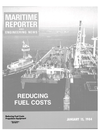
REDUCING FUEL COSTS First In a Series-Propulsion Equipment
Diesel Engine Manufacturers Continue To Improve The Fuel Efficiency Of Their Engines In an effort to reduce fuel costs, the American marine industry has undergone a renaissance in marine engineering. The last decade has seen the deepsea U.S.-flag shipowners go from being unilateral proponents of steampowered merchant vessels to stalwart supporters of diesel power. The decade also saw significant changes in fuel characteristics and price structure. The principal change affecting marine fuels was the reduction in heavy fuel quality coinciding with the price structure, change that made it very attractive for vessel operators to use the lower quality fuels. These changes had the potential for adverse affects on the operation of dieselpowered vessels.
As expected, the diesel engine manufacturers did not stagnate during this period but rather met the challenges of the marketplace with new technological improvements.
They have made the diesel engine a mechanical engineering marvel capable of satisfying the needs of the deepsea owners as well as the inland waterway operators.
They have made this inherently efficient engine available in such a wide range of power, size, and weights that an appropriate engine is available for nearly all marine applications.
Of primary concern to all operators is the ability of diesel engines to operate with the most economical available fuels and still maintain their cycle efficiency and reasonable maintenance schedules.
Diesel manufacturers, well aware of the basic constitutents of the heavy marine fuels, undertook design refinements to minimize the adverse affects of the harmful elements in the fuel. Nearly all engine manufacturers have taken the tack of using special materials and carefully controlled engine component cooling as the methods of minimizing the impact of vanadium on engine longevity. A review of manufacturers literature reveals that most manufacturers claiming their engines are capable of burning the lower quality fuels boast of their special cooling features, especially relative to exhaust valves and seats. Sulfur attack of cylinder walls also seems to have succumbed to a commonly accepted remedy—insuring that cylinder wall temperatures are high enough to prevent sulfuric acid condensation and/or using sufficiently alkaline cylinder oils to neutralize the acid deposits on the cylinder walls. Obviously, if an engine manufacturer is designing an engine for a market intending to use a high-quality fuel, such as gas oil, it is not necessary to take these measures to insure engine compatibility with the vanadium and sulfur.
In addition to vanadium and sulfur, other fuel properties or constituents have a bearing on the operation of diesel engines. Some of these other properties or constituents are viscosity, density, Conradson carbon residue, asphalthenes, water content, ash, catalytic fines, and cetane number. Although some engines are more tolerant than others to fuel properties and/or contaminant variations, no engine is totally immune from highly degraded fuels.
The ingenuity of the modernday diesel engine designer is further exemplified by the development and perfection of the superlong- stroke engines. These engines have not only resulted in relatively low crankshaft rpm's compatible with propellers of large dry bulk carriers and tankers but have resulted in thermal efficiencies heretofore unattainable in a thermo-mechanical energy conversion device—thermal efficiencies greater than 50 percent. Nicolas Carnot would have been proud of the modern diesel designer.
One casualty of the very high efficiency of super-long-stroke engines is a relatively low amount of usable heat in the exhaust gases.
The very efficient expansion of the cylinder gases results in low exhaust gas temperature, which in turn results in low exhaust gas energy availability thereby reducing the amount and/or conditions of the waste heat produced steam.
Manufacturers of four stroke cycle, medium/and high-speed engines have concentrated on improving engine volumetric efficienty and air-fuel mixing as the primary means of improving engine efficiency.
Design improvements of modern marine diesel engines go beyond thermodynamic cycle advances and into the realm of engine maintenance.
The use of hydraulic devices for pre-tensioning of bolts, studs, and tie-rods, as well as custom rigging devices for easy handling of heavy components, are commonplace. Advanced designs of cylinder heads to include valve cages, which simplifies valve maintenance, are commonplace on four stroke cycle engines and two stroke cycle engines using uniflow scavenging, especially on those en- gines designed to burn the lower quality fuels.
The responsibility for a well operating diesel vessel does not rest solely with the engine manufacturer but must be shared with the ship designer, the onboard operators, and the ashore support effort.
The design marine engineer responsible for the systems design must pay close attention to the vessel's intended operating mode and expected available fuel. On board systems should be engineered with sufficient margins to allow for service growth as well as the expected and unexpected that the future holds in store. One system in particular that design marine engineers should be liberal in defining system specifications is the fuel oil conditioning system.
Equipment selected should not be expected to operate at the extremity of its operating range at design power. A liberal equipment selection policy might be slightly more expensive initially but most likely will result in lower life-cycle costs for the vessel.
Once the ship is designed, the fate of its machinery is mainly dependent on the operating crews and shore support staff. Although modern diesel engines need only a bare minimum of supervision once operating, it is important to insure that the engine is well monitored by both automatic systems and a very competent cadre of marine engineers—individuals with a very thorough knowledge of diesel engines and the uncanny ability to detect problems before they become serious.
What follows is a synopsis of the technological activities and accomplishments of many diesel engine manufacturers addressing the challenges they face in designing marine diesel engines that will help usher in the 21st century.
B&W ALPHA Circle 71 on Reader Service Card B&W Alpha Diesel A/S of Frederikshavn, Denmark, is a company of the M.A.N.-B&W Group that designs, manufactures, markets, and services complete vessel propulsion systems. Last year the company completed the integration of the in-line and V version of the 20/27 M.A.N.-B&W diesel engine and the in-line version of the 32/36 M.A.N.-B&W engine with existing Alpha controllable-pitch propellers and gearboxes. This has resulted in four-cycle diesel propulsion systems developing as little as 680 bhp at 1,000 rpm, which can burn heavy fuel oil up to 2,100 sec. Redwood 1 at 100 F.
A new series being offered is the 20/27-VO propulsion system. While the engine itself is not new, the system incorporates the new Alphatronic I and Alphatronic II— the company's latest electronic remote control systems. Features of the new control systems include: reliable attainment of economical operation through the optimum combination of engine rpm and propeller pitch; simple controls requiring minimum attention of the watch officer; simple installation, basically a single electrical cable connection from the wheelhouse control panel to the engine room; easy maintenance, with as many functions as possible on easily replaceable, printed circuit boards; and a clear, easily understood display of essential information.
The Alpha Diesel product line now includes the following series: 20/27, 136 bhp per cylinder at 1,000 rpm; 23L, 155 bhp per cylinder at 825 rpm; 23/30, 170 bhp per cylinder at 825 rpm; L28/32, 285 bhp per cylinder at 775 rpm; and L32/36, 500 bhp per cylinder at 750 rpm.
B&W HOLEBY Circle 72 on Reader Circle Card B&W Holeby Diesel A/S of Denmark manufactures 4-stroke diesel engines in the power range from 450 to 5,500 bhp. The company also supplies diesel generator systems of shipboard use.
