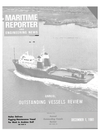
Moss Rosenberg Verft Develops Energy-Saving LNG Carrier
One of the many features that characterizes an LNG carrier is the presence of cargo boil-off, the result of heat leakage to the cargo f r om the surroundings. Until now, the boil-off has been utilized as fuel in producing steam f o r the steam-turbine propulsion plant. However, LNG has lately become comparatively expensive, and associated with relatively low thermal efficiency of the steampropulsion- plant system, the use of boil-off as fuel is now considered uneconomic.
Moss Rosenberg Verft a.s. of Moss, Norway, decided to develop a 130,000-cubic-meter LNG carrier, paying particular attention to low operational costs and low cargo losses. The primary objective of the project study was to minimize boil-off and, therefore, consider alternative propulsion plants.
The firm developed a project ship which is the result of comprehensive programs and analyses, where the following areas were closely studied: reduction of boil-off, improvement of propulsion efficiency, reduction of hull resistance and optimization of the economical speed of the vessel.
Research and development work over the last f ew years have led to improvements with respect to reduced heat leakage to the cargo tanks. By inserting a ring of austenitic steel, a thermal brake, in the skirt supporting the spherical tank, heat leakage through the skirt can be reduced by more than 50 percent. Further, insulation thickness can easily be increased without any effect on the ship's main dimensions. This combination of improved insulation thickness and a skirt with thermal brake may reduce the boiloff rate f r om 0.25 percent to 0.11 percent.
Different alternatives of propulsion machinery were studied.
The recent developments of largebore slow-speed diesel engines with low fuel-oil consumption has made such plants most attractive f o r LNG ship application. Such installations, h o w e v e r , cannot utilize cargo boil-off in the conventional way and the installation of a reliquefaction plant for the cargo is required. This also will result in increased delivered quantities of LNG. Compared to a steam-propulsion plant without reheat, the savings in fuel expenses on a diesel plant with boil-off reliquefaction is in the region of 36 percent (energy prices mid 1981).
Due to the increasing fuel costs, Moss Rosenberg also believes that the economical speed of the future ship will be lower than what is normally used today.
Based on the firm's studies so far, the future LNG ship of their design might have the following particulars: cargo capacity of 130,000 cubic meters, a length between perpendiculars of 240 meters, a molded breadth of 48 meters, a molded depth of 27 meters, a draft of 11 meters, four cargo tanks with the first having a diameter of 36.8 meters and the other three of 40.7 meters and speed of about 18 knots. The propulsion machinery would consist of a large-bore slow-speed diesel engine with a maximum continuous rating of 26,000 kw. The auxiliary machinery would consist of three diesel generators.
Resides being attractive as far as construction costs are concerned, this project also is attractive as concerns the operating costs. Based on prices from August 1981, it may be possible to obtain savings for the projected ship of about $300,000 on a standard 21-days round trip when traveling at the economical speed of 18 knots.
The Moss Rosenberg spherical LNG tank design has been in operation since 1973. A total of 101 spherical cargo tanks are installed on board 20 carriers transporting LNG worldwide.
