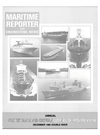
OUTSTANDING OCEANGOING SHIPS OF 1985
A roundup of some of the most notable vessels delivered by shipyards during 1985—selected for their outstanding design features, fuel efficiency, performance, and service characteristics.
AMERICAN OHIO Samsung Shipbuilding Samsung Shipbuilding and Heavy Industries Company of South Korea recently delivered the 35,900-dwt containership American Ohio to First American Bulk Carrier Corporation of Washington, D.C.
The new vessel and a sister ship, American Georgia, were built through financing by the pension fund of the National Marine Engineers Beneficial Association, and have been chartered to United States Lines. They will be used, along with three Odense-built containerships chartered from Crowley Maritime, on USL's service to and from South America on the routes acquired with the purchase of Delta Lines.
The American Ohio has an unconventional asymmetric stern whose performance and economy has been proven in more than a year's operation of the Humboldt Express and Cordillera Express that Samsung's Koje shipyard delivered last year to Hapag Lloyd. In addition to providing excellent maneuverability and seakeeping properties, the asymmetric stern is said to provide fuel savings of some eight percent at a service speed of 19.1 knots, a cost reduction of about $360,000 per year.
The new containership has an overall length of about 675.8 feet, beam of 105.6 feet, depth of 61.7 feet, and maximum draft of 37.7 feet. Main propulsion is provided by a Hyundai/Sulzer 6RTA76 diesel engine with maximum continuous rating of 19,740 bhp at 95 rpm, driving a SMM 5-bladed fixed propeller via Kobe Steel shafting. Electric power is supplied by three 1,470-kw generators driven by Daihatsu 6DL- 32 diesels.
The container loading capacity of the vessel is 552 FEUs plus" 16 TEUs, or 1,120 TEUs in holds and 1,291 TEUs (including some empties and reefer containers) on the basis of five tiers on deck—a total maximum capacity of 2,411 TEUs.
Electric outlets for 308 reefer containers are provided on the upper deck.
Ten container holds have cellular guides for 40-foot-box stowage except for forward in No. 1 hold that is fitted with 20-foot cell guides, and the No. 10 hold that can accommodate 20-foot or 40-foot containers.
Underdeck passageways are provided on the upper deck and second deck for easy and safe personnel transit between living quarters or the engine room and the forecastle.
The American Ohio has been built to American Bureau of Shipping classification + Al(E), +AMS, + ACCU, and meets all the rules and regulations of the U.S. Coast Guard and Maritime Administration for a U.S.-flag vessel. Accommodations are outfitted to the highest standard, with single cabins and private lavatories provided for a crew of 25.
The spacious bridge is designed for convenience of navigation and best visibility. Complete navigation and communications equipment is installed, including radars, echo sounder, Decca Navigator, Loran C, satellite navigator, and weather facsimile.
The underwater hull is coated with self-polishing antifouling supplied by International Paint (Korea).
ASAKASAN MARU Mitsui The 197,060-dwt ore carrier Asakasan Maru, built at the Chiba Works of Mitsui Engineering & Shipbuilding Company (MES), was delivered early this year to joint owners Mitsui O.S.K. Lines and Sawayama Kisen Kaisha. The big bulker has an overall length of about 984 feet, beam of 164 feet, depth of 79 feet, and full-load draft of 58.5 feet. She is powered by a slow-speed Mitsui/B&W 7L80MCE diesel engine with a maximum continuous rating of 20,700 bhp at 80.8 rpm. On sea trials the ship attained a speed of 16.35 knots.
A special feature of the new ore carrier is the superstructure located aft, which is shaped like a compact, streamlined tower. Such towershaped superstructures have been used by MES in the past for only four ships—three tankers built in 1965 for Fred Olsen of Norway and another in 1968 for Anders Wilhelmsen & Company, also of Norway.
Reflecting the current trend for increasing the energy efficiency in ships, use of this unusual superstructure to reduce air resistance is now attracting renewed interest.
A Mitsui ATG-V turbogenerator system (mixed-pressure turbine system) is installed for maximum utilization of the waste heat of the main engine exhaust. The ship is also equipped with a thyrister convertorinvertor type shaft generator that can be used as an emergency propulsion motor, and a power management system for most effective utilization of the turbogenerator's output.
Other energy-saving features in- elude a Mitsui Integrated Duct Propeller, a reaction rudder, and extensive use of high-tensile steel in the hull structure to reduce weight. The exterior hull bottom and waterline areas are coated with self-polishing antifouling paint.
Windlasses, mooring winches, and deck washing equipment are fitted with remote control systems with a view to reducing the crew's workload.
The engine control room and cargo control room are integrated for more performance of the duties of both. The main engine room is designed for unmanned operation, and has obtained NK's "MO-A" notation.
EASTERN SUN Jeffboat Jeffboat, Incorporated, of Jeffersonville, Ind., at mid-year delivered the motor tanker Eastern Sun to Sun Refining & Marketing Company of Aston, Pa.
