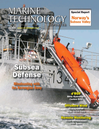
d’ROP Bibby’ Hydromap’s Custom-built ROV
Self-dubbed a ‘revolution in coastal ROV survey,’ Bibby HydroMap unveiled its d’ROP system onboard its new survey vessel, Bibby Athena, a the National Oceanographic Center in Southampton, UK. MTR spoke with Andrew McLeay, Managing Director of Bibby HydroMap, for details.
In an industry where innovation is common, Bibby HydroMap’s d’ROP system truly stood out at an active Ocean Business last month in Southampton. d’ROP is a custom developed solution by the company, touted to be a revolution in coastal ROV survey with particular productivity gains in shallow water survey and inspection. d’ROP was showcased onboard the new 27.5m purpose built semi-swath coastal survey vessel Bibby Athena, and was set to embark on its first commercial mission immediately after the exhibition.
In a market teeming with advanced ROV platforms and options, the first natural question for McLeay is: Why custom design this yourself?
“The decision was taken to develop the d’ROP as we have a set of very specific survey tasks that lie beyond the capabilities of existing observation class ROVs and require the dynamic capabilities of a powerful work class vehicle, said McLeay. “We obviously cannot accommodate a work class ROV spread aboard our own vessels due to size and weight limitations. We also need the ability to be able to deploy in shallow water, something that is not usually associated with a work class ROV, and especially not with an offshore support vessel. Much of our work is in coastal areas with strong tides and being able to work through an entire tidal cycle is a major advantage.”
While d’ROP surely does not look like any other vehicle in the field, there are some classic markers – namely four massive, powerful thrusters – that link it with its brethren.
“What we have effectively done is to take the basic components of a powerful work class ROV, strip off all the peripherals and redundant systems that we don’t need and have created a compact but exceptionally stable and powerful platform focused entirely on deploying survey sensors at the optimum geometry for maximum resolution and data quality,” said McLeay. “ In reality there was no existing single ROV product that could address our specific requirements.
Developing d’ROP
The d’ROP is based upon a concept conceived in-house within Bibby HydroMap, and started with a desk top study to look at the potential options to turn the concept into reality. “A partnership was formed with a small company called HydroBotics which provide ROV engineering consultancy and project management services,” said McLeay. “Hydrobotics were then contracted to manage the build, commission and deliver the system. Bibby Marine Survey Services own the patent for the concept.”
Why d’ROP
d’ROP is a dynamic Remotely Operated Survey Platform that borrows and combines technology and operating principles from ROVs, ROTVs and modern dredging systems.
“The main operational advantages are the ability to maintain track or station in high current environments, automated launch and recovery, reduced number of support staff as a conventional pilot is not required, bringing work class capability to shallow water and providing a highly adaptable platform with high payload capability of up to 500kg,” said McLeay.
It is deployed vertically beneath the support vessel, getting vertical position from a heave-compensated winch and combined LARS, with its thrusters maintaining heading and altitude in relation to a survey line. Courtesy of its massive thrusters, it is designed to be able to hold station and remain stationary, operate at very slow speed for depth of burial surveying or track at up to four knots for acoustic survey. “The high power propulsion is to give the platform the ability to maintain position in strong cross tides as well as operate at up to 4 knots in acoustic survey mode.”
While it has numerous advantages, there is a drawback according to McLeay: “It has limited excursion ability and operates directly beneath the vessel only and is limited in depth capability by the available length of lift umbilical cable.”
Following its unveiling in Southampton, the unit was scheduled to be deployed on its first live contract surveying an AC power cable and measuring depth of burial on one of the North West England wind farm sites.
According to McLeay, the decision on whether to hold this technology close or commercialize has yet to be taken. “Initially the platform was developed to service an in-house requirement although the level of interest in the system may prompt us to explore the possibility of producing multiple units for wider use.”
