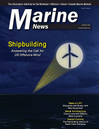
David Clark Company: An American Success Story
David Clark Company is best known within the marine market for its wireless and digital headset workboat crew communication systems – the Series 9900 Wireless Marine Headset System and the Series 9100 Digital Marine Headset System. The company has over 20 years of experience designing and manufacturing boat crew communication solutions for a variety of workboats, e.g., patrol boats, fire/rescue craft, and offshore service vessels.
But you may not know that David Clark Company started out as a knitting factory for making men’s and women’s specialty garments and evolved into a leading provider of critical communication solutions for high-noise environments and leading-edge aerospace crew protective equipment. Here’s how it happened.
So, who was David Clark?
How does a small garment knitting company in Worcester, Mass., end up becoming an iconic brand and indelible part of aviation and aerospace history? The answer is largely due to one man. A man who left school to go to work at the age of fifteen. A man who earned no diplomas after grammar school. A man who, unlike some titans of business today, shunned the spotlight and desired to stand in the shadow of his accomplishments, preferring to bestow credit upon those that “did the real work.” That man? David Myron Clark.
David Clark, founder of David Clark Company, Worcester, Mass. (Photo: David Clark Company)
David Clark Company was incorporated in Massachusetts in 1935 after developing a new concept of knitting two-way stretch fabric for men’s and women’s specialty undergarments. The knitted blanks were sold to corset manufacturers for sewing, finishing and resale. Despite being short of cash and having the top of its building blown off by a hurricane in 1938, the company persevered. In time, a total of six patents for knitting were applied for and granted. In 1939, David Clark Company developed and patented a unique supporting undergarment for men called “The Straightaway” (essentially a compression garment for men) which sold in stores in New York and New England, and via direct mail.
“G”-forces and the partial pressure suit
With America’s involvement in World War II seeming inevitable, David Clark, working through business associates in Washington, D.C., approached the War department to consider prototype garments which he had recently developed to address “the dreaded blackout”, or G-induced loss of consciousness among fighter pilots. It was through his contacts at the War Department that he was introduced to E.J. Baldes, head of the department of Biophysics at the Mayo Clinic, in November of 1941. The two men would become lifelong friends. David Clark recalls in his memoir, The Development of the Partial Pressure Suit, “We each had similar and great interests in aviation; I’d not worked at it at all, but he had worked with Drs. Boothby, Lovelace and Bulbullian – all at the forefront of aviation medical research – in the development of improved methods for supplying pilots with oxygen to breathe so that they might fly at higher altitudes. I presumed that I might be able to help develop some sort of protection from the ‘Dreaded Blackout’ experienced by pilots of high-performance aircraft when conducting high speed maneuvers in flight. I believed that I should offer my services and facilities to the government.”
David Clark rapidly moved his company into war mode, adding sewing machines, and began making tent parts, jungle hammocks with insect netting and roofs, as well as fragmentation bomb parachutes, on prime contracts. His passion, however, was developing the “Anti-Blackout” (ultimately referred to as a “G”- Suit). With the help of the Department of Biophysics at the Mayo Clinic, the company fabricated 22 progressively improved designs.
Initially, the military was skeptical. Again, from his memoir, Clark recalled, “I wrote to the Commanding Officer at Wright Field [now Wright-Patterson Air Force Base] in Dayton, Ohio, and received a classic reply, ‘There is no existing data indicating that apparatus such as you describe would be helpful.’ I was to hear that many times, with only slight variations in the next few years.”
The first government check sent to David Clark Company for its pioneering work on the partial pressure “anti-g” suit. The $13 check was never cashed and kept as a souvenir. (Photo: David Clark Company)
Undeterred, David Clark persevered. After experimenting with several suit pressure valve and inflatable bladder designs, the company received its first check from the government on June 2, 1944, for a partial pressure anti-g suit – made out for thirteen dollars! Since then, David Clark Company’s contributions and accomplishments read like a Who’s Who list of aerospace history:
- First Operational Capstan Pressure Suits developed for X-1 rocket plane test pilots who broke the sound barrier and first explored high-altitude flight.
- X-15 Full-Pressure Suits developed for test pilots who flew the X-15 to record speeds and altitudes - Mach 6.70 and 354,200 feet.
- Gemini Space Suits developed for each mission's unique requirements, including the G-4C space suit for Ed White's first U.S. space walk.
