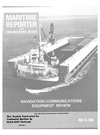
NEW GHH-Constructed Drydock, Mission Bay, For Continental Maritime
In mid-March, Mighty Servant 3 began a 14,400-mile voyage from Bremen, West Germany to San Francisco, Calif. This heavy-lift ship, operated by Wijsmuller Transport B.V., Ijmuiden, Netherlands, transported the 25,000-ton-lift-capacity floating drydock Mission Bay to Continental Maritime of San Francisco, Inc.'s shipyard. The drydock was constructed at M.A.N.- GHH Sterkrade's dockyard in Blexen, West Germany. Delivery of the drydock will culminate a project that started in June 1983 with preliminary design discussions between Continental Maritime and M.A.N.- GHH. Design details were finalized in April 1984.
The drydock hull was designed and constructed in accordance with the regulations and under the supervision of the American Bureau of Shipping (ABS). After completion of commissioning trials at Continental Maritime's shipyard in San Francisco, it will be classed +A1 floating drydock by ABS. In addition, it is designed and constructed to meet the U.S. Navy's drydock safety certification criteria published in Military Standard 1625 (B).
Plates for construction were ordered up to 3.75 meters in width and up to 15 meters in length (this limited the average waste for the entire dock to approximately 2.5 percent). These large-size plates were welded from one side with copper rail backing into panels by using automatic welding machines. The frames were welded by using semiautomatic welding machines and a special jig. Similar special-type jigs were used for welding of T girders which serve as web frames or bearers.
The dock sections were constructed in a separate prefabrication shed before transfer to the assembly yard.
The dock was constructed on a horizontal level with the centerline bulkhead resting on the continuous tilting line which consisted of loaddistributing concrete blocks with lowerable sand box equipment. The dock lay with its complete bottom surface on sleeper blocks which were in turn supported by concrete slabs and which could be vertically adjusted and readjusted by hydraulic jacks.
Weld shrinkage was allowed for and the dock is built with considerable hogging which is distributed over the length as a curve and which was maintained by continuously checking by leveling. The maintenance of the hogging along with the weld sequence of the longitudinal and transverse section joints was based on experience and provides the dock with a precisely horizontal keel line when afloat after launching in the "stress-relieved" position, an important factor in proper dock operation.
The complete dock construction yard, covering 138,000 square meters, was carefully laid out to permit the highest quality construction with low labor and overhead costs.
The launching took place on March 11, 1985. The sponsor, Mrs.
Constance Picchi, wife of Continental Maritime's chairman and chief executive officer Roger A.
Picchi, named the dock Mission Bay.
The order for the new dock was placed with the stipulation that it be delivered and ready for docking a ship as early as May 1985. The decision to use a heavy-lift ship was mainly dictated by this time factor.
Traveling at a speed of 13-15 knots, the ship took the route around South America through the Strait of Magellan.
The dock was loaded on the heavy-lift ship Mighty Servant 3 for the trip to California on March 15, 1985. Prior to the arrival in California, Continental Maritime of San Francisco completed the final preparation to the berth for the dock at Mission Bay Pier 50.
The M.A.N.-GHH Sterkrade staff will commission the dock and perform a part of the tests required for the ABS classification. Keel blocks, bilge blocks, crane and other equipment will be unlashed, placed in operating positions and tested.
Tests already completed at the shipyard in Germany include: tightness test of all tanks, test of the electrical connections and function tests of all machines and equipment. All other tests will be conducted in San Francisco according to a program developed by M.A.N.-GHH Sterkrade in consultation with Continental Maritime and ABS.
Innovative features of the drydock include an advanced system of adjustable keel and bilge blocks developed by M.A.N.-GHH and modified specifically for the docking of U.S. Navy ships with large deadrise.
In addition, the dock has been outfitted with a sonar dome pit, 102 feet by 40 feet by 5 feet. The pit allows shipping or unshipping of the sonar dome rubber window of U.S.
naval ships in a wide variety of docking positions. The dock is outfitted with steel portable transverse girders and heavy plates which are used to cover the pit when not in use. Keel blocks can be placed on this covering structure. The pit provides ample working area around the SQS-26 and SQS-53 sonars installed on U.S. naval combatants, up to and including CG 47 and DDG-51 classes.
The dock incorporates two dock arms which support working cars for personnel working on topsides or superstructure. Each arm travels on a rail system, located on the inner side of either wing wall, and each dock arm is outfitted with an endwork platform. The dock arm position can be controlled from this platform. The working platform is automatically held in the horizontal position.