The 2,500-dwt product carrier was designed to carry clean petroleum and lube oil products for the U.S. Eastern Seaboard. This new generation of coastal tankers not only enables the operator to service restricted terminals and limiteddraft accesses, but concurrently op- erate safely and reliably in open ocean trade.
The new vessel has an overall length of 280 feet, beam of 45 feet, and design draft of 16.5 feet. She is powered by two GM Electro-Motive Division 8-645E7C diesel engines developing a total of 2,900 bhp, driving Lips propellers via Reintjes WAV 1450 reverse/reduction gears with WABCO controls. Two Detroit Diesel 8V71 engines drive 120-kw International Electric generators for ship's service electrical power. Compressed air for starting the main and auxiliary engines is provided by two Quincy D325 air compressors.
The 25,700-barrel capacity of the Eastern Sun is handled by three Goulds deepwell and one Sier Bath self-priming cargo pumps. These are driven by Detroit Diesel 8V71 engines.
The cargo pump engines are located in a heated deck machinery room, providing effective weather and sea protection.
To gain substantial economic benefits of reduced manning, the new tanker was designed to full unattended engine room requirements (the American Bureau ACCU notation), with automation equipment provided by Harbor Marine Engineering.
Mooring operations are accomplished through the use of deck machinery powered by a central hydraulic system. Redundant hydraulic pumps are driven by front power takeoffs attached to the cargo pump engines. A hydraulic fixed-boom crane is provided for cargo hose handling. In addition to the dualwildcat anchor windlass, two mooring winches and a vertical capstan are installed for handling lines, all provided by New England Trawler.
Navigation and communications aids and controls include two Raytheon Marine Pathfinder radars, electric autopilot and steering control system, and fully automatic Loran C and RDF equipment, as well as Raytheon SSB and VHF radiotelephones.
The Eastern Sun was designed by Sun Refining & Marketing in conjunction with J.J. Henry Co., Inc. of New York. She is classed by the American Bureau of Shipping +A1, Oil Carrier, +AMS, ACCU.
GOLDEN QUEEN Mitsubishi The 7,918-dwt chemical tanker Golden Queen, built at the Shimonoseki Shipyard & Engine Works of Mitsubishi Heavy Industries, Ltd.
in Japan, was delivered in April this year to Kyoei Kisen Company of Tokyo. She is expected to operate in worldwide service, including the Great Lakes and Mediterranean areas. The parcel tanker is fully equipped in accordance with the IMO Chemical Code to carry 132 kinds of cargoes, including petroleum products, safely, reliably, and efficiently.
The vessel has an overall length of 357 feet, beam of 58.4 feet, depth of 58.4 feet, and design draft of 25.6 feet. Her main propulsion engine is a Mitsubishi UE 6UEC45HA diesel with a maximum output of 6,000 bhp at 185 rpm; normal output is 5,400 bhp at 179 rpm, producing a service speed of 13.7 knots. A pressurized fuel oil supply system enables the main engine to operate on heavy fuel of up to 5,000 sec Redwood 1. The machinery installation, equipped for automation to satisfy the MO requirement of Nippon Kaiji Kyokai, is designed to permit the main engine, generators, and engine room auxiliaries to be controlled and monitored remotely from the engine control room. In order to safely navigate narrow channels and harbors, the vessel is equipped with a controllable-pitch propeller and a Mitsubishi/KaMeWa bow thruster.
Cargo space is partitioned by two longitudinal bulkheads and several transverse bulkheads. Center tanks are built of stainless steel, without interior frame members in order to facilitate cleaning. Arrangement and frame members of the wing tanks, which are built of mild steel coated with inorganic zinc paint, also give full consideration to the cleaning requirements. Each tank is served by a separate pump and cargo line so that various cargoes can be handled simultaneously, free from contamination. The cargo control room is equipped to facilitate quick and accurate control of cargo handling and monitoring, while reducing the crew's workload. An MHI loading computer is provided to calculate not only the stability and longitudinal strength of the vessel but also the stability when damage occurs under any given loading condition.
Features incorporated in the design of the accommodation space include: the engine casing is separated from the living space to eliminate engine room noise; a floating floor construction is used in the control room and accommodation area; a skewed propeller is used to reduce vibration; and hydraulic power units are installed in the forecastle away from the living quarters.
HOLIDAY Aalborg The 46,052-grt luxury cruise liner Holiday was delivered this year by Aalborg Werft in Denmark to Carnival Cruise Lines Inc. of Panama.
Designed and built as a steel-hulled, twin-screw/rudder passenger ship, she has a raked stem, transom stern, bulbous bow, bow and stern thrusters, and fin stabilizers.
The new liner has an overall length of 727 feet, beam of 92 feet, depth to upper deck of 69 feet, and design draft of 24.6 feet. A total of 716 standard cabins are arranged on decks 4, 5, 6, and 7, and 10 deluxe verandah suites are located on deck 11 forward. Total passenger capacity is 1,794, and she carries a crew of 646 persons.
Propulsion is provided by two low-speed Sulzer 7RLB66 diesel engines with integral thrust bearings, each coupled directly to KaMeWa controllable-pitch propellers having a highly skewed blade design. The main engines each have a maximum continuous rating of 15,770 bhp at 140 rpm.