- Apollo Block I Suits utilized to train the initial Apollo astronaut crews and support initial missions.
- Apollo Communications Carrier worn by all Apollo astronauts on lunar missions, providing clear and reliable communications with mission control on Earth.
- Standard Full-Pressure Suits worn by pilots of various high-altitude aircraft such as the F-4, F-15, XB-70, HL-10, X-24, U-2, AND SR-71 Blackbird.
- Shuttle Advanced Crew Escape Suits and Launch Entry Suits worn by space shuttle astronauts.
- Contingency Hypobaric Astronaut Protective Suit (CHAPS) and variants such as SALUS for commercial space flight.
- Orion Crew Survival Suit (OCSS) to support NASA’s emerging missions beyond low earth orbit, to the moon and beyond.
The Red Bull jump
Among the many other accomplishments not listed above, one of the most high-profile was the design and manufacture of the pressure suit worn by skydiver and adventurist Felix Baumgartner for the Red Bull Stratos Program. In October of 2012, Baumgartner jumped from a capsule 128,000 feet above earth (at that time a world record), suspended in space by a balloon. He became the first human being to break the speed of sound outside a vehicle. Baumgartner landed by parachute safely in the New Mexico desert. The David Clark Company suit performed flawlessly.
Skydiver and adventurist Felix Baumgartner’s record-breaking jump in a pressure suit designed by David Clark Company. (Photo: David Clark Company)
Perceived by most as a “record breaking stunt” by thrill-seeking adventurists, the effort was actually the culmination of a detailed design, development, test and evaluation (DDT&E) effort to advance the state of the art for aerospace crew protective equipment, vehicles and related escape systems. The jump from such an extreme altitude provided the company with important data and information on the performance capabilities of its suit and occupant—information that has since been used to enhance the design and manufacture of subsequent suits for military pilots and astronauts.
“Our support of the Red Bull Stratos Program was an opportunity for us to showcase our ongoing commitment to enhance the safety and performance of those who work in challenging environments every day, whether they be extreme altitudes, the vacuum of space, or in the realms associated with high-G flight,” said Dan Barry, Vice President/Director of Research & Development at David Clark Company. “Mr. Clark recognized that the unique capabilities and expertise developed by his company represented a true, National asset, the preservation and advancement of which remains a core focus of our operations 88 years later.”
Hearing protection headsets
In 1952, David Clark was invited to be a guest on a five-day training cruise on the F.D.R. aircraft carrier (the largest in the Navy fleet at the time) by Dr. Ralph Christy, a navy friend of the then ‘Clark Company’, who was charged with Pilot and Flight Crew Protection. That invitation and the five days that ensued proved to be a major turning point for the company. David Clark was stunned by the volume of noise on the carrier flight deck with jets taking off and landing. At a decibel rate far exceeding the threshold that can cause permanent hearing damage, Clark observed some men were also subjected to confusion by the noise. He was later informed that some had been injured and even killed by propellers and jet intakes.
Months later, while visiting the home of David Clark, Dr. Christy proposed that the Clark Company devise protective devices against the noise and the two began sketching out ideas. After a series of prototypes were tested, the 372-2 Hearing Protector received a patent in October 1953. By 1957, the Clark Company’s best year up to that time, more than half the profits were derived from over-the-head style hearing protectors, with the USAF joining the U.S. Navy as primary customers.
Inset: Vintage David Clark hearing protector, circa. 1953. Aircraft carrier Navy pilots on “Vultures Row” wearing modern-day David Clark hearing protectors. (Photo: David Clark Company)
Aviation headset pioneers
During the early 1970s, David Clark Company began to broaden its focus in an effort provide aviation pilots with headsets that provide, not only hearing protection from engine noise in loud aircraft cockpits, but also the ability to communicate clearly with ATC. This effort resulted in the introduction of one of the first, viable, communication headsets for aviation pilots: the Model 10BB/F.
Model H10-BB, David Clark’s first aviation headset manufactured in 1974. Today, David Clark offers the broadest line of aviation headsets in the industry. (Photo: David Clark Company)
Today, David Clark Company serves the general aviation, commercial aviation, marine and military markets with the broadest line of fixed wing and rotary wing headsets in the aviation industry, including flagship models DC ONE-X and DC PRO-X2 Series active noise reduction (ANR) headsets and the Model H10-13.4 passive noise-attenuating headset, the longest and best-selling headset in aviation.
