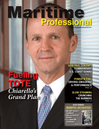
Moving Ahead with MLC: the true course to compliance.
The Maritime Labour Convention 2006 (MLC) impacts the world’s 1.3 million mariners in one way or another. In a nutshell, MLC embraces fundamental principles found in other international labor conventions and applies to all ships entering member port states, as well as to all flag state signatories. Entering into force on 20 August 2013, one year after registering 30 ratifications of countries representing over 33 per cent of the world gross tonnage of ships, the convention today has been ratified by more than 60 states, representing 80 percent of global shipping.
The MLC Code addresses the minimum requirements for seafarers to work on a ship, conditions of employment, accommodations and amenities, healthcare and social issues. For some operators, it means simple compliance with a minimum set of standards and managing the costs associated with that standard. For others, it entails a genuine effort to improve the lot of mariners everywhere. For all of them, audit, enforcement and certification of compliance are also part of the game.
Compliance and Enforcement
As Port State Control authorities prepare to launch a crackdown to ensure that watchkeepers are getting the hours of rest set by the STCW Convention, MLC compliance will also be on the minds of shipowners everywhere. A three-month Concentrated Inspection Campaign (CIC) starting on September 1 2014 by Tokyo and Paris MOU inspectors will zero in on verification of watchkeepers’ hours of rest, the vessel’s Minimum Safe Manning Document (MSMD) and records of rest. As many as 10,000 inspections could be carried out during the CIC.
The road to compliance can entail a minimal effort or it can mean an extraordinary leap forward for those seafarers lucky enough to toil for a progressive thinking operator. Whichever route is taken by the operator, the effort begins with certification of compliance. Typically, this involves the use of an auditor as named by the flag state of the vessel in question, but this is dependent on the individual flag state’s rules and other “recognized organizations” can be named to perform the audits. As a rule, this aspect of the process is rigidly controlled.
Lloyds Register (LR) is one such approved organization. Robert Brindle is LR’s MLC & STCW Lead Specialist, Marine Management Systems, in the Classification Group. Brindle told MarPro in July that Lloyds Register had, to date, carried out more than 5,000 individual MLC inspections since January 2013. As with any new protocol, he said, ships and their operators get better at compliance with practice. MLC has been no different.
In all cases, the process involves looking at how an operator and the vessel manage the MLC Code. That starts with a close look at the declaration of compliance (Part II – the company’s responsibility) and part one (flag) – the summary of flag rules. Says Brindle, “The goal should be to meet the regulations and improve the life of the seafarer.”
Brindle, who at one time sailed for the Cunard Steamship Company Ltd and holds a Class I Master’s certificate, brings the deep experience of a human resources (HR) manager to the job. The rare combination serves him well as he leads a global team of auditors who are navigating sometimes uncharted waters in much the same way that the vessels they audit are trying to do. Brindle explains, “I’m here to lead a team of global inspectors. We need to educate inspectors to look at things that they never had to do before.” This includes the understanding of the collective bargaining agreement in place.
The review begins by making sure that the operating company’s declarations are in concert with flag rules. Then, every vessel is done in sequence. LR’s Brindle says that a ship review can be done within a day, with the on board inspection usually spanning about 6 to 8 hours, depending on what is required for a particular flag state. Brindle explains, “Typical hot button issues include comparing the hours of rest against the records of Overtime and then verifying that the crew is actually getting paid for the work that they do.”
One common deficiency noted by LR inspectors is that Seafarer work agreements sometimes do not meet the requirement of MLC. Along with that, says Brindle, is the responsibility of the seafarer to carry their work contract with them at all times. He adds, “This is just as important as any other competency certificate.” Another area needing attention is the formatting of medical certificates, but Brindle says that this is usually a flag state issue or in other words, an observation, not a deficiency. And, he says, some flags, to their credit, have made changes.
Other garden variety deficiencies include finding discrepancies between Work and Overtime records, but, he says, this mostly involves seafarers not filling out the forms properly, as opposed to outright falsification. As for living conditions on board vessels, this aspect of the global merchant fleet is improving. Brindle admits, “You see it [poor sanitation, amenities, living conditions], but far more rarely than in the past.” That’s good news.
All violations of the MLC Code are reported to the flag state. Serious issues could result in a vessel’s detention. According to LR, any and all deficiencies must be corrected within 3 months. As the process matures, it is getting smoother and Brindle says that the Code is beginning to have its desired impact, saying, “Deficiencies are reducing over time. For example, a company operating 40 ships might undergo the first 10 vessel inspections with varying degrees of success and typically, the next 30 will go smoother because they know what inspectors are looking for.” In other words, practice makes perfect.
Like safety, real commitment to the tenets of MLC has to start at the top, where the decision to invest time, energy – and yes, sometimes money – has to be made. And, crew welfare involves far more than just a clean ship and a fair day’s wage. Shipowners who buy into that concept are already well ahead of the curve.
