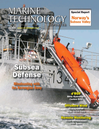
Meet the AutoNaut
Exhibitions are fertile grounds to discover new technologies, and Ocean Business 2015 in Southampton, U.K. last month did not disappoint. Here MTR speaks with Dan Alldis, Naval Architect at MOST (Autonomous Vessels) Ltd. regarding his companies new offering to the subsea market.
For readers not familiar, describe MOST.
MOST (AV) Ltd. is a micro start up based on the South coast of the United Kingdom. At the waterside office in Chichester, the team are responsible for the R&D, project management and the build of their product, AutoNaut. Plymouth is their base for sea trials, deployments and customer demonstrations. Trading since late 2012, the team has developed an Unmanned Surface Vessel (USV) called AutoNaut. Wave propelled, silent, persistent and cost efficient, it is a revolutionary data gathering platform designed for tasks which are inherently dull, dirty, dangerous and deep (long range). With boats in service with academic institutions in the U.K. and the U.S., MOST (AV) Ltd. are working hard on developing the next generation of AutoNaut vessels and marketing this revolutionary platform across a range of industry sectors.
Provide, in details, the vehicle.
AutoNaut is primarily wave propelled; harvesting the energy from the ‘motion in the ocean’ to propel the vessel forwards, the product of some 30 years of experimentation by company Director, Mike Poole. Over the last two years, the engineers at MOST (AV) Ltd. have been working hard to develop the efficiency and robustness of the system and prepare the product for the conditions expected on persistent, offshore data collection missions.
AutoNaut is available in two sizes, 3.5m and 5m but the technology is scalable and unmanned boats up to 10m are possible (this limit in size reflects likely maritime operating regulations). The 3.5m vessel is easily car-topped or trailored and can be launched with just one person.
AutoNaut can be remotely driven away from a slipway or towed to a release point using a small support boat. For recovery, AutoNaut can be sent back to a waypoint just offshore and escorted back in with a support boat or can be recovered by a ship at sea using a crane or davit.
The wave propulsion will offer 2 – 3 knots vessel speed with a 3.5m hull and 3 – 4 knots with a 5m hull. In the case of calm weather or in an area with strong tidal streams, an electric propulsion pod is available to provide 1 – 2 knots speed; this is also useful when maneuvering away from a slip.
Photovoltaic panels trickle charge the vessel’s lead gel batteries during daylight hours, powering the command and control system and sensors. In low sunlight areas and for high power sensors, a methanol fuel cell can be added to the fully autonomous power supply to charge the batteries.
AutoNaut can be controlled using local UHF or WiFi comms, or an Iridium Satellite link. Waypoints, tracks and missions can be sent to the vessel by the pilot at any time and easily amended dependent on weather conditions or mission requirements. With AIS collision avoidance enabled, AutoNaut will assess all AIS targets within a 4km range and avoid any which are on a collision course. Radar transceivers are an option most customers chose, as a failsafe to alert those around of the vessel in their proximity.
AutoNaut is fully configurable to any customer’s requirements. A wide range of sensors can be fitted through the hull, on a mast and / or towed behind the vessel. ADCPs (Acoustic Doppler Current Profilers), CTDs (Conductivity Temperature Depth), weather stations and Passive Acoustic Monitoring arrays have all been integrated and trialed in AutoNauts to great effect. The 5m hull design is optimized to operate high resolution Multi Beam Echo Sounders.
In brief, walk us through the rationale to design this vessel … what problem(s) was it developed to solve?
Operating any manned ship for data collection is expensive. Salaries must be paid, food, fuel, maintenance is costly and often range and sea conditions limit the areas in which data can be gathered. With an unmanned surface vessel, data can be collected 24/7 in a much wider range of weather conditions, for much longer periods and more cost effectively.
The patented wave propulsion system further increases the persistence of AutoNaut. In theory she could propel herself at two knots indefinitely collecting data across the oceans. In principle the limiting factor on mission length will be biofouling, barnacles and marine growth etc., which will slow the vessel down and impact sensor performance.
