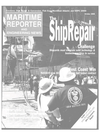
U.S. Navy Keeps Ship-Shape With Software
The Naval Surface Warfare Center uses Adams software to simulate USN ship hull and deck equipment. The technology is used for conceptualization and design-for-manufacturability simulations. As a result, design cycles have been slashed by 50%.
Hull and deck machinery equipment — such as watertight closures, cargo/weapons elevators, embarkation equipment, cranes, boat handling equipment, and habitability — is an integral part of a U.S. Navy ship mission.
Whether moving ammunition or providing helicopter access, these systems must be fully operational when called upon. In addition, they must be safe to operate, maintainable by the ship crew, and affordable to the Navy throughout the equipment lifecycle.
Hull and deck machinery equipment is a responsibility of the Naval Surface Warfare Center, Carderock Division (NSWCCD) in Philadelphia, Pa. NSWCCD is an engineering field activity under the Naval Sea Systems Command (NAVSEA). In this capacity, they provide research and development, test and evaluation, fleet support, and in-service engineering for surface and undersea vehicle hull, mechanical, and electrical (HM&E) systems, and propulsors. In addition to the U.S. Navy, support is also provided to the Maritime Administration and maritime industry.
Ralph Tursi. mechanical engineer, supervises the mechanical computeraided Engineering (MCAE) section of the NSWCCD Hull and Deck Machinery Department. His team plays a vital role in the design of this equipment for new construction ships, as well as design improvements for in-service craft. In this role, Tursi and his team are faced with several engineering challenges.
Says Tursi. "First, we must take into account that the shipboard environment is typically harsh and promotes corrosion. As a result, we must ensure that shipboard designs are reliable and able to withstand the unique elements encountered onboard ship." Other important design considerations exist for Navy shipboard equipment.
Tursi explains, "In today's 21st century Navy, our ships feature an elite, highly trained, professional crew. These crews must rely on extensive automation. The ship and crew need to focus on the mission at hand, with less time available to devote to equipment maintenance. In addition, the demographics of the typical Navy crew have changed, with significantly more women than in the past.
As a result, habitability design specifications must also accommodate the female population. We must incorporate these human factors into our designs accordingly." Since ships are fighting machines, the equipment must withstand military requirements. Tursi adds, "This is an important distinction between Navy and commercial vessels. The commercial industry is certainly driving many of the latest technological innovations. As a result, the Navy typically looks to indus- try for technologically advanced products and equipment. However, these products in many cases necessitate modifications to withstand military requirements. This issue can make designing our equipment very challenging." The U.S. Navy is just as demanding as any civilian or commercial customer. Says Tursi. "It is imperative that shipboard equipment be safe, reliable, and affordable throughout the life of the ship.
Our primary mission as a NAVSEA activity is to support the Naval fleet. If we cannot accomplish this, the Navy will find someone else who can." Tursi and his team extensively utilize MCAE software to help them meet their objectives and customer expectations. "We use a variety of MCAE tools, such as 3D modeling, finite element analysis, and mechanical systems simulation software.
Mechanical systems simulation software is probably one of our most important MCAE tools." says Tursi, "and for this we utilize the Adams product from Mechanical Dynamics, Inc. (Ann Arbor.
Mich.)" Tursi's team implements Adams as both a conceptual tool and design tool. "The software allows us to demonstrate to our sponsor what a new design will look like as an end-product. Once we obtain their approval, we use the same conceptualization models and apply engineering expertise. We model the design in a CAD software, download the geometry to a finite element analysis (FEA) program.
and then simulate the design in Adams to check it for real-world performance. Adams helps us conduct a complete design-for-manufacturability study prior to building any physical prototypes." As a conceptualization tool. Adams assists Tursi and his team in creating and visualizing new ideas.
