A S, Bergen, Norway, are connected to 38 cargo pumps, three ballast pumps, two windlasses, seven mooring winches, two deck cranes, two F.O. transfer pumps, and one tank cleaning pump.
The Johnson Chemstar was dual classed by the American Bureau of Shipping and Det norske Veritas.
MADAME BUTTERFLY The Madame Butterfly is the first in a series of four pure car, truck carriers (PC/TC) delivered by Kockums, A.B., Malmo, Sweden, to Wallenius Lines, Stockholm.
The 13-deck, 17,000-dwt Madame Butterfly is the first major ship of this type to be built outside Japan. She can transport 6,120 passenger cars or a combination of 2,900 cars and 520 commercial vehicles.
Designed for a service speed of 20.3 knots, the ship has an overall length of 198.12 m, a molded breadth of 32.25 m, a height to the sixth deck of 13.64 m (13.69 m aft), and a scantling draft of 11.5 m (about 650 feet, 105.8 feet, 44.8 '44.9 feet and 37.7 feet).
Built to Lloyd's Register of Shipping classification, the vessel's propulsion is supplied by a Burmeister and Wain type 7 L80GFCA direct-reversing diesel engine which is derated to 18,400 bhp at 106 rpm for fuel economy.
It drives a solid propeller and is remotely controlled from the bridge or from the engine control room.
The electrical supply is from three diesel engine-driven 2,000- kva, 1,600-kw, 440-volt alternators, each engine being a Wartsila- Vasa 4-stroke unit running at 720 rpm.
To conserve fuel, the autopilot is designed to reduce unnecessary course corrections. Each ship of this series has a 1,500-hp bow thruster.
M a c G r e g o r S c a n d i n a v i a of Gothenburg was consulted by Kockums on the logistics involved in moving 6,120 cars on or off a vessel having 52,000 internal meters (about 170,612 feet) of roll.
MacGregor claims operating costs have been minimized because the ship design obtains the maximum deadweight within parameters of seaworthy integrity and because of the reduction of cargo handling time in port.
MacGregor contributed 13 separate items to the Madame Butterfly.
These include the stern and side entry ramps, the six internal ramps, five deck covers and eight doors, and the fixed and hoistable car decks.
MARIGOLA M. & B. Benetti Shipyards, Viareggio, Italy, delivered this sophisticated 12,000-dwt chemical carrier to Carbocoke S.p.A. di Navigazione of Palermo. The Marigola's propulsion—a G.M.T. CC 600.5 engine—is the pioneer commercial application of the new G.M.T. low-speed diesel.
The engine produces 8,250 hp at 250 rpm, driving a four-blade c o n t r o l l a b l e - p i t c h p r o p e l l er through a gearbox having a 2.083:1 reduction ratio. A power takeoff from the gearbox drives a 750-kw Ansaldo generator. The auxiliary machinery consists of two G.M.T. BL 230.6 diesel engines, each developing 1,225 hp at 900 rpm.
The Marigola has 22 cargo tanks — eight center stainlesssteel and 14 wing tanks coated with Rustban 191. The ship can load and unload three different products simultaneously. All the tanks are fitted with stainlesssteel coils; the center tanks having AISI 316L Mos grade coils.
Each tank has its own piping and pumping system. There are 22 hydraulically powered submersible pumps, 16 of which are Termomeccanica Italiano CDVS 100s with a 80 m3 /h capacity at 80 m head, and six are CDVS 150s with a 150 m3 /h at 110 head.
The stainless-steel pumps are fed by a hydraulic station supplying 960 kw of power.
Hydraulic power units are remotely controlled through two control panels arranged in a small room on the main deck. One panel is hydraulic and permits the readout and adjustment of the pressures; the other is electric and allows control of the main functions of the cargo plant.
The deck machinery, manufactured by the Benetti yard, consists of two hydraulic self-tensioning windlasses, two hydraulic self-tensioning warping capstans of nine-ton capacity, and four 4-ton hydraulic windlasses for Great Lakes service. Other deck gear includes two 3.5-ton landing booms, a hydraulic davit two-ton at 11.5 m and a portable davit f o r the portable pumps. The electrohydraulic steering gear is a Frydenbo type HS 181D set.
The wheelhouse is equipped with two Decca radars (type RM 1226C) with plotting, azimuth stabilizer, and performance moni t o r ; Decca satellite navigator, type D53; Plath Angulus radio direction finder with homing system ; Kelvin Hughes echosounder; and Microtecnica Sirius Mk 2 gyrocompass.
A Dancom HF 1200 radio station is installed in the communications room.
