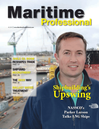
New Ballast Water Management Regulations
Ready or not, here it comes. Are you prepared?
In March 2012, the U.S. Coast Guard (USCG) amended its regulations on ballast water management by establishing standards for the allowable concentration of marine organisms in ballast waters discharged in ports and coastal areas of the United States. The new regulation includes procedures for independent testing and approval of ballast water treatment (BWT) systems to be installed on ships to meet these standards. According to the USCG, the new requirements will be more effective than ballast water exchange (i.e., flushing our ballast water and replacing it with mid-ocean water while in transit) in controlling the introduction and spread of non-indigenous species (NIS) in waters of the United States. The requirements of the Ballast Water Management (BWM) Regulation (Federal Register, Vol. 77, and No. 57), treatment options to meet these requirements, and what ship owners should be doing now to comply should all be key concerns for today’s ocean operators.
BWM Regulatory Summary
Applicability: The regulation applies to all U.S. and foreign commercial vessels equipped with ballast tanks that discharge ballast water into U.S. waters, operate outside the U.S. Exclusive Economic Zone (i.e. more than 200 nautical miles from U.S. shorelines), and practice ballast water exchange. It also applies to ships that do not operate beyond the EEZ but take on and discharge ballast water in more than one Captain of the Port Zone and are larger than 1,600 gross register tons. U.S. Department of Defense or USCG vessels, crude oil tankers engaged in coastwise trade, or vessels that operate exclusively within one USCG Captain of the Port Zone are exempt from the regulation.
Implementation Schedule. The new requirements will be phased in for different types of vessels, as follows;
- New Vessels (commissioned on or after Dec 1, 2013): on delivery
- Existing Vessels (<1,500 cubic meters ballast water capacity): 1st dry dock after Jan 1, 2016
- Existing Vessels (1,500-5,000 cubic meters ballast water capacity): 1st dry dock after Jan 1, 2014
- Existing Vessels (> 5,000 cubic meters ballast water capacity): 1st dry dock after Jan 1, 2016
Time extensions may be granted by the USCG case by case if the ship owner or operator can document that BWM regulatory compliance is not possible. However, extension requests must be made at least 12 months prior to the scheduled implementation dates cited above.
Ballast Water Discharge Standard: The ballast water discharge standard replaces ballast water exchange to significantly improve protection of ecosystems within U.S. waters. The requirements, based on organism size and use of indicator organisms, are equivalent to the IMO discharge standard adopted by other countries:
Size-Based Organisms:
- For organisms >= 50 um (zooplankton): < 10 organisms per cubic meter (applies to zooplankton)
- For organisms < 50 um to >=10 um: < 10 organisms per milliliter (applies to phytoplankton)
Indicator Organisms:
- < 1 coliform forming unit (CFU) Vibrio cholera per 100 mL
- < 250 CFU Escherichia coli per 100 mL
- < 100 CFU enterococci per 100 mL
As noted in the BWM regulation, the USCG plans a “practicability review” no later than January 1, 2016, to determine whether an even tighter discharge standard is warranted based on available treatment technologies for shipboard applications, environmental impacts and cost.
Ballast Water Management Requirements. To meet the new discharge standard, a seagoing commercial vessel must employ one of the following BWM methods:
- Install and operate a BWT system approved by the USCG to meet the regulation’s ballast water discharge standards at all times.
- Install and operate an alternative management system (AMS) that has been type-approved by a foreign administration in accordance with testing requirements of the International Maritime Organization (IMO), for up to five years from the BWM compliance date for that particular vessel.
- Only use water from a U.S. public water system for ballast water provided that the ballast tanks have been previously cleaned and no seawater subsequently introduced into ballast tanks or supply lines.
- Discharge of ballast water to an onshore reception facility for treatment.
For most vessels, only the first two methods will be feasible from logistical, safety and operating cost standpoints. And because of the tight regulatory implementation schedule, it is anticipated that most vessels will install an AMS for short-term (less than five years) compliance, and vessels with previously installed BWT systems (to meet foreign IMO-based discharge standards) will seek an AMS determination from the USCG to continue to operate those systems. Note that systems with AMS approval will become USCG type approved BWT systems if they can meet land-based and ship-based testing requirements.
Reporting Requirements: The operator of a vessel must maintain written records on the ship’s ballast water management operations, essentially the same as that required for ballast water exchange. This requirement can be met by using the Ballast Water Reporting Form from the IMO ballast water management guidelines. Monitoring records must be kept for at least two years. The regulation does not specify record-keeping requirements for operating BWT systems, but it is expected that this information will need to be provided to USCG inspectors upon request.
Enforcement and Penalties: Vessels will be subject to USCG inspections, which will include sampling and analysis of ballast water discharges and examination of documents to determine compliance with the BWM regulation. In addition, every vessel will be required to have a specially designed sampling port at each overboard discharge point for use by USCG inspectors for collecting representative ballast water discharge samples. Sampling procedures for shipboard inspections are still under development by the USCG and will be posted on its website when available. The owner or operator of a vessel who violates the BWM management or discharge standard requirements is subject to a civil penalty up to $35,000 per day.
BWT System Approval Procedures: The manufacturer of a BWT system must apply to the USCG for type-approval. The application must detail the design, shipboard installation, component testing and O&M system requirements, and present results of land-based and ship-board testing by a USCG-accepted Independent Lab. Land-based testing must meet the requirements of the Generic Protocol for Verification of Ballast Water Treatment Technologies (called ETV Protocol), published by the U.S. EPA Environmental Technology Verification Program in September 2010. Land-based testing will determine if the BWT system can reliably meet the discharge standard for prescribed challenge water conditions. Shipboard testing must be performed for at least six months to demonstrate that the system will meet the discharge standard when operated in a shipboard environment.