The ability to launch and recover the AutoNaut easily from a slipway or a ship is beneficial. A route can be pre-programmed from a launch site from where she can make her own way out to the survey area, complete her mission, send data back in real time and drive herself back for recovery with all the raw data safely logged onboard.
AutoNaut can replicate what a wave buoy can do, except there are no expensive moorings which are prone to breaking, she can deploy herself without the need for a ship and she can recover herself. AutoNaut is also capable of sampling across a range of sites, autonomously and under her own power.
In short, AutoNaut is a cost effective, low man-power data collection platform. Zero emission, extreme persistence and capable of surviving extreme weather conditions.
Specifically, how is your vessel designed to work, and what differentiates it from other vessels on the market?
Other wave propelled vessels are already being used in a number of offshore industries, but AutoNaut is the only vessel on the market which uses pitch and roll to propel herself forwards. The monohull has a draft of less than half a meter which reduces fouling and entanglement and increases efficiency; sensors mounted through the hull also have an uninterrupted view of the water column below. The hull is carefully designed so that in the event of capsize, she rights herself and carries on with her mission.
The wave propulsion is silent, which means an acoustic array is able to record a full 360º without interference from a propulsion system. AutoNaut is a ‘storm-proven’ unmanned surface vessel technology, weathering Storm Force 10 winds and 7m significant wave heights in the Atlantic Ocean in October 2014.
Are there any new or innovative use technologies on our vessel that we won’t see on others? Please be specific.
As mentioned above, the wave propulsion system has been developed into a simple, elegant solution offering silent, persistent and cost effective operation. While wave propulsion technology is used on other craft, AutoNaut is a unique monohull vessel. This technology is not new. Back in 1895, Herman Linden build his Autonaut using a system with some similarities to the MOST (AV) Ltd AutoNaut. Company director Mike Poole picked up on the idea during his research in the 1980’s and began developing his own version of the system in his free time. Mike even built a 25m wave tank at the bottom of his garden in Devon to test his designs (much to the dismay of his neighbours downhill!). In 2012, Mike was introduced to David Maclean, a retired Royal Navy Commodore running MOST Ltd. (Marine One Stop Technologies); David loved the idea and began working with Mike to engineer the system for production.
Since 2013 the company has grown organically and has now built four AutoNauts while developing the systems to improve reliability and efficiency.
AutoNaut has a revolutionary command and control system developed and built by H-Scientific Ltd., in Waterlooville, UK. The Micro-Spectre system provides all the autopilot, powering and sensor control systems onboard, allowing pilots to remotely operate AutoNauts from anywhere with an internet connection.
The system is custom built and runs without an operating system (Windows / Linux etc.) which means the current draw is extremely low. The whole system runs on H-Scientific’s RCW (Remote Control Workstation), an innovative front end package which gives pilots access to AutoNaut’s systems 24/7. Power consumption, sensor sampling and mission control are all manageable easily from the intuitive program.
Sensor data is captured and stored in ‘raw’ form on the AutoNaut’s data logger. The platform control system can analyze the data and compress into packets which are sent over the satellite communications network at intervals set by the pilot. This is an extremely valuable tool which allows an operator to evaluate the data being captured, change settings or alter the mission profile to track specific features or phenomena.
In looking at your vessel and its capabilities, rank the top three markets/niches you see it serving best, with short descriptions of why.
There are a number of different markets which AutoNaut will become invaluable within.
• Scientific Data Gathering
AutoNaut is already being used in the U.K. and U.S. to gather scientific data; from CTD and water content analysis to current profiling and meteorological data collection. The National Oceanography Center in Southampton have been a major partner with MOST (AV) with ajoint SBRI project with dstl, which provided funding to develop the prototype AutoNauts. NOC (Southampton) purchased their own AutoNaut ,‘Gordon’, which has already been used on a deployment in the UK, tracking Oceanic Fronts off the Isles of Scilly and tagged fish off the Plymouth Coast in Devon, United Kingdom. Texas A&M University have bought an AutoNaut for use in the Gulf of Mexico . It will use an ADCP and CTD to monitor the loop currents typical around the Gulf as well as providing a comms link between other university assets.
