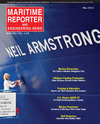
SEEMP: Potential Win-win for Commercial Vessels
SEEMP can make a fleet more competitive in a difficult business environment while reducing its impact on the environment.
In January 2013, the International Maritime Organization (IMO) put into force new regulations intended to improve the energy efficiency of ships over 400 gross tonnes (gt) on international voyages, including a requirement to keep on board a ship-specific Ship Energy Efficiency Management Plan (SEEMP). This initiative is intended to reduce ship greenhouse gas (GHG) emissions by encouraging ship operators to reduce energy consumption.
Since that time, there has been much discussion within the shipping industry about the potential domestic enforcement of the SEEMP.
Recently, the U.S. Coast Guard (USCG) expressed its intention to enforce the IMO SEEMP requirement for vessels over 400 gt on international voyages during vessel boarding by checking to see that the vessel has an up-to-date SEEMP. If the SEEMP does not exist or is outdated, the USCG intends to notify the U.S. Environmental Protection Agency.
Currently an SEEMP is not a domestic requirement for U.S. flagged vessels engaged solely in U.S. trade.
Although the SEEMP does not have any formal enforcement measures, it is in the best interests of ship owners and operators to develop and implement a plan by monitoring the vessel’s energy efficiency, improving existing operations and implementing new energy-efficiency technologies as they become available and are appropriate to the vessel.
In doing so, they will be able to reduce costs and improve operating margins while reducing the environmental impact of GHG emissions.
Improving ship design and operation
The new regulations were adopted in 2011 under the International Convention for the Prevention of Pollution from Ships (MARPOL). These regulations have two components:
• The Energy Efficiency Design Index (EEDI) requirement specifies GHG emissions limits to be met or exceeded for new ship construction.
• The Ship Energy Efficiency Management Plan (SEEMP) requires ships to have an energy-efficiency management plan aboard.
For news and background on the development and promulgation of these regulations, visit http://www.imo.org/MediaCentre/HotTopics/GHG/Pages/default.aspx.
The IMO considers CO2 to be a greenhouse gas and recognizes the fact that the amount of CO2 generated per kilowatt of power produced depends on the efficiency of the heat engine (diesel, gas turbine or steam turbine) and the hydrogen-carbon ratio of the fuel (heavy fuel oil having a lower ratio than natural gas). Accordingly, the IMO’s Marine Environment Protection Committee (MEPC) has chosen fuel consumed per unit of effective transport work as the measure of unit GHG emissions.
The EEDI uses a comprehensive equation to calculate a targeted consumption quotient [g/(unit-work)] as a standard for ship designers and owners to meet or better during the vessel’s design phase. In recognition of improving technologies, the EEDI efficiency target energy consumption (CO2 emissions) get more stringent with time.
Implementing the required SEEMP is a four-step process as outlined in IMO’s “2012 Guidelines For The Development Of A Ship Energy Efficiency Management Plan” (MEPC 63/23 Annex 9). The four steps for developing a ship-specific SEEMP are as follows:
• Planning
The planning process includes determining the current status (baseline) of the ship’s energy usage and the expected energy efficiency to be gained by implementing the plan.
• Implementation
Implementation of the energy improvement process described in the planning process includes defining the person(s) in charge of implementation and the incorporation of a record-keeping system that will be beneficial for self-evaluation.
• Monitoring
The ship’s energy efficiency should be quantitatively monitored using an established method. The guidelines note that continuous and consistent data collection is the foundation of monitoring; however, they also state that over-burdening of the ship’s crew should be avoided.
• Self-evaluation & improvement
This stage is intended to produce meaningful feedback for the next planning cycle.
It should be stressed that the SEEMP is a continuous process wherein the plan is periodically updated as feedback is received and factored into the process.
Continuous monitoring without "additional burden"
Continuous monitoring of the vessel’s energy consumption is both a requirement of SEEMP and a practical prerequisite to improving energy efficiency and reducing operating costs.
The IMO recognizes that adding more data collection and record-keeping responsibilities to already overloaded shipboard crews can be counterproductive and potentially dangerous. Not only do the 2012 SEEMP guidelines caution against over-burdening the crew with data collection and continuous monitoring, they also suggest that the information should be transmitted, stored and analyzed ashore.
Fortunately, the shore-side facilities and utility industries have been using energy-efficiency management plans for decades and, in most cases, the technology developed for shore-side can easily be transferred to the maritime industry. Continuous energy monitoring and verification firms have been collecting and monitoring energy use in facilities such as large building complexes, hospitals and power plants, in some cases, for decades.
They have reported the collection and monitoring results to plant operators and owners and, when appropriate, their engineering staff has alerted the operators of issues that needed immediate attention. They have also suggested cost-effective ways for operators and owners to improve performance and save money — both by improving existing operations and through cost-effective equipment upgrades.
