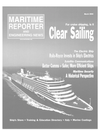
Metal Fusion Helps Stop Corrosion
New advances in metal fusion technology produce a metalized coating with no porosity, which can be applied at rates similar to those achieved by airless painting practices. The substrate temperature does not affect the process, and there is no curing time. The competitive process results in extremely long t e rm near permanent corrosion protection, which is designed t o be competitive in price with conventional corrosion systems. High speed metalizing of a variety of substrates can be accomplished rapidly under harsh field conditions. As there is no cure time required for the process, which can be used to apply up to 35 mils with only one coat, the application time is often much reduced f r om a conventional corrosion prevention system. Pitted steel and corroded rivets can be filled with metal easily, thereby eliminating welding and steel replacement. Rivet seams on oceangoing vessels were sealed and operated for years through difficult weather conditions without leaking after quickly metalizing corroded areas. Pure copper, as opposed to leaching cuprous oxide, can be permanently bonded to steel, wood and fiberglass providing permanent protection against marine fouling. The process throws plasma or molten metal against the substrate at high velocities, which melt the peaks of steel substrates forming an alloy bond at the surface.
This produces very high adhesion and tensile strength when compared with conventional systems. The metal alloy which forms on the surface is impervious to air and water inclusions, and when zinc or aluminum are applied, provide cathodic protection as well as a total oxygen and moisture barrier. The new advanced technique produces a film of metal on the substrate that will not undercut, has no porosity, and less than one percent air inclusions in the coating. Most metals that can be put into wire f o rm can be applied. The process has design approval from ABS, and has been approved for use in chemical tank linings by the USCG. The Federal Highway Administration endorses metalizing for bridges with no topcoat, or with a single cosmetic coat only. Some marine applications include using pure aluminum for a near permanent non-skid, which has very high abrasion, and wear characteristics when compared with conventional materials. Aluminum non-skid can even be steam cleaned when contamination f r om hydraulic fluids, grease and fuel are encountered. Applying stainless to bowthruster tunnels helps to eliminate cavitation problems, which can erode carbon steel quickly. Application of zinc to ballast areas turns the entire tank into a zinc anode, and zinc can be applied to tightly adhering rust providing a hard coating without surface prep. As there are no chemicals, curing time, or solvents involved in metalizing, a variety of cosmetic topcoats can be applied directly to the metalized surface as soon as it is applied. For more information Circle 44 on Reader Service Card
Other stories from March 2004 issue
Content
- Bollinger Delivers Tidewater Supply Boat Jonathan Rozier page: 8
- World's Largest Dry Transport Vessel Delivered page: 10
- Port security: A Historical Perspective page: 12
- Delayed Enforcement of Change to "Shipper" Element page: 16
- MTSA: Another Key Layer of Port Security page: 17
- When Security is Made Simple page: 20
- Business Milestone for Vietnam page: 24
- "Made in Germany1 — a New High page: 24
- Miracle on Ice page: 26
- New President & CEO at Kvaerner Masa-Yards page: 28
- He's No Regular Joe page: 30
- Cruise Passenger Travel Grows 8 Percent; New York and Galveston Post Big Gains page: 32
- HAL's Vista Sails with ROCHEM Technology page: 33
- Royal Caribbean Takes Mariner of the Seas page: 34
- NorseMerchant Ferries Plans Service Upgrade page: 37
- Grimaldi Continues Fast Track Expansion page: 38
- Costa Places $450m Order With Fincantieri page: 40
- Losing ontact... Not an Option page: 44
- Ship Security Alert Systems (SSAS) page: 50
- GALILEO Lifts Off page: 52
- Icebreaker Uses Satellite to Break Through Communications Barriers page: 55
- Cellular Fixed Wireless Helps Deliver Mercy page: 57
- Homing in on Ships' Electrics page: 58
- Shipconstructor Chosen as Standard page: 61
- Contract for New Product Tanker Design page: 62
- BollFilter: 50 Years of Success and Counting page: 65
- The Corrosion Control Challenge page: 66
- Nippon Paint Restructures page: 69
- Metal Fusion Helps Stop Corrosion page: 69
- Maritime Security Professional Training page: 72
- Training the Trainer to Keep Knowledge Afloat page: 74