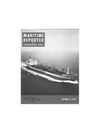
Modules Towed To Site For Construction Of Offshore Plants
With the rapid increase in the need for large plants in nonindustrialized areas, major Japanese shipbuilders have each developed unique methods to build large plants utilizing their engineering and shipbuilding techniques, such as barge-mounted plants.
Some of them have already exported bargemounted plants for production of pulp and mortar, as well as for desalination.
A method described below is a "Module Plant System" which was developed by Mitsubishi Heavy Industries, Ltd. The plant constructed under this system is the offshore natural gas liquids facilities for Qatar General Petroleum Corporation, and final shipment was recently completed.
Mitsubishi-developed Module Plant System is, in a word, an efficient prefabrication method for plant construction. It has the following features: (1) Specially developed system and equipment for transportation and erection; (2) Easily transportable, and completely assembled modules of high quality, and (3) Simplified, no piling foundation.
MHI has all the fundamental techniques required for this system, which have been acquired through long experience as one of the leading shipbuilders, heavy machinery manufacturers and plant engineering contractors.
Major steps of the Module Plant System are divided into the following six stages: (1) Engineering, (2) Procurement and/or fabrication of equipment and materials, (3) Module fabrication, (4) Loading and ocean transport, (5) Unloading and inland transport, and (6) Civil engineering and installation work.
Of the above-mentioned major steps, the module fabrication is carried out under the following process: Equipment and materials are delivered to and stocked at the module fabrication factory under a firm schedule and careful material control.
Fabrication of modules is made under the same production control as in well-equipped factories. A factory with ample stock yard and facilities for module fabrication, as well as loading on oceangoing vessels, is considered to be most suitable.
The Module Plant System has the following advantages as compared to conventional methods: (1) High quality, (2) Lower cost, (3) Faster delivery, (4) Less work at site, and (5) Less effects from local conditions.
As the main stages of the construction process are carried out under the same production control as applied in the factories, and because on-site work is minimized, it is possible to eliminate unfavorable local factors which may seriously affect work flow at site.
Moreover, making the most of these advantages, the system makes it possible to undertake construction of any type of plant based on a total integrated contract.
The LNG facility for Qatar General Petroleum Corporation is to separate gas from oil during offshore drilling and transport it to shore by a process developed by Mitsubishi.
The LNG facility will be installed in waters with a depth of 35 meters, about 85 kilometers offshore east of Doha, along the coast facing the Persian Gulf. Installation of the entire facility is scheduled to be completed by July 1979.
Composition of the facility: At present, there are three oil wells in operation in the sea area. For these three oil wells, three stations will be erected, each comprising a compressor (compression unit) platform, a glycol dehydrator/power generator platform, and a living quarters platform (for the operators) . The platforms will be connected by bridges.
Weight of platforms and modules: Compressor platform — three units, each 4,000 tons. Each unit consists of three modules, which are put together at the site. Glycol dehydrator/power generator platform—three units, each 1,100 tons. Each unit consists of one module. Living quarters platform—three units, each 1,100 tons. Each unit consists of module.
As described above, one station includes five modules and weighs a total of 6,200 tons.
The three stations weigh 18,600 tons in total.
In addition, a riser-deck with a weight of 100 tons will be added. This means that there will be in all, 16 modules.
Other stories from October 1978 issue
Content
- Shipyards Support Marinfec Asia 79 page: 4
- New Firm To Buy Five Vessels For Service Great Lakes To Europe page: 4
- C.Y. Tung Group Enlarges Fleet To 118 Vessels page: 6
- Bath Iron Works Names Allan G. Anderson page: 6
- MarAd Approves Title XI Guarantee For Eagle Dredge page: 7
- Two New Parcel Tankers Added To Stolt-Nielsen Fleet page: 7
- Gibbs & Cox, Inc. Opens Newport News, Va. Office —R. Delia Rocca Named page: 7
- Abex Corporation Names Paul J. Powers President Of Denison Division page: 7
- Built By Main Iron Works, The 6,000-HP McAllister Tugboat Jabbar Will Work In Arabia page: 8
- El Paso Announces Proposed Offerings page: 8
- ITT Decca Marine Names Richard Muller page: 8
- Title XI Requested To Reconstruct Flat-Deck Oceangoing Barges page: 10
- Triangle Fleeting Corp. Names Jeffrey Kindl VP And General Manager page: 10
- Foster Wheeler To Supply Inert Gas Systems For LNG Tankers At Quincy page: 10
- C.F. Bean Corporation Names John Lescroart Executive Vice President page: 10
- National Marine Service Names Glennon Bequette Shipyard Division VP page: 11
- Royal Netherlands Orders Three New Freighters From Dutch Shipyards page: 11
- Gotaverken Plans To Build 37,000-DWT Icebreaking Bulker page: 12