Crew Comms: Key Morale Builders
The new normal for merchant seamen includes access to an adequate array of communication options while employed on board. Shipowners who do not provide such amenities are now finding it tough to keep mariners on board. Looking to leverage that growing demand from the marine sector, KVH Industries provides, in addition to myriad other products, in-motion satellite TV and communications systems for vessels. Recent KVH acquisitions of Videotel (July 2014) and Headland Media (May 2012) have now been rolled into KVH Media Group and allow KVH to bring more eLearning and better tracking of each crewmembers certificates to shipowners.
The company’s global reach now reaches as many as 25,000 vessels, with services varying from training and eLearning services (about 11,000 vessels) to movies and newspapers deliver by DVD, email, etc., (about 10,000 vessels) and the KVH miniVSAT service (about 4,000 vessels). Tens of thousands of mariners are receiving the benefit of robust connectivity, quality entertainment and the advantage of on board learning that potentially reduces the amount of time which has to be spent training during vacation periods. For shipowners, New SOLAS Regulations and STCW benchmarks are becoming harder to comply with and still harder to track. KVH helps to track all of it, in a turnkey package, allowing an operator to confidently outsource the task, if desired.
All of that is great news for the crew, but it also costs money. On the other hand, KVH provides low cost content delivery – large amounts of data delivered just once to all customers – which frees up bandwidth to do other things. Jim Dodez, KVH Senior Vice President for Marketing and Planning says, “Ships no longer have to ‘resize’ comms to allow both. This can save a lot of money.”
Moreover, KVH now reaches more than 105,000 seafarers on its innovative CrewToo social media site.
CrewToo is a social media site for mariners, or as Jim Dodez calls it, “The Voice of the Seafarer.” In a nutshell, it allows communication and socializing, and is open to crewing agencies and job seekers alike. In some cases, it can help verify the qualifications of a mariner prior to hiring.
Recently KVH delivered the World Cup via IP Mobilecast service to approximately 1000 seafarers. Dodez explains, “We talked to our best clients and got great response.” He added that other premium content, including English Premier League football, would also be delivered in the near future. But owners and crew don’t have to be satisfied with what KVH thinks is interesting. The service allows customers to pick and choose what content they want based on the demographics of the crew. And the new KVH business acquisitions brought on a lot of new media expertise into the picture. Today, KVH is collecting news broadcasts and rebroadcasting to ships, sometimes with only 3-4 hour delay.
Market leading operators naturally turn to market leading equipment and service providers. For example, Harvey Gulf International Marine and its President and CEO Shane Guidry are known as high end providers of multi-missioned offshore support vessels in the Gulf of Mexico, and beyond. Proving conclusively that even flag states that haven’t signed the MLC Code can still more than comply with its intent, Harvey Gulf is updating its onboard communications solution with KVH.
New Harvey Gulf mariners quickly find out what long time employees already know. All Harvey Gulf newbuild hulls have all the bells and whistles related to crew comfort and amenities. Acquisitions of used tonnage get upgraded – or they get sold. In terms of communications options for the crew, the KVH provided suite is impressive. It includes, 24/7 access to telephone services, DirectTV on all vessels (the Captain and Chief Engineer have their own receivers and some vessels have TV access in all cabins), access to the KVH newly acquired content from Headland Media and of course, Internet. Notably, Harvey Gulf is in the process of rolling out WiFi across all of its vessels.
MLC and Medical Predictors
There are few things more important than the health of a mariner. For that reason alone, the well being of mariners is central to the central purpose of MLC. With that in mind, more than one year ago, the Yale University School of Medicine, in conjunction with managed healthcare solution provider Future Care, Inc., released a study entitled Preliminary Evaluation of Seafarers Health Care and Determination of Predictors of Illness. The effort to provide proactive as opposed to reactive healthcare to mariners was underway. Until then, very little research had been conducted on the health and general welfare of the world’s seafarers.
With the goal of determining risk factors for injury, illness and disability among seafarers, the collection of anonymous, protected and genericized data was begun. The effort, according to Dr. Martin Slade, Director of Research, Occupational & Environmental Medicine at Yale University School of Medicine, has now been expanded toward trying to determine predictors of repatriation among seafarers. Slade and his colleagues began to look at repatriation as the maritime counterpart of an emergency room visit for land based workers.
With pre-employment medical examination data on approximately 20,000 seafarers in hand, they matched that data to those seafarers that were repatriated. Initial observations based on analysis of this data revealed that lifestyle conditions were strongly associated with repatriation. The relatively simple interventions that could be developed to significantly reduce repatriation rates and costs are only now becoming evident.
