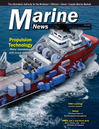
INSIGHTS: Edward C. Schwarz, ABB VP of Sales, New Builds
Based in Miramar, FL, ABB Vice President Ed Schwarz is today responsible for developing and leading the newly created new sales team for ABB in North America.
He is the firm’s leading advocate for new build opportunities in US and Canada and more importantly, developing the business strategy necessary for bringing hybrid and electric solutions to North America market. A graduate of the U.S. Merchant Marine Academy at Kings Point, NY, he earned a Bachelor of Science in Marine Engineering and Shipyard Management in 2000. Additionally, he served in United States Navy as Lieutenant, US Naval Reserve until 2011. He served at sea in a variety of engineering roles and has earned his Chief Engineer’s license. Prior to joining ABB, he also worked for ZF Marine Propulsion Systems and Voith Turbo Schneider Propulsion, where he managed and promoted technical and practical aspects of those respective marine divisions. As ABB takes a pole position in the quest to clean up the environmental footprint of marine vessels, and Schwarz is at the tip of the ABB spear when it comes to implementing that strategy. Listen in this month as he leads a discussion into the greener and more fuel efficient future of the marine industry.
You have been quoted as saying, “Prior to every major adoption of technology in the US inland river market there is a perfect alignment of opportunity and solution.” Tell us why inland operators are finally ready for hybrid and/or electrification of propulsion.
Just as the diesel engine superseded steam and steam did the sail, the combined benefits of the electric propulsion represent the next generation of towboat for the US inland water¬way, from which there is no going back. Once owners enjoyed the benefits of lighter, more reliable diesel engines they stopped building large and dangerous steam boilers for inland vessels. Once the US inland owners start to enjoy the benefits of diesel electric propulsion they will not look back favorable on the disadvantages of diesel mechanical systems. At a time when speculation in shipbuilding and slow economic growth continue to haunt the maritime sector, owners find themselves under continuous pressure to minimize costs by maximizing operating efficiency. Shipping has also come under increasing scrutiny from regulators and environmental bodies over its environmental, with emissions from ships the number one concern. Recently introduced NOx emissions rules mean that conventional diesel mechanical marine engines can only meet EPA Tier 4 performance requirements by adding expensive, bulky, heavy, complex and hard to maintain aftertreatment - either costly Exhaust Gas Recirculation (EGR), or Selective Catalyst Reduction (SCR) using urea on board. Alternatively, inland operators should consider diesel electric propulsion, which is not only increasingly preferred by global shipping but which can meet Tier 4 standards using Tier 3 main engines, without the need to devote space, engineering time or finding bunker calls for urea.
Everyone wants to be ‘green,’ but most won’t go that way until it also produces green for the bottom line. Share some of those competitive advantages that will eventually propel inland operators to make the switch.
The new regulations covering emissions from US inland vessels have major cost implications for owners looking to build new vessels, at a time when there is a significant requirement to replace an aging river fleet. The costs involved are significant enough to prompt considering the ROI of alternative technologies. The ‘conventional’ option involves installing two large EPA Tier 4 main engines supplemented by an after treatment system – either the costly EGR option or SCR that features additional piping, its own refill and urea storage tank and demands separate maintenance. There is no likelihood that investments in after treatment technology can be recovered from shipping contracts. Alternatively electric propulsion provides the ability reduce the major operating costs of engine maintenance and fuel. A vessel that spends 40% of its operation time at less than 50% propulsion load can be worked using two engines instead of three when compared to a mechanical driven system. This capability results in fuel economies when engines are under part load. But even more importantly, owners can reduce total engine running time by up to 50% – significantly reducing engine maintenance.
Is a retrofit to diesel electric and/or battery operations feasible for existing boats or is this trend primarily best suited for newbuilds?