In addition to diesel engines, Holeby production includes major components such as crankshafts and connecting rods for use by licensees in the manufacture of 4- stroke B&W engines, as well as spare parts for its own engines.
The company also manufactures fuel oil mixing units and other auxiliary equipment.
As a result of recent development projects, all types of Holeby engines can now be supplied in uprated, four-valve versions that can be operated efficiently on the same heavy fuel as the big main propulsion engines. Holeby calls this development its Unifuel system.
BERGEN DIESEL Circle 58 on Reader Service Card Reducing fuel expenses, which are representing an ever-increasing part of a ship's total operating cost, has always been one of Bergen Diesel's main endeavors. Generally, there are two ways to achieve that: (1) building engines that have the lowest possible specific fuel consumption and the ability to burn low-grade heavy fuels; (2) developing engine systems for ship propulsion and power generation that allow engine operation near the engine's and the system's point of optimum efficiency.
The thermal efficiency of Bergen Diesel's K-range of engines is as high as today's state of the art will allow, giving a realistically low specific fuel consumption over a wide load range. Furthermore, the K-type engine is the product of more than 20 years of heavy fuel operation experience, and is thus capable of burning low-grade, highviscosity heavy fuels while maintaining extremely long component overhaul intervals and component life.
To be able to operate vessels at or near the point of optimum fuel efficiency, Bergen Diesel has designed sophisticated engine systems that have been put into successful operation. For fishing vessels, systems with high-output shaft generators, driven via twospeed gearboxes from engine front end power take-offs, allows the use of shaft generators at two engine speed modes, i.e., the free-running and the trawling speed, for inexpensive, main-engine-generated electric power. Hybrid power systems, being a combination of diesel- electric and diesel-mechanical power transmission to the propellers, give offshore supply and anchor- handling vessel operators the possibility to utilize the advantages of both systems.
Bergen Diesel generating sets operating on the same type of residual fuel as the main engines on larger vessels reduce the volume of distillate fuel consumed, and can enhance the economic performance of any vessel considerably.
CATERPILLAR Circle 57 on Reader Service Card Caterpillar 3500 Series marine engines have set new standards for fuel savings—savings that can actually allow repower with full payback in less than IV2 years.
Fuel savings may in fact exceed 35 percent at all operating loads, not just within a limited range or at "rated" load.
Designed for tighter oil control than two-cycle engines and most four-cycle engines, the 3500s can save several thousand dollars a year in lube oil costs alone.
For simplified maintenance, front-mounted governor and sidemounted oil, water, and fuel transfer pumps improve accessibility.
Fuel filters, oil, and oil filters can all be changed at the same time.
Access covers near the camshaft and in the crankcase allows simple and effective visual inspection.
These and other 3500 Series design features translate into less maintenance time and lower maintenance costs.
COLT INDUSTRIES Circle 56 on Reader Service Card Colt Industries' Fairbanks Morse Engine Division continues to offer both the Colt Pielstick and the Fairbanks Morse opposed-piston diesel engines. The Fairbanks 38D8-1/8 opposed-piston engine is offered in both blower-scavenged and turbocharged versions, with horsepower ranges from 708 to 3,500 bhp at 750 rpm, and 920 to 4,200 bhp at 900 rpm. These engines have always enjoyed high fuel efficiency, but today's sophisticated electronic control and monitoring systems are squeezing even better fuel economy from them.
Fairbanks Morse continues to produce the Colt Pielstick PC-2.3V and PC-2.5V diesel engines, with ratings from 6,420 to 11,700 bhp at 520 rpm. These engines are capable of burning heavier grades of residual fuels.
The Engine Division now offers the Colt Pielstick PC-2.6 L & V and the high-horsepower PC-4.2V diesel engines. The PC-2.6, with horsepower ratings from 4,422 to 13,266 bhp, is a development of the PC-2 series medium-speed engine with the same general dimensions.
The PC-2.6 engine can burn all heavy fuels available on the market. The engine is fitted with water-cooled cages and exhaust valves, especially adapted to the fuel's vanadium content. The advanced technology of the PC-2.6 engine enables it to burn the poorest foreseeable heavy fuel without major modifications.
The Colt Pielstick PC-4.2V, rated from 16,270 to 29,286 bhp, is able to burn residual fuels of up to 4,000 sec. Redwood #1 at 100 F with a 400 ppm vanadium content.
The Colt Pielstick engines are backed by SEMT Pielstick's ongoing research and development programs.
The PC engine family has approximately 60 million hours of experience running on heavy fuels.
COMBUSTION ENGINEERING Circle 55 on Reader Service Card Combustion Engineering, Inc. is a leading supplier of steam generating equipment for the marine industry, both military and commercial.
CE has designed and manufactured main propulsion, auxiliary, and waste heat boilers for more than 40 years. In addition to new product design and manufacture, CE offers after-market support including service and OEM parts.
In recent years, CE has been involved in various marine research and development projects including improved boiler reliability, development of improved oil atomizers, and development of low excess air burners.
While marine steam generators have always been capable of burning degraded fuels, many shipowners are looking for alternative fuels to reduce their operating costs. CE has been actively involved in the development of modern, coal-fired marine boilers, with four ships presently in service and two more scheduled for delivery in 1984.
As another alternative, some shipowners are interested in burning PETCOM (petroleum coke/oil slurry). Hereto, Combustion Engineering has been at the forefront of this new technology, performing atomization and combustion tests for marine boilers.
RELIABLE POWER - RELIABLE SHIP CUMMINS ENGINE Circle 54 on Reader Service Card Cummins Engine Company manufactures six series of marine diesel engines rated from 170 to 1,250 bhp, continuous-duty operation.
Designed for heavy-duty workboat and fishboat applications, both main propulsion and ship service auxiliary power, Cummins engines have developed a reputation over the years for fuel-efficient power.
Since the mid-1970s, the Cummins K marine engines have developed a reputation for fuel efficiency as well as reliability. The KT/KTA-1150 series are in-line, six-cylinder models developing 400- 475 continuous bhp at 1,800 rpm; displacement is 1,150 cubic inches (18.9 liters).
The KT/KTA-2300 and KTA- 3067-M engines, introduced in 1978 and 1980, respectively, complete the Cummins product line with high horsepower, reliability, durability, and fuel economy. The 2300 series engines are a 12-cylinder, V configuration design with a displacement of 2,300 cubic inches (27.8 liters). The turbocharged engine has a rating of 800 bhp at 1,800 rpm, and the turbo/aftercooled version has a 940 bhp rating at 1,800 rpm.
The KTA-3067-M engine is rated at 1,250 bhp at 1,800 rpm for continuous- duty applications. It is a 16-cylinder engine with 3,067-cubic- inch (50.3-liter) displacement.
Recognized at their introduction as the most fuel-efficient marine diesel engines in their horsepower range, the K series engines have been improved continually to reduce specific fuel consumption.
Over the past three years, Cummins has reduced the specific fuel consumption for these models an additional 2-3 percent.
