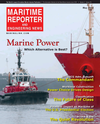
Meet the Future Surveyor
By Greg Trauthwein
Knut Ørbeck-Nilssen, CEO Maritime, DNV GL discusses the future of class
DNV GL is now integrated and fully armed to address the challenges of the day. Drones for tank inspections? Virtual surveyors? Unmanned ships?
DNV GL leaves no stone unturned in the quest to bring class into the future as Knut Ørbeck-Nilssen, CEO, DNV GL – Maritime, explained to MR in March.
Among classification societies DNV GL seemingly perpetually pushes the edge of innovation, with a combined Norwegian and German pedigree and a cumulative maritime experience more than three centuries. It was a little more than three years ago when it was announced that classification societies DNV and GL would merge into one, and according to Knut Ørbeck-Nilssen, CEO, DNV GL – Maritime that process is, for all intents and purposes, completed. With that box ticked, Ørbeck-Nilssen and crew now turn attention to battening down the proverbial hatches and riding out the current market slowdown, all the while planning for and investing in a future that may not provide growth anytime soon.
“Many of the markets are quite depressed at the moment, so we, having merged two and a half years ago, are in a really good position now,” said Ørbeck-Nilssen. “In 2013 we had already started to enjoy the synergies of the connection and to take out costs. So we have now created an excellent platform to deliver in challenging markets.”
In counting his classification blessings, Ørbeck-Nilssen contends that DNV GL has:
•The widest distribution of offices serving the maritime industry
•A streamlined organization with many of the double functions (of the two organizations) removed, allowing it to reduce its cost base significantly.
•A scale and set-up that is ideal for the coming 5 years.
DATE Night
While DNV GL talks up the role of emerging technologies as well as anyone, Ørbeck-Nilssen contends that his team’s mission is simple and focused: to be very close to the maritime industry and to the customers as a class society, providing excellent services on safety and quality.
In fact the merger process truly allowed management to strip down to the bare essence of class, effectively keeping the good and jettisoning the bad. “We reached out to the major stakeholders to strategically position the rule set … 2,000 comments from more than 800 stakeholders led to 700 rule modifications,” said Ørbeck-Nilssen “That’s the way we like to work, to really engage the industry, getting better proposals in hands.”
While the merger process resulted in a number of enhancements across the organization, Ørbeck-Nilssen is most keen to discuss DATE, which means Direct Access to Technical Experts.
“Speed matters a lot in the maritime industry, and to be able to respond fast to our customer’s requests is a top priority,” said Ørbeck-Nilssen. “We have set up a system called DATE (Direct Access to Technical Experts). This is five centers that we maintain in different time zones around the world, staffed by technical experts dealing with requests from customers 24/7/365.”
The goal is seamless global coverage established to answer customer’s questions quickly and effectively courtesy of five hubs situated in Singapore, Houston, Piraeus, Hamburg and Oslo. Take for example a request coming into Hamburg at 8 p.m. Friday evening. If Hamburg is unable to resolve the matter, the problem will be shifted to Houston for resolution, who works with the customer directly.
“With this, we are delivering a response in less than 6 hours on more than 75% of the cases,” said Ørbeck-Nilssen. “I think that this is really leading in the industry, and there is no added cost to the customer.”
The key to DATE’s success is not simply bolting on staff, rather deploying existing staff and knowledge more intelligently. “We had all of the experts onboard, it was more about how we move these experts – not physically but virtually moved – closer to the action and the customers,” said Ørbeck-Nilssen. “For us, taking class to the next step is really about being data smart, and how we can utilize digitalization in the effort.”
More Tech Tools
As the shipping and shipbuilding world evolve, so too does class. DNV GL in particular is keen to invest in technologies that it views as not simply cheaper, rather more efficient and effective too. To that end it offers:
ECO Insight
“We developed a product that we feel is at the vanguard of digitalization in ECO Insight,” said Ørbeck-Nilssen. “ECO Insight is designed to help owners and operators optimize vessel performance.” For example, fuel cost continues to be a large area of focus, and even though the cost of fuel has come down, it still represents a significant cost for the ship owner. According to DNV GL, ECO Insight offers a better way of benchmarking their operations, not simply vessel to vessel, but vessel to fleet, and ultimately vessel to world fleet. “ECO Insight is a unique product in the way in which it combines all of the data that DNV GL has on the vessels, and combines with the AIS system so that we at any one point in time know where the vessel is, where it is going, and we can combine with fuel and weather data,” said Ørbeck-Nilssen. “We can combine various data streams to determine how the vessel is doing, how well the fleet is doing. I think we will see much more of this in the future; the way in which you can combine different data streams.”
