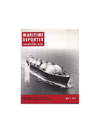
Boiler And Engine Room Controls
A control manufacturer, like any other organization, is in business to sell a product at a profit and therefore, makes every effort to develop and standardize a line of products that is acceptable to a given market in terms of overall performance and is within established price limitations.
On the other side, however, as a result of the owner's personal touch in conjunction with the variations of shipyard's identities, words like "standard system" or "exact duplicate" are not listed in a marine engineer's dictionary.
In a nostalgic moment I came to the unexpected realization that a fundamental change in control principles has occurred at regular intervals of approximately 10 years.
The first automatic combustioncontrol system was introduced in 1933 and was based on the transfer of the process variable (steam pressure) into a hydraulic analog signal. The controlled signal was then transferred into a power piston motion, located in the same unit.
As of this day, no hydraulic control units are known to be in operation aboard ships anymore.
The N-type electric combustion control units which were introduced in the early 40's were based on the same principles of a controller and a power actuator directly linked together, but using an electric-driven motor in lieu of a hydraulic power cylinder.
Thus, two major disadvantages of the hydraulic application were eliminated, namely the high-pressure hydraulic power-supply unit and the relatively expensive high level of tolerances required for proper operation of the hydraulic controller units.
Several electric N-type control units are still operating in the original design stage and can be found both aboard seagoing vessels and inland-based boiler installations.
A complete redesign of the almost 10 year old N-type electromechanical combustion control system was introduced to the market in 1951 under the appropriate trade name N-51.
*Mr. Dirriwachter, manager of engineering, General Regulator, Dallas, Texas, presented the paper summarized here before a meeting of the Pascagoula Section of the American Society of Naval Engineers held in Gautier, Miss.
The control principles of the N-series were completely maintained, but the requirements of better characterization capabilities were incorporated together with the solid linkage for fuel and air demand by means of a shuttle bar. In addition, a proper fuel-to-air ratio adjustment was accomplished. The most important aspect of this development was the recognition of a total control system of multiple variables responding to a single demand in lieu of individual control loops accidentally linked together.
The N-51 concept became an international marketing success, basically because of its simplicity, reliability and its attractive initial purchase price and installation cost. More than 2,200 units have been installed since the original introduction and most of them are still successfully in operation all around the world.
More than 20 years of continuous efforts preceded a major breakthrough in establishing the use of air pressure for analog signal transmission.
The most significant change in the principles of control technology was the idea of assigning individual mathematical functions to separate instruments and then building up a control system, as required, by selecting the proper mathematical units, in contrast to the established control systems, consisting of individual loops, each controlled by a single instrument with fixed mechanical relations between the various functions.
This principle opened the flexibility to the customer and the control manufacturer to provide for anything from a minimum of analog controls (e.g. drum level control only) to a considerably more complex, interconnected analog control variety in which each system responded to its own needs, but at the same time affected other related boiler controls.
The pneumatic controls became a worldwide accepted source of control systems and some form of pneumatic signal transmission can be found on every seagoing vessel in today's merchant marine.
At the beginning of the 70's the marine world was finally ready to accept the solid-state control in the engine room. For many years electronic controls were successfully applied in the stationary industries, but special requirements for shipboard applications had to be ironed out before the marine industry would accept electronic controls, plus simplified maintenance procedures to assure that a relatively nonelectronically- oriented crew could keep the system in operation, and cost reduction, especially in the field of spare parts.
At first, the digital electronic controls were introduced which would operate in conjunction with the conventional analog controls.
Digital control functions are s u c c e s s f u l l y used for: burner management systems; annunciator systems; vital auxiliaries auto/ stand-by systems; sequential pump startup systems, and makeup and spill systems.
The "All-Dark" concept refers to a console arrangement that shows no indication by means of illumination when all operating conditions are normal. Of course, gages and demand readouts are available to enable the operator to continuously monitor the status of the running equipment.
The conventional way of status indication by means of separate indicating lights for "on" and "off" status, makes a console layout of this size almost inoperable.
The operator will be in a continuous state of confusion because with so many color-coded lamps, the console will look like a giant Christmas decoration with lights steady or flashing on and off all the time. When an alarm situation occurs, the operator will have to figure out which lights are supposed to be illuminated, which lights are not supposed to be illuminated, and which lights changed status as a result of the alarm condition.
The "All-Dark" control console eliminates this confusion completely.
Whenever an abnormal situation arises, an audible and visible alarm is initiated in the annunciator system. At the same time the operator's attention will be directed towards the proper console section where one or more indicating lights are illuminated.