A high-pressure water blast system is located on the safety deck, port and starboard. Each system includes an electric-drive pump, a water supply tank (with both fresh and saltwater inlets), distribution piping, hose valves, hoses and nozzles.
Water outlet pressure and flow will range up to 10,000 psi and 100 gpm. Pressure and flow characteristics are easily varied with interchangeable plunger conversion sets.
The new drydock is another step by Continental Maritime toward implementing the firm's decision to become a full-service shipyard.
"We're primarily trying to attract Navy ship repair work," said Continental's president D. Whitney Thornton II. He also stated the yard is in an ideal position to increase its West Coast commercial work through competitive pricing and quality workmanship.
This ship repair firm presently employs 520 people in its San Francisco yard and 430 people in its San Diego yard. The first scheduled drydocking for Mission Bay will be the Ex-President Monroe which Continental Maritime is converting into the Gem State (TACS-2), an auxiliary crane ship.
For full details on the services offered by Continental Maritime, Circle 25 on Reader Service Card For complete detailed literature and full specifications on M.A.N.- GHH drydocks, Circle 26 on Reader Service Card
Read NEW GHH-Constructed Drydock, Mission Bay, For Continental Maritime in Pdf, Flash or Html5 edition of May 15, 1985 Maritime Reporter
Other stories from May 15, 1985 issue
Content
- Scheidt Named Marketing And Sales Vice President For American Steamship page: 5
- Radio-Holland USA, B.V. Automates Coastal Station WLO's Radiotelex Service page: 5
- Terry Announces New GLT Single-Stage Turbine page: 6
- NEW GHH-Constructed Drydock, Mission Bay, For Continental Maritime page: 8
- Free Brochure From Baldt Details Moor-Free™ Rapid Release System page: 8
- Korobov Elected Vice President-Finance For COMSAT TeleSystems— Mutnick Named Controller page: 10
- Tano Receives Additional Coast Guard Contract Valued At $2.7 Million page: 10
- Daewoo Wins $16.5-Million Contract To Build Offshore Vessel For India page: 10
- Exclusive Rep For Danish Firm Introduces Radiotelephone System page: 10
- Weerts Named Senior Program Manager For American Systems page: 11
- ABS Developing New Computer Programs To Aid Ship Designers page: 11
- Smith Appointed Senior Vice President For American Steamship page: 14
- Bohme Named Product Development Manager For Simpson Timber page: 14
- Joseph Joins COMSAT As Executive Vice President page: 14
- Lundberg Reappointed Director General Of INMARSAT page: 16
- Literature Available On Clemco Industries' 'Educt-O-Matic' page: 16
- Hubbard Named To Newly Created Position At American President Lines page: 16
- SNAME Introduces New Quarterly— The Journal Of Ship Production page: 16
- Cambridge Instruments Completes New Plant page: 16
- Navigation & Communications Equipment — A R e v i e w— page: 18
- Elliott White Gill Thrusters Offer Unique Advantages page: 32
- Tompkins To Market BFGoodrich Bearings In Four Eastern States page: 33
- Los Angeles SNAME And ASNE Sections Meet In Joint Session page: 34
- Literature Available On FIRE-PREP® 2012 From Nalco Chemical page: 34
- Skantek Announces SK-401, An OCR Software Technology Breakthrough page: 34
- John Crane Offers Literature On Their Line Of Bellows Seals page: 34
- Flakt Offers 20-Page Brochure On Facilities And Capabilities page: 36
- Clemco Pipe Cleaning Tools Blast-Clean Pipe Interior Without Rotating The Pipe page: 39
- Hitachi Delivers Jackup Rig Built For O N G C Of India page: 39
- PRC Announces Availability Of New Family Of Mercaptan Functional Polymers page: 40
- New Boiler Cleaning Technique Offers Savings For Vessel Owners page: 45
- Gulfport Orders Second Paceco Container Crane page: 45
- Brochure Available On HF-SSB Radio Products From Harris Corporation page: 45
- Halter Marine Awarded $85-Million Navy Contract To Build Six T-AGOS Ships page: 46
- Bailey Joins Selkirk Metalbestos As Staff Engineer For Piping Line page: 46
- Zito Named Vice President- Marketing & Development Of COMSAT Technology page: 46
- No Claims Yet On Cat's Over-The-Counter Parts Availability Guarantee page: 46
- Racal Wins $2.8-Million For Marine Simulators page: 46
- McTighe Offers Brochure On High-Flow & Low-Flow Oil/Water Separators page: 46