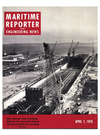
Floats Ships Off Building Platform Into Drydock
Setenave-A New Portuguese Shipyard Setenave — Estaleiros Navais de Setubal (Setenave Shipyards), was founded in May 1971 for the purpose of operating a new construction shipyard at the mouth of the Sado River, in the vicinity of the town of Setubal, Portugal. The facility is 25 miles south of Lisbon on a man-made island.
At a later stage, the decision was made to build the yard as a combined newbuilding and repair yard for large ships. This decision was based on the fact that the number of large ships sailing and on order was increasing so steadily that a shortage of docking and repairing facilities could be foreseen.
Furthermore, Lisnave Shipyard, the successful repair yard in Lisbon, could not add any more docking capacity to their pres- ent three large drydocks and it was, therefore, decided to build the necessary additional drydock capacity at Setenave.
The two drydocks at Setenave, one of 700,000-dwt capacity and one of 320,000-dwt capacity, will complement the available drydocks in the Lisbon area and will be operated in conjunction with Lisnave.
The area where the yard is located is ideally suited for a shipyard. Sheltered by the peninsula of Troia from the open sea, it provides safe anchorage and mooring places for ships of any size. The total area of the river owned by Setenave amounts to more than 750 acres, of which about 250 acres is reclaimed as an island on which the yard is located.
As the area is not yet industrialized, the availability of labor is no problem; and from the very start of the yard, extensive training programs have been put into operation with the assistance of Lisnave Shipyard and of Setenave's own school.
To ensure that the shipyard would have sufficient availability of "know-how," agreements were made with three foreign shipyards — Eriksbergs Mek. Verkstads of Goteborg, Kockums Mek. Verkstads of Malmo, both in Sweden, and the Rijn Schelde Verolme Group in the Netherlands—to assist in the training programs.
The recognition that substantial economies in both newbuilding and repair could be achieved through the combined use of capital facilities, led to a novel layout of the yard.
In essence, the areas devoted to repair are wholly separate from the areas devoted to newbuilding, except for the joint use of the graving dock and cranes.
The newbuilding portion of the dock is novel, in that the building dock floor is at the same ground level as the shipyard and the dock is formed by surrounding walls. These walls continue along the repair dock. In order to launch a newly built vessel, special lock gates are fitted at both ends of the newbuilding platform and the repair dock. The entire dock is pumped up to a sufficient height above sea level to allow the newly built vessel to float into the repair dock.
Then, the water level in the dock is reduced to sea level, the lock gates removed and the ship undocked.
The newbuilding dock is 1,378 feet long by 246 feet wide. It can be extended an additional 328 feet.
The main ship-repair dock is 1,476 feet long and 246 feet wide. It is capable of handling ships up to 700,000 dwt. It is in line with the newbuilding dock. A smaller repair dock is 1,148 feet long and 180 feet 6 inches wide. It can serve for vessels up to 350,000 dwt. The combination repair and newbuilding dock share the use of a 500-ton portal crane, and all docks are serviced by 100-ton and 15-ton revolving jib cranes.
The very latest design approach has been employed in the layout of the newbuilding yard to achieve highly efficient production.
The newbuilding plate shop has an initial annual steel output of 120,000 tons, capable of being doubled if need be.
The newbuilding yard occupies an area of approximately 90 acres. The layout is based on a U-shaped flow line, which starts at the steel unloading dock and ends at the outfitting pier.
After unloading, the steel is stored by magnetic cranes in the steel stockyard. From the stockyard, plates and sections or profiles are transported by a conveyor-belt system through an automatic shot-blasting and shop-priming machine, after which the material arrives in a buffer storage from where the heavy plate shop is fed.
In the center bay of the heavy plate shop the sections and profiles are processed, cut to size, and any other preparation is done.
Also, all webframes and similar lighter structures are prefabricated in this shop.
The automated panel line is situated in the left-hand bay over the full length of the shop and comprises a cutting station, plateassembling station, welding station, section turnover station, turntable, frame feeding and fitting station, webframe fitting station and some finishing stations. Complete blocks of up to 350 tons can be lifted from the end of the panel line by the special Scheurle block transporter. The right-hand bay is used for the prefabrication of all shaped sections for the bow and stern of a ship.
The plate shop is fitted with ample crane capacity to facilitate the work. Modern oxy cutting machines are installed, controlled numerically by an MG-16 computer-based director, or optically by a tracing table for 1/10 scale drawings.