The retrofit market is the largest market in the US due to the cost of construction for new vessels. Everyone knows that the US keeps vessels the longest of any other market. This creates a lot of interest in bringing new technologies to existing vessels. There is no limitation to retrofit except space and weight but usually this equipment can be fitted in unused areas like top decks or lower utilized spaces. An example of a very successful major retrofit is the Tycho Brahe and Aurora which have been converted from conventional diesel engine operations to battery power as part of ForSea’s strategy to reduce the environmental footprint along the 4km route between Sweden and Denmark. The vessels operate on a high intensity ferry route that transfers over 7.4 million passengers and 1.9 million vehicles between urban port terminals in Denmark and Sweden. The conversion of these over 100-meter ferries, both built in 1991, required installation of a 4160 kWh battery on each vessel, as well as battery racks, energy storage control systems and ABB’s Onboard DC Grid power distribution technology. Additionally, ABB supplied automated shore-side charging stations using an industrial robot to optimize the connection time and maximize the charging period, leveraging 3D laser scanning and wireless communication between ship and shore. This is a landmark project, and we are convinced it will come to be seen as a critical step in shipping’s environmental revolution, as well as a milestone in rolling out ABB’s ‘Electric, Digital, Connected’ strategy for shipping.
Niagara Falls tour operator Maid of the Mist has ordered two new passenger vessels sailing on pure electric power, enabled by ABB’s technology. Flesh out that propulsion system and its components for the readers.
The Maid of the Mist project is truly revolution because the vessel will not be fitted with ANY engines – it is truly all electric and the fact the electricity comes from the local hydro dam means a true zero emission vessel. ABB has been tasked with providing a completely integrated solution that takes power from the utility, manages it and delivers to the L-drives and bow thrusters. In addition to integrating the ship-to-shore battery charging connection, ABB will supply the Maid of the Mist newbuilding project with switchboards, drives, batteries (from Spear), propulsion motors for both sets of stern and bow thrusters, and the integrated control system, as well as the ABB Ability Marine Remote Diagnostic System for remote equipment monitoring and predictive maintenance. ABB Ability is ABB’s leading offering of digital solutions and services.
In terms of the Maid of the Mist passenger vessels, give us an idea of the cost difference for these vessels had the operators opted, for example, for an EPA tier 4 solution?
The Maid of the Mist vessel would have probably been able to use multiply Tier 3 engines (less then 800HP each) thus staying below Tier 4 requirements. But even compared to Tier 3 propulsion solutions there is a financial benefit to the owner to go full battery electric. When an owner makes the decisive decision to go full battery electric they are enjoying benefits both on the initial design and operation. There is benefit in not just removing engines but also all the accompanying exhaust ducts, foundations, shaft lines, electrical connections, cooling, fuel lines, multiply pumps, and fuel tanks. The new ABB system for these types of vessels (ABB Onboard Microgrid) is a new compact-size solution, ABB makes similar efficiencies achievable for smaller, lower-power vessels operating over short distances that larger vessels have enjoyed for many years. Onboard Microgrid reduces the footprint and weight of the electrical equipment on board by eliminating the need for bulky transformers and main switchboards. That leaves more space on the vessels and provides greater flexibility in the positioning of system on board- thus saving money during design. The system is almost completely pre-engineered and self-contained. This saves costly time during the vessel construction period.
But the real costs savings come during the operations by reducing many of the major costs of operation like engine maintenance and fuel costs. It also improves space and layout of the vessel allowing for in this case more passengers to enjoy the top deck without the stacks taking up space and spewing exhaust and heat. Lastly, if you are in the business of services to the general public one cannot underestimate the paradigm shift in where millennials will spend their money or support. Anyone who lives with, works with or knows millennials, is also aware that they are reshaping what is important in consumer culture- this includes environmental issues.
The two biggest sticking points for the use of batteries on commercial vessels have been, until recently, weight and/or the physical footprint of these units necessary to provide the required propulsion power. We’ve come a long way, haven’t we? Tell us a little about the progress made on that front.
Marine batteries are to some degree rooted in “ESS systems” – containers full of batteries that provide peak shaving to power plants. Until recently, marine batteries used heavy, inflexible backplanes as the basis of their systems. The most advanced batteries on the market use easy connections with light, adaptable racking. This contributes to a reduction in weight and a footprint. We expect big advancements in two or three years from development in battery chemistry, but the myth that batteries have to be big and heavy has already been busted.
