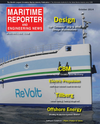
Condition Based Monitoring & Saving Cash
Fuel Optimization: Fleet Management Tools Cut Fuel Consumption, Boost Reliabilty
Profitability in shipping goes up and down in waves. 2012 wasn’t too bad, with annual operating costs shrinking by 1.8% on average versus 2011, when average costs rose 2.1%, but 2013 weighed anchor in the losses column for many. And 2014? So far the waters are choppy, with the overall mood up in May but dipping down in the quarter that ended in August, according to Moore Stephen’s quarterly Shipping Confidence Survey.
Much of what worries the industry concerns issues over which it has little to no control – oversupply, global political instability, private equity investments, environmental regulations, mob-backed piracy on the high seas and the perennial winner, rising fuel costs, all of which conspire to drive up operating costs and push down profits. It’s a surefire recipe for pessimism and uncertainty.
“The slight decrease in confidence ... coincides with deterioration in the political situation in areas of the Middle East and Ukraine. Shipping operates on a global stage, and must inevitably be affected by international events,” said Moore Stephen partner Richard Greiner at the release of his August report. He added that operations costs and regulatory compliance are also a continuing cause for concern among owners and operators.
All that gloom and doom could be paralyzing, leading ship owners to circle the fleet and drop anchors until the iffy market blows over. But that’s not how you win at this game, and it’s certainly not a strategy for making money, or for that matter, keeping your budget on an even keel.
The smart, and ultimately successful marine operation looks for what can be controlled, and then takes aggressive action to manage those variables no matter how small a savings it may appear to reap.
Get In The Game
“At the end of the year, a lot of half percentages saved [end up] equaling a lot of percentages in total,” says Jörgen Mansnerus, vice president, marine management, for Bore, Ltd. With six ships already running NAPA fleet management software, he estimates that Bore is seeing an ROI “in the region of 5%,” more or less, on each ship. “ROI is a year, a year and a half max.” Over at American Roll-On Roll-Off Carrier (ARC), Fred Finger, vice president of operations, is seeing small tweaks, such as a nominal change in arrival departure time across 35 voyages a year making “huge changes in fuel costs, saving hundreds of thousands of dollars.”
And then there are the big numbers. In another case, optimization efforts during a trial on one ship uncovered sensor data showing an unusually worn piece of equipment. Focusing on that one piece, ARC looked out across its fleet and took careful measurements to see if the same problem existed elsewhere. It did – on five out of six ships. Addressing the issue resulted in a cool half a million dollar savings in fuel optimization, according to Finger. In fact, even on a trial basis, he estimates the fuel savings the company has achieved so far “significantly outstrip the cost of what we’ve put into place.”
These examples are just the tip of the iceberg. There is lot on board ship that can be monitored and actively controlled to varying degrees to achieve savings: fuel and lubricant consumption, energy efficiency, equipment maintenance, data gathering for regulatory compliance and port paperwork, administrative and crew workloads, cargo loading and weight, trim optimization, and emissions, ballast and other environmental issues ad nauseum.
“The amount of data that is processed nowadays was impossible just a few years ago,” observes Hendrik Bruhns, CEO, Herbert-ABS Software Solutions, a provider of operations management applications.
Smart operators also realize that while they can’t control the weather or the waterway, any more than they can control the river of regulation, they can control and plan their response to those variables.
It’s all about scrabbling for savings wherever you can find them. Profit margins are what keep shipping lines afloat, and that is best secured by running a lot of tight ships. And If you’re going to run a tight, compliant ship, it helps to monitor and track every turn of every piston, crank and wheel; every drop of fuel, ballast and waste; every change in the wind, current and speed, and a million things in between. And if you want to do all that, you can’t rely on the observations and record-keeping of an ever shrinking, ever busier, fat-fingered crew. No, you’re going to need help, primarily in the form of fleet and operations management applications fed by automated data sensor feeds.
The goal here is not just to track and modify where needed, but, as Helm, a maker of vessel enterprise management and operations software, likes to say, your solution needs to be “the information bridge between your departments, your vessels and your customer.” Not to mention, a direct line to the savings column.