According to AMLICO of Stamford, Conn., exclusive U.S. representative of G.M.T., the Marigold's hull was designed by the shipyard with a view to achieving the best performance, service speed, maximum tank volume, and deadweight to meet owner requirements. The design was tested extensively in ship model basins in Vienna and Rome.
The c h e m i c a l c a r r i e r was classed by Registro Navale Italiano, meeting all IMCO, SOLAS, and U.S. Coast Guard requirements.
MERAK EIGHTY NKK (Nippon Kokan) of Japan built the 42,000-dwt car/bulk carrier Merak Eighty — fitted with temporarily hoistable cardecks— for Irvine Shipping Inc.
of Liberia. The bulk carrier is NKK's first new vessel to be equipped with hoistable decks.
She was built at the Shimizu Shipyard.
The cardeck installation, called N K K - K v a e r n e r Hoistable Car Deck System, is applicable to vessels having topside wing tanks, and provides temporary decks in the recessed space between the topside tanks and the tank tops by utilizing hold space to a minimum.
Merak Eighty has a length between perpendiculars of 184^50 meters, molded beam of 30.48 meters, molded depth of 17.75 meters, and draft of 11.55 meters (605.3/100/58.2/37.9 feet). Her single main engine is an NKK/ S.E.M.T. P i e l s t i c k 10PC4-V570 diesel with a maximum continuous rating of 15,000 bhp at 400 rpm, providing a service speed of 15.1 knots. Car capacity is approximately 2,650 units.
The basic concept of the hoistable deck technology is that dur- [...] mensions of the holds, hatches, and weather deck have been optimized for the carriage of containers, giving the vessel a maximum capacity of 494 TEUs. The SD18 is equipped with 12 ten-ton SWL cargo derricks f o r handling general cargo, on the assumption that if containers were to be carried it would probably be while on charter to a container line which would use specialized handling gear at port. The PNSC however has opted for a mix of two 35-ton and four 25-ton 20-m boom Velle Cargospeed units to permit container handling with the ship's own gear. These can be coupled, providing a 55-ton capacity. All the winches are electrohydraulically d r i v e n by Sunderland Forge equipment.
The weather deck and shelter deck MacGregor hatches are wire operated; those on the shelter deck being flush fitting. Maximum loading f o r the 'tweendeck hatch covers is 3.00 ton/m2 , while the upper deck covers can sustain 1.75 ton/m2 . Holds No. 2, 3 and 4 have twin hatches, 8 m wide at the weather deck and 7.74 m wide at the 'tweendeck.
For propulsion, as with the cargo gear, the PNSC has chosen to exceed the standard specification by fitting a Clark Hawthorne Sulzer 6RND 68M diesel engine instead of the five-cylinder Sulzer wide range of specific gravities, vapor pressures and viscosities.
An e l e c t r o n i c cargo control system integrates into a single remote cargo control panel the central hydraulic system operation, cargo pump control, hydraulic valve actuation, cargo tank level gaging, tank temperature monitors, inert gas control system, ballast system operation, and gaging and emergency shutdown system.
Devoe Marine Coatings supplied all protective coatings for the Dynachem—for cargo tanks, ballast tanks, and vessel surfaces.
A highly chemical-resistant lining, Devchem 251 was applied to the cargo tanks. Two coats of water-based Catha-Coat 305, an inorganic zinc coating topped with Catha-Seal, was used on the ballast tanks.
OXY TRADER The Oxy Trader, a 42,260-dwt liquid bulk carrier, was the first of three integrated catamaran tug-barge (Catug) vessels built by Avondale Shipyards, Avondale, La., for Occidental Petroleum Corporation.
The vessel is designed to transport highly viscous, dense and c o r r o s i v e superphosphoric acid (SPA). Many other bulk liquid products also can be transported.
Designed by Hvide Shipping and its affiliate, Seabulk Corporation, the Catug is an integrated tug/barge (ITB) that combines the efficient hull form of a ship with the w i d e - b e a m , shallowdraft characteristics of an oceangoing barge. Tug and barge sections were constructed separately and are designed to be employed as an integrated unit.
The design utilizes a twin-hull catamaran tug with a propulsion and steering system in each hull to increase its safety and reliability.
It is reportedly more maneuverable than a single- or twinscrew ship. The tug and barge may be separated rapidly in case of emergency.
Other benefits inherent in the design include lower capital costs and substantially lower manning requirements than conventional ships, all resulting in markedly reduced financial and operating costs.