Based upon the data, the strongest predictor of repatriation was the seafarer’s body mass index (BMI). BMI is a measure of relative weight based upon a person’s height. People with values between 18 and 25 are considered normal, people with values between 25 and 30 are considered overweight, and people with values above 30 are considered obese. Compared to seafarers with normal BMI, overweight and obese seafarers are 50% more likely to be repatriated. Graph 1 amply demonstrates this tendency.
Another surprising predictor of repatriation is the measure of kidney function (Creatinine), something can be measured via simple blood test. Even at the high end of the normal range of measurement (deciles / umol/L), the incidence of repatriation is twice that of those seafarers at the lower end of the scale (Graph 2).
More in-depth analyses are underway to identify other demographic, medical and occupational predictors of repatriation as well as to see if there are separate predictors for different subpopulations of seafarers. Yale and Future Care are on the case. Imagine what could be accomplished if all shipowners pooled this pre-employment health data in a responsible fashion, with the ultimate goal of the seafarer’s wellbeing at heart?
MLC by Design
Central to the care and comfort of the seafarers is, quite naturally, largely a function of the environment that he or she is asked to work in. Thirty years ago, it was not unusual to see a shipowner abruptly cancel plans for an elevator shaft in a newbuild design after choking on the exorbitant cost to put it in. There wasn’t much thought given to the mariner’s comfort in those instances, and if you were unlucky enough to get assigned to such a vessel, you certainly didn’t forget anything when you came down to work in the morning. It was a long way back up.
Today – with the MLC Code and seafarers who actually have choices – and in the highly competitive world of offshore oil & gas, the equipment that ensures both comfort and operational readiness is everything. Because of that, even naval architects and designers are getting involved in the MLC Code.
According to Curt Leffers at the Elliott Bay Design Group (EBDG), his firm gets involved with the MLC convention in designing the accommodation layouts in their OSV designs. For example, sound damping is usually something that EBDG talks about with the Owner at the very beginning the vessel design process. He told MarPro, “There are a couple of damping systems for sound insulation available, and we have been specifying them much more frequently over the last couple of years. Additionally, it’s important to point out that it is becoming more common to place main engines in resilient mounts to reduce vibration and improve the crew experience.”
And, crew comfort – MLC or not – is coming to the forefront. Leffers says, “As designers, we do get involved in the creature comfort aspects of the vessel design even if they aren’t’ directly related to the MLC convention. We have seen a shift over the years in the desire for vessel Owners to provide additional comfort for crew members. This is especially true for workboats, where some of our clients have mentioned that providing additional comfort is an important element in attracting good crew members.” One way in particular that designers are getting involved in crew comfort, adds Leffers, is in the design of the HVAC system. The systems, for example, can be designed where each berth has an independent thermostat so crew members have more control of in the temperature of their berths.
Jim Hyslop, Manager of Project Development at Robert Allen LTD also weighed in. The MLC Code is definitely impacting the design process, says Hyslop, adding, “Clients are asking for this. From our perspective, it’s got primarily to do with crew accommodations. The size of cabin, the amount of natural light they have – those are the main things.”
Hyslop also points to noise as an important issue. “First, it is important for the crew to have low noise levels, also low vibration levels. These are separate things. We do a lot of work on that, it’s a big issue on tugs because they have big engines for size of the boat. Most of the noise and vibration comes from the engine, so most of the tugs do employ resilient mounting – that’s when the engine is mounted on rubber or steel.”
MLC and the Bottom Line
For some operators, MLC might represent just another headache – and an added expense – in the daily effort to balance the books. Still others see it as a way to stay out in front of the competition. Separately, the U.S. Coast Guard’s 25th Commandant, ADM Paul Zukunft, points to his service members and calls them his most important assets. Using that logic, the easiest route to MLC compliance may well involve addressing those issues before anyone comes up the gangway. That process can take many shapes and forms, from medical predictors to shipyard design, or providing creature comforts and high-end amenities. For those that do, the upfront costs will eventually translate into backend dividends.
(As published in the 3Q 2014 edition of Maritime Professional - www.maritimeprofessional.com)
Read Moving Ahead with MLC: the true course to compliance. in Pdf, Flash or Html5 edition of Q3 2014 Maritime Logistics Professional
Other stories from Q3 2014 issue
Content
- The Economics of Slowing Down Ships page: 10
- Nobody Rides for Free … page: 18
- Fuel Management & Safety page: 20
- Moving Ahead with MLC: the true course to compliance. page: 36
- Profile: Coast Guard Administrative Law Judge Brudzinski page: 40
- Evolving Threats Met by Market Innovation page: 42
- Seafarer Shore Leave: MLC Business, or Not? page: 47
- Searching for a career with Military Sealift Command? page: 54
- Newport News Fosters Home-grown Talent page: 58
- Maritime Training & Employment Numbers page: 62