Drones
DNV GL is eagerly exploring the use of drones in its work, with the aim of increasing quality while reducing risk during the survey process. “We need to look at new technologies to see how we can use them to modernize the way we work, how we interact with our customers,” said Ørbeck-Nilssen. “If you are inside of a tank, you can fly that drone, outfitted with a flash and a video camera. You can fly it all the way up to the underside of the deck and you can get a very clear close visual inspection to check corrosion, cracks and to see if there is a need for closer inspection. By doing this, you save much effort and the need for scaffolding. The next step in this development is to see how you can make the drone system explosion proof. If you are able to put a drone in that situation where it is guaranteed not to produce any sparks, you don’t even have to gas free the hold, saving cost and time for the operator.”
Virtual Surveyor
“We are open to look to other industries for inspiration and ideas, and to that end we have had for a couple of years an interesting project with the German Aeronautical Institute, looking at ways to see how can we put a camera on our surveyors helmet, to digitize the results of the inspections,” said Ørbeck-Nilssen. This is not simply a system to take photos, rather a complete video imaging set up including measurements on photos so that it is provided to scale. Once captured, the photos are immediately correlated to the exact place on the vessel courtesy of the electronic drawing or 3D model, allowing the next inspector to see the past inspection trends. In short the system will create a digital model where the vessel is represented virtually with data and images added from inspections. The system is in its development phase through 2016. For the ship owner it provides readily available data that can be streamlined immediately to its headquarters, allowing them to engage not only with the crew onboard, but the company experts at the home office. “You get a much more interactive dialogue, rather than post-inspection back and forth. You really integrate, and it brings us much closer to the customer,” said Ørbeck-Nilssen. “If you project this a little bit further into the future, you can ask: who is carrying the helmet, who is flying the drone? It could be a surveyor, it could be the crew. This has the possibility to really take the business of surveying to the next step, giving us a virtual presence onboard the ship versus having a surveyor onboard as often as today. Naturally we would like to be onboard at certain intervals, but if some of the physical presence of today can be replaced by virtual presence, it could create some really interesting opportunities.”
Data Smart
When talk inevitably turns to ‘Big Data,’ Ørbeck-Nilssen contends that there is a lot of fluff in the industry conversation, and he thinks discussions should center on practical application of data to shipping operations.
“For DNV GL it is really important to try and make this as concrete as possible,” said Ørbeck-Nilssen. “As an example, we were really fortunate to get six months of operating history from an advanced vessel from a ship owner, a vessel with about 10,000 sensors.”
DNV GL had a pair of its data scientists examine the data, extracting some useful information. “As engineers we are always preoccupied with understanding ‘why’, so if this breaks down, why is it happening,” said Ørbeck-Nilssen. In examining the data it was found that one critical piece of equipment consistently had an increasing the temperature pattern throughout the six months trial, meaning the friction was also rising. If it had gone unnoticed long term, it would have resulted in a breakdown or an early maintenance event. In examining the data, the heat spike was correlated to a specific crew, and by talking to the crew members, they could release the torque a bit, the friction and temperature came down, and the equipment was saved from failure or early maintenance. But Ørbeck-Nilssen admits that change does not come quickly or easily.
“These things come with investment,” said Ørbeck-Nilssen. “You need sensors on the ship, you need to access, store and analyze the data. I think really it’s about demonstrating how this can be useful to save costs, increase efficiency or increase safety.”
(As published in the May 2016 edition of Maritime Reporter & Engineering News)
Read Meet the Future Surveyor in Pdf, Flash or Html5 edition of May 2016 Maritime Reporter
Other stories from May 2016 issue
Content
- Automated Skill Erosion page: 20
- ECDIS: The Quiet Revolution in Maritime Navigation page: 24
- Navico Makes its Commercial Push page: 26
- Fujiwara Takes the Helm at ClassNK page: 30
- ABS: Sharpening its Global View page: 34
- Meet the Future Surveyor page: 38
- Tech & Design Solutions for Modern Workboats page: 50
- Can Shipping Help Greece Ride out the Storm? page: 60
- Maritime Turkey Set for a Tailwind page: 62