"Working with Adams is a much more productive use of our time than trying to draw manually or with a 2D system. Adams enables us to conceptualize a design quickly. The software has been a real winner with that aspect of the design cycle. For us to be able to show a non-technical person not only what our designs will look like, but how they will perform are very important. The technology helps our customer better understand the equipment and designs that we will provide." Tursi likes the ability to expand Adams models. "We can transform our conceptual designs into real engineering models.
That process eliminates a lot of rework and time. We can quickly move from concepts to working models with real engineering information. The software facilitates engineering efficiency and productivity.
As a result, we have reduced our design cycles by at least 50 percent." Prior to implementing Adams, the team addressed new product designs manually. "We would typically develop 2D CAD sketches. Even when we migrated to 3D software to develop new designs." adds Tursi. "the process remained difficult because of the number of configurations we needed to show our customer. The 3D models were simply still shots.
However, with Adams as part of our toolkit, we now have the ability to show real-world equipment simulations. In addition, we are now armed with the powerful flexibility to change design configurations on the fly. We and our customers are very confident that we can develop and optimize the best possible designs." After implementing Adams for several projects, Tursi says the Navy realized the difference in his department's ability to address new product design requirements in a much more expedient manner.
Other stories from October 2000 issue
Content
- Danish Two-Stroke Bastion page: 8
- Powering-Up the Finnish Range page: 10
- Marine Employment Resource Debuts page: 13
- From E-Biz to E-Bust: Is Online Chartering and Sale and Purchase Possible? page: 15
- MaritimeDirect Strengthens Its E-Commerce Team page: 16
- Maritime Records and Contracts: Electronically Signed, Sealed, Delivered and Maintained? page: 17
- Maritime Industry Mourns Congressman Bateman page: 24
- BP Takes Three DH Tankers From NASSCO page: 26
- New Technology on Display at Fish Expo I WorkBoat Atlantic page: 27
- South America Gets "Kit" Traelers page: 27
- SSPC Reaches Half-Century Mark page: 29
- New Hempel Coatings Meets Future Requirements page: 31
- Ohio Innovator page: 34
- Corrosion Control Electronically page: 34
- Improving Fuel Efficiency and Maintenance Time Within The Chevron Fleet page: 36
- Litton Avondale Holds Keel Laying Ceremony page: 37
- The Abandoned Shipwreck Act: Useful Tool for Historic Preservation or Paper Tiger? page: 38
- FGH Receives $52 Million Worth Of Orders page: 42
- A Helping Hand In Stralsund page: 43
- SWM Uses Automation To Speed Workflow page: 44
- ShipRepair & Conversion Is A Maritime Exclusive page: 47
- Cammell Laird, Cascade General Enter Agreement page: 48
- Millennium's Vibration Problem Not Related To Gas Turbines page: 50
- On The Waterfront With NNS' Director Of Ship Repair page: 52
- AMHS Ferry Visits Bellingham Bay Shipyard page: 53
- Toftejorg Features Cleaning Concept For Mud Tanks page: 54
- Fleetguard's Centriguard Reduces Emissions page: 54
- Near Miss Caused By Deficient Air Pipes page: 57
- After 25 Years, Smit International Keeps Evolving page: 58
- Atlantic Marine Keeps Docks Working page: 60
- H&W Gets Its $31M From Global Marine page: 60
- National Safety Council To Hold Workshops page: 61
- Good Luck Chartering The "Rust Bucket of the Month" page: 62
- Eyes Onboard page: 62
- Subsea Installation, Heavy Lift And Transport Vessels Show Muscle In FPSO Market page: 64
- Great Lakes' Biggest Dual-Mode ITB Begins Service page: 65
- Hike Metal Constructs Boat For Pilotage Authority page: 65
- Kvichak Delivers To Pilots Association page: 66
- Gladding-Hearn Delivers First Of Two To Charleston Pilots page: 70
- Bollinger To Construct Supply Boat For Lytal Ocean page: 71
- Latest Developments in Engine Room Simulators page: 74
- U.S. Navy Keeps Ship-Shape With Software page: 76
- OSL, Philadelphia Gear Form Alliance page: 79