DAIHATSU DIESEL Circle 53 on Reader Service Card With its extensive experience in the marine field, Daihatsu has developed a new type of engine, the DL series, which features low quality fuel burning, low load operability, and low fuel consumption.
These DL series engines— DL-20, DL-26, DL-28, and DI^32— are a medium-speed type (600-1,000 rpm) with outputs covering the range from 750 to 3,000 bhp (550 to 2,205 kw). They are suitable for both main propulsion and auxiliary generating roles.
Severe tests and experiments under various conditions on all parts of these engines were carried out at the Daihatsu laboratory and factory before they were placed on the market. Daihatsu's traditional design concepts—simple and sturdy construction, easy maintenance, and lower maintenance costs—are fully incorporated in the DL series engines.
Since the DL series was placed on the market, Daihatsu reports an increasing number of orders from many overseas shipowners.
EFFICIENCY SYSTEMS Circle 52 on Reader Service Card Efficiency Systems Inc., a subsidiary of Flowtron Industries, Inc., had developed and is marketing Fuel Log, a line of low-cost fuel management systems that enable operators to reduce fuel consumption by about 10-15 percent.
Fuel Log I consists of a slowflow meter and engine performance sensors connected to each engine and wired to an electromechanical read-out that provides gallons per hour, total fuel used, and trip fuel. The more advanced Fuel Log II includes a microprocessor- based read-out that also provides shaft rpm, engine rpm, fuel remaining, time and date, and a printer.
The heart of the energy-conserving unit is the slow-flow liquid meter manufactured by Transamerica Delaval Inc. under an exclusive license from Flowtron covering Flowtron's patented technology.
Information from the meter, when processed through the Fuel Log read-outs, enables marine operators to quickly determine maximum engine efficiency at any given moment, weather, sea condition, and on-board weight. Operators can then instantly adjust engine rpm and tank flow to yield maximum power using the least amount of fuel.
Fuel Log systems come in three sizes, for engines that consume up to 40, up to 360, or more than 360 gallons per hour, and are priced from $3,500 to $14,500, including installation and operator training.
DETROIT DIESEL Circle 73 on Reader Service Card The Detroit Diesel Allison division of General Motors offers advanced fuel economy models of its 149 Series diesel engines. The turbocharged and intercooled engines are said to be the most fuel-efficient heavy-duty diesels available in their power range.
The Detroit 149 engines in 12- and 16-cylinder, V configurations are expected to show fuel economy improvements of about 3.5 percent over previous engines at the same horsepower ratings. The 12-cylinder models are available up to 894 bhp, and the 16-cylinder versions up to 1,212 bhp. The fuel economy improvements are the result of a number of engineering developments, including new turbochargers, unit fuel injectors, and a new airflow system.
With the new system, the power required to drive the Roots type blowers used in Detroit two-stroke cycle engines is reduced significantly as the engine reaches operating speeds. As that happens, the increased airflow from the turbochargers takes over the function of providing the intake air needed to maintain combustion and scavenging in the cylinders. A special valve takes the load off the blower by equalizing the pressure on both sides of the rotors, reducing blower horsepower. The new turbochargers and unit fuel injectors have been carefully tailored to match the needs of the new system for optimum fuel efficiency.
Detroit Diesel 149 Series engines have been popular with the commercial fishing industry for many years.
ELECTRO-MOTIVE DIVISION Circle 74 on Reader Service Card A new, more fuel-efficient version of the popular 645 Series diesel engine was introduced in 1983 by the Electro-Motive Division of General Motors. Compared with previous 645 models, the new engine is said to provide a reduction in fuel consumption of about 3 percent.
The new EC engine series combines innovative design features that insure superior performance, extended operating service, and enable the engine to withstand higher operating pressures with state-of-the-art turbocharger technology.
The 645EC uses a 16:1 compression ratio piston, increased from 14.5:1, producing the same power output with less fuel.
A newly designed impeller and compressor have been incorporated into the turbocharger.
Last year EMD also introduced a heavier crankcase option, the 645F engine. This engine, designed for high horsepower outputs, is currently available in 16- and 20-cylinder models.
A new multi million-dollar, blended fuels, engine test facility is under construction by EMD. In addition to this investment, the company has expanded its computerized design and manufacturing capabilities into an integrated CAD/CAM system that allows engineering designs to be communicated directly to the shop floor.
The Computer Aided Design/Computer Aided Manufacturing puts the factory of the future into EMD's operations today.
FLEET MANAGEMENT SYSTEMS GROUP Circle 51 on Reader Service Card The Vessel Management System (VMS) has been designed by Fleet Management Systems to provide the operator with the information required to maximize vessel profitability.
The functional, display, and analytical capabilities of the VMS are combined to support fuel management, engine diagnostics, and maintenance management programs, custom designed for any particular business operation.
The VMS fuel management package collects engine and vessel operating data to build a speedpower curve for the vessel under actual operating conditions. From this, the VMS can recommend the optimal speed for minimum fuel consumption.
Should such variables as wind speed or direction, current velocity, or fuel quality change, the VMS will immediately recalculate the speed-power curve and recommend a change in throttle setting, if required. This provides a real time system that helps the crew maintain optimal vessel performance.
VMS offers a wide range of valuable management capabilities. Its software is designed in conjunction with the customer to meet his special needs. The shipboard VMS can load data on cassettes for posttrip analysis. An office software package provides for financial planning and life-cycle management.
The VMS fuel management package can be the foundation on which to build a complete fleet management system. In many cases, the VMS can be linked to existing shipboard monitors and/ or sensors to provide a fully integrated system. Telecommunications capabilities are built into every VMS.
FOSTER WHEELER Circle 50 on Reader Service Card In this ever-changing world of ours, flexibility, availability, and economics are paramount to survival in the business world. Foster Wheeler Boiler Corporation proposes that in the marine trade, the above three elements are available when you take advantage of "Fuels of Opportunity." To have to purchase a specific quality fuel or shut down your plant leaves you at the mercy of local and world conditions. To be able to buy "Fuels of Opportunity" leaves you able to apply the three elements of survival.
Foster Wheeler's fluidized bed steam generator design permits you to switch from one fuel to another at unmatched cost savings and fuel flexibility with efficient burning of petroleum coke, residual oil, lignite, anthracite, and bituminous and sub-bituminous coals. Fluidized bed boilers are available in sizes for installation on board a tug up through the largest oceangoing vessels.
GMT Circle 75 on Reader Service Card GMT of America Corporation has been formed as a subsidiary of Grandi Motori Trieste S.p.A. of Italy to promote and market GMT engines in the U.S. Besides commercial marine diesels, GMT is also a leading designer and builder of naval engines.
GMT has one of the world's most modern plants for the design, manufacture, and testing of diesel engines. Its product line includes: low-speed, two-stroke engines from 5,000 to 44,000 bhp; medium-speed, four-stroke models in two cylinder sizes for a power range from 3,500 to 28,000; and high-speed, fourstroke engines with bores of 210 and 230 mm covering the 800 to 7,000 bhp range.
