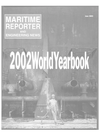
A Naval Architect's Look At Design Trends
Reading tea leaves on a boat underway is an exercise in frustration because just as the leaves start to settle, another wave comes along and changes the picture.
Similarly, trying to foresee trends in the marine industry. Just as you see things shaping up, a change occurs and the industry is re-shujfled. However I believe that I can discuss three particular trends that are part of our collective future.
Regulations The first of these is the fact that the marine industry will continue to see a growing body of regulations affecting how we design, build, and operate vessels.
Some examples of the alphabet soup that we must deal with include ADA, STCW, ISM, EPA, etc. These regulations are being created by organizations both within and outside of the marine industry. Many marine regulators such as the U.S. Coast Guard are increasingly relying upon other bodies such as the American National Standards Institute (ANSI), National Fire Protection Association (NFPA), and American Society for Testing of Materials (ASTM). Their purpose in doing so is to try and keep the regulations more current. However, this also can mean that the regulations are getting further away from our industry.
We have also seen a shift from prescriptive regulations to performancebased regulations. What does this mean to the industry? Let's look at some examples: • Prescriptive Regulation — "Each compartment must have two means of escape, one of which must be a pathway or ladder meeting regulation ABC, the other way be a vertical ladder on horizontal egress via a designated widow with minimum dimensions of X by Y." • Performance Based Regulation — "Demonstrate that there is a safe egress path from each compartment given the following hazard scenarios: fire, flooding, extreme heel and trim." The prescriptive regulation is more objective. It's easier to measure compliance.
The performance based regulation is more flexible but requires more effort by all parties (designer/builder/operator/ regulator). We have seen that both the U.S. Coast Guard and the International Maritime Organization (IMO) are increasingly working on risk-based approaches to regulations, which are clearly performance based. By introducing the notions of risk and associated consequences, the regulations are potentially more rational and objective. I fear however that the cost of demonstrating compliance to such risk based regulations will be expensive.
Increase in sophistication of systems The second trend that I see is the increasing sophistication of systems and equipment onboard vessels. Perhaps our future vessels will be "smart" with voice-activated systems, integrated command, control, and communication, and self-checking equipment to facilitate maintenance and improve reliability.
We are already seeing smart equipment as shown by two examples.
• Electronic combustion controls on diesel engines — improve power, reduce emissions, adapts to load/mission profiles.
• HVAC systems — Self adjusts to reflect time of day, season, handles dif- ferent latent and sensible heat loads, varies air volumes to suit occupancy.
Every technology has its flip side, however,. "Smart" equipment needs to be programmed just as your VCR needs to be programmed to record programs.
Just because you can program your VCR to receive TV programs two months in advance on alternate Tuesdays, how many of us need or want that capability?
Who remembers how to reprogram them when the power fails? We see the same challenges in these new sophisticated systems. As a firm, Elliott Bay Design Group has had to help customers with: • Programmable electronic circuit breakers that trip off-line for no apparent reason.
False readings from sensor affected by radio frequency interference from power circuits or from voltage spikes.
• Elevator controls where a loss of power causes the system to re-boot with a consequent loss of programming.
As an industry we need to carefully consider the benefits and potential problems that come with modern technology- Vessel Affordability The third trend is a little harder to define but is no less real. I believe that U.S. ship owners and shipyards will increase working together to make vessels more affordable. This means that the ship owners must become more knowledgeable about construction practices.
They need to understand the balance between labor costs and materials costs, the impact of scheduling on labor productivity, and how contract provisions such as quality standards can impact the shipyard overhead. For example, bulkheads and decks can be stiffened by bulb flats instead of angles.
The material cost is higher but coating systems are easier to apply so the coatings last longer. A proactive owner will understand the life cycle cost benefits that result from different construction techniques.
Smart owners will ask their designer and/or builder about where the dollars are in the vessel. Sometimes spending more money on a piece of equipment that is easier to install can result in a net saving. Does the yard have preferred suppliers for doors, electrical equipment, valves, etc.? Why do they prefer them and is there a savings to the customer?