This way, regardless of the increased amount of controls and automation, the supervisory function of the operator is simplified.
Electronic engine room automation is becoming more and more a fact of life aboard U.S. ships.
Several new shipbuilding programs include electronic controls and centralize the supervision in a separate control room. While at the same time more and more sub-systems are transferred from local operation to the control center.
The most important reason is not to reduce the manning level, but to improve the overall visibility of the plant status and to reduce the reaction time where human intervention is required.
At the same time, efficiency of the plant can be improved due to an increase of automation with instantaneous self-corrective actions and interface with other related sub-systems.
The computer is here to stay and that means one day the computer will be in the U.S. ship's engine room controlling the steam propulsion plant. When considering today's state of the art, computer application can be expected to take over the conventional controls in the early 80's.
A centralized engine room management consists of: controlling, monitoring, alarming, and safety trips.
It can be anticipated that the transfer from what we now call conventional controls to computer controls will not be so abrupt as to take over all the functions at once.
The introduction of the computer will occur in the monitoring function. This momentary monitoring will be combined with permanent logging and, since the storage capability is inherent with the computer, analyzing the plant performance will be directly available for the plant operators.
The next step will be to transfer the alarm and trip functions to the computer with conventional back-up of the trips.
Finally, the controls, both analog and digital, will be programmed into the computer system with conventional takeover capabilities of the most vital controls as a back-up.
The selected design approach must be to assure continuity of today's plant operations and today's plant supervision, and not to convert the plant operator into a computer operator. This objective can be accomplished by providing the operator with control panel devices which are similar in form and identical in function as those devices now employed in central automation. An important aspect of design consideration must be to assure that the operator becomes an integral part of the computer controlled activities, because the computer is not to replace the human bodies in the engine room but to prevent human errors in decision making and provide for immediate actions when needed.
Although the introduction of the computer aboard ship is another major change in control principle, the transfer will happen as smooth and unnoticed by the operators as all previous changes thanks to the fact that the computer will be applied for the same operating objectives as today's control functions.
Other stories from July 1977 issue
Content
- Rules For Floating Dry Dock Construction Published By ABS page: 4
- Proposal Calls For Ship's Spare Parts To Be Based Ashore page: 4
- Two Arabian Projects Totaling $80 Million To Great Lakes Dredge page: 6
- Raytheon Marine Opens New York Office page: 6
- The LNG Aquarius Is The First Of Twelve LNG Tankers Being Built By General Dynamics page: 7
- G.E. Marine Gas Turbines To Power German Frigate Ships page: 7
- ABS To Consolidate Headquarter Operations page: 8
- Western Union Int'l To Market New MARISAT System page: 8
- Skagit Corporation Appoints F.K. Weimann page: 8
- National Supply Builds 15,000-Psi Subsea BOP And Wellhead System page: 9
- Carrington Slipways Receive Order To Build Offshore Supply Vessel page: 10
- MarAd Approves Loan To Finance Bulk Carrier page: 10
- Gulf Trading Names Kenneth L. Hawthorne page: 10
- Mamo II Joins Dillingham Fleet In Hawaii page: 10
- Lantana Boatyard To Build 134-Foot Alaskan Landing Craft Of Krogen Design page: 10
- New Zealand Awards Multimillion-Dollar Contract To Sembawang page: 12
- Seven Seas Towing Names Capt. Cleveland Operations Manager page: 12
- Clay Chiles Awards Marathon LeTourneau 150-44-C Rig Contract page: 12
- Multipurpose/Container Ships Ordered From Korea Shipbuilding page: 14
- Propulsion Systems, Inc. Expands Thruster Line page: 14
- San Francisco Hosts SNAME Spring Meeting And STAR Symposium page: 14
- Hillman Transportation Names Kenny President page: 16