GENERAL ELECTRIC Circle 70 on Reader Service Card While General Electric Company produces test data on burning low-grade alternative fuels in its diesel engines, it is producing electricity for use in its factory in Erie, Pa.—a new wrinkle for cogeneration. Three 16-cylinder GE7FD engines, each rated at 3,400 bhp, are run an average of 14 hours a day, five days a week, at 10 percent over their rating.
Each engine is connected directly to a 3,000-kw generator that gives it a load to work against, and which produces the electric power.
The engine test facility, which cost $3.9 million, is contained in a 6,000-square-foot addition to the powerhouse building. The primary function of the new facility is to evaluate performance of newly developed engine components through life tests. These tests will be conducted in parallel with GE's continuing search for more economical fuels. And as fuel costs also have a major impact on engine testing, the powerhouse project has been developed to recover some or all of those costs.
It is expected that tests conducted in the new facility, along with tests currently being conducted on a workboat, will result this year in the issuance of a modified fuel specification to allow a blend of up to 30 percent residual content. Earlier work by the GE Transportation Equipment Products Department's Diesel Development Laboratory has already resulted in specification for a 10 percent blended fuel.
General Electric markets three sizes of diesel engine—8, 12, and 16 cylinders—with ratings ranging from 1,375 to 3,600 bhp.
GEORGE ENGINE Circle 69 on Reader Service Card As much as an 11.5-percent reduction in fuel consumption can be realized by George Engine Company's "bypass operation"—the upgrading of a Detroit Diesel 149 series engine from its normally aspired (NA) configuration to a turbocharged, intercooled, blower-bypass (TIB) configuration using the latest high-tech components from Detroit Diesel. Fuel savings provide a rapid payback of the cost of the conversion.
The blower-bypass is a simple butterfly valve arrangement that automatically diverts the incoming combustion air around the Roots blower when turbocharger boost has reached a sufficient level.
With the Roots blower bypassed, it no longer imposes an accessory load on the engine; the horsepower that was previously required is now available at the flywheel to do useful work.
With a smaller fuel injector, the TIB configuration produces the same horsepower at the same rpm as the NA arrangement, but does it with significantly less fuel. Alternatively, the owner may elect to use larger injectors to achieve greater horsepower output, but still at a competitively low specific fuel consumption figure.
HITACHI ZOSEN Circle 68 on Reader Service Card In response to what it sees as the need for an integrated approach to saving energy, Hitachi Zosen has performed comprehensive research toward the realization of more fuel-efficient ships. As a result, Hitachi now offers an integrated energy-saving package consisting of four independent systems: improvement of hull performance; improvement of main propulsion plant; application of efficient measures for the machinery plant; and optimization of navigation and maneuverability features.
These systems may be applied independently, in combination, or as an integrated, total energy-saving system. Among the items that may be included in the Hitachi package are the HZ bulbous bow; self-polishing type coatings; low-rpm, large-size propeller mounted in HZ nozzle; superlong- stroke, low-speed main engine; shaft generator; and 2- or 3- stage, pressure-type exhaust gas economizer.
KHD Circle 76 on Reader Service Card A range of weight- and cost-saving diesel engines has been developed by Deutz Engines Ltd., British subsidiary of Klockner- Humboldt-Deutz AG, in which new technology has made them safely operable well within Zone 2 minimum requirements, without the need for purge-pressurized enclosures.
Until recently, only a few small diesels have ever been adapted to operate free-standing in a Zone 2 environment, and these were extensively customized to suit particular applications. With this latest KHD development, it is now possible for Deutz 816 diesel engines in a variety of sizes and configurations with outputs ranging from 120 to 870 kw (163 to 1,180 bhp) to be operated safely in areas outside the protection of specially designed, purge-pressurized enclosures.
The Deutz 816 series is available as a package adapted for Zone 2, which calls for a maximum surface and gas temperature of 250 C.
Deutz has gone beyond this requirement, with a maximum temperature of 180 C.
Development of the 816 to Zone 2 standards was carried out in response to a growing demand from oil companies. Building a purgepressurized enclosure is costly, imposing a weight penalty and creating problems of accessibility to the engine.
In adapting the 816, Deutz started out with certain advantages.
The engine was developed originally for mining applications and meets strict West German regulations. The temperature of most of the engine surface was already well below the Zone 2 requirement, the problem of cooling being limited to the exhaust system.
Even in this respect some of the work had already been done, as the 816 had an option of watercooled exhaust manifolds and turbochargers.
KRUPP MaK DIESEL Circle 67 on Reader Service Card According to MaK, there are different ways to improve the total economy of a vessel's propulsion plant. Items that can be fully influenced by the engine maker are: reduce the specific fuel consumption; design the engines for the lowest grades of heavy fuels that will be available in the future; and provide heavy-fuel engines for a wide output range in order to generate auxiliary power on board ships with engines using the same low-grade heavy fuels burned in the main propulsion diesels.
MaK offers heavy-fuel engines in the power range from 740 to 9,000 kw (about 1,000 to 12,240 bhp). Each power demand can be covered by in-line engines with a minimum number of cylinders.
Developments to reduce fuel consumption were introduced for MaK's large-bore, four-stroke M601 engine with 580-mm bore and 600- mm stroke. Improvements in the past two years regarding optimizing injection and scavenging brought the specific fuel consumption of an 8M601 engine with an output of 8,000 kw (10,880 bhp) down to 125 grams per brake horsepower-hour. Reliability of the engine was not affected because the measure of increasing the firing pressure was not yet used.
Besides the reduction of the fuel consumption of all engines, MaK delivers small auxiliary engines in the power range of 740 kw (1,006 bhp) and above for so-called "onefuel" ships, where main and auxiliary engines both operate on unblended low-grade fuels such as CIMAC 12. Four such installations are now in operation, the first since 1981. Operating experiences are encouraging, and further orders have been received for 11 one-fuel ships with MaK main and auxiliary engines burning the same low-grade fuels.
Further improvements in economy are possible for the peripheral equipment, such as improvements in propulsion efficiency by means of low-speed propellers, and waste heat recovery by means of using exhaust gas and cooling water energy for generating electricity in turbogenerators.
M.A.N.-B&W DIESEL Circle 66 on Reader Service Card M.A.N.-B&W Diesel, as the world's largest designer of marine diesel engines, has successfully developed engines with the highest thermal efficiency available, while at the same time maintaining a very high level of service reliability.
With the introduction of the MC low-speed series, M.A.N.-B&W has brought the fuel consumption down to 118 grams per brake horsepower- hour, which, compared with the 156 g/bhph 10 years ago, means a reduction of about 25 percent. At the same time the corresponding revolutions of the direct-coupled propeller have been reduced from 114 rpm to 60 rpm, which has led to an increase in the propeller efficiency of 12-15 percent. These factors combined mean a total saving in the fuel oil consumption on propulsion engines alone of up to 40 percent.