Similarly, a commercial or passenger fleet owner can contract with a third-party marine monitoring and verification service for continuous onshore monitoring and analysis of real-time data sent over the web from the vessel’s onboard machinery plant control and monitoring system (MPCMS). Ship system data may include main engine performance and fuel consumption, the ship’s HVAC system and electrical generation for hotel load. Daily fuel consumption and voyage reports enable the owner to make informed fuel purchasing decisions based on historical and forecasted operations, validate emission regulation compliance, and verify the performance of energy-efficiency initiatives.
The Value of SEEMP
Owners and operators should not view complying with SEEMP as another regulatory burden; rather, it should be viewed as a plan for lowering energy consumption and lowering fuel costs. For owners of existing chartered vessels, defining and implementing SEEMP most likely will justify an increased charter rate; for ship operators, improved vessel energy efficiency means savings on fuel and associated costs.
To be truly energy efficient, operators should look beyond the vessel’s overall fuel consumption and the transport work performed by the vessel. They should look past the low-hanging fruit available to reduce fuel consumption — reducing ship speed, propeller polishing, hull coatings and/or cleaning, etc. They should also examine non-propulsion power energy uses, such as balance of plant loads, hotel loads including air conditioning and cargo related loads. This is especially important for vessels that have a very large hotel load, such as cruise ships, and for vessels operating at reduced speeds.
Remember that when vessels are operated at reduced speeds, the non-propulsion component of the total energy consumption is a greater fraction of the total.
When properly implemented and used, SEEMP will empower owners, operators and crews with the knowledge required to make cost-effective decisions to save energy and reduce operating costs. In particular, when monitoring is expanded to record how the energy is used within the vessel, it will enable them to understand the vessel’s energy consumption trends and take or plan additional energy-efficiency measures.
If the crew is relieved of the burden of continuous data collection and record keeping, they are likely to view the SEEMP as a positive development since it will give them — especially the chief engineer and the master — a tool to better operate the ship.
Ultimately, the marine industry as a whole may come to view the SEEMP not only as another set of regulations, but as a way to make our fleet more competitive in a difficult business environment while reducing the industry’s GHG impact on the natural environment.
The Author
Jose Femenia is the former Engineering Department Head and director of the Master of Marine Engineering Program at the United States Merchant Marine Academy and Engineering Department Chairman at the SUNY Maritime College. Femenia now serves as a consultant at utiliVisor, which provides comprehensive energy monitoring and advisory services for the marine industry. He is a licensed professional engineer.
(As published in the May 2014 edition of Maritime Reporter & Engineering News - http://magazines.marinelink.com/Magazines/MaritimeReporter)
Read SEEMP: Potential Win-win for Commercial Vessels in Pdf, Flash or Html5 edition of May 2014 Maritime Reporter
Other stories from May 2014 issue
Content
- New Concept Eliminating Crude Oil Spill Spread page: 10
- BOS Provides 2-5% Fuel Savings page: 10
- Floating Production System Orders Outlook page: 12
- The Treatment of Foreign Seafarers page: 16
- Hydrodynamic Software Suites page: 19
- SEEMP: Potential Win-win for Commercial Vessels page: 20
- Ergonomic Controls Innovation for ECDIS, Bridge Controls page: 22
- To Litigate, or Arbitrate? That is the Question page: 24
- Experts Weigh Training Factor into Sewol Tragedy page: 26
- Does e-Learning Work? page: 30
- Elmer A. Sperry: Pioneer of Modern Naval Tech page: 32
- Aviator & Engineer: Lawrence Burst Sperry page: 38
- U.S. Navy's AGOR 27: R/V Neil Armstrong page: 40
- Classification Leaders Weigh in on Marine Propulsion page: 44
- Interview: Rich Hobbie, Water Quality Insurance Syndicate (WQIS) page: 48
- Mammoet: World’s Biggest Crawler Crane Installs Legs on Ship page: 52
- ALP Tugs Get Rolls-Royce Deck Equipment page: 52
- Traction and Control System for Tugboat Winches page: 53
- Townsville Opts for a Liebherr LHM 420 page: 53
- WASSP Goes Wireless with New Remote Mapping System page: 55
- Danelec’s 3G VDR page: 55
- ABB Energy Management System page: 55
- Transas Liquid Cargo Handling Simulator page: 55
- Color LCD Radar from SI-TEX page: 55
- Martek: Network-Connected ECDIS page: 55
- Vessel Optimization Data page: 55
- Lilaas L01 Control page: 56
- Northport Actisense Engine Monitoring Units page: 56
- MarineNav’s New Line of Displays page: 56
- Voyager Planning Station Adds AtoBviaC Distance Tables page: 56
- L-3 SAM for DanTysk Wind Project page: 56
- Navis Joystick System for New Yacht page: 56
- Ship-to-Turbine Oil Change System page: 57
- USN Orders Hoffer Flow Measurement Systems page: 57
- Phoenix Launches HDL-LED Series page: 57
- New Line of Safety Switches page: 57
- HAL Retrofits VDRs on Fleet page: 57
- New Steering System page: 57