Automating the data stream is a no brainer. No human can possibly track and count every little sensor blip or degree of change (and do it accurately every time). As Bore’s Mansnerus remind us, “If wrong input, wrong output.” Fortunately, there is no shortage of products that can handle those chores efficiently and accurately.
Classes of Management Tools
Rob Bradenham, General Manager of ESRG, developers of OstiaEdge, a data analytics platform that helps users to make decisions about fuel, energy, operation and maintenance, divides the industry into two broad categories:
* Traditional fleet management applications, which act like “marine-focused ERP systems” with a strong focus on managing maintenance. He said they’ll handle parts orders, maintenance crew scheduling, payroll, and track noon reports etc., often based on manually input data. “They are like a marine version of SAP.”
* Data analytics, which are software platforms that connect to a variety of on board and on shore sensors and various ship systems and analyze automated data feeds in a variety of different ways using different techniques.
Bruhns would probably re-label what Bradenham calls traditional fleet management, as operations management. In his view, the latter looks at daily operations, such as trim, stability and load management, crew workload and safety issues. He characterizes fleet management in general as being more concerned with what drives fuel consumption and the overall position of the entire fleet.
Both executives concede there is a lot of overlap between the two areas. Muddying the waters more, says Bradenham, is that applications in both categories vary in terms of their depth. For example, in the data analytics camp, some applications provide data transparency, enabling users to use the data and pipe some ashore, but don’t do much beyond showing the available data. At the other end of the scale are products that use a variety of analytics, from simple trending to complex algorithms and different predictive and prognostic technologies, to show users different outcomes based on changes they could make.
Needless to say, the application packaging options are many, ranging from suites offering “complete” coverage to independent tools and modules that can be purchased separately to monitor specific equipment and issues. Figuring out which way to go can be daunting.
The trick of it all, says ESRG’s Bradenham, is realizing that the starting point for a fleet’s data management and optimization strategy, isn’t the project launch. It’s not even the installation or the selection of the package or modules. It’s talking about what it is you want to do, and figuring out what you have already in place, by doing what he likes to call a “Gap Analysis.” It also involves laying out a technology investment strategy that will meet the needs of all stakeholders. “We often see ship owners making an investment for one stakeholder, what we call ‘buying in silos.’”
Bore’s Mansnerus points out, however, that it’s hard to know you really want, and how you want it presented, until you’ve played with the application for a bit. That means ship operators need to keep future growth and customizability in mind when selecting packages, so changes can be made as painlessly, and as cheaply as possible, down the road. Because the one thing everyone can agree on is that there will always be more changes coming down the road.
What Ship Operators Really, Really Want
Containing, lowering and optimizing fuel consumption is job number one at many companies, particularly within the cargo-carrying global fleet of tankers, containers, RoRos and bulk carriers. “Owned by one, often operated by another, fuel consumption is the overriding concern,” says Bradenham. As is monitoring for fuel theft in some areas of the world.
Another driver, he said, for these owners is growing pressure from customers like the oil and gas companies, which are starting to demand transparency into fuel consumption rates, and how vessels are being operated.
Reliability and driving down the cost of down time rules the day for another industry sector – offshore support vessels such as tugs, defense vessels and even cruise ships. “The cost of downtime for a lot of these segments is huge,” said Bradenham. Take platform support vessels, which have fairly high daily charter rates. If they can’t deliver the vessel every day under the terms the contract states, they could lose all or part of that daily rate, which Bradenham says could be $20,000 to $40,000 a day. “If the vessel is down, that revenue is not coming back to the owner.” This means heading off maintenance issues is key. These clients are seeking a state of what the Navy calls “maximum readiness.” Even so, fuel prices affect everyone.
When the industry goes to 0.1% sulfur content in fuel in 2015, the price of fuel is going to go up dramatically, says Finger, so everyone is going to want to operate their vessels as efficiently as possible. “A 1% savings this year could be a 2% or 2.5% savings next year.”
It’s relatively easy to measure the ROI on an investment in fuel consumption tracking, but maintenance is trickier, because the avoidance of a failure isn’t something that was in the budget, and it’s not going to boost a bottom line. And yet, it’s not hard to calculate the fallout from a system or equipment failure, were it to happen.