The Siemens propulsion control system, which includes automatic main engine overload control as well as an engine load increase feature, incorporates different operating modes, including: constant-speed operating mode at 136 rpm for shaft alternator operation; and two combination operating modes—one thrust mode and one pitch mode— where the engine speed, propeller thrust, and propeller pitch are controlled according to a pre-established curve.
At sea, the ship will normally operate in the constant-speed mode at 136 rpm, and the shaft-driven alternators will feed the main switchboard. As it is not the intention to run the two shaft alternators in parallel, the main switchboard is capable of being operated in a "split" mode by means of a section breaker on the bus bar. In this mode each alternator will feed half of the main switchboard.
The vessel's hull form has been developed to give good propulsion and seakeeping performance with due regard to the large propeller tip clearance requirements at the various design conditions. The lines have been designed to give the smallest possible resistance, with the bulbous bow designed for a draft of 24.6 feet and optimized for a service speed of 19.5 knots.
Except for certain parts of the public spaces, where special features are introduced, Dampa continuous ceiling systems consisting of prestressed, baked enamel, steel/aluminum panels, are used throughout the accommodations. Sound-absorbing decks consisting of mineral wool slabs with steel tops are installed in the crew accommodations above the engine rooms as well as below the bandstand and dance floors to provide maximum insulation against noise.
The Holiday is a typical example of the ships produced by the Ship Division of Aalborg Vaerft—a highly complex passenger vessel of the most advanced design and comprising the latest technology, purposebuilt to insure full compatability with the requirements of the owner.
IDEMITSU MARU Ishikawajima-Harima The 258,090-dwt, super-energysaving very large crude carrier Idemitsu Maru was delivered recently by Ishikawajima-Harima Heavy Industries Company's Kure Shipyard to Idemitsu Tanker Company of Tokyo.
The big tanker has an overall length of 1,058 feet, beam of 196.85 feet, depth of 94.5 feet, and maximum draft of about 63 feet. Propulsion is provided by a low-speed IHI/ Sulzer 8RTA84 diesel engine with a maximum continuous rating of 23,500 bhp at 65 rpm and normal rating of 21,150 bhp at 62.5 rpm. On sea trials, this latest model of the Sulzer design achieved a fuel oil consumption rate of 117.5 grams per brake horsepower hour.
The Idemitsu Maru was designed and equipped with the latest energy- saving features, and is operated with a reduced crew of only 16 persons.
IHI's LV (Low Viscosity) hull form minimizes resistance by improved design, and the bulbous open stern lowers the thrust reduction and increases wake gain by improved stern hull form design.
The low propeller speed of 65/62.5 rpm improves propeller efficiency and reduces required propulsion power.
The IHI SSG-MK III (Super- Economical Shaft Generator System) saves fuel by generating electric power either by feeding steam from an exhaust gas economizer to a turbogenerator, or by a shaft generator system taking power off the propeller shaft. The IHI Electric Differential Epicycle Drive can control generator frequency within the allowable range against the change in main engine output between 40 and 90 percent of mcr.
The ship is equipped with an IHI Navigationmate, an automatic navi gation system with digital chart navigation combined with Loran C and NNSS. Navigation, machinery, radio, and cargo and ballast operations are centrally controlled from the bridge. TV cameras monitor the engine room and cargo manifolds, and the deck machinery is fitted with a central hydraulic system with remote operation. A sequential remote control system for warm-up of the cargo pumps includes remote start and stop operation.
The tanker's segregated ballast tank capacity is sufficient for safe navigation even in rough sea conditions without filling the cargo oil tanks with ballast water. The exterior hull is coated with self-polishing antifouling paint.
ISOLDE Kockums The pure car/truck carrier Isolde has been delivered by Kockums AB of Malmo, Sweden, to Wallenius Lines of Stockholm. With a capacity of 6,230 passenger cars and 540 heavy vehicles, the new ship has an overall length of 649.6 feet, beam of 105.9 feet, depth to weather deck of 103.35 feet, and scantling draft of 38.7 feet.
The main engine is the latest model low-speed Sulzer 7RTA68 diesel rated 18,100 bhp at 106 rpm, providing a service speed of 20 knots. Isolde is a unifuel ship, with the main and auxiliary engines burning the same heavy fuel oil of up to 600 cSt. Direct-reversing and driving a fixed Lips propeller, the main engine is remote-operated from the bridge or the engine control room. Machinery fulfills the UMS requirements of Lloyd's Register of Shipping for unattended engine room.
Electric power is provided by three 1,600-kw alternators driven by Wartsila-Vasa 6R32 diesel engines installed in a separate compartment.
Heavy vehicles are loaded on the 4th, 6th, and 9th decks, which are reinforced to carry heavy loads. The 5th, 7th, and 10th decks, and part of the 8th, are divided into hoistable sections that allow vehicle heights of up to 20.34 feet.
The 6th deck is normally the car entrance deck, but at higher berths the middle outside ramp may also be attached to the 7th deck. Two outside loading ramps are positioned at the starboard side; the aft one is rigged with a 25-degree aft angle to accommodate long vehicles.