The Oxy Catugs are powered by two 9,100-bhp Colt-Pielstick, 14-cylinder direct reversing engines, one in each hull. Each engine drives a four-bladed, 20-footdiameter, slow-turning propeller.
Each power unit has its own separate rudder and steering mechanism.
A service speed in excess of 15 knots has been achieved.
Built to ship scantlings with heavy reinforcement for the very dense SPA c a r g o e s , the Oxy Catugs have an SPA carrying capacity of 40,100 metric tons at a draft of 36 feet. The five SPA tanks are located in the center of the barge; they are clad with 3,17L stainless steel.
Each tank is equipped with heat exchangers drawing steam from two waste heat boilers in the engine uptakes or from a separate boiler plant on the barge.
This maintains the SPA at a temperature above 150°F while in transit. Hydraulically operated submerged pumps are capable of discharging all cargo tanks to less than four gallons within 20 hours. Tanks are cleaned by hot fresh water washing via a portable Butterworth system.
Ten wing tanks are coated with water-based inorganic zinc, and may be used to carry petroleum products. The vessel also is fitted for protectively located segregated ballast. The unique design permits the Catugs to carry a wide variety of other liquids — clean and dirty oil products, and liquid chemicals.
SEABEX ONE The Seabex One, a combination offshore rig support vessel and a dynamically positioned diving mothership, was built by Nobiskrug Werft G.m.b.H., of Rendsburg, Germany, for Seabex I n d u s t r i e l l e Tief s e e t e c h n ik G.m.b.H. of Germany and Comex of France.
Seabex One was designed to provide a range of services including support of divers, underwater welding, and the installation and maintenance of offshore drilling rigs and fixed structures.
The vessel also is equipped for fire-fighting and is capable of evacuating up to 500 people from stricken offshore structures.
A large moonpool is incorporated in the vessel, measuring 15 meters by 8 meters (about 49 by 26 feet) which Seabex claims is the first of a size and configuration that ensures there is sufficient access for lowering the underwater vehicles and equipment.
The vessel's deepsea saturation diving system allows up to 16 men to work at three different levels to a maximum depth of 450 meters (1,476 feet). The diving equipment can be lowered either through the moonpool or over the side.
The Seabex One is equipped with seven decompression chambers and a hyperbaric rescue vessel for 12 divers. Other underwater- related equipment includes a welding habitat for constructing oil and gas pipelines, pipe alignment frames, and a cable burying machine. Lockout submersibles are available as are one-atmosphere diving systems.
The moonpool is surrounded by a covered deck space, and the remainder of the deck provides about 1,000 mJ of open space having a load capacity of five tons m2 — specific areas of which are strengthened to permit the installation of winches, davits, and other gear.
Equipment handling is facilitated by a two-ton mobile crane and a Liebherr offshore crane having a 50-ton capacity at a radius of 15 m, or 100 tons when operating through the moonpool.
The crane is fitted with a heave compensation arrangement which can maintain its boom steady in relation to either the sea floor or to another vessel alongside. It can operate to a depth of 300 meters. The vessel also is fitted with a 100-ton capacity H frame at the stern.
The K o n g s b e r g fire-fighting system consists of four monitors of 1,800 m3 /h throughput, powered by two gas turbine driven pumps delivering 3,600 m3 /h each at a pressure of 15 bar. The fire monitors are inertia stabilized and can provide accurate cover even in bad weather, which Seabex officials regard as an improvement over other systems.
The vessel's maneuverability and propulsion are supplied by a combination of Pleuger ducted propellers and transverse thruster units. Two reversible fixedpitch nozzle propellers fitted at the stern, which can be steered through a full 360 degrees, are capable of delivering 2,300 hp each at 202 rpm. They are powered by two AEG electric motors running at 700 rpm.
Two similar units are mounted at the bow, each with an output of 1,500 hp at 238 rpm. These are aided by two lateral thrust Pleuger fixed blade units — one forward and one aft —- of 800 hp each.
The complete arrangement is controlled by a Kongsberg Albatross 503 dynamic positioning system, which uses data obtained principally from an inertial platform, an acoustic reference system, and two taut wires.
The Seabex One wires are attached to an above-water part of the structure near which it is station keeping, as contrasted to other taut-wire systems that are linked to weights on the sea floor. The multiple data sources ensure a safety margin in the event any part of the system breaks down.
Power for the electrical propulsion is supplied by five auxiliaries, each consisting of an MAK 8M332AK engine and an ADG generator, producing a total output of 6,450 kw, using fuel of 30 cSt (200 sec. Redwood), and an emergency generator set of 300 kw.