- John J. Bajor Joins Midland Marine Corp page: 12
- Diamond Shamrock To Charter Chemical Tanker Building At Avondale page: 12
- Crowley Maritime Corp. Appoints Jay Brickman page: 15
- General Electric Credit Buys Its Eleventh Tanker page: 16
- Rear Adm. Westfall Addresses ASNE Charleston Section page: 16
- Continental Oil Announces Six Executive Promotions page: 16
- Hillman Barge & Construction Elects R.E. Kenny And B.T. Kelley page: 16
- Chairperson, Member Appointed To Kings Point Advisory Board page: 18
- Los Angeles-Long Beach Propeller Club Names Officers For 1978-79 Term page: 18
- U.S.-Flag Fleet To Double In The Last Quarter This Century page: 20
- U.S. Navy Awards Ingalls $287 Million Contract To Design And Build First Of A New Class Destroyer page: 20
- Exxon International Awards Maintenance Contract To Stanwick page: 21
- Crowley Maritime Names Jim Grissom Manager San Juan Operations page: 21
- ITC Completes 6,237-Mile Dry Tow To Argentina With Six Oil Barges And Two River Towboats page: 22
- NICOR, Inc. To Acquire National Marine Service page: 22
- Port Weller Dry Docks Plans Shipyard On Lake Erie To Build And Repair Large Ships page: 22
- Mobilization Ship Design To Be Unveiled November 6 At Conference In Arlington page: 22
- 27 New Members Elected To American Bureau Of Shipping page: 24
- George Lowman Elected Farrell Lines Chairman page: 26
- Furuno U.S.A. Formed In South San Francisco page: 26
- Gastech 78 To Focus On World Supply And Demand For LNG And LPG page: 27
- Butterworth Systems Receives IMCO Approval page: 30
- Atlantic Diving Forms SeaTec International, Ltd. page: 30
- Ruddie E. Irizarry Named President Of PRMMI— Carr, Calderon Also Named page: 30
- Evergreen Handt Corp. Names Three Executives page: 31
- AIMU Reports On Hull Insurance Market At Annual Conference page: 32
- Crowley To Provide Maintenance Services Worldwide For Navy page: 32
- Rutland Maritime Names Peter Gallagher page: 32
- Alario And Associates Named To Represent Shipyard In Greece page: 33
- Hofstra And Webb Jointly Announce New Relationship page: 34
- Reynolds Announces $580-Million Upgrading For Sea-Land Service page: 34
- Tampa Ship Repair & Dry Dock Dedicates New $23-Million 900-Foot Graving Dock page: 35
- Singapore Marine Conference Set For February 1979 page: 40
- St. Louis Ship Delivers Second Of Four Supply Vessels To Gulf Mississippi Marine Corp. page: 40
- Hitachi Zosen Asaka Works (Sakai) Delivers Ro/Ro Carrier Dana Maxima page: 40
- Sperry Division Names Blumberg Marketing Communications Manager page: 42
- J.J. Scott Of Sea-Land Named Director Of Mideast Por page: 42
- Floyd Mechling Retires From Union Mechling page: 42
- Jacques B. Hadler To Direct Research Activities At Webb page: 43
- Admiral Benkert Elected President Of AIMS page: 44
- AWO Elects James Potter —Industry Issues Examined At Board Meeting In Tulsa page: 44
- Tidewater To Acquire Insurance Firm In Texas page: 46
- Steam Turbine Operating Guide Now Available page: 46
- Shipping Executives To Review Maritime Policy At Oakland Conference page: 46
- Kubota To Stockpile Anti-Corrosive Pipe In Texas Facility page: 48
- Kawaski Delivers Cargo Ship Equipped With Derrick Capable Of Lifting 600 Tons page: 50
- Investment In Tankers: The Case For Optimism page: 50
- International Firms Plan Large-Scale Operations In The Beaufort Sea page: 52
- USCG Removes All Personnel Restrictions Based On Sex page: 53
- Hawaii Site Selected For Testing Nodules Gathered From Ocean Floor page: 53
- Hawaii Site Selected For Testing Nodules Gathered From Ocean Floor page: 53
- New Starlite Is Second 122-Foot Combination Boat From MARCO Yard page: 53
- New Abex/Denison Bulletin Describes Pressure Valves page: 54
- Booklet Published On Bulk Liquids And Solids In Standard Freight Containers page: 54
- President Signs Murphy Energy Bill page: 54
- General Electric Credit Names Joseph Heimerl page: 54
- FMC Launches Another World's Largest Barge page: 55
- Passenger Liner's Fast Repair At Northwest Marine Iron Works page: 55
- MacGregor's Novel Solution To Quay Height Variation page: 56
- Oceanology International For Offshore Industry Set For March 3-7, 1980 page: 56
- Hawaii Firm Announces Plans To Construct A Stable Semi-Submerged Fishing Vessel (SSFV) page: 57
- SNAME New York Section Reports Meeting Program For 1978-1979 Season page: 57
- Newfoundland Makes Bid For $.75-Billion Investment In Fishery page: 57
- Modules Towed To Site For Construction Of Offshore Plants page: 58
- New York Metropolitan Section Begins New Season With Past Chairman's Night And Third Generation Ro/Ro Paper page: 58
- Shipbuilding Experts Meet To Discuss Ways To Increase Automation And Productivity page: 58
- Halter Delivers Second Supply Boat To Gonsoulin Enterprises page: 59
- Ship Structure Committee Publishes Two New Reports page: 59
- Texas Gas Transmission Inland Waterways Division Announces Personnel Changes page: 60
- A.L. Burbank & Company, Ltd. Announces Election Of Officers —Celebrates 50th Anniversary page: 61
- Maritime Data Network Announces Computerized Charter Fixtures Library page: 62
- Sperry Computerized Positioning System Permits Pipelaying In 2,000-Ft. Waters page: 62
- American Bureau Of Shipping Classes 53 Vessels In August page: 62
- Hatch & Kirk Inc. Acquires Cleveland Diesel Engine Assets page: 64