Internal ramp systems between decks and to doors and openings in the transverse bulkheads make it possible to load/discharge the entire ship via only one of the outside ramps.
All navigation equipment is of the latest design. The Raytheon radar installation has an anti-collision computer with free choice of picture presentation and other features.
The Kockumation autopilot is of the totally adaptive, fuel-saving type with set-radius steering for turns. In addition to a Decca Navigator, a Magnavox satellite navigation system is installed.
The speed log equipment is duplicated, a Jungner pressure log for deep waters and a Krupp-Atlas doppler log for more restricted waters. Other equipment includes a Raytheon weather facsimile recorder, Simrad echo sounder, Plath magnetic compass and gyrocompass, and Ramanteen radio direction finder.
The Isolde operates with a crew of 23. Two 50-person Fiskars covered motor lifeboats and four 25-person Viking life rafts are provided.
JAPAN APRICOT Hitachi Zosen The 194,226-dwt bulk carrier Japan Apricot was completed at midyear by the Ariake Works of Hitachi Zosen and delivered to her owner, Japan Line, Ltd. Designed to carry iron ore and coal, the huge ship is operating mainly in transportation of iron ore between Australia and Europe, and from Brazil to Japan under contracts of affreightment with Hamersley Iron Pty. Ltd. and Sumitomo Metal Industries Ltd., respectively.
The Apricot has an overall length of about 984 feet, beam of 156 feet, depth of 82 feet, and maximum draft of 60.16 feet. Her main engine is a low-speed Hitachi/B&W 6L80MCE diesel with a maximum continuous output of 16,500 bhp at 83 rpm, providing a service speed of 13 knots.
A range of energy-saving factors and various devices allow the ship to operate with a crew of 28. Features to reduce fuel costs to the minimum include: the Hitachi-developed HN Nozzle to improve propulsion efficiency; the energy-saving main engine will be operated in a derated mode; turbogenerator and shaft generator; tower-shaped accommodations house to reduce wind resis- tance; adaptive autopilot system; and self-polishing antifouling on the hull exterior.
Cargo-handling and ship mooring operations, as well as machinery room equipment are highly automated to save labor needs. The machinery automation equipment qualifies the ship for the Nippon Kaiji Kyokai MOA notation for unmanned engine room.
2ND LT. JOHN P. BOBO Quincy Shipbuilding The first new-construction, purpose- designed Maritime Prepositioning Ship (MPS), the 2nd Lt.
John P. Bobo, was delivered by General Dynamics Quincy Shipbuilding Division early this year.
Named in honor of a U.S. Marine Corps Medal of Honor recipient, this vessel is the first of five ships designed and built by the Quincy shipyard for chartered service to the Military Sealift Command. The first three vessels were delivered this year; the next two are scheduled for 1986 delivery. All will be operated by American Overseas Marine Corporation, a General Dynamics subsidiary created for this and other marine endeavors.
The Maritime Prepositioning concept, which originated only within this decade, provides for highly mobile, forward location afloat storage of a mix of selected equipment and supplies for Marine-Air- Ground Task Forces. The Bobo and her sister ships are the only newconstruction vessels of the 13 ships that will provide for the requirements of three Marine brigades throughout the world.
The Bobo has an overall length of 671 feet, beam of 105 feet 6 inches, and depth to the main deck of 82 feet. Full-load draft is 29 feet 6 inches, with a corresponding deadweight of 22,700 long tons. Propulsion is by a pair of Stork-Werkspoor medium-speed 18TM410 diesels, each with an output of 13,200 bhp at 580 rpm. These drive a highly Jskewed fixed Ferguson propeller through double-input, single-output Lowmann & Stolterfoht reduction gears. The machinery space is rated + ACC by the American Bureau of Shipping, signifying one-man engine room attendance, monitored by a General Electric distributed microprocessor control panel.
The profile of the Bobo is distinct.
Due to the high volume and low density of her cargo, she resembles a modern pure car carrier in her very high main deck and squared off upper hull. The forward mooring deck is lowered 18 feet below the main deck, providing excellent visibility from the wheelhouse. Other features of the design are the large accommodation deckhouse and elevated aft helicopter platform.
This house provides living quarters and working areas for a total complement that can exceed 170 men during military operations.
The helicopter platform can accept the landing of the Marine Corps CH-53E helicopter. The 1,120-ton deckhouse was assembled and completely outfitted separately from the hull, and using the Quincy yard's immense Goliath crane, was erected on the hull in what is said to be the single heaviest lift in U.S. shipbuilding history.
The cargo being carried and stored on the MPS is diverse. The ship carries 1,400 vehicles stowed on seven decks across two midship holds; 530 twenty-foot containers in two forward holds and on the main deck; a combined cargo of about 1,600,000 gallons of gasoline, diesel, and jet fuel in deep double-bottom tanks; and a variety of lighters, landing craft, and heavy deck cranes.
Unlike commercial vehicle carriers, the MPS has a minimal amount of vehicle hold equipment.