Bibby Athena
Builder Socarenam Boulogne, France
Designer Bureau Mauric
Length x Beam x Draft 27.5 x 10 x 3.5 m
Tonnage 145 gt
Class Lloyd’s Register 100A1SSC Catamaran, G6
Flag UK
Main engines 2 x Cummins KTA19 M3
Gears Twin Disc MG516C
Survey Propulsion 2 x Schottel SPJ57 azimuth pumps jets
Bow thrusters 2 x Schottel SPJ15 azimuth pump jets
Speed 12 knots
Survey speed 6 knots
Endurance 10 days
Fuel Consumption, transit 2.5 cu.m./day
Fuel Consumption, survey speed 1.2 cu.m./day
Fuel Consumption, DP 1.8 cu.m./day
Generators 2 x Scania DI13-074M
Tank capacity, gas oil 24 cu. m.
Tank capacity, fresh water 8 cu. m.
Tank capacity, water maker 2 cu. m./day
Crane Palfinger
Max. lift 5450kg @ 4.2m
Moonpool 2.05 x 2.3m
A-Frame Hydrualic 8000kg SWL with 6.5m deck clearance
Sonar winch MacArtney Cormac 4
Radar, AID, Echosounder, Navtex, Satcom Furuno
Autopilot Navico
ECDIS Navmaster
dGPS C&C Tech
Heading iXBlue Quadrans
Heading2 iXBlue Hydrins
Speed log Skipper
VHF Icom
DP1 System Sirehna EasyDP
d’ROP
Manufacturer Hydrobotics (under license from
Bibby Marine Survey Services, patent pending)
Dimensions 1.8 x 1.2 x 1 m
Weight 460 kg in seawater, 500 kg in air
Depth rating 300 m
Max thrust, Forward 848 kgf
Max thrust, Reverse 760 kgf
Max thrust, Lateral 804 kgf
Hydraulic Power 75kW (100SHP), nominal 3000V AC
Auto functions Heading, depth, altitude, track follow
Base equipment Fiber optic gyro, gyro, altimeter, depth sounder, color camera, mono low light camera, LED lighting, USBL beacons
Optional equipment DVL, Sonar, MRU
Survey Capability TSS350, TSS440, TSS Dual Track, Multi-beam echo sounder, side scan sonar, gradiometer, 3D imaging sonar
Deployment Through moon-pool or over-side/cantilever
SWL 4100 kg on bottom layer
Average line speed >30m/min
Lift umbilical Double armored, lift,
16 conductors plus fiber optic link
Diameter 27.2mm
Breaking strength 38038 kgf
LARS Passive cursor with latch box and
umbilical sheaves on a 20 ft. ISO skid
SWL 4100 kg
Power unit Hydraulic integrated into umbilical winch
Output 37.5kW
Power requirements 1x400v/350A and 1 x 400v/75A
(As published in the MAY 2015 edition of Marine Technology Reporter - http://www.marinetechnologynews.com/Magazine)
Read d’ROP Bibby’ Hydromap’s Custom-built ROV in Pdf, Flash or Html5 edition of May 2015 Marine Technology
Other stories from May 2015 issue
Content
- Grasshopper Rides Falcon for 3D View of Dam page: 8
- Meet the AutoNaut page: 14
- WindSentinel Floating LiDAR Helps Cut Costs page: 22
- AUVs: Getting Defensive page: 28
- Dive into Norway's Subsea Valley page: 38
- d’ROP Bibby’ Hydromap’s Custom-built ROV page: 44
- MacArtney Launches NEXUS MK VII MultiPlexer page: 50
- EvoLogics Launches High-speed Mini-modem page: 50
- New Tracking Tech: Diver6 System page: 51
- Applanix’ Expanded Marine Product Portfolio page: 51
- Kongsberg’s New Marine Motion Sensor page: 51
- Falmouth Scientific’s New Chirp Transceiver page: 52
- Teledyne TSS Launches Powertrack Subsea Cable Tracker page: 52
- Valeport’s SWIFT SVP page: 53
- Dolphin Sea View 2D Sonar page: 53
- Fifth-Generation OCTANS Launched page: 53
- New Sonardyne ‘Syrinx’ Doppler Velocity Log page: 55
- New Software from EIVA page: 55
- Linden Photonics Debuts Hybrid Cables page: 56
- STR Unveils Rechargeable Battery Pack & Charger System page: 56
- New Switchable Magnet Launched as Tool for ROVs page: 57
- New Multibeam Z-Boat page: 59
- Seaperch Underwater Robotic Championships page: 60