Bruhns estimates there is something like 80,000 ships in service that were built for a different fuel price then they are operating in today. “These ships were designed with a higher focus on increasing the amount of cargo they could carry, and a lesser focus than you need nowadays on fuel consumption.” They might use 20% more fuel than a vessel designed after fuel prices skyrocketed, he estimates, adding that fuel can come to a third of total operating expenses. “[For them] the only way to keep profitable and be able to operate in a competitive environment is to continue retroactive methods for minimizing fuel consumption,” like, for example, trim and draft optimization. Otherwise, he said, “Ships use so much fuel that if it becomes too expensive, and you can’t compete, it’ll put you into bankruptcy.”
There are many ways in which to tackle this beast. From fine-tuning HVAC systems (See related story, page 50), to cargo load optimization, breaking routes into definable legs and tinkering with speed and course per each leg, to knowing when to clean the hull and maintain the engines, and on and on. The options are legion. “American Presidents Line used our software for its whole U.S. container fleet to optimize loading vessels for fuel savings,” says Bruhns. “They reported significant fuel savings” as a result. Optimizing the loading and unloading sequence of a vessel also helps to minimize time in port, which has a large cost implication of its own, while also making sure the vessel is not stressed and design limits are met so that the vessel stays safe. And optimizing the distribution of cargo enables the back office to know whether an offered load can be carried. “What-if scenarios are a big part of the software, letting companies plan the next load while carrying one,” he said.
“What-ifs” are a big part of voyage optimization systems, too. Mansnerus’ NAPA installation not only lets him see arrival and departure times tracked against fuel consumption, but built-in voyage optimization allows the company to see what a slight change in scheduling might mean in euros or dollars’ worth of consumption.
Slight changes in schedule or RPMs, for example slow steaming, can also have “unintended consequences” that could wipe out any gains. “You may optimize fuel consumption but find you’ve done it at the cost of creating a more frequent failure rate for your equipment,” cautions Finger.
There’s a third issue for owners and operators, and that’s compliance with a boatload of environmental regulations, such as SEEMP requirements and emissions tracking. There are lots of applications coming to market to address those needs, but the big issue for many ship owners is what investment should they make, and what will they be required to do.
Separate from the issues driving fleet management and operation software purchases, is what users are looking for from those vendors.
Keep Your Hands Off That Data
For some users, like Christopher Rodenhurst, USCG (ret), Fleet Manager for APL Maritime, Ltd., one-stop shopping and minimal human intervention is key. “We use a suite provided by different vendors, and as much as possible the designs are meant to be integrated, and we are shooting for non-human interaction.”
In APL’s case, he explained, the company’s mixed of applications has optimal trim software talking to the loading program; while optimal routing (weather), ship reporting (e.g. noon reports) are fed into a web-based Fleet Manager application that tracks the vessels, including fuel consumption, current and predicted weather, and also can provide MARPOL VI (Air Quality) documentation for SEEMP. Purchasing software for the vessels talks to APL’s financial software, and tracks maintenance crewing and payroll.
“The bottom line: I like one-stop shopping so most of the data ends up in one spot and is query ready. I do not use management software that is not willing to expand or talk to other vendors that have a piece that will make a viable product if they combined their efforts,” he adds.
It’s not hard to understand Rodenhurst’s position when you hear the voice of experience from Mansnerus. “The one thing you have to remember is that the software is only one third of the actual price in the end. There’s attaching the interfaces [the installation] and the need to do training.” Bore uses a suite of products from NAPA, and spent most of 2012 in a nine-month trial that proved to be “very extensive.” So the more integration issues that crop up between applications with proprietary code, from different suppliers, the more costly a project could become.
And this is on top of a certain level of customization that is already on the table, given that no two ships are alike – even if they are the same model made by the same ship yard – and given that the management software must interface with an array of systems and sensors that can vary from ship to ship. Since its 2012 trial, Bore has rolled out its fleet management system across five vessels, with plans to extend it to three more. “Each ship is individual,” with different ages, brands of systems and levels of automation, Mansnerus says. “You need to do the project and planning for each ship, it’s almost like a different installation each time,” he added.
For obvious reasons, one of his criterions is configurability. ESRG”s Bradenham cautions, however, that users want to take care that whatever they do, it doesn’t require the services of a software developer. “It would be prohibitively expensive.”
One of Bore’s other primary requests to NAPA was for a less than a 1% data error rate, with no hiccups when going through data transfer or sensors, and it has achieved that goal.