MacGregor-Navire supplied a hinged, fully slewing stern ramp 110 feet long with a road width of 24 feet. This ramp was designed with the capacity for loading the heaviest Marine Corps tracked vehicles, and for launching amphibious craft while at anchor. Navire also supplied the 53-foot-wide, 15-foot-high stern door, and six watertight bulkhead vehicle doors, both overhead and side-hinged. All of the cargo doors are hydraulically operated by local controls with indication at the pilothouse damage control station.
There are two hoistable car ramps, and a hoistable ramp cover installed to provide access to the various levels of the holds.
The Bobo has proven to be a highly maneuverable vessel. Her short length, open stern, and lack of a bulbous bow allow her to respond rapidly to helm commands. The spade rubber is powered by a Frydenbo rotary vane steering gear. To assist with slow-speed maneuvering and mooring operations, General Dynamics chose the Omnithruster PV 1100 jet-type bow thruster powered by a Reliance Electric 1,000-hp motor operating at 500 rpm.
LEONARD J. COWLEY West Coast Manly The latest addition to the Canadi- an Department of Fisheries and Oceans fisheries patrol fleet, the 2,244-gt Leonard J. Cowley, is the largest and most sophisticated vessel of her type in Canada. Operating out of St. John's, Newfoundland, her major function is the surveillance of the offshore fishing fleet within the Canadian 200-mile exclusive fisheries zone as far north as 75 degrees latitude and within the Northwest Atlantic Fisheries Organization waters outside the zone.
This mission requires precise navigation, excellent boarding facilities, and superior communications as well as seakindliness in all kinds of weather, substantial capability in ice, and helicopter facilities. All of these requirements are fully met, and the vessel is also equipped for search and rescue operations.
Built by West Coast Manly Shipyards of Vancouver, B.C., a division of Rivtow Industries Limited, the ship has an overall length of about 236 feet, maximum beam of 46 feet, and mean draft of 14% feet. Propulsion is provided by two 12-cylinder Polar Nohab F312A diesels with total output of 4,184 bhp, driving a single controllable-pitch propeller.
The vessel is classed by Lloyd's Register of Shipping 100 Al, Ice Class 1, LMC. Machinery and electrical control and monitoring systems meet Lloyd's requirements for Unmanned Machinery Space.
Designed by Cleaver and Walkingshaw of Vancouver, the Cowley has numerous innovative features, representing state-of-the-art technology in navigation systems, communications, electrical monitoring and control, accommodations, helicopter facilities, maneuvering, wheelhouse design, and boarding facilities.
The unique wheelhouse is designed to maximize visibility in all directions. Shaped like a trapezoid with extended wings, it provides six distinct yet interdependent work stations.
Boarding facilities are provided to meet the principal mission of the ship—the boarding of offshore trawlers at sea in winds to Beaufort 7. Boarding craft are of the Watercraft RI-22 type, built by Crockett McConnell Inc. of Bridgewater, N.S., and are propelled by water jet drives powered by Ford Mermaid diesel engines. The port boat is launched by a Miranda davit, and the starboard craft by a HIAB 180 Seacrane.
MANITOU Lindenau The Paul Lindenau shipyard in Kiel, West Germany, in May this year delivered the energy-saving, IMO Type II oil/chemical tanker Manitou to Atlantic-Rhederei F. & W. Joch of Hamburg. This specialized tanker is the fourth of a series that Lindenau developed in collaboration with the owner.
Built for worldwide trading and classed by Germanischer Lloyd, the Manitou has an overall length of 380 feet, beam of 51.8 feet, depth to main deck of 30.5 feet, and draft on summer freeboard of 23.5 feet.
Main propulsion is provided by a Krupp MaK 6M551AK diesel engine with a maximum output of 3,500 bhp at 375 rpm. Service speed is 14 knots. A Schottel bow thruster is installed for enhanced maneuverability.
Electrical power is produced by three Volvo Penta/Siemens diesel- driven generator sets and by a Siemens shaft generator.
Due to the optimal lines of the hull and the patented Lindenau bulbous bow, 20 percent less propulsion power is required for this vessel compared with similar oil/chemical tankers with the same deadweight and draft.
The double hull construction enclosing the cargo tanks reduces the amount of energy needed to heat the cargo due to the isolated air layer.
Cargo piping and heating coils are of stainless steel. All cargo tanks are coated with Camrex Camcote epoxy.
Further advantages include the easy cleaning of the tanks and quicker unloading due to the slanted form of the tank bottoms.
Electronic equipment includes two Decca radars, Decca Navigator, Anschutz gyrocompass and gyropilot, Atlas echo sounder, Plath radio direction finder, and Debeg radio station.
The tanker has two oil-fired boilers and an exhaust-gas boiler that are used for preheating the heavy fuel oil, and heating water and accommodations.
Under favorable conditions (high outside temperature), part of the exhaust-heat energy can also be used to heat the cargo.
The Manitou is equipped with a free-fall lifeboat with a 26-person capacity. She is said to be the first oil/chemical tanker authorized to have such a lifeboat. Two inflatable life rafts are also provided, each with a capacity for 20 persons.