A profile bending machine of 700-ton capacity, a portal press of 700-ton capacity and a roll press of 2,000-ton capacity also are installed in the right-hand bay. The prefabricated blocks are transported by a Scheurle road transporter to the blockstorage area beside the building platform.
Here the blocks are joined, outfitted and completed as required before being lifted by the gantry crane.
The first new construction was a forebody (872 feet long) for a 316,000-dwt tanker that Eriksberg was building. The construction of a 316,000-dwt tanker for Soponata Sociedade Portuguesa de Navais Tanques, Lda., was started in November 1975.
Drydocking and repair activities started in June 1975.
The repair shops are grouped between the repair piers and the drydock to facilitate access and minimize transport.
During the first phase of the yard development, seven repair berths for large ships are available, all serviced by 50-ton jib cranes. All other facilities, such as plate shops, pipe shops, machine shops, etc., are duplicated in both the newbuilding and repair yards to insure that they can operate independently.
A shore-based tanker-cleaning station is being built adjacent to the yard with two berths and sufficient capacity to handle all sizes of tankers.
Setenave is represented in the United States by Setenave Shipyards, Inc., P.O. Box 9056, North Bergen, N.J. 07047.
Read Floats Ships Off Building Platform Into Drydock in Pdf, Flash or Html5 edition of April 1976 Maritime Reporter
Other stories from April 1976 issue
Content
- Floats Ships Off Building Platform Into Drydock page: 6
- MarAd Approves Title XI To Finance $23.2-Million Barge/Towboat Program page: 8
- Bethlehem Appoints R. Newcomb Treasurer Shipbuilding Operations page: 8
- Schedule And Papers— SNAME Spring Meeting In Philadelphia, Pa. page: 10
- Russians Buy Oil Barriers From U.S. page: 12
- Todd To Build Six Guided Missile Frigates For Navy At Base Price Of $295 Million page: 13
- Marketing Expert Joins Oil Mop As Executive VP page: 14
- GAO Wants To Know Why Navy Is Not Using Commercial Tugboats page: 20
- Vancouver Shipyards Moves 457-Foot Ferry To Launching Position On Film Of Water page: 23
- Northern New England Section Of ASNE Elects Officers For 1976 page: 24
- Three-Year Navy Salvage Contract Awarded To Crowley page: 25
- Samson Ocean Systems Names R.H. Blanchette Regional Manager page: 25
- Evergreen Marine Corp. Announces New Ships And Plans New Services page: 27
- American Club Elects Officers And Admits Central Gulf Lines page: 27
- Navy Awards Bath Iron $224-Million Contract For Five Missile Frigates page: 28
- N.Y. SNAME To Hold Tanker Symposium At Kings Pt. April 23 page: 32
- Connecticut Company To Represent Swedish C-P Propeller Firm page: 33
- AWO Elects Geary Chairman Of Board —Directors Named page: 34
- Dual Keel-Layings Mark Submarine Tender Construction At Lockheed Shipbuilding And Construction Company page: 36
- Canadian Yards Building For Export page: 37
- 2nd International Symposium On Ship Operation Automation Set For Washington In August page: 37
- Tubbs And FitzGerald Named Vice Presidents At Donhaiser Marine page: 39
- Halter Marine Delivers Crewboat For Service In Arabian Gulf page: 41
- First Swedish-Owned Oil Rig Commissioned At Bethlehem-Beaumont page: 42
- Far East Levingston Names Lovie & Co. U.S. Representative page: 43
- Shipbuilders Council Elects Officers page: 43
- Halter Marine Names A.J. Rizzo Director Of Public Relations page: 44
- McDevitt Named President Of Three Maritime Firms page: 44
- SNAME Los Angeles Section Hears Of Conversion Of Existing Schooner Hull To Brig Pilgrim page: 45
- SNAME San Diego Section Hears Discussion Of Engineers' Tasks page: 46
- DeLaval IMO Pump Division Publishes Illustrated Bulletin On Pumps For Gas Turbines page: 48
- SNAME Philadelphia Section Discusses The Why And How Of Offshore Oil/Gas Drilling page: 48
- ARCO Installs Unit To Evaluate MARISAT page: 49
- Kawasaki-Built Ore Carrier Develops 18 Knots On Trials page: 50
- R.T. Greene Forms New Marine Company page: 50
- Conoco And Gulf Oil Enter Agreement With British On North Sea Oil Production page: 51