Most popular David Clark aviation headset models today, left to right: DC PRO-X2 ANR Series, DC ONE-X ANR Series and the H10-13.4 passive noise-attenuating headset. (Photo: David Clark Company)
Critical communication headset system solutions
By the mid-1980s, the company continued to expand its reach into new markets with the introduction of Wired Headset Communication Systems designed for airline/airport ground support personnel, as well as firefighters and first responders. These systems were designed to provide clear communication and enhance performance, safety, and situational awareness (while still providing hearing protection) for crews working in high-noise environments. Thousands of David Clark wired systems are still being used in these markets today.
The advent of wireless and digital headset systems
Buoyed by the success of its wired headset systems, the David Clark Company forged ahead with the introduction of the Series 9900 Wireless System in 2011. Wireless systems, featuring advanced Digital Enhanced Cordless Telecommunications (DECT) technology, provide users with all the communication advantages of wired systems, while also providing the additional benefit of mobility and freedom of movement, without being tethered to an apparatus or other equipment—a huge benefit for firefighters on the fireground and for ground support personnel during aircraft pushback, deicing and other airport ramp and maintenance applications.
Series 9100 Digital Headset System components, including Communication Headsets, Master Station, Headset Station, Belt Station and Wireless Gateway. (Photo: David Clark Company)
The Series 9100 Digital System, introduced in 2017, affords workboat crews with the advantages of Scalability for a virtually unlimited number of users, Versatility with multi-channel programmability and the ability to seamlessly integrate wireless headsets for a “hybrid” wired/wireless communication solution, and Simplicity for ease of programming and operation. Wired and wireless capability from the same system enhances programming flexibility for a broader range of mission requirements and creates highly adaptable configuration schemes.
A sea change in workboat crew communications
In the early 1990s, David Clark Company took aim at the workboat segment of the Marine market and introduced the Series 9500 wired headset communication system for patrol boats, fire/rescue craft, tug and tow boats, offshore service vessels and other specialized workboats. Having gained over 20 years of experience in the marine market, the company quickly saw the advantages of its Wireless and Digital Headset Systems for workboat crews.
Series 9900 Wireless Headset System components, including Communication Headsets, Belt Stations, and Wireless Gateway. (Photo: David Clark Company)
The Series 9900 Wireless and Series 9100 Digital (wired) systems have both been well received by workboat crews worldwide, featuring rugged reliability, excellent headset comfort, and are built with marine-grade components offering ingress protection, salt/fog corrosion resistance, wide ranging temperature tolerance and superior shock/vibration absorption to stand up to harsh marine environments.
David Clark Company has also formed relationships with several leading boat manufacturers including SAFE Boats International, Zodiac and MetalCraft Marine. As one example, the David Clark Series 9100 hybrid (wired and wireless) system was installed on the Multi-Mission Interceptor (MMI) demo patrol boat from SAFE Boats International. Rob Goley, Coast Guard veteran and now Business Development Director for Federal Programs at SAFE Boats International, had this to say: “Many missions are long, with many hours on the boat. The operators require comfortable equipment when they’re underway. The David Clark [Series 9100] system is comfortable, easy to use, reliable, and it works. That’s critical for our operators that are out using this equipment.”
Rob Goley pilots the Multi-Mission Interceptor (MMI) demo boat from SAFE Boats International, equipped with Series 9100 Digital Headset System. (Photo: David Clark Company)
The future
David Clark Company remains fully committed to maintaining the highest levels of product quality, performance, customer service and support for its aerospace crew protection equipment and critical communication headsets and systems. The David Clark Company story will continue to be characterized by its core values of corporate integrity, ingenuity and innovation—consistent with the vision of its founder, David Myron Clark.
Read David Clark Company: An American Success Story in Pdf, Flash or Html5 edition of August 2023 Marine News
Other stories from August 2023 issue
Content
- Interview: Mike Complita, Elliott Bay Design Group page: 10
- NSMV: The Model of Future of Government Shipbuilding page: 16
- Labor Shortages, Climate Change & Technology: They’re All Related page: 18
- David Clark Company: An American Success Story page: 22
- US Shipyards Investing to Add Serious Lifting Power page: 28
- Offshore Wind: US Shipbuilders Answering the Call page: 34
- Clean Technology Lasers: A New Tool to Remove Corrosion and Scale page: 40