Extensive research and development, coupled with M.A.N.-B&W's vast accumulated experience in medium-speed operation, has resulted in systematic optimization of the full line of the mediumspeed diesel program. All this latest diesel technology is also being applied to the new L58/64 engine (1,215 kw per cylinder at 450 rpm) that is scheduled for testing this year. Expected specific fuel oil consumption of this engine is 123 g/ bhph.
M.A.N.-B&W is committed to meet the challenges of a changing world of operating conditions and technology, to the benefit of the world's shipowners.
MTU OF NORTH AMERICA Circle 77 on Reader Service Card MTU of North America, Inc., is the American subsidiary of Motoren- und Turbinen-Union Friedrichshafen GmbH (MTU) of West Germany, which is owned jointly by Daimler-Benz and M.A.N. The U.S. company has devoted more than five years to building a sales and service organization that reflects the high standards of the MTU organization worldwide.
The MTU diesel engine line covers an output range from 440 to 10,000 bhp at speeds between 1,000 and 2,400 rpm. Basic design features common to the series are: V configuration, water cooling, exhaust gas turbocharging, and charge air cooling.
The model 20V 1163 TB 93 engine introduced in 1983 is evidence of MTU's continued success in its development program, which focuses on increasing engine power and power concentration, reducing fuel consumption throughout the entire speed range, extending operating range through higher pressures, and improving partialload characteristics.
The major obstacle to fulfilling these goals, which also include the use of lower quality, heavier fuels with lower cetane numbers and higher impurity levels, is that the individual requirements are inter- dependent and, therefore, require a common solution. MTU's solution is cylinder cutout, cylinder charge transfer, and sequential turbocharging; all three systems have been proven in actual service trials.
With the boost in power in the 1163 Series from 349 to 496 bhp per cylinder (an increase in mep from 305 to 426 psi), MTU's twostage turbocharging is also employed for the first time, in addition to the systems mentioned above. This allows overall engine dimensions to be kept almost constant, and results in a power to volume ratio of 11.7 bhp per cubic foot, and a weight to power ratio of 4.4 pounds per bhp with the 20V1163 producing 9,920 bhp.
Output of the 396 Series engines has also been increased. With a maximum rating of 2,570 bhp and a weight of 10,475 pounds, the 16V 396 penetrates a power range previously served only by larger, heavier engines.
MTU's marine diesels are designed for a wide range of commercial and naval applications.
These include continuous duty with a power range of 590 to 4,930 bhp for vessels with unlimited operating range and/or unrestricted continuous operation, and medium duty with a power range of 640 to 5,425 bhp for passenger vessels in seasonal service, patrol boats, and cruise engines for vessels with combined propulsion systems.
MWM-MURPHY Circle 98 on Reader Service Card In early 1983 Motoren-Werke Mannheim A.G. (MWM) announced an expansion of its U.S.
sales and service network aimed at marketing the company's higheroutput engine series in North America. The MWM-Murphy Large Bore Division, headquartered in Houston, has been organized to market MWM's 400 and 500 series multi-fuel engines.
The 400 series is a four-stroke, direct-injection design available in diesel oil, natural gas, dual fuel, intermediate, and heavy fuel versions.
There are three basic model classifications in the 400 series— the 440, the 441, and the newest 444. The 440 and 441 models have the same 9.06-inch bore, 10.6-inch stroke, and swept volume of 684 cubic inches per cylinder. The new 444 model has the same bore but the stroke has been increased to 12.6 inches, giving a displacement of 812 cubic inches per cylinder.
The longer-stroke 444 is available in in-line 6- and 8-cylinder turbocharged-intercooled models, and has an operating speed up to 750 rpm. It was designed for optimum performance on lower grade and heavy fuels up to 3,500 sec.
Redwood 1, which may be the norm in years to come. Redesign of the internal cooling circuit and new generation turbochargers has increased the overall efficiency of the basic engine design, producing an output significantly greater than 440 model with no detrimental effects on fuel consumption. For the introductory model 444, output on diesel fuel was 250 bhp per cylinder at 750 rpm—2,000 bhp for the 8-cylinder model.
Basic design features of the 400 series include individual cylinder heads with four valves per head in an overhead arrangement, and piston cooling on all turbochargedintercooled models. All models, both naturally aspirated and turbocharged- intercooled, are oilcooled.
The 500 series, the largest of the MWM product line, is divided into two separate engine families—the 510B and the 501. The 510B is comprised of four basic turbo- Ongoing laboratory; This advanced techno properties and contarr prescribes the dosage tives needed to neutra harmful effects. Emplc efficiently, the FOCUS can dramatically reduc maintenance and repa where chemical treatrr is the answer.
Learn more about lems of lowgrade fuel < and how Magnus Mari solving them. Send for full color brochure fully ing the FOCUS Progre charged-intercooled engines with a common bore of 13 inches and stroke of 14.2 inches. An in-line version is offered with six or eight cylinders and a V type with 12 or 16 cylinders. Like the 400 series, the 510B has been designed to operate on a variety of fuels, even the poorer grades with viscosity up to 3,500 sec. Redwood.
Design characteristics of the 500 family allow operating speeds between 600 and 750 rpm. The 510B has a swept volume of 1,879 cubic inches per cylinder and an output of 525 bhp per cylinder, up to 8,400 bhp for the 16-cylinder model operating on diesel fuel. Currently, only the 6- and 8-cylinder models are available for operation on dual fuel and natural gas; output at 750 rpm is 1,890 bhp for the 6-cylinder model and 2,515 bhp for the 8-cylinder unit.
The 501 model is available in a turbocharged-intercooled in-line version with six or eight cylinders.
Each has a bore of 14.2 inches and stroke of 17.7 inches; operating speed is between 428 and 514 rpm.
Designed for operation on diesel and poorer grades of fuel, output at 514 rpm is 2,475 bhp for the 6- cylinder model and 3,300 bhp for the 8-cylinder version.
ONAN Circle 91 on Reader Service Card The Onan Corporation of Minneapolis recently introduced the L317D-M and the L423D-M marine propulsion engines. With ratings of 43.5 bhp and 60 bhp at 3,600 rpm, and weights of 475 and 549 pounds, respectively, the latest Onan engines are part of a family that will eventually offer models with ratings up to 150 bhp.
With a weight-to-horsepower ratio of about 11:1, the four-cycle L317D-M engine has a displacement of 105 cubic inches. The L423D-M has a weight-to-horsepower ratio of about 9:1 with displacement of 140 cubic inches.
Both models have a common 3.5- inch bore and 3.62-inch stroke.
Onan has been a well-known supplier of marine machinery for more than 25 years. This experience has resulted in a number of features and options on the propulsion engines, including a marine cooling system, marine gear, marine alternator, and special mounting system.