• Oil, Gas & Renewables
With oil prices down and oil majors looking for ways of reducing their costs, unmanned systems are a real option for service providers in the Offshore O, G & R sector. AutoNauts can complete MBES survey on assets underwater, monitor hydrocarbon slippage from surface assets and transfer platforms, provide marine mammal monitoring around piling and drilling sites and offer security and surveillance possibilities to an operator. These tasks can be completed by manned ships, but within strict weather and sea condition windows often with a high premium. An AutoNaut can carry on sampling autonomously for extended periods at a fraction of the cost.
• Defence and Security
AutoNaut’s silence, persistence and minimal visual and radar profile makes it a valuable asset for a number of defense operations. The ability to autonomously track assets both on and under water for extended periods is extremely valuable. Unmanned systems are often used for the 4 D’s; Dull, Dirty, Dangerous & Deep (long distance). AutoNauts can operate in ‘swarms’, collecting oceanographic data and still and video images eg for border security, among many other applications.
In overview, what did you see in the autonomous vessel market that told you that this was a good time to invest in a new system.
The ability to offer 24/7 data capture at a fraction of the price of a manned asset is extremely valuable to many people. Autonomous systems have been outlined by the UK Government as one of the ‘Eight Great Technologies’. The First Sea Lord, Admiral Sir George Zambellas has said “The Royal Navy will lead – and win – through the innovative and robust exploitation of Marine Autonomous Systems. They open up a new world of possibilities”.
The riverene and lake survey market is flooded with small Autonomous Surface Vessels but very few are proven inshore and offshore in extreme conditions; this is where AutoNaut excels.
What was the greatest challenge in bringing this vehicle from a concept to reality?
As an engineer, I must always think about the conditions in which the vessel will operate. The biggest challenge we have faced is how we engineer the systems to withstand the harsh offshore environment, while keeping an eye on weight, cost and manufacture. We are always completing research and feasibility studies on the new technologies and materials available to us. Our hulls are a composite of Glass and Kevlar Fibers giving us excellent impact and structural strength; almost literally bullet proof! We have used SLS (Selective Laser Sintering) 3D printing to create intricate parts quickly and to extremely high tolerance which have been used in the production vessels to great effect.
Putting electronics in saline environments has proved tricky, and we have had to design sub-sea housings to encase electronic components and assemblies to ‘proof’ them in the case of submersion. The offshore environment will quickly find any design or manufacturing weakness and we are always looking for improvements to our resilience.
What do you envision will be the greatest challenge in bringing this vehicle from reality to market success?
There are two hurdles to jump over when bringing AutoNaut to market:
• Proving the concept and reliability: Our technology sometimes seems ‘too good to be true’, a boat that needs no engine, can weather any storm and collect data at a fraction of the cost of a manned ship. The way to prove this is to have the vessels out there collecting real data for as long as possible. As a small, startup company this can be demanding and expensive, but we now have two 12+ day missions under our belts and an Atlantic storm which AutoNaut weathered almost unscathed. Now that we have AutoNauts with our customers, we should see them racking up the nautical miles pretty quickly.
• Convincing customers that breaking the mould could save them a lot of money: We are slowly seeing many companies coming round to using unmanned systems, with many trials and tenders available for the feasibility of using USV/ UUV’s for data gathering. However as the technology is so new, most ‘big’ companies are reluctant to commit to buying unmanned systems, because of the potential risk. AutoNaut has been branded a ‘game changer’ which is both good and bad, because it really can improve data capture efficiency, and productivity.