Each of the MoTM vessels will be powered by a pair of battery packs with a total capacity of 316 kWh, split evenly between two catamaran hulls. Having two fully independent power systems on board will increase the resilience of operations by creating a redundancy. Can the battery packs operate with just one unit if the other is unavailable for whatever reason? Is this sufficient to propel the vessel safely and if so, for how long?
This redundant arrangement is very important for an all-electric (no engine) system. Each hull houses enough power and both stern and bow thrusters to drive the vessel independently. This allows for true redundancy. As long as the vessel is able to recharge, the vessel can operate with a 50% loss of the system.
The European innovation project FLAGSHIPS has been awarded 5 Million Euros from the EU to support deploying two commercially operated zero-emission hydrogen fuel cell vessels in France and Norway. In France, a hydrogen pushboat operated by Compagnie Fluvial de Transport (CFT) will serve as a utility vessel on one of its most demanding rivers, the Rhône. Define the term ‘utility’ vessel. Will this truly be a workboat?
This is a major milestone in inland marine industry. It seems at times that the inland market is later to adopt new technologies – in this case, inland is on the vanguard of zero emission technology. The project is a retro fit of a push-boat for the transportation of cargo and moving barges. It pushes two barges and convoy lengths is up to 180 meters (~600 feet). The vessel’s daily operation is inside the Port of Lyon manipulation barges and weekly operation moving barges between Port of Lyon and Docks Fulchiron. It is very similar to the typical US Fleeting operation in the lower Mississippi River that some times acts like a unit tow – by volume of vessels, this is properly the most common pushboat vessel operation in the US. ABB and Ballard Power Systems will leverage the existing kilowatt-scale fuel cell technologies and optimize them to create a pioneering megawatt-scale solution suitable for powering larger ships. With an electrical generating capacity of 3MW (4000 HP), the new system will fit within a single module no bigger in size than a traditional marine engine running on fossil fuels.
The diesel electric system decides how much power is needed. Hence, and for larger operators, the likelihood that one Captain or another will be labeled the ‘fleet gas hog’ can be eliminated. For its part, ABB claims as much as a 30 percent fuel savings. Flesh out those numbers for us.
Going with automated electric propulsion brings many advantages including automation. Our automation system allows the Captain to run his/her vessel as they normal would and the system then automatically decides how much power is needed and starts or shut-downs engines accordingly.
It is important that the Captain have available all the install power to quickly maneuver his/her vessel. But we will also start to see Captains change the way they operate vessels once they have the instant toque of full power at zero speed that comes from a motor. Other markets, introduced to ‘speed of throttle response and quick availability of standby power,’ start to naturally operate the vessels in a more efficient and effective way. In a real life example, we calculated an owner to save about 15-25% fuel reduction using a diesel electric system. They reported about a 50% reduction in fuel used. When we interviewed the Captains they explained that due to their confidence in the standby power being available so quickly, they ran vessel at lower loads more frequently then in the past. The goal is not just installed horsepower but actual performance exactly when it is needed – this is the efficiency that a well designed electrical system can bring an owner.
ABB has already supplied over 1,300 vessels featuring diesel electric propulsion. When will we see the first inland pushboat using such technology?
Very soon. We are having very encouraging conversations with owners that believe the technology is a perfect fit for operation. Ultimately, it the vessel owners that need to see the value. These are conversations we are having today. The industry has been very accepting of learning about electric propulsion, asking probing questions and now looking for the opportunities to implement. We fully expect to see ETBs sailing in 2020.
Read INSIGHTS: Edward C. Schwarz, ABB VP of Sales, New Builds in Pdf, Flash or Html5 edition of July 2019 Marine News
Other stories from July 2019 issue
Content
- INSIGHTS: Edward C. Schwarz, ABB VP of Sales, New Builds page: 14
- Successful Sustainability Starts with … Lubricants page: 22
- OP/ED: A Measured Response page: 26
- PROPULSION TECH: How to Get to Hybridization page: 28
- PROPULSION: ‘Power’ to the People page: 31
- Maritime Simulation & Training: a partnership that pays off page: 40
- All Aboard with Fire Safety page: 44
- OP/ED: Stronger Together page: 46
- Lowering Shipbuilding Costs with Immersive Training page: 48