OOSTERHUIS INDUSTRIES (MITSUBISHI) Circle 65 on Reader Service Card Oosterhuis Industries, Inc., marine engine distributor for Mitsubishi Heavy Industries America, Inc., has been marketing heavy fuel burning diesel engines for more than 20 years. Based on that long experience, the Oosterhuis firm feels that in the lower horsepower ranges and for inland vessels, blended fuel could be a better choice than heavy fuel oil.
Mitsubishi offers the 4-cycle SNMTK and the SU-MTK marine propulsion and generator diesels suitable for operating on diesel fuel and on blended fuel oils. The SN-MTK is available for propulsion in a power range from 400 to 1,500 bhp at 1,550 rpm, and operates satisfactorily on a blended fuel of 16 cSt at 86 F with a sulfur content of less than one percent by weight. A mix of 50 percent marine diesel of 4 cSt and 50 percent heavy fuel of 350 cSt could provide such a blend.
The SU-MTK is available for propulsion applications from 1,500 to 3,000 bhp at 1,200 rpm, and operates on a blend of 30 percent marine diesel oil and 70 percent heavy oil. Oosterhuis offers a blending unit that blends the proper quantities while taking fuel on board, making separate storage tanks and heating coils unnecessary.
When operating on blended fuel, a fuel oil separator is required, and depending on lube oil capacity, a lube oil separator is recommended.
Oosterhuis Industries, through its affiliated Marine Engineering, Inc., can supply and install the entire propulsion package from engines and reduction gears to oil separators, electric oil heaters, tailshafts, and propellers.
PANDEL INSTRUMENTS Circle 64 on Reader Service Card A computer-based fuel management system, the FMS-3, was introduced recently by Pandel Instruments, Inc. The . system compares the fuel burned versus the speed made for vessels in the 4,000-bhp range and up. It consists of two major components: flow and temperature sensing devices, and the main computer unit with the system display.
The FMS-3 monitors individual engine burns and vessel speed, and the computer calculates the fuel burned per mile of operation.
Performance charts for the individual vessel may then be constructed to allow operation at known efficiency levels. The system is configured to function with marine diesel engines using lowpressure fuel supply pumps and return fuel circuits. It has hardware and software correction factors for fuel heating during recycling; aeration of the return fuel, and flowmeter calibration.
Speed inputs to the FMS-3 come from either the vessel's on-board knot log or from the Pandel Channel- Scan"' remote depth sounder.
System outputs are displayed on a 12-inch CRT that is equipped with an amber display format that presents no degradation of night vision.
Display formats are readily changed in system software to meet any particular fleet requirements.
Several of these FMS-3 systems are now operating successfully on the inland waterways.
PENSKE G M POWER Circle 63 on Reader Service Card Penske GM Power, Inc. represents Detroit Diesel Allison and Electro-Motive Division products that have survived the test of time and consistently provided the kind of value and dependability that produces results. The company is authorized to carry all Detroit Diesel engines and also offers the EMD 645 Series.
The Penske-engineered Detroit Diesel 8V92TI, a high-performance marine power package, is a compact, heavy-duty engine with a horsepower-to-weight ratio of 6.4 pounds per shp, establishing a new standard for the industry.
The 8V-92TI marine propulsion engine was developed using only field-proven components and thoroughly tested by Penske's own dynamometer.
Today's Detroit Diesel and EMD engines incorporate the latest stateof- the-art design modifications, such as low smoke injectors, bypass blowers, high-output turbochargers, aftercoolers, and refined engine timing. More importantly, these features are incorporated into the reliable and affordable engine design that has gained worldwide recognition and offers unsurpassed application and standardization potential.
Penske field engineers are ready to survey equipment for refurbishment or replacement, train operators and technicians, and establish comprehensive preventive maintenance programs to guarantee optimum reliability and equipment life.
SACM Circle 92 on Reader Service Card SACM (Societe Alsacienne de Constructions Mecaniques) of France manufactures medium- and high-speed, four-stroke, direct injection diesel engines known for their lower specific fuel consumption and compact size. The company is represented in the U.S. by F.W. Donnelly Company of Houston.
For the offshore drilling and production industry, SACM is one of Europe's leading suppliers of diesel generator sets with continuous, 60-cycle ratings from 100 to 4,000 kw. These compact sets are in use on one of the world's largest semi-submersibles, the Dyvi Delta, and on the production platforms Statfjord B and Statfjord C.
SACM engines ranging from 100 to 8,400 bhp are in use throughout the world in a variety of commercial and military high-speed vessels.
These include the Bell-Halter BH 110 surface effect ship, the Westamarin catamaran, and SAR 33.
The French company is a leader in the development of reduced volumetric ratio (RVR), Hyperbar, and two-stage turbocharged engines that provide excellent powerto- weight ratios. The SACM 520 V12 S3 (Hyperbar) diesel has a top rating for fast patrol boats of 1,400 bhp at 2,500 rpm, and a dry weight with accessories and reduction gear of 7,480 pounds.
SACM is active in the development of intermediate fuel burning capabilities for its medium- and high-speed engines, with more than 13 years of experience with this type engine. For marine propulsion, these diesels range from 100 to 5,600 bhp, while for generator sets ratings from 100 to 3,600 kw are available.
SEAWORTHY SYSTEMS Circle 62 on Reader Service Card Seaworthy Systems, Inc. (formerly Seaworthy Engine Systems, Inc.) has prepared more than 100 energy audits on all types of vessels, many of which are older steamships operating in vastly different operating modes than their original design. In performing such audits, Seaworthy has found that many such vessels, because of their machinery and cycle arrangements, are operating at rates well off their economic optimum for present-day operating conditions.
As a result of these observations, some operators have reviewed their operations and performed, or had performed, detailed technical and economic evaluations of machinery and cycle arrangements.
In addition, some have also evaluated present fuel systems, auxiliary components, and operational profiles to identify and rank various options and modifications for improving and/or restoring the thermal and combustion efficiency.
While many of the modifications are basic and common knowledge, their application to a specific vessel must be evaluated based on the required investment and projected economic payback of the specific ship.
The average steamship is operating with a fuel bill of $3-6 million per year. A savings of 3 to 7 percent is often obtainable from the application of certain modifications.
It is generally understood that the less costly modifications will give the quickest paybacks, with others becoming economically attractive if extended operating life is projected.
SULZER Circle 60 on Reader Sen/ice Card The end of 1983 saw the commissioning of the first Sulzer RTA superlongstroke engines to be used for steam-to-diesel machinery conversions.
Both the 1,813-TEU cellular containership Remuera Bay of Overseas Containers Ltd., and C.Y. Tung's 2,300-TEU Oriental Educator have each been equipped with a 9-cylinder RTA76 engine resulting in considerable fuel cost savings.