AutoNaut in the Field
In early 2014, The National Oceanography Centre in Southampton began planning the MASSMO mission, which was to take place in October/November 2014. This first part of the mission was to deploy multiple unmanned vehicles in a ‘fleet’ to track Oceanographic Fronts from the Isles of Scilly in South West England and out towards the continental shelf in the Celtic Sea. The second part of the mission was to be just off the coast of Plymouth, England and this was to track ~85 fish tagged by the Marine Biological Association based on Plymouth Hoe.
AutoNaut was selected to be part of the fleet, and a boat was commissioned by NOC to join their rapidly growing MARS (Marine Autonomous Robotic Systems) Fleet. For phase one of the mission, she was to be fitted with AirMar weather station, Solar Insolation sensor, a WetLabs Triplet PUC and to tow the J+S Narcine Array, a passive acoustic array for marine mammal monitoring. For phase two of the MASSMO project, she swapped the acoustic array for a VEMCO VR2C acoustic modem which was to monitor the ‘pings’ produced by trackers attached to fish released off Plymouth Breakwater. During both phases, she was fitted with two powered GoPro cameras, capturing high-res still images to monitor sea birds and marine litter. The results were extremely positive with various sightings of birds, litter and marine traffic.
Phase One saw AutoNaut launched from a slipway in the Isles of Scilly, she was towed out just past the harbour entrance and then released and sent on her way out to the Celtic Sea. She was escorted just past the Islands, with the piloting taking place in the MOST (AV)head office in Chichester. After reaching the ‘muster’ point, she made her way down to the ‘Candy Floss’ Array in the Celtic Sea for data calibration. On the way to the muster point she successfully weathered a Force 10 Atlantic storm with 7m+ significant wave height. The waves were extremely steep and dangerous, but AutoNaut self-righted and carried on with very little damage. After 13 days at sea, she was sent back to a waypoint just North of the Isles of Scilly and met by the recovery team in a RIB which towed her back to the harbour for recovery up the beach.
Phase two saw AutoNaut launched from Plymouth Harbour and towed clear of the breakwater where she was released and sent for calibration on the ‘range’ set up by the MBA. During this mission AutoNaut successfully tracked a number of fish which were tagged and released up to 3 months earlier!
The data captured and sent back in real time over Iridium was analyzed by the staff at the MBA and NOC and partner companies and proved to be extremely useful.
Plans are already in place for NOC to use their AutoNaut again in a similar mission over the next 12 months.
(As published in the MAY 2015 edition of Marine Technology Reporter - http://www.marinetechnologynews.com/Magazine)
Read Meet the AutoNaut in Pdf, Flash or Html5 edition of May 2015 Marine Technology
Other stories from May 2015 issue
Content
- Grasshopper Rides Falcon for 3D View of Dam page: 8
- Meet the AutoNaut page: 14
- WindSentinel Floating LiDAR Helps Cut Costs page: 22
- AUVs: Getting Defensive page: 28
- Dive into Norway's Subsea Valley page: 38
- d’ROP Bibby’ Hydromap’s Custom-built ROV page: 44
- MacArtney Launches NEXUS MK VII MultiPlexer page: 50
- EvoLogics Launches High-speed Mini-modem page: 50
- New Tracking Tech: Diver6 System page: 51
- Applanix’ Expanded Marine Product Portfolio page: 51
- Kongsberg’s New Marine Motion Sensor page: 51
- Falmouth Scientific’s New Chirp Transceiver page: 52
- Teledyne TSS Launches Powertrack Subsea Cable Tracker page: 52
- Valeport’s SWIFT SVP page: 53
- Dolphin Sea View 2D Sonar page: 53
- Fifth-Generation OCTANS Launched page: 53
- New Sonardyne ‘Syrinx’ Doppler Velocity Log page: 55
- New Software from EIVA page: 55
- Linden Photonics Debuts Hybrid Cables page: 56
- STR Unveils Rechargeable Battery Pack & Charger System page: 56
- New Switchable Magnet Launched as Tool for ROVs page: 57
- New Multibeam Z-Boat page: 59
- Seaperch Underwater Robotic Championships page: 60