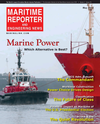
Tech & Design Solutions for Modern Workboats
By Kathy A. Smith
EPA Tier 4 regulations (for engines of 804 hp and higher) and propulsion advancements have many manufacturers and vessel designers changing course to adapt to new requirements and customer demands.
Jensen Maritime is designing a new 110-ft. harbor class ship assist docking tug with 6,770 horsepower. “It’s a little larger than most. The extra length allows for towing which is secondary use,” says Vice President Johan Sperling. “There will be Tier 4 equipment in it. It’s new territory and we believe this will become the minimum size vessel that you’ll see on the West Coast going forward.”
Bryan Nichols, Director of Jensen’s business development, observes that Jensen’s customers want to map out multipurpose vessels they can build and still operate within the ship assist and escort sector. “A single tug can be more efficient,” he says. “We’ve maximized this vessel under the rules so it can be operated efficiently under the 500 ITC regulations.”
Robert Allan Limited’s (RAL) President Mike Fitzpatrick reports RAL has been working with most of the engine manufacturers and owners in the U.S. to make sure that tugs they’re going to build for next year will be capable of taking the extra equipment on board. “It’s causing us a few redesign efforts but for most of our tugs, it’s not a major problem,” he says. “There is a cost implication for owners to comply with IMO Tier 3 and EPA Tier 4 requirements, which is causing an increase in engine prices of about 30 percent regarding Tier 4, which probably results in a five percent increase in total construction costs for U.S.-built tugs. In some countries such as Asia, with low labor costs, total costs can increase by 10 percent.”
Jensen designed two Tier 4 multipurpose tugs currently under construction for New York-headquartered McAllister Towing. The two 100-foot-long, 40-foot-wide escort vessels, each with 6,770-horsepower, are powered by 3516E Tier 4 Caterpillar engines and Schottel SRP4000FP Z-drive propulsion units. They are scheduled for delivery in 2017. The Brian A. McAllister and the Rosemary McAllister will be the first in the fleet to utilize high-efficiency catalytic after-treatment technology to reduce emissions and will have an approximate bollard pull of 90 short tons.
While Tier 4 is a current hot topic, LNG is still in the offing despite slumping oil prices. “We have different LNG harbor tugs and various other designs ready to go for customers who don’t want to live with Tier 4 requirements,” says Sperling, who notes Jensen’s parent company Crowley has spent a considerable amount of investment in LNG.
RAL’s Fitzpatrick explains, “The average cost differential to build a small tug with LNG burning fuel capability might be as high as 40 percent.” For the most part, he says, the market is still looking at hybrid options. “Even there it’s hard to build an economic case for hybrids. Tugs operate at lower power, so they don’t burn a lot of fuel. The cost differential of a hybrid tug might be $2 million, and at current fuel prices, it takes a long time to pay that back.”
Seattle-based Elliott Bay Design Group, recently designed a new 95-ft tug built this year for a Harley Marine ATB configuration with Tier 3 engines, but John Waterhouse, Chief Concept Engineer, says it’s the first tug the company has designed in several years. On Tier 4, he says, “We adapt designs to suit these extra pieces of equipment that are now being added to some vessels, however some projects we have are below the displacement range requirements for Tier 4.” He also expects to see more reinvestment in equipment for the North Pacific fishing vessel fleet, which may come about as it did in the 1980 when several offshore supply boats were repurposed for commercial fishing.
Interest in hybrid solutions for advanced commercial fishing vessels is on the rise, notes Knut E. Røsvik, Senior Vice President Propulsion, Product Management, Rolls-Royce Marine AS. “I expect this trend of electrification we see in commercial and offshore vessels will also be a direction for other kinds of workboats as well,” he says.
Recently, one of the first BG33-45 Bergen B series low sulphur-burning diesel engine was installed on a 79 m factory shrimp stern trawler of Rolls-Royce NVC 374 design for a Canadian shipowner that is expected to be delivered from VARD’s Aukra yard in Norway in December 2016. The new engine, launched in 2015, offers a 20 percent increase in power per cylinder, over the current Rolls-Royce Bergen B-series engines, which allows the power demand to be met with fewer cylinders.