The new RTA engine series is now the world's best-selling, uniflow- scavenged, low-speed engine design, with current orders for more than 370 engines to be manufactured by the worldwide Sulzer family, representing a total output of just over four million bhp. The RTA provides for better fuel economy than previous engine generations by virtue of its optimum combination of extremely low specific fuel consumption and lower rotational speeds, permitting higher propeller efficiencies at modest first cost. Moreover, the improved fuel economy has been achieved without compromising Sulzer traditional reliability on poor-quality fuel oils. Six cylinder bore sizes, ranging from 380 to 840 mm, cover an engine power range from 1,720 to 35,520 kw (2,320 to 48,360 bhp).
The conversion of the Remuera Bay, performed at IHI's Chita Yard in Japan, is of particular note because it involved remodeling the ship's afterbody from twin- to single- screw propulsion. The original steam plant had a combined output of 35,790 kw (48,660 shp) at 108 rpm. The new 9RTA76 diesel gives 21,780 kw (29,610 bhp) maximum continuous rating at 95 rpm, but the service speed is now only two knots less than before.
In the case of the Oriental Educator, and her two sister ships that are to be converted by the end of March and July this year, the single- screw steam turbine plant was originally rated for a maximum output of 27,850 kw (38,000 bhp) for 23.5 knots. In an effort to contain rising fuel costs, the ship had been slow-steaming at 19.5 knots with the service rating of 17,280 kw (23,500 bhp). The same speed is now maintained by the 9RTA76 at a service output of 18,510 kw (25,170 bhp) at 90 rpm, but with a 37 percent reduction in daily fuel consumption at that speed.
Sulzer low-speed diesel engines have already taken a major role in the wave of steam-to-diesel conversions of recent years. The large, fast containerships built in the early 1970s with powerful steam turbine plants had proved particularly vulnerable to the high fuel price levels of the past decade.
After initially slow-steaming, many were re-engined with more fuel-efficient diesel machinery. For example, 10 ships trading between Europe and the Far East were each repowered with twin 8RND90 diesels, reducing their fuel costs by some 30 percent.
SW DIESEL GULF (STORK WERKSPOOR) Circle 6 1 on Reader Service Card SW Diesel Gulf, Inc. specializes in heavy-duty, heavy fuel engines in the power range from 1,000 to 20,000 bhp; all are of the 4-stroke type. The engines have been designed to use low-grade fuel and can be operated reliably on highviscosity fuel containing 5 percent sulphur and 500 ppm vanadium.
This is possible because of the many special, heavy fuel features, such as deep-cooled valve seats to avoid hot corrosion by vanadium pentoxide/sodium compounds.
The most modern member of the Stork family is the SW280 design with an output of 400 bhp per cylinder at 1,000 rpm. This engine is particularly fuel economic, with a specific fuel consumption of 194 grams per kw-hour (0.315 pounds per horsepower-hour). This engine series runs reliably at 900 rpm on heavy fuel.
Because of long inspection intervals, maintenance costs are low when burning heavy fuel and are further reduced by the use of special hydraulic tools to loosen and tighten the nuts of important engine parts such as cylinder heads, main bearings, and big end bearings.
The use of these tools makes torque wrenches superfluous, and makes life for the crew and maintenance people a lot easier.
TRANSAMERICA DELAVAL Circle 59 on Reader Service Card The dramatic changes in marine power favoring slower-speed diesel engines offering more efficient operation on less expensive, heavy fuels presented technical criteria not at all new to Transamerica Delaval's Engine and Compressor Division. Unlike many of the foreign- built diesels whose "degraded fuel" experience is largely with straight-run residuals, Transamerica's Enterprise medium-speed engines have been burning a considerably lower quality, heavily cracked residual type oils for years.
The company's R4 diesels (450 rpm), and its recently introduced R5 units (514 rpm), have been evolved over the years with combustion systems that have the proper materials, systems techniques, and intensive cooling configurations to obtain the most efficient use of heavy fuels with minimum maintenance penalty.
Critical in heavy fuel operations are Enterprise design characteristics that discourage low-temperature sulphur corrosion, precisely control temperatures in the components exposed to the combustion gases of slow, hot-burning heavy fuels, and that avoid the need for performance degradation.
For example, cylinder heads are cast steel, providing the strength for the use of thin sections in critical areas to control thermal distortions.
The Enterprise four-valve head is designed for maximum air and exhaust flow efficiency. Steel piston crowns with nodular iron skirts permit thinner walls between the combustion chamber and "cocktail shaker" action of the cooling oil for reduced thermal stresses. Compression rings are chrome plated and specially profiled for long life on residual fuel.
Recent evolutionary developments that led to the Enterprise R5 diesel (mcr range, 3,600 to 12,200 bhp) have brought the company's medium-speed family 40 percent more horsepower per cylinder and per square foot of installation space; the latest in heavy fuel efficiency; 3.5 percent lower specific fuel consumption; and the versatility afloat that often gives the medium-speed unit a net operating cost advantage over its competitors.
VOLVO PENTA Circle 93 on Reader Service Card Volvo Penta offers a marine version, the TMD 120, of its 12-liter diesel engine. Specifically designed for use as the main propulsion engine in workboats and other craft, it is said to have high output in relation to weight and installed dimensions, low fuel consumption, and a high level of reliability.
The B version of the TMD 120 features advanced control of the injection and combustion processes, with new injectors that provide more rapid injection at higher pressure, and with decreased combustion delay. Together with efficient turbocharging and a combustion chamber of a new design, these features are said to yield considerable improvement in efficiency.
Other technical refinements in Volvo's 12-liter diesel include piston cooling, a hoseless seawater system with heat exchanger, and thermostat-controlled cooling of the engine block, cylinder heads, turbocharger, and exhaust manifold.
The Swedish company's diesel line includes 2-, 3-, 4-, and 6-cylinder engines covering 12 different models; some are equipped with turbochargers and others with both turbochargers and aftercoolers.
Additionally, Volvo offers twin engines driving through a single compound gear, providing a single shaft output from 336 to 580 shp.
This twin-engine/single-output package provides many advantages, including "take-home" capability on one engine.
The heavy-duty Volvo line in- eludes the model MD 120A, a 6- cylinder engine with maximum continuous rating of 168 bhp at 1,800 rpm, and the 6-cylinder TMD 120A with mcr of 260 bhp at 1,800 rpm.
WARTSILA DIESEL Circle 94 on Reader Service Card Wartsila Diesel, one of the world's leading manufacturers of medium-speed diesel engines, has three production plants: the Wartsila Vasa factory in Finland, the Trollhattan factory in Sweden, and the recently opened Wartsila Power Singapore in Singapore.
Wartsila's product development program focused on the design of diesel engines capable of both maximum economy and safe operation even in the most demanding applications. As a result, the company now produces two highstandard, medium-speed engines designed and developed from the very beginning to operate on the poorest quality fuel.