Two engine rooms are needed to house the equipment and a large control room is situated on the lower 'tweendeck above the control room. There are acccom- modations for 86 persons, two evacuation rooms with 50 bunks each, and a hospital onboard. The Seabex One was built to Det norske Veritas classification.
SUTORETAI MARU The 3,700-gt Sutoretai Maru is not a new vessel in the sense that she was delivered in 1981. But by the addition this year of a stern end bulb (SEB) developed by Kawasaki Heavy Industries of Japan, she certainly became an "outstanding vessel." She became the first ship to be equipped with the newly developed propulsive power-saving system— the SEB. When the passenger vessel was placed in service fitted with the bulb, the addition showed excellent results. Owned by the Tokai Risen Company, Ltd., and the Maritime Credit Corporation, the vessel was built in 1978 and serves on the Tokyo- Miyake Island-Hachijo route.
The Kawasaki-SEB was fixed on the ship's main stern hull around the center line and near the full-load waterline. The purpose was to save propulsive power by reducing wave pattern resistance and stern part local resistance from the effect of the interference between the waves generated by the bulb and by the stern hull.
The basic theory of the SEB was developed by a research group led by Prof. Dr. T. Inui of Tokyo University, an authority on the wave-making resistance theory. Under the guidance of this group, KHI has continued to study the SEB for practical use, [...] to keep the deck hatches at a required level for dockside loading.
The huge cargo area is divided into five holds. A series of poweractuated gates in each hold feeds pellets or coal onto a conveyor belt that lies beneath the entire length of the cargo hold area. The De Lancey's unloading system is capable of discharging pellets at the rate of 10,000 tons per hour.
The 260-foot boom can swing to either side f o r piling cargo ashore under high-speed unloading conditions.
Main propulsion power for the De Lancey is provided by two 8,560-bhp Colt-Pielstick diesel engines.
Each engine is directly connected to a four-blade, lTVj-footdiameter controllable-pitch Bird- Johnson propeller through a specially designed reduction gear and shafting system.
Designers of the De Lancey were most concerned with two aspects of the main drive system— reliability and low maintenance.
The result is a simple, unencumbered drive system capable of delivering power to the propellers efficiently and in a minimum of space.
The arrangement of completely independent drive systems for each engine optimizes overall reliability; if for some reason one engine is nonoperational, the other can still power the ship. Four 800-kw, 480-volt main electrical generators are driven by separate Caterpillar diesel engines.
The De Lancey has a maximum capacity of 152,000 gallons of heavy fuel oil f o r main propulsion, and carries 31,000 gallons of light diesel oil fuel f o r generator, heater, and boiler service.
Each controllable-pitch propeller assembly is fitted with four stainless-steel movable blades. An automatic pitch-control system hydraulically c h a n g e s propeller pitch according to engine speed to provide f o r optimum running economy and to prevent overloading and stalling the engines when the vessel is heavily loaded at low speeds.
Single-lever controls in both the pilothouse and engine room provide for combined control of engine speed and propeller pitch.
Provision is also made f o r a split control of speed and pitch from the pilothouse and engine room.
Separate control units connected to the central pilothouse unit are located on both the port and starboard bridge wings.
Maneuvering the huge 1,000- footer is simplified by the twin screws and the arrangement of a rudder behind each propeller.
The ship also can be steered by varying the speed of each engine.
A 1,500-hp Bird-Johnson electrically driven bow thruster facilitates docking.
Reversing is a c c o m p l i s h ed t h r o u g h the controllable-pitch propellers. The onboard St. Louis ship F.A.S.T. sewage treatment plant, which meets stringent federal standards, produces completely clean effluent for discharge, or f o r temporary holding while the vessel is in waters where discharge is prohibited by local regulations.
