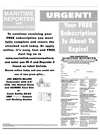
Advantage of Marine Guard Foam Filled Marine Fenders
Special Advertising Section Urethane Products Corporation's Marine G u a r d™ Foam Filled Marine Fender offers many significant advantages over Hard Rubber and other types of fenders. Foam filled marine fenders are fabricated from a closed-cell resilient foam that absorbs significant quantities of energy when compressed. The foam is protected by thick, filament-reinforced outer elastomer skin. This construction offers a number of important features and advantages.
High Energy Absorption With Low Reaction Force Marine Guard Foam Filled Fenders have both highenergy absorption and low reaction force. Reaction forces at rated compressions are lower than most other fenders at comparable energy levels. The low reaction force of the foam filled fender is an important consideration in the design of piers and quay walls, where significant economies are produced by eliminating the need for load-spreading panels, which are required for most large hard rubber fenders.
Foam filled fenders dissipate a significant portion of energy internally and do not cause the vessel to rebound from the berth as readily as pneumatic or hard rubber fend- Tough Outer Skin Foam filled fenders have a rugged polyurethane elastomer outer skin, with nothing o snag hull protrusions or dock fittings. To provide added strength, the thick skin is reinforced with nylon filaments. Independent tests have shown that this gives the outer skin of the fender a rear strength improvement of 4 to 6 times than that of an equivalent thickness of unreinforced skin. Other types offenders with a layered construction are subject to delamination between the layers of fabric reinforcing and rubber membrane. T he urethane elastomer skin is far more resistant to the degrading effects of oil, chemicals, ozone and UV radiation than is the vulcanized rubber used in other types of fenders.
Urethane is also very abrasion resistant. Formulated specifically for marine fenders, the outer fender skin undergoes strict quality control at the manufacturing plant.
Custom Size and Colors In addition to traditional fender sizes, foam fender manufacturing processes allows the fenders to be designed and supplied in custom sizes, capacities, configurations and col- Laboratory and Field Tests Marine G u a r d™ Foam Filled Fenders have been extensively tested to verify their performance, ruggedness and durability. Compression tests are conducted in a certified laboratory using one of the world's largest compression testing machines. These fenders consistently excel in all other required tests, including energy absorption; capacity and reaction forces; ultimate compression; cyclic compression (dynamic and sustained loading); transverse pull tests; and longitudinal pull tests. Years of field operation with foam filled fenders have confirmed the ability of these fenders to take the rugged service for which they are designed.
Quality Materials testing, verification and inspection are in accordance with the standards and practices of: • ASTM (American Society for Testing and Materials) • ISO (International Organization for Standardization) • AWS (American Welding Society) • AISC (American Institute of Steel Construction) • SSPC (Steel Structures Painting Council) Statistical quality techniques include statistical process control and sampling plans. Quality systems have been audited and approved by the many organizations, including: • ABS (American Bureau of Shipping) - system and type approvals • DCMC (Defense Contract Management Command) • DGSC (Defense General Supply Center) • ISO (International Organization for Standardization Simple Installation Installation of Marine Guard^1*^ Foam Filled Fenders is simple compared to hard rubber fenders, which require specialized mounting fixtures. The fenders use standard chain pendants attached at each end of the fender. Loadspreading panels between the ship and the fender are not required. Fender transportation using standard rigging methods is easily accomplished.
Total Buoyancy The natural buoyancy of foam filled fenders also allows them to be installed in a floating position between a ship and dock or another vessel. This is particularly beneficial in areas with large tidal or seasonal water level fluctuations since, unlike fixed fendering, the floating fender can rise and fall with changing water levels. The floating fender remains at the water line of the vessel for optimum fendering.
Burst Resistance When a Marine Guard ' ^ Foam Filled Fender is compressed, the compression force is resisted by the pressurization of many small, completely closed foam cells and by the buckling of the cell walls, the resistance to cell bursting is very high. The fender skin is not a pressure containment boundary; therefore, there is no need for pressure relief valves or inflation valves on the outer cover.
Safety Because of the foam filled fender's unique design, it will not explode or sink. It retains its energy absorbing and standoff capabilities even if the skin is damaged. This extra margin of safety can be vitally important in docking, marine salvage, offshore construction or ship-to-ship transfer operations.
Low Maintenance The foam filled fender has been designed to resist environmental conditions. The exterior is highly resistant to ozone, hydrocarbons, ultraviolet radiation, sweater and other environmental factors, and the skin color is integrated into the elastomer.
Reliable Performance All of the above factors combine to eliminate many of the post purchase maintenance and potential replacement costs of other fenders. Years of successful performance in the field have established the foam filled fender as the standard tendering solution for the industry.
Tel: (562) 6 3 0 - 4 9 82 Fax: (562) 6 3 0 - 6 9 74 www.urethaneproducts.com e-mail: [email protected] Circle 2 6 0 on Reader Service Card
Read Advantage of Marine Guard Foam Filled Marine Fenders in Pdf, Flash or Html5 edition of February 2004 Maritime Reporter
Other stories from February 2004 issue
Content
- Northrop Grumman Delivers Aegis Destroyer page: 3
- Izar Gijon Delivers Two Massive Dredgers page: 10
- Boeing Connexion Moves to the High Seas page: 10
- New Ferries for Hawaii? page: 11
- Damen Delivers First-of-Class ASD Tug page: 12
- OMI Pleads Guilty to Illegal Dump, To Pay $4.2M Fine page: 14
- Teekay Orders Aframax Tankers page: 15
- Wartsila to Discontinue Production in Turku page: 15
- China Preps To Take World Lead page: 16
- Secondhand Prices Tanker Prices Up 35% page: 16
- Continuous Synopsis Record page: 18
- A 3D Virtual Interface to Access Ship Data page: 20
- MAN B&W Debuts ME-GI Dual Fuel Engine page: 21
- Rebuilding Single Hull Tankers to Double Hull Tankers page: 22
- Thor-Lube Stern Tube Bearing System on Shell LNG Carrier page: 24
- K-Sea Acquires Integrated Tug Barge Unit page: 25
- Boosting Deepsea RoRo Capacity page: 25
- MTS Rosette: State of the Art Inland Tank Ship page: 26
- Fourth New ATB Tank Vessel for MTC page: 30
- Company Focus: Staying Connected with INTERCON page: 31
- Innovative Coastal Trader page: 32
- Halifax Shipyard On Hand To Replace Lost Rudder page: 33
- East Isle Shipyard Wins $16M Contract page: 34
- Transport Canada Takes Lead on Safety page: 35
- Hike Metal: Steady Progress to Success page: 36
- Car Ferry Saves Fuel with New Engines page: 37
- The ISPS Code page: 38
- Temporary Hull Repair on FPSO Stands the Test page: 39
- New 12,000-sq.-m. Workshop Pays Dividends page: 41
- Series Design in the New Regs Environment page: 42
- Aluminum Boats Prove Their Mettle page: 44
- Success Aboard QM2 page: 49
- LCD's Turning Black page: 50
- The Needs of Maritime Electronic Equipment page: 51
- Advantage of Marine Guard Foam Filled Marine Fenders page: 52