The advanced technology also includes Rolls-Royce’s Promas integrated propeller rudder system, which provides increased propulsion efficiency for both single screw and twin screw configurations helping to reduce fuel consumption in both towing and transit conditions. Additionally, a power electric system with a hybrid shaft generator is also part of the propulsion package. “We have spent a lot of Research and Development investment in developing this leading edge system, analyzing the design through CFD and other techniques to refine it,” says Røsvik.
When asked what is coming for workboat propulsion solutions and how much more can be tweaked to match what’s expected in the future, he says, “We tend to think what we have today has achieved what is possible to achieve. But every time we expend the effort to use our best engineers who are developing new tools and techniques, we find there is more to gain.”
Lifecycle costs are also a pressing issue for vessel owners, according to Røsvik. “I think one of the enablers that can make a difference is equipment monitoring systems,” he says. “Our customers want to increase the service intervals on our equipment from what is currently three to five years to 10-year intervals. A trend we see increasing is to be able to do condition-based overhauls of the equipment. Instead of doing it at a five-year interval, the overhaul is done when the condition monitoring system tells you it’s time to do it.”
The use of Z-drive technology in the North American inland river market is becoming the norm, thanks to propulsion supplier ZF Marine Propulsion Systems Miramar, LLC (ZF). The Florida-based company, representing the marine components division of the Germany-headquartered ZF Group, has been helping owners change the design of their fleets and modernize the propulsion systems they’ve been using for 60 years.
“Our thruster technology allows customers to look at using smaller engines but gain better performance than some of their older vessels so they can reduce fuel burn,” says Edward Schwarz, Industrial Technology, Business Unit Marine Propulsion Systems, Business Development Manager. ZF also provides parts commonality across propulsion platforms in order to help fleets reduce parts inventory.
With a variety of innovative products such as transmissions, control systems, thrusters and propellers, and offices worldwide, ZF is a significant player in the commercial market. While the name of the game is to help vessel owners improve fuel economy and efficiency by optimizing drive systems for workboats, Schwarz says increasing vessel safety is also critical. “As contracts get more competitive as more requirements come in, everyone is looking to run their vessels as safely as possible, so we’re always looking at areas where we can improve safety. We’ve provided thrusters for over 40 new vessels in a little over three years. This technology is helping make our customer’s vessels safer and brings modern engineering to their systems.”
On another safety note, RAL’s Fitzpatrick says the new Maritime Labor Convention regulations for crew accommodation is causing most tugs to get bigger. “Tugs have become shorter and wider to accommodate that, but we’re now putting 80 ton bollard pull in a 25-meter tug that a few years ago would have been maxed out at 60 tons. The class regulations and international stability regulations still have to catch up. It’s something we’re pushing the class societies to recognize.”
He also remarks that RAL is seeing a growing trend toward tugs that are tailored for each specific operation, though it is different in different parts of the world. For now, designs that meet Tier 4 requirements are a challenge, particularly on vessels that are tightened up against tonnage limits. “We build a lot of tugs that are 499GRT internationally, and any change to those is always an issue,” he says.
“If we need to add some volume into the engine room, we need to take it away somewhere else.”
(As published in the May 2016 edition of Maritime Reporter & Engineering News)
Read Tech & Design Solutions for Modern Workboats in Pdf, Flash or Html5 edition of May 2016 Maritime Reporter
Other stories from May 2016 issue
Content
- Automated Skill Erosion page: 20
- ECDIS: The Quiet Revolution in Maritime Navigation page: 24
- Navico Makes its Commercial Push page: 26
- Fujiwara Takes the Helm at ClassNK page: 30
- ABS: Sharpening its Global View page: 34
- Meet the Future Surveyor page: 38
- Tech & Design Solutions for Modern Workboats page: 50
- Can Shipping Help Greece Ride out the Storm? page: 60
- Maritime Turkey Set for a Tailwind page: 62