Read Outstanding Vessels in Pdf, Flash or Html5 edition of December 1981 Maritime Reporter
Other stories from December 1981 issue
Content
- MarAd Approves Farrell Lines Ship Charter To Military Sealift Command page: 4
- 83 Vessel $3.4-Billion Program Planned By Japanese Shippers page: 4
- Veliotis Takes New Post With General Dynamics page: 4
- Petroterminal De Panama Selects EMH To Construct Tanker-Loading Buoys page: 6
- Name Peter West VP Of Transway Operations page: 6
- Sun Company, Levingston Sign Letter Of Intent For Pa. Shipyard Sale page: 6
- American Steamship Names D. Ward Fuller As Its Chief Operating Officer page: 6
- SNAME-Hampton Roads Hears Paper On Fuel Savings In Cargo Heating Systems page: 10
- Multipurpose Semisubmersible Built To Handle North Sea Emergencies page: 10
- Maher Expands Container Facility, To Install First Paceco Transtainers In N.Y. page: 15
- Kvaerner, Oy Navire To Merge Shipbuilding, Equipment Capabilities page: 15
- Baldt Inc. Develops New Abrasion-Resistant Chain —Brochure Available page: 15
- Kaiser Engineers Awarded Service Contract For Trident Sub Facilities page: 16
- SNAME Philadelphia Section Discusses Ship Design By Personal Computers page: 18
- M/V Europa Completes Sea Trials; Luxury Cruise Liner Filled With Many Environmental Safeguards page: 18
- Gulf Oil Announces Exec Assignments For Corporation And Divisions page: 18
- Award RCA $339 Million In Contracts For Navy's Aegis Weapon Systems page: 19
- Three Top Management Changes At Levingston page: 20
- Outstanding Vessels page: 22
- Largest U.S.-Built Hopper Dredge Launched At Avondale Shipyards page: 22
- ASNE Flagship Section Hears Paper On Engineering Costs And Risks page: 22
- DredgeMasters To Acquire Aquamarine Corporation page: 24
- Advanced Marine To Design New Ferryboat page: 24
- Newfoundland's Ocean Cargo Services Seen Expanding With Coming Offshore Oil Boom page: 24
- Soviets Plan Nuclear Powered Merchant Ship, To Be Completed By 1984 page: 25
- Spanish Shipbuilders Assoc. Publishes New Brochure —Copies Available page: 26
- Name John Malagraph General Manager Of Advanced Marine In N.Y. page: 26
- Shell To Provide Bunkering Service At Port Of Mobile —Literature Available page: 27
- Appoint Hession President Of Koehring Clyde, Whirley Crane Producer page: 27
- Name Parks President Of Farrell Lines page: 27
- Todd-Seattle Sponsors Marine Diesel Seminar page: 28
- Norcontrol To Install $3-Million Vessel Traffic System —Literature Available page: 28
- SNAME page: 36
- Moss Rosenberg Verft Develops Energy-Saving LNG Carrier page: 41
- $2.1-Million Title XI Guarantee For Tanker IGS And COW Retrofit page: 41
- SNAME New York Hears Paper On Marine Gas Chemists page: 42
- Utility Vessel M/V Lamnalco Mallard Delivered To Kuwait Service By HUDSHIP page: 42
- SNAME-New England, ASNE Hear Rear Adm. Beecher On Battleship Reactivation page: 42
- Allis-Chalmers Receives $6-Million M u d Pump Order From Wilson page: 43
- $1 -Billion Lube Oil Refinery To Be Constructed In Saudi Arabia page: 43
- Deliver 13th Supply Boat To Marsea Agencies Fleet, Plan Eight More For 1982 page: 48
- Paducah Marine Ways To Add Fab & Prop Shops page: 48
- Brown & Root Affiliate Awarded Pipeline Contract In Danish North Sea Area page: 50
- Maritime Safety Group Honors 12 Persons For Technical Presentations page: 50
- Award $12-Million Contract To Uniflite For Boats Used By Navy's Special Forces page: 53
- Hold Dedication And Ribbon-Cutting Ceremony At New Bell Halter Yard page: 53
- SNAME's Great Lakes And Rivers Section Meets At Universty Of Michigan page: 56
- Canadian Shipbuilders Group Sets Date For 1982 Conference page: 56
- Sperry Introduces New Ship Control System —Literature Available page: 57
- St. Louis Ship Announces Management Appointments At Engine Repair Division page: 58
- New Brochure Describes Allied Water/SweetWater R/O Water Maker page: 58
- Papers On Containerships, Bulkers Presented By SNAME California Sections page: 60
- Submarine LNG Carrier Proposed By General Dynamics For Arctic Regions page: 60
- Joseph Lykes To Retire As Head Of Lykes Steamship; James Amoss To Be CEO page: 69
- Student Papers Meeting Held By SNAME New England Section page: 69
- Coast Guard Proposes Maneuvering Standards For U.S.-Flag Vessels page: 70
- MSC Accepts Third Sea-Land Containership page: 70
- Commission Destroyer USS Scott Third Ship In A New Class page: 81
- Nuclear Attack Submarine La Jolla Commissioned At New London page: 81
- Bergeron Delivers 160-Foot Tank Barge Tide Mar 34 To Tidewater Marine page: 87
- Kings Craft Delivers Matmar Drill III, Third Of Four Crewboats From Yard page: 87