- Harland And Wolff Belfast Yard Building 333,000-Ton Tankers page: 16
- 'Tina' Is A Happy Blend Of Innovations And Proven Designs page: 17
- General Dynamics Awarded $354-Million Sub Contract —Option For Two More page: 17
- Thunderbolt Marine Industries Launches Twin 96-Foot Tugs For Panama Canal Services page: 17
- Moore McCormack And Aeron Marine Apply To Transport Oil For SPR page: 17
- Scottish Offshore Opens Texas Office page: 18
- New Vessel Joins Circle Line Fleet page: 18
- Electro-Nav Now Sole U.S. Distributor Of BEN Speed Logs page: 18
- Jeffboat Starts Work On A Second Ferry For The Mississippi River Bridge Authority page: 20
- Robert L. Hague Post To Honor Admiral Rea page: 22
- New 75-Foot Marine Lubricants Supply Vessel page: 23
- International Paint Names Donald S. Otto page: 23
- Anixter-Mark Announces Five-Way Ratchet Mount page: 23
- SNAME Pacific Northwest Section Holds Joint Meeting With ASNE page: 24
- President Carter Presents $25,000 Prize For Energy-Saving Device page: 24
- MacGregor Publishes Ro-Ro Encyclopaedia page: 25
- Avondale Launches First Of Four Tankers To Carry Alaskan Oil For Sohio page: 26
- New Shipyard Operating North Of Arctic Circle page: 26
- Farrell Lines And General Electric Credit Create A Maritime First page: 28
- Dravo SteelShip Expands Facilities page: 28
- USCG Certified No-Discharge Oxidizing Toilet Now Available page: 28
- Worthington Compressors Announces New Marine And Navy Sales Force page: 34
- Carrington Slipways Building Cement Carrier page: 34
- Tragosa Charters Seven Tidewater Vessels For Offshore Mexico page: 34
- De Laval Separator Issues Marine Brochure page: 34
- Dutch And American Firms To Jointly Build Hopper Dredge In U.S.A. page: 35
- R.J. Reynolds Industries Elects McEvoy To Board page: 35
- American Abrasive Metals Announces New Non-Slip Roll-On Safety Coating page: 35
- Marine Surveyors To Hold 19th Marine Conference In New York In October page: 36
- Boiler And Engine Room Controls page: 37
- Magnavox Introduces Marisat Shipboard Communications Terminal page: 38
- ASNE Charleston Section Reports Activities page: 38
- Pacific NW Section Hears Two Papers At Annual Spring Meeting page: 39
- Omnithruster Describes Maneuvering System In New Brochure page: 40
- Port Of New York Maritime Association Elects Officers page: 40
- Cargo Preference Measure Vital To U.S. Shipbuilding page: 41
- Delta Shipyard Delivers 120-Foot Seismic/Utility Vessel To Shell Oil page: 41
- Donald Staples Named Comptroller Of GM's Electro-Motive Division page: 42
- Peterson Maritime Services Open Office In Houston page: 42
- Zapata Marine Realigns Marketing Group Posts page: 42
- Over 1,500 Attend ASNE Annual Meeting page: 42
- Raytheon Introduces New Radiotelephone page: 43
- Seaworthy Engine Systems Appoints Jack E. Horner page: 43
- New Luxury Hotel Barge Begins Thames Cruises page: 43
- NDTA New York Chapter Elects Captain Fritzke page: 44
- National Maritime Council Elects Barker Chairman page: 44
- Stow Manual Contains Information On Solving Valve Problems page: 45
- General Regulator Opens East And West Coast Sales/Service Offices page: 45
- Lincoln Warren Named ODECO Vice President Oil & Gas Exploration page: 45
- Naval Engineers Announce Combat Systems Symposium Set For Oct. 12-13 In Maryland page: 46
- Papers On Navy C-P Propeller Program And Spray Patterns Of Jet Thrusters Discussed At Joint SNAME Chesapeake/ASNE Meeting page: 46
- Mississippi Marine Towboat Delivers Harbor Boat To Union RR page: 47
- Northwest Marine Iron Works Names Grider And Hiller page: 47
- Marine Electric RPD Markets Steering Gear Power Failure Alarm page: 47
- Halter Delivers New 185-Foot Ship To Offshore Services Ships, Inc. page: 48
- Equitable Delivers Ferry To State Of No. Carolina page: 48
- Crowley Maritime Appoints Richard Simpson And Alan Cavis To Caribbean Division Posts page: 49
- SNAME Chesapeake Section Elects Officers- Hears Paper On Domestic LNG Vessel Construction page: 49
- SNAME Los Angeles Section Honors Past Chairmen —Discusses Paper On Slow-Speed Marine Diesels page: 50
- M / V Gulf W h a l e Christened At Q u a l i t y Equipment Y a r d For O p e r a t i o n By Seven Seas T o w i n g page: 51
- General Cargo Ships Becoming Obsolete page: 52
- Kevin Patrick Smith Forms Supplier's Marine page: 52
- Trus Joist Brochure Describes Revolutionary Scaffold Plank page: 53
- Mar A d Awards Contract To Study Perishable Commodities page: 54