Read Moss Rosenberg Verft Develops Energy-Saving LNG Carrier in Pdf, Flash or Html5 edition of December 1981 Maritime Reporter
Other stories from December 1981 issue
Content
- MarAd Approves Farrell Lines Ship Charter To Military Sealift Command page: 4
- 83 Vessel $3.4-Billion Program Planned By Japanese Shippers page: 4
- Veliotis Takes New Post With General Dynamics page: 4
- Petroterminal De Panama Selects EMH To Construct Tanker-Loading Buoys page: 6
- Name Peter West VP Of Transway Operations page: 6
- Sun Company, Levingston Sign Letter Of Intent For Pa. Shipyard Sale page: 6
- American Steamship Names D. Ward Fuller As Its Chief Operating Officer page: 6
- SNAME-Hampton Roads Hears Paper On Fuel Savings In Cargo Heating Systems page: 10
- Multipurpose Semisubmersible Built To Handle North Sea Emergencies page: 10
- Maher Expands Container Facility, To Install First Paceco Transtainers In N.Y. page: 15
- Kvaerner, Oy Navire To Merge Shipbuilding, Equipment Capabilities page: 15
- Baldt Inc. Develops New Abrasion-Resistant Chain —Brochure Available page: 15
- Kaiser Engineers Awarded Service Contract For Trident Sub Facilities page: 16
- SNAME Philadelphia Section Discusses Ship Design By Personal Computers page: 18
- M/V Europa Completes Sea Trials; Luxury Cruise Liner Filled With Many Environmental Safeguards page: 18
- Gulf Oil Announces Exec Assignments For Corporation And Divisions page: 18
- Award RCA $339 Million In Contracts For Navy's Aegis Weapon Systems page: 19
- Three Top Management Changes At Levingston page: 20
- Outstanding Vessels page: 22
- Largest U.S.-Built Hopper Dredge Launched At Avondale Shipyards page: 22
- ASNE Flagship Section Hears Paper On Engineering Costs And Risks page: 22
- DredgeMasters To Acquire Aquamarine Corporation page: 24
- Advanced Marine To Design New Ferryboat page: 24
- Newfoundland's Ocean Cargo Services Seen Expanding With Coming Offshore Oil Boom page: 24
- Soviets Plan Nuclear Powered Merchant Ship, To Be Completed By 1984 page: 25
- Spanish Shipbuilders Assoc. Publishes New Brochure —Copies Available page: 26
- Name John Malagraph General Manager Of Advanced Marine In N.Y. page: 26
- Shell To Provide Bunkering Service At Port Of Mobile —Literature Available page: 27
- Appoint Hession President Of Koehring Clyde, Whirley Crane Producer page: 27
- Name Parks President Of Farrell Lines page: 27
- Todd-Seattle Sponsors Marine Diesel Seminar page: 28
- Norcontrol To Install $3-Million Vessel Traffic System —Literature Available page: 28
- SNAME page: 36
- Moss Rosenberg Verft Develops Energy-Saving LNG Carrier page: 41
- $2.1-Million Title XI Guarantee For Tanker IGS And COW Retrofit page: 41
- SNAME New York Hears Paper On Marine Gas Chemists page: 42
- Utility Vessel M/V Lamnalco Mallard Delivered To Kuwait Service By HUDSHIP page: 42
- SNAME-New England, ASNE Hear Rear Adm. Beecher On Battleship Reactivation page: 42
- Allis-Chalmers Receives $6-Million M u d Pump Order From Wilson page: 43
- $1 -Billion Lube Oil Refinery To Be Constructed In Saudi Arabia page: 43
- Deliver 13th Supply Boat To Marsea Agencies Fleet, Plan Eight More For 1982 page: 48
- Paducah Marine Ways To Add Fab & Prop Shops page: 48
- Brown & Root Affiliate Awarded Pipeline Contract In Danish North Sea Area page: 50
- Maritime Safety Group Honors 12 Persons For Technical Presentations page: 50
- Award $12-Million Contract To Uniflite For Boats Used By Navy's Special Forces page: 53
- Hold Dedication And Ribbon-Cutting Ceremony At New Bell Halter Yard page: 53
- SNAME's Great Lakes And Rivers Section Meets At Universty Of Michigan page: 56
- Canadian Shipbuilders Group Sets Date For 1982 Conference page: 56
- Sperry Introduces New Ship Control System —Literature Available page: 57
- St. Louis Ship Announces Management Appointments At Engine Repair Division page: 58
- New Brochure Describes Allied Water/SweetWater R/O Water Maker page: 58
- Papers On Containerships, Bulkers Presented By SNAME California Sections page: 60
- Submarine LNG Carrier Proposed By General Dynamics For Arctic Regions page: 60
- Joseph Lykes To Retire As Head Of Lykes Steamship; James Amoss To Be CEO page: 69
- Student Papers Meeting Held By SNAME New England Section page: 69
- Coast Guard Proposes Maneuvering Standards For U.S.-Flag Vessels page: 70
- MSC Accepts Third Sea-Land Containership page: 70
- Commission Destroyer USS Scott Third Ship In A New Class page: 81
- Nuclear Attack Submarine La Jolla Commissioned At New London page: 81
- Bergeron Delivers 160-Foot Tank Barge Tide Mar 34 To Tidewater Marine page: 87
- Kings Craft Delivers Matmar Drill III, Third Of Four Crewboats From Yard page: 87