The Vasa 32 engine is well established in the world's marine market, and is installed as the main or auxiliary power source on a variety of ships. This engine, with its seven different cylinder versions—4R32, 8R32, 9R32, 12V32, 16V32, and 18V32—covers an output range from 1,820 to 8,350 bhp at 720 to 800 rpm. The Vasa 32 can operate on fuel with a viscosity up to 380 cSt.
The second of the company's heavy fuel engines is the Wartsila Vasa 22HF, said to be the smallest engine in the world developed exclusively to operate on heavy fuel.
The output range of the 22HF covers 720 to 3,480 bhp at 900 to 1,200 rpm. This engine is available in five different cylinder configurations— 4R22HF, 6R22HF, 8R22HF, 12V22HF, and 16V22HF—and can run on the same viscosity fuel as the Vasa 32, 380 cSt.
Main features of these engines are: starting, running, and stopping over the entire load range on heavy fuel without any limitations; heavy fuel operation with the same safety and reliability as when operating on distillate fuel; and all engines can run on the same type of heavy fuel.
The ability to burn heavy fuel successfully lies in a purpose-designed diesel engine and fuel-handling system. Wartsila's heavy fuel engines feature: increased preheating of the engine before starting, including jacket water, lube oil, charge air, fuel system on both the high- and low-pressure side, and fuel nozzles; increased filter capacity of both fuel oil and lube oil; higher temperature and improved insulation of the injection pump control system.
Since 1980 Wartsila Diesel has been represented in the U.S. by Wartsila Power Inc., headquartered near New Orleans, with branch offices in New York, Houston, and Seattle.
WAUKESHA Circle 78 on Reader Service Card Waukesha Engine Division's AT25 Series 250-mm bore, medium- speed diesels operate economically and efficiently on heavy fuels. These high-output engines, built under a license agreement with Sulzer Bros. Ltd., are available in 6- and 8-cylinder in-line and 12- and 16-cylinder V models with a power range from 1,260 to 4,800 bhp (941 to 3,581 kw) at 720 to 1,000 rpm. Enginator® electric generating systems are rated to 3,040 kw, 60 Hz at 900 rpm.
The AT25 was designed specifically with heavy fuel operation in mind. The bore-cooled cylinder head and two-part piston insure lower induced stresses and moderate valve seat temperatures. Compared with the double-bottom cylinder head design used for most engines of this type, deformations with the bore-cooled head are 2% times lower. In particular, this means greatly improved valve sealing conditions. Also, the use of valve rotators insures uniform temperature distribution, resulting in full-load valve seat temperatures of only 788 F (420 C)—important when running on heavy fuel.
Designed with a high degree of parts interchangeability, all pistons, piston rings, connecting rods, cylinder heads and liners, injection pumps, and nozzles are interchangeable among all AT25 models. Main bearings, camshaft segments, and piping components are common within the in-line and V configurations.
Features for ease of maintenance include quick-access covers for camshafts and main bearings, and a provision for quick removal of rocker arm covers for valve adjustments.
Water, lube oil, and fuel transfer pumps are located on the front of the engine for ease in maintenance. Hydraulic tensioning of main bearing studs and connecting rod studs is accomplished with specially designed tools to insure accurate loading of these critical joints.
WESTINGHOUSE Circle 95 on Reader Service Card Combustion trim control systems manufactured by Westinghouse Electric's Combustion Control Division are saving $168 a day in fuel costs aboard Moore McCormack Bulk Transport's 39,232-dwt tanker Mormacsun.
Each system installed on the ship's two boilers consists of a Westinghouse Hagan Model 211 heavyduty oxygen analyzer and a Model 1400 microprocessor-based oxygen trim controller.
Operating at an average speed of 15 knots, the 15,000-shp Mormacsun burns about 16,600 gallons of fuel oil per day. Prior to installation of the combustion control systems, the air-to-fuel ratio in the boilers was adjusted manually based on visual observation of flue gas and use of a hand-held flue gas analyzer. Though some excess air is necessary for smoke-free operation, the amount of oxygen in the flue gas is a good indication of combustion efficiency, as it is directly proportional to excess air.
Too much excess air results in dollar losses because extra fuel is burned to heat the excess; too little excess air increases costs because unburned fuel goes up the stack.
The systems aboard the Mormacsun have consistently controlled the excess oxygen at levels ranging from 2.5 to 3 percent, a reduction of at least 1 percent from previous operation. Mormac engineers believe a 1-percent reduction of excess oxygen produces fuel savings of at least three barrels of oil per day in each boiler.
Based on these calculations, Moore McCormack achieved a payback on the equipment alone in about eight months. Including the cost of installation, the payback on the total package was about 15 months.
Read REDUCING FUEL COSTS First In a Series-Propulsion Equipment in Pdf, Flash or Html5 edition of January 15, 1984 Maritime Reporter
Other stories from January 15, 1984 issue
Content
- Brown & Root Inc. Forms Joint Venture In Holland With Two Dutch Companies page: 5
- Bethlehem Steel Signs Licensing Agreement For Tension Moored Platforms page: 5
- New Bath Iron Works Repair Facility Opens In Portland page: 6
- Penske G M Power Head Discusses Service Support For Maritime Industry page: 6
- Jacobson Delivers Shipdocking Tug 'Chessie' To Chessie System page: 10
- Latest Europort Exhibition A "Resounding Success" page: 10
- Carmen Guide Appointed President Of Lake Shore —Malsack Named Chairman page: 12
- Mobile Marine Introduces Advanced-Design Workboat page: 12
- Financing Completed For U.S. Lines Containerships Building At Daewoo Yard page: 13
- Navidyne Unveils New INMARSAT Ship Terminal —Literature Available page: 13
- Indikon Introduces New Web Deflection Indicator —Literature Available page: 14
- T C S Industrial Appointed Distributor for NABRICO —Literature Available page: 14
- Joint SNAME, IME And NYPE Meeting Discusses Use of Inexpensive Fuels page: 16
- Michigan Wheel Awarded Navy Contract For Carrier And Oiler Propellers page: 18
- Seaworthy Engine Systems Shortens Corporate Name page: 18
- Joel Alper Appointed President Of COMSAT World Systems Division page: 18
- REDUCING FUEL COSTS First In a Series-Propulsion Equipment page: 20
- Esercizio Cantieri Launches Tug/Supply Vessel Of New Design page: 41
- NASSCO Begins Conversion Of First Maritime Pre-Positioning RO/RO page: 41
- New Marine Autopilots Introduced By Racal —Literature Available page: 42
- Steam Plant Optimization Topic At New York Port Engineers Meeting page: 42
- BIW Chief Engineer Addresses Northern New England ASNE page: 45
- Lifeboat Quick-Drop System Unveiled By SeaTek And MCR page: 45
- Scholarship For Panamanian Students At Kings Point Funded by Justin Bonanno page: 50
- O'Boyle Firm Appointed Exclusive U.S. Agent For Astilleros Espanoles page: 51