A manufacturer may also submit existing data from type-approval testing by a foreign administration, and work with a USCG-accepted Independent Lab to evaluate data and fill any data gaps by having the system tested in accordance with the ETV Protocol. If the BWT system is approved by the USCG, a certification number and approval certificate will be issued to the applicant specifying acceptable ballast water quality uptake conditions (e.g., freshwater, brackish water or seawater) and engineering parameters for operating the system.
BWT Systems
The global market for BWT systems is predicted to grow to over $34 billion through 2020 in response to IMO and USCG-based ballast water discharge regulations (Frost and Sullivan, 2012). BWT systems are now manufactured by dozens of companies around the world, including traditional suppliers of marine equipment, suppliers of municipal water and wastewater treatment equipment, and shipbuilders. As of November 2013, 35 BWT systems have received IMO-type approval from foreign administrations, and 28 of these have been accepted into the AMS program by the USCG.
As shown in Figure 1 above, these systems include various treatment technologies and combinations but are typically arranged to provide two stages of treatment: (1) physical solid-liquid separation to reduce sediment and remove larger organisms, and (2) disinfection to kill or inactivate smaller organisms. The disinfection processes can be further classified into physical or chemical treatment processes. The latter may involve residual control to meet discharge limits for active chemical substances or physical enhancement technologies to improve treatment performance.
As shown in Figure 2, the global market for BWT systems is dominated by two treatment technologies -- UV and electrochlorination. These are manufactured by 26 equipment suppliers and compose 85% of the approximately 1,500 IMO type-approved BWT systems installed to date. The basic process trains are generally described above.
UV Disinfection: This is a two-stage treatment process with a pressure-rated filter unit (typically with micron-rated disks or membrane elements) to remove sediment and larger organisms, followed by a UV disinfection unit to inactivate smaller plankton, bacteria and viruses. No chemicals are required to operate the system. During ballasting, water is typically processed through both the filter and UV stages as water is pumped into the ballast tanks. Solids captured by the filters are discharged at the ballasting location. During de-ballasting, the filter is typically bypassed and water is treated by the UV unit only before discharging overboard.
Electrochlorination: This is a two-stage treatment process with a micron-rated pressure filter or strainer followed by an electrochlorination unit. The latter is essentially an on-demand chemical system, which uses electrolytic cells to generate a sodium hypochlorite (bleach) solution from seawater and electricity. Some treatment systems pump the entire ballast water flow through the electrolytic cells, whereas others use a small slipstream to generate a concentrated hypochlorite solution, which is then recombined with the main flow. During ballasting, water is processed through both the filter and electrochlorination unit as water is pumped into the ballast tanks. A chlorine residual (or residual oxidant) is maintained in the tanks for a minimum contact time (typically a few days) to improve disinfection and eliminate regrowth of organisms during transit. During deballasting, a neutralization chemical (e.g., sodium bisulfite) is added to the water to remove the oxidant residual as it is pumped overboard. Note that this type of system cannot be used in freshwater areas such as the Great Lakes because it requires salinity for hypochlorite production.
Complying with the New Regulations
The new BWM regulation will increase costs for ship owners/operators to evaluate, install, operate (including additional record-keeping) and maintain BWT systems with regulatory compliance dates, starting now for new build vessels and at the next scheduled dry-dock for many existing vessels. They must therefore quickly become familiar with the new requirements, risks of non-compliance, and necessary steps to bring individual ships or fleets into regulatory compliance.
For owners/operators of seagoing commercial vessels, most important will be to select an appropriate type-approved BWT system that is compatible with the ship’s existing ballast water system and can be operated to ensure compliance safely by the crew. Key design considerations for BWT system selection include:
- Ballast pump capacities and operating pressures
- Ballast tankage volume (if required for disinfection contact time)
- Available space for the BWT equipment
- Uptake and discharge piping arrangements
- Chemical storage location (if required)
- Discharge sample location (for USCG inspection use)
- Ship routes (and associated ballast water quality conditions)
- Integration of the BWT system controls into the ship’s ballast control system
- Training requirements for crew members.
BWT system selection is made more complicated in that the USCG has not type approved or certified any systems yet, although it plans to over the next year or two. In the meantime, AMS-accepted systems must be used with only a five-year regulatory compliance horizon, with no certainty that they will ultimately be approved by the USCG for long-term compliance with the BWM regulation.
Given the complexity and uncertainties of the BWM regulatory requirements, tight implementation schedule, system installation challenges, and the myriad of BWT systems on the market, many ship owners are hiring a qualified engineering firm to assist in selection of the most appropriate BWT system and work with the selected equipment supplier to design and install the BWT system on a particular ship or fleet. The planning, engineering and installation of the BWT system needs to be carefully coordinated with the vessel drydock projects.
(As published in the 4Q 2013 edition of Maritime Professional - www.maritimeprofessional.com)
Read New Ballast Water Management Regulations in Pdf, Flash or Html5 edition of Q4 2013 Maritime Logistics Professional
Other stories from Q4 2013 issue
Content
- Aker Rhymes with “Soccer” page: 8
- Changes in Oil Trade Patterns and their Effects page: 10
- Maritime M&A: Financial Crisis to Present Day page: 16
- When is a Ship Not a Ship? page: 18
- NASSCO’s Parker Larson on All Things Shipbuilding page: 20
- Beyond Shipbuilding: Training and Recruitment page: 24
- The Aker Way: From Surviving to Thriving page: 32
- Converting for the Oil Market page: 40
- Damen Looks Offshore page: 43
- 3D Laser Scanning for the Marine Industry page: 46
- Technology Answers Risk and Security Questions page: 49
- Setting Standards for Maritime Security page: 52
- New Ballast Water Management Regulations page: 54