ARC is almost at the end of its initial one-ship evaluation phase for a package from ESRG, where a major goal involved replacing manual inputs with automatic data feeds.
Retrofitting Middle-Aged Ships
Eliminating manual data entry and the shadow of human error is a major issue, particularly where it involves the need to retrofit what Finger calls “middle-aged tonnage” with the sensors needed to enable automated data collection. The cost to do this can range from a few hundred to tens of thousands of dollars.
“The challenge for us is that there isn’t a lot of digital information already built into our vessels. Anything we do, we’re probably going to have to change at least the interface and likely sensor as well, to get the digital output we need to put into the system to analyze performance. It’s why we’re doing this on one ship first,” says Finger.
It’s also why Finger will only go so far with his existing fleet. It’s a delicate balance. “I have to take into account that we’re retrofitting to optimize the back third of lifespan for these ships, more or less.” Amortizing over 10 years is a relatively short window, he noted, adding that it probably isn’t worth it to spend a huge amount of money on his aging fleet. “We’re looking at this differently than someone with a new build coming out.”
ESRG tells clients to do a quick survey of what they’d got onboard, noting that often owners have no idea what they have installed and to what extent. “There are creative ways to think about data, you don’t always need the brand new, shiniest sensor; sometimes another sensor on board can be used as a proxy,” says Bradenham. He tells companies they don’t need do everything at once, to start uploading data from the sensors they have in place into the new applications and to then grow their automated data collection efforts from there.
The automated part is critical, not just for the sake of “pure” data collection, and the ability to feed the collected information into customized reports that will better enable decisions designed to optimize operations, but also from a personnel perspective.
Crews today are stretched in multiple directions beyond just ordinary seafaring duties.
Add in the growing demand to collect data for input into compliance reports, and a major goal of many ship owner/operators has become lessening the administrative burden on the crew, most especially ship officers.
Bore is hoping to reduce the administrative workload for its officers by 50% by moving to automated logs and report generation as much as possible.
ARC moved to install ECDIS on its entire fleet early, in great part because it is working toward creating a paperless system. “Ship officers spend an inordinate amount of time updating and maintaining charts. We want to free them up to do a lot of other things,” says Finger. It’s the same reason he wants to automate the Noon Report, which at minimum requires the involvement every day of the captain, chief engineer and the third mate on watch, and eliminate as much of the “white noise” from regulatory requirements as possible.
“The more time that can be spent on work that has to be done, the less waste from that perspective. We don’t want the crew doing things that don’t add value, so more we can automate, the better,” he added.
This in turn indirectly contributes to the objective behind SEEMP: freeing up crew to do other tasks, lessening the likelihood of their either having to work extra hours, or of tasks not getting done on time, leading to a more rested, refreshed crew, and a better atmosphere on board, says Bruhns.
In his view, this also leads to better safety at sea. “You can see by collision and other incidents that the accident rates have come down.”
Another personnel issue concerns ship management and long-standing “culture” norms.
If The Captain Isn’t Happy,
No One is Happy
“The biggest expectation we see from clients is that, ‘We’ll be able to make better, more data-driven decisions,’ as opposed to, ‘well, this is the way we’ve always done it.’ There is definitely a culture change issue here; the technology is the easier part of this,” claimed Bradenham.
“In the old days, the Captain was next to God on board. But now it is easier to convince people that they have to operate in a different manner to find the ship energy savings,” says Mansnerus . “It was hard without facts to talk to them. They’d say, ‘I know – I’ve been here for 20 years.’ But now we have a system with proven facts that it pays to handle the ship a little bit differently,” he added.
“The captains need to buy in this. If they don’t, it’s a fail,” agreed Finger.
Also standing in the way of efficient data collection are parallel systems making multiple entries of the same data, just in different forms or formats, often in programs that are not connected to each other, says Herbert’s Bruhns. This is redundancy that has to be ferreted out as part of the planning for a successful data management scheme.
Customers also don’t realize that better information won’t necessarily naturally fit into its business processes, such as the maintenance planning process or route scheduling.
According to ESRG, companies need the right data at the right time, but they also need the right person who can incorporate the improved data into the company’s back office programs.