NOSAC TASCO Daewoo Shipbuilding The first RO/RO car carrier built by Daewoo Shipbuilding & Heavy Machinery Ltd. of South Korea, the Nosac Tasco, was delivered early this year to K/S Benargus, a subsidiary of Oivind Lorentzen Shipping of Norway. A sister ship, the Nosac Express, followed for Wilh Wilhelmsen; both companies are equal partners in the consortium Norwegian Specialized Auto Carriers (NOSAC), the operator of the new ships.
Each of the new car carriers has a capacity for 5,532 cars, and operates with a crew of only 13, a reflection of their high degree of automation.
The Nosac Tasco has an overall length of about 640 feet, beam of 105 feet, depth of 101.5 feet, and design draft of 27.9 feet. Propulsion is by a Hyundai/B&W 6L80GB lowspeed diesel engine having a maximum continuous rating of 19,250 bhp at 96.5 rpm and normal continuous rating of 17,320 bhp at 93.2 rpm, driving a Lips highly skewed, fixed-pitch propeller. Service speed is 19 knots.
Equipment necessary for remote control, automation, and monitoring/ alarm is installed so that 24- hour unattended machinery space operation can be achieved in normal seagoing conditions, earning the Det norske Veritas EO notation. While the engine room is arranged centrally at the after end of the ship, the cargo space above it has been optimized by placing the exhaust casing and funnel on the extreme starboard side.
Electric power is provided by three diesel gensets—two comprising Bergen KRG9 engines driving 1,205-kw Nebb alternators, and one with a Bergen KRG5 diesel and 670- kw Nebb alternator. While under way, a Siemens shaft generator installed in the intermediate shift produces 800-kw through a static frequency converter. An emergency 160-kw generator powered by a De troit Diesel engine is located on the upper deck.
The steam supply is produced by a Sunrod oil-fired boiler. While at sea with the main engine running at normal load, steam is generated by a Sunrod exhaust gas boiler. A Flakt Dirivent system provides for the effective ventilation of the engine room.
The Nosac Tasco has a total of 12 decks for car stowage. Decks 2, 4, 5, 7, 8, and 10 are liftable to accommodate a broad range of vehicle sizes.
In the case of decks 4, 5, 7, and 8, lifting is accomplished by means of hydraulic jigger cylinders manufactured by MacGregor Far East.
Decks 2 and 10, however, are lifted by specially built Nissho movable deck lifters.
Two MacGregor external ramps are fitted for roll-on/roll-off cargo loading and discharge, one approximately at midship and the other at the stern. Larger and heavier vehicles are loaded via the stern ramp, which is about 147 Vi feet long and 34V2/54 feet wide, and is canted 36 degrees to starboard of the ship's centerline. This ramp is designed to carry 112 tons. Its clear opening at the threshold is approximately 54 feet wide and 21V2 feet wide. The starboard ramp, normally called the side ramp, is fixed at 90 degrees to the ship's side; clear threshold opening is about 23 feet wide and 16 feet high.
ORANGE BLOSSOM Trosvik The specialty tanker Orange Blossom, said to be the world's first purpose-built ship for transportation of fruit juice concentrate in bulk, was delivered early this year by Trosvik Verksted A/S of Brevik, Norway, to Atlantic Reefer Corporation, which is under the general management of Atlanship S.A. of Switzerland.
The unique vessel was designed by Dwinger Marineconsult Inc. of Denmark; the firm also developed the hull lines, which have a very low resistance and thus will insure low fuel oil consumption. The Trosvik Group developed the detail drawings, and Dwinger carried out plan approval and construction supervision on behalf of the owner.
The Orange Blossom has an overall length of 475.7 feet, beam of 70.5 feet, depth to upper deck of 41.3 feet, and full-load draft of about 32 feet. She is able to carry 12,000 tons of juice concentrate in stainless steel tanks, cooled to below 32 F.
Propulsion is provided by a Japanese- built M.A.N.-B&W diesel engine with a maximum continuous output of 9,000 bhp at 111 rpm.
B&W Holeby in Denmark provided her three diesel alternators, and Sabroe of Aarhus, Denmark, delivered the refrigeration plant. Trosvik Industri A/S, a member of the Trosvik Group, supplied the steering gear.
The majority of other equipment and outfit is of Norwegian origin.
Crew accommodations include single cabins with private showers and toilets for a normal complement of 20, plus some spare cabins, as well as a spacious reception room with bar.
Classed by Lloyd's Register of Shipping, the Orange Blossom is fitted with comprehensive navigation equipment, automation systems, and remote controls.
PAUL BUCK Tampa Shipyards The 30,000-dwt motor vessel Paul Buck, first of five sophisticated T-5 product carriers designed and constructed by Tampa Shipyards Inc.
in Florida, has been delivered to Ocean Carriers, Inc. of Houston.
The new ship is now being operated by the owner's subsidiary, Ocean Product Tankers, Inc., under a charter to the Navy's Military Sealift Command.
The tanker has an overall length of 615 feet, beam of 90 feet, depth of 53 feet 8 inches, and design draft of 34 feet. She is powered by a slowspeed Sulzer 5RTA76 fuel-efficient diesel engine, which also drives an attached shaft generator to provide electric power while the ship is underway.
