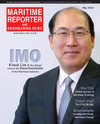
Cranes, Heavy Lift Shipping, Engineering and New Technologies
By Yahaya Sanusi, Deputy Head of Transport Engineering, AAL
Compared to new technologies, conventional engineering in shipping is a relatively simple science: computable and generally predictable. However, heavy lift shipping presents challenges that go far beyond what is required with standard unitized cargoes. The transportation of project cargoes - often highly valuable components of multi-billion-dollar projects - requires expert planning to ensure they are loaded and transported safely and efficiently.
Last year AAL shipped two giant cyclone vessels (22m x 11m x 10m and weighing over 500mt each) to Petronas’ $27 billion RAPID project in Malaysia. For such a project it’s essential to gauge the ratio between the weight of cargo to crane capacity, and also the displacement of the ship. Once these ratios approach unity and especially if they are combined with many other cargoes, detailed planning is required to have an optimal solution. In this respect the two cyclone vessels presented a number of challenges. They were loaded onto the AAL Fremantle, one of our 19,000dwt S-Class vessels, in Mailiao, Taiwan, using its combined 700mt cranes to safely lift and stow the cargo into one of its three giant, box shaped holds and weather deck respectively. Two weeks later they were safely delivered.
The Human Element
AAL believes the most important factor in the safe loading of complex cargoes is not the specification of our equipment - important though this is - but the human element.
Lifting equipment can be broadly similar across the heavy lift industry, at least amongst specialist carriers. A high-quality carrier should invest in effective engineering equipment when lifting, loading, securing, transporting and unloading the extraordinary cargoes seen in the multipurpose sector, but it is the human element that separates one cargo carrier from the next, especially when a few centimetres can make all the difference, or when it comes to the effective use of vessel to give maximum intake.
AAL operates one of the youngest and most advanced fleets in the sector. AAL’s 21 multipurpose vessels offer superior infrastructure with side-mounted heavy lift cranes, large and even deck space, removable and height-adjustable ‘tween decks, large box shaped cargo holds with independent dehumidifiers, strengthened tank tops as well as appropriate lifting and lashing equipment. With our mix of 31,000 dwt A-Class, 19,000 dwt S-Class and 33,000 dwt W-Class vessels, we also lead the ‘Mega MPP’ vessel segment (30,000+ dwt). However, the key to success is in-house technical and engineering team.
New Tech: Theory and Reality
The heavy lift shipping industry has slowly implemented many new technologies in many aspects of their work. But if one looks at the technical aspect, there can be discrepancies between the theory and the reality.
While new technologies such as 3D-simulation, finite-element analysis and motion response analysis are slowly working their way into the daily operations of multipurpose shipping, understanding of how these technologies contribute to the safe handling of project cargoes fluctuates across the industry. In such cases engineering capacity can be lost in trying to implement these complex calculations, without comprehension of the benefits. Multipurpose shipping is already a highly specialized sector and new technologies must be thoroughly understood before their implementation disrupts the accepted standard. Continuing without this can result in additional costs and resources, and may also affect the safety of the operation.
On the other hand, as more general cargo carriers muscle in on the multipurpose sector, we’re seeing the industry’s best practice methods become diluted. Crews of general cargo carriers may not necessarily have the right knowledge and experience to safely transport the multi-billion-dollar cargoes common to the industry. For instance, some such crews and vessels might stick to the 1 m initial stability during the lift, as opposed to considering other relevant stability criteria, or confuse the requirements between damage and intact stabilities.
The new IMO Resolution MSC.415(97) is an important milestone in heavy lift shipping. When it takes effect in January 2020, for the first time there will be international legislation setting stability criteria for lifting procedures, so it is important for crews transporting project cargoes to understand and adhere to best practice methods and calculations.
Emerging technologies
Exciting technological developments lie ahead. Just like autonomous cars are now being tested on our roads, the first autonomous ship will be tested in 2019. Today conventional ships with deckhouse aft are limited when transporting tall cargo in case visibility from the command bridge is impaired. But the authorities must rethink. As long as safety standards are met, surely, they must accept new technologies such as proximity sensors and infra-red cameras to replace the naked eye.
There are other interesting technologies, such as Big Data Analytics, Virtual Reality, Expert Systems or Artificial Intelligence. All have hardly touched our industry yet, but I am sure they will find applications in the future, along with the already available 3-D simulation and, to a certain aspect, intelligent stowage planning.
The engineering tools and methodologies used in shipping have remained relatively the same for the last 15 years. If shipping is to keep step with technology, then we need to evolve, including our physical tools. However, whilst the equipment used is important, investment in the right people is still the key to maximising the value of a carrier’s engineering capabilities. It takes time to train young people to become experts. If we want to maintain or even push up the standard we must be prepared to invest to keep the industry interesting and attractive for young and brilliant people to join the industry.
Yahaya is Deputy Head of Transport Engineering at AAL, and has worked in shipping for more than two decades. Prior to joining AAL, Yahaya worked at Thyssen Nordseewerke shipyard, Macor Neptune, and Beluga Shipping.
Read Cranes, Heavy Lift Shipping, Engineering and New Technologies in Pdf, Flash or Html5 edition of May 2018 Maritime Reporter
Other stories from May 2018 issue
Content
- Scrapping Risks page: 12
- Ship Tech: U.S. Coast Guard R&D Center page: 12
- Cranes, Heavy Lift Shipping, Engineering and New Technologies page: 14
- Riding Shipping's Digital Wave page: 16
- Interview: Darren Larkins - CEO, SSI page: 18
- Interview: Volvo Penta's Ron Huibers page: 24
- German Shipowners Get Back to Basics page: 26
- LNG is the Bridge to ‘Zero Emissions’ Shipping page: 30
- Interview: Kitack Lim, Secretary-General, IMO page: 34
- New Maritime Fuel Rules: Scrubber Solutions page: 42
- Kouroumplis: Greece Continues to Pace the Global Shipping Sector page: 46
- Skentelbery Drives Grand Bahama Shipyard page: 54
- Fuels, Lubricants & Green Marine page: 60
- MarTID: A New Tool for Maritime Training Professionals page: 66