Is the yard's standard detail for a handrail acceptable rather than the designer's approach? I think lhat more owners will ask questions and conduct a dialogue with the shipyards. Everyone will benefit.
The U.S. shipbuilding industry will also work smarter, not harder. On a recent contract for a fishing vessel we compared an overseas yard that could build the vessel with 40,000 labor hours vs. a U.S. yard that required 50,000 labor hours. This kind of gap will be closed as U.S. yards spend more effort on improving their production practices and the associated planning. For example: I recently visited a yard where they traditionally spent 60 labor hours to fit a bow wrapper plate with come-alongs, wedges, and trimming excess from the plate. After learning about line-heating methods they were able to fit a similar plate within 12 labor hours. The plate was cut neat and treated with line heating to take a numerically predicted shape.
Successful shipyards will adopt some new technologies and processes.
Technologies will include line heating, statistical accuracy control, 3-D product modeling, and product work breakdown structures. New processes will include a detailed build strategy, increased use of shipyard standards and specific vendor equipment, better control of schedule and material flow, and zone-by-stage construction.
At a recent meeting of the Passenger Vessel Association Sen. Trent Lott, (R-Miss.), expressed his opinion that the U.S. could be competitive in shipbuilding. We will do so if we continuously seek to improve our shipbuilding processes, benchmark ourselves against our international competitors and train our work forces to use the tools we have.
There you have my three trends. I think that they apply to all market sectors of the diverse and interesting marine industry. A common theme among them is communicating information and asking questions. At a seminar on regulations a speaker said, "You're either a player or a victim." Let's all be players and work together.
Read A Naval Architect's Look At Design Trends in Pdf, Flash or Html5 edition of June 2002 Maritime Reporter
Other stories from June 2002 issue
Content
- Bollinger To Acquire Halter Marine page: 6
- Bidding War Comes to an End page: 6
- Jotun And NOF Marine Coatings Join Forces page: 8
- Thunder Horse Will Get Wartsila Generators page: 10
- United Defense to Acquire United States Marine Repair page: 10
- New Order For MAN B&W Diesel ME-Engines page: 12
- Fares Al Salam Parts The Red Sea page: 14
- Redundancy The Next Watchword? page: 20
- Cargo Handling's New Force page: 22
- A Naval Architect's Look At Design Trends page: 24
- Conoco Leads The Way For GOM Shuttle Tankers page: 27
- Daewoo Shipbuilding To Build, Refit LNGs For Exmar page: 27
- Navy League Comes to NY for Centennial Celebration page: 28
- Prospects Abound, But Where's the Money? page: 32
- OPA '90 - The Oil Pollution Act of 1990 page: 33
- Container & RoRo Tonnage — Non-Contiguous Liner Trades page: 35
- Matson Signs $220M Contract With Kvaerner Philadelphia page: 38
- GL: Exporting German Precision page: 40
- World Shipbuilding to Fall Slightly page: 44
- Tanker Market is Solid page: 45
- Bergesen Releases 1Q Results page: 46
- OMI Announces 1Q Results page: 47
- MAN B&W Turbocharger Technology Unveiled page: 49
- Answering the Call from Above page: 50
- Thrane & Thrane Offers Capsat Fleet77 page: 53
- Crisis Management and the Integration of Vessel Tracking Technologies page: 60
- Rear Admiral Pluta Redefines Maritime Security page: 64
- Ship Graveyard page: 68
- Intertanko's Sustainable Challenge page: 72
- German Barging: Over the Divide page: 76
- Blohm+Voss: 125 Years Young page: 80
- Thordon Makes Inroads With COMPAC Shaft Bearing page: 90
- Halifax Lays Keel For First of Two OSV's page: 91
- Owners Approve White Rose Oilfield page: 91
- Voyage Data Recorders page: 92
- Titan Re-Floats IMaersk La Guaira page: 96
- Austal USA Enters Repair Market page: 96
- Maritime Industry Remembers Nealis page: 97