The combination of these two characteristics provides the owner with excellent operating economy.
The propulsion plant is designed for unmanned operation, and is classed +AMS by the American Bureau of Shipping. The engine is direct drive via a solid shaft to a fixed 4-bladed, nickel-aluminumbronze propeller manufactured by Ferguson. The Sulzer 5RTA76, with a maximum continuous rating of 18,400 bhp at 98 rpm, has been derated to prolong its service life, and is especially adapted to drive a shaft generator through a speed-increasing gearbox.
The Paul Buck is designed to deliver 30,000 long tons of petroleum products worldwide, and is icestrengthened for Arctic or Antarctic operations. Cargo is carried in seven pairs of tanks, each pair being segregated from any other pair to allow seven different liquid cargoes to be carried. Each tank is fitted with a stainless steel, high-pressure hydraulic cargo pump supplied by Framo.
The pumps are sized to discharge the entire cargo within 16 hours, and in service have achieved this easily. All cargo tanks are fully inerted by an inert gas generator.
This inert gas system is designed to supply two pairs of tanks through dedicated systems to guard against cargo contamination; the remaining five pairs are served by a common system. Cargo piping and inert gas piping are constructed entirely of stainless steel. Facilities for underway replenishment at sea are provided from two stations; refueling at sea capability over the stern is also incorporated.
The unique construction of the cargo tanks developed by Tampa Shipyards has substantially reduced surface area compared with conventional construction. This results in significant cost reduction in epoxy coating maintenance inside the cargo tanks.
Water ballast is carried in double bottom and wing tanks, totally segregated from the cargo, and is arranged to qualify for "Protectively Located Segregated Ballast" under IMO regulations.
The entire hull, except foundations and superstructure, is constructed of AH36 high-strength steel, realizing a 15-percent saving in total steel weight over Grade A steel, and is designed for a scantling draft of 36 feet. This allows the owner the flexibility of deeper drafts.
Extensive vibration analyses were confirmed by instrumenting the ship during sea trials and conducting a comprehensive vibration survey.
Noise predictions were also made and confirmed to be acceptable by survey during sea trials.
This survey, combined with the vibration characteristics, results in a comfortable living atmosphere for the operating crew.
PROBO BIAKH Hyundai The 36,500-dwt Probo Biakh, a highly advanced and sophisticated product/bulk/oil carrier, was delivered at midyear by the Hyundai Shipyard in Ulsan, South Korea. A sister ship, the Probo Brali, was also delivered this year, and a third, the Probo Britt, is scheduled for January 1986. Owner of the ships is L.
Gill-Johannessen, a member of the Norwegian Bulkhandling Group.
These PROBO vessels have been cited by the Norwegian Shipping Association as "Examples of Norwegian Ships of the Future." The Probo Biakh has an overall length of 597 feet, beam of 104.8 feet, depth of 59 feet, and summer draft of 43 feet. Propulsion is provided by a slow-speed Hyundai/ B&W 4L80MCE diesel engine with a maximum continuous rating of 12,800 bhp at 83 rpm; normal continuous rating is 10,800 bhp at 79 rpm, providing a service speed of about 15.3 knots.
The new ship was designed as a specialized oil products and bulk carrier, and is equipped to carry both clean and dirty oils, including crude, as well as dry bulk cargoes such as ore, coal, alumina, cement, and grain, and any quantity of caustic soda solutions up to her deadweight capacity. In addition, she is self-loading and self-discharging, with two traveling gantry cranes de- signed for continuous operation under tropical conditions and dusty environments.
Internal cargo surfaces and hatch covers are coated with pure epoxy paint down to the double bottoms for compatability with a wide range of oil products. For each tank there is one hydraulically driven, submerged cargo pump located in the cofferdam between the tanks. All cargo pumps are remote-controlled from the cargo control room. Tanks and piping are designed for seven grades of cargo. Efficient cleaning equipment insures thorough cleaning of the tanks, with two permanent, high-pressure cleaning guns in each tank.
The integrated Valmet automation system installed in the Probo Biakh is of a star configuration, where the several dedicated systems are connected to the various processes such as navigation, main and auxiliary machinery, cargo plants, and communications. The hose computer acts as a data collector, central mass storage, and central information and reporting system.
All control and monitoring systems operate as individual systems independent of the host computer.
One of the main aims of the onboard system is to centralize the various controls so as to have control from any one center at any given time.
The engine control system is designed to be operated from three individual control centers: the mas- ter station in the engine control room, and slave stations in the cargo control room and the wheelhouse.
Any monitored or controlled point may be displayed and controlled from any station, either by individual group displays or by process mimics.
SVEA Wartsila The 33,830-gt passenger cruise ferry Svea was delivered this year by the Helsinki Shipyard of Wartsila Oy to Oy Svea Line (Finland) AB.
The new vessel has an overall length of 551 feet, beam of 90.5 feet, and draft of 20.7 feet. Propulsion is provided by four Wartsila/Pielstick 12PC2-6V medium-speed diesel engines, each developing 8,975 bhp.
Service speed is 22 knots.