There are many next steps in the evolution of fleet and operations management software – more openness, more plug- and-play, easier automation of basic reports to cut administrative workloads, more connections to non-industry communication standards, greater transparency – even development of a common system into which all data can be fed and then utilized by a variety of systems.
One possibility that particularly stands out has the potential to change the game entirely by bringing everything back to the drawing board – for ship design that is.
Ships are often built to the lowest cost possible, and they are built in traditional shipyards for very conservative clients. The biggest cost drivers today are the steel plating, type of engine and other heavy equipment.
What vendors, and some fleet owners and operators would like to see is a new build process that puts a greater emphasis on defining the technical framework up front, and mandating certain requirements. “If you do it up front, the vendor will provide it as part of the response to the RFP, often at no added cost,” claims Bradenham.
Herbert’s Bruhns says it is already happening.
The software is bought by the ship yard, which gives the vendor the data they need to set the up the package, which is then installed and ready to go once the ship goes into service.
From a user perspective, the potential of this approach to eliminate a great deal of the initial setup stages they now have to slog through, and the ability to skip right over retrofitting issues and cost, means that next generation of ships will likely be the one to move fleet and operations management efforts from the purview of bigger fleets into the main stream, where the hunt for ever greater performance optimization and cost-cutting will become as second nature to the crew as electronic navigation is today.
(As published in the October 2014 edition of Maritime Reporter & Engineering News - http://magazines.marinelink.com/Magazines/MaritimeReporter)
Read Condition Based Monitoring & Saving Cash in Pdf, Flash or Html5 edition of October 2014 Maritime Reporter
Other stories from October 2014 issue
Content
- They Said It ... Paul N. Jaenichen, U.S. Maritime Administrator page: 11
- Cutter Suction Dredge CSD500 from Damen page: 18
- Quantitative Risk Analysis for LNG Terminals page: 20
- Offshore Supply Vessels: The U.S. Can Compete page: 22
- New Solutions for Electric Ship Propulsion page: 24
- Classic Design with Tomas Tillberg page: 28
- Innovative Enviroship Concept Wins Big page: 30
- Design (R)Evolutions page: 32
- Condition Based Monitoring & Saving Cash page: 38
- HVAC Systems: The Stealthy Drain on Energy Efficiency page: 50
- What’s New in Floating Production? page: 52
- SSI Releases ShipConstructor 2015 page: 54
- SENER Releases FORAN V70R3.0 page: 56
- MAN Diesel & Turbo Debuts New High-Speed Engine page: 58
- VULKAN Couplings Debuts New Products page: 59
- Cat Unveils MaK M 25 E Platform page: 60
- ZF Marine Debuts ZF W10000 Transmission page: 61
- Wärtsilä’s New CPP System page: 61
- Hatz Presents New Engine Concept Study page: 62
- Schottel Shifts Focus Offshore at SMM 2014 page: 62
- Wärtsilä’s LNGPac: AIP from DNV GL page: 63
- GreenSteam Optimizer on Display page: 63
- Leistritz Debuts Three New Pumps page: 64
- Van Heck Advances Dredging Innovation page: 65
- Georg Fischer Piping DWV Fittings page: 65
- Bestobell Extends Valve Range page: 65
- Teekay Couplings Plastlock Pipe Coupling page: 66
- W&O Actuated Valve Solution for Vigorous page: 66
- Alfa Laval Launches PureSOx 2.0 page: 67
- Meet the Transas T-Bridge page: 68
- New Waste Energy Converter from Calnetix page: 68
- GAC’s EnvironHull HullWiper on Display page: 68
- BMT Showcases Monitoring Portfolio page: 68
- GEA’s CatFineMaster Debuts at SMM page: 70
- Engine Supervision and Management Software page: 70
- GPS-controlled Food Waste Discharge page: 70
- New Raytheon Anschütz Navigation Radar page: 70
- Raytheon Anschütz ShipGuard page: 71
- GNS Launches First VMS page: 71
- Revamped XChange page: 71
- GEA Heat Exchangers page: 71
- WR On-stack Scrubber Emission Monitor page: 71
- Improved Controller for Rexroth AHC page: 71
- NavStation Launched at SMM page: 71
- Wild Well’s Subsea Capping Stack page: 71
- Kelvin Hughes Product Range Expands page: 71