The interiors of the Svea reflect the high standard set by the Finlandia Class built in 1981 for the Helsinki- Stockholm route. Passenger accommodations comprise 566 cabins with a capacity of 1,625 persons.
All cabins have individual climate control, temperature alarms, and shower/toilet facilities.
As the ferry will spend only about one hour in port, special attention has been paid to reducing the time required for loading and unloading the car decks, handling the provisions and stores, and discharging waste ashore. Vehicle capacity is 530 motor cars or, as an alternative, 60 long-distance trucks and 40 cars.
Careful consideration was also given to the special requirements posed by the part of the route that goes through the sensitive archipelage environment. These needs are mainly related to maneuverability and the minimization of wave generation.
The high total engine output of 17,950 bhp makes it possible to reduce speed in the archipelage, as the time lost can be made up on the open sea. The vessel complies with all the relevant environmental protection rules.
All restaurants are located on Deck 7; passengers can choose between cafeteria, a la carte, smorgasbord, or gourmet-style service. Bars and tax-free shops are situated on Deck 8, which also has a conference center with a capacity of more than 400 persons.
Navigational equipment includes two gyrocompasses and repeaters, a magnetic compass, autopilot, echo sounder, draft indicator, wind meter, two speed logs, radio direction finder, Decca Navigator, and weather chart facsimile receiver. Comprehensive radar equipment comprises four radars, including an ARPA unit.
The Svea is registered in Sweden and built according to the Swedish requirements for passenger vessels.
She is designed to comply with the rules of Det norske Veritas, with the classification +1A1, Carry Ferry A, EO, Finnish/Swedish Ice Class Rules 1971, 1A Super, and also fulfills the regulations of SOLAS 1974.
The extent of the remote control and monitoring systems exceeds the DnV rules for unmanned machinery spaces.
Read OUTSTANDING OCEANGOING SHIPS OF 1985 in Pdf, Flash or Html5 edition of December 1985 Maritime Reporter
Other stories from December 1985 issue
Content
- United States Cruises Applies To M a r A d For $150-Million Title XI page: 4
- PA Series Heavy Fuel Diesel Now Available From Fairbanks Morse page: 6
- Six-Page Color Brochure On Energol Lubricants Offered Free By BP Marine page: 6
- Getty Fleet Orders Lips Speed-Adapted Propellers To Increase Efficiency page: 6
- Karl Senner Offers Free Color Brochure On Reintjes Marine Gearboxes page: 6
- OMSA Elects New Officers —Congressman Warns Of California Plan' page: 8
- Birka Line Cruise Ship Launched At Valmet's Helsinki Shipyard page: 8
- Fire Combat, Inc. Offers 10-Page Manual On Fire Suppression Systems page: 9
- Texaco Appoints Quegan General Manager, Marine Department page: 10
- Fernstrom Elected President And CEO Of American Ship Building page: 10
- New Briefcase Computer For Marine Industry From NAV-COM page: 12
- Furuno USA Introduces New Doppler Speed Log And ARPA Line page: 12
- W. Anthony Watt Heads Sales And Marketing Division At Moran Towing page: 14
- Marinette Delivers First Of Ten Torpedo Weapons Retrievers page: 14
- Bassett Named President Of Interocean Management page: 14
- Kockums To Build Ferry With First Coal-Fired Marine Steam Engines In 30 Years page: 16
- COSCO And McMullen Form New Company— COSCO North America page: 17
- Cunard Gives $115-Million Contract To Lloyd Werft To Convert QE2 To Diesel And Alter Accommodations page: 17
- Harnischfeger To Build World's Largest Dipper/Clamshell Dredge page: 18
- Bethlehem Steel Dedicates Its New Sabine Yard In Port Arthur, Texas page: 18
- Totem To Acquire Controlling Interest In Interocean Steamship Corp. page: 20
- OUTSTANDING OCEANGOING SHIPS OF 1985 page: 22
- NOTABLE CONVERSIONS OF 1985 page: 44
- Bender Shipbuilding Wins $4.5 Million In Contracts page: 49
- Construction of 'Theodore Roosevelt' Ahead Of Schedule And Under Budget page: 50
- Magnavox Introduces New Generation SatCom And New GPS/Transit SatNav Receivers page: 51
- GPS/Transit SatNav Receivers page: 52
- Network 90, Integrated Marine Management System For Reduced Costs And Maximized Profits page: 55
- SHIPBOARD COMPUTER SURVEY page: 58
- Ellicott Machine Corporation Announces Personnel Changes page: 68
- Vapor Corporation Announces New Sphere Matrix Technology page: 68
- U.S. NAVY SHIP PROCUREMENT Second Quarterly Update—November 1985 page: 70
- MSI Conducting Tests For Proposed Canadian Ferry With Voith Schneider Propulsion page: 77
- Design Improvements In EMD's 645FB Diesel Provide Higher Horsepower, Better Fuel Economy page: 78
- Perko Presents The 200 Series International Navigation Lights page: 81
- Coast Guard Completes Installation Of Advanced Navigational Aid In N.Y. Harbor page: 85
- Macmeter Offers Metering Protection page: 91
- MARDATA Named North American Agent For Lloyd's Information Services page: 91