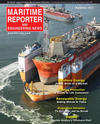
CFD to Assess SSP’s Crew Boat Docking Tunnel
MARIN combined CFD with fast-time simulations and intensive testing on its bridge simulator to explore the full potential of the new SSP HUB.
To save on costly helicopter crew transport, SSP Offshore took a good look at its SSP Plus design and decided to add a large crew boat docking tunnel, running straight through the center of the big round floater. The tunnel allows fast sailing crew boats to dock inside the HUB, thereby cutting out helicopter transfers. MARIN was put to work testing the HUB design to make sure a safe crew boat entry into the unit was possible under extreme operational conditions. A multi-stage campaign was required, ranging from CFD calculations to determine the complex interaction of the HUB’s exceptional design with the environment, to intensive simulation exercises on the bridge simulator with experts from SSP, Austal and MARIN.
To be located offshore Brazil, the SSP HUB features an omni-directional shape and the ability to rotate, thereby redirecting its tunnel position depending on the environmental conditions. If beneficial, the tunnel can be closed by weather tight doors on the wave-ward side of the unit.
Safe Crew Bboat Entry
One of the key questions SSP needed answering was whether the HUB was able to accommodate safe crew boat entry in the harsh environmental conditions of the Santos Basin. For this, the unique design of the shallow docking tunnel running through the floater could be a determining factor. Waves typically change their height, length and direction when travelling over a sudden transition from deep to shallow water, and could thereby hamper the crew boat pilot during entry into the tunnel. Current and wind travelling around the HUB, and possibly through the tunnel, could further restrict the approach and docking operation. By using a combination of CFD tools, MARIN set out to study the complex wave, wind and current flow phenomena that occur around the entrance of the HUB tunnel. As these flows are driven by non-linear effects, conventional linear potential flow tools are simply not capable of capturing the flow details with enough accuracy.
Environmental Conditions
Wind and current velocities inside and outside the HUB were computed using ReFRESCO, for both a completely open tunnel and a tunnel that was closed on the side affected by the environment. For a range of environmental conditions flow fields could be visualized in detail and showed recirculation, shielding and intensification zones. The results will allow SSP to anticipate environmental directions, for which the CFD predicted strong cross flows at the entrance of the tunnel, by using the rotating capabilities of HUB.
To get a better understanding of the wave patterns inside the docking tunnel, unsteady wave simulations were performed using ComFLOW. Special attention was paid to possible resonant wave modes inside the tunnel. The results of the CFD provided SSP with critical wave amplification factors inside the tunnel, together with the environmental conditions for which these amplifications occur. With this knowledge, SSP can set criteria for redirecting the HUB, using the weather tight tunnel doors and possibly other mitigation means to avoid large water motions inside the tunnel.
Simulation Study
To provide SSP with the answers it is looking for, the knowledge obtained from the CFD simulations were only half of the equation. The capabilities of the Austal Trimaran crew boat and captain also had to be taken into account. To that end, a realistic and fast-time simulation model of the HUB, environment and crew boat was developed and put to the test on MARIN’s bridge simulator. To achieve realistic simulation exercises, the environmental conditions on the simulator were tuned using the CFD simulations and a detailed model of the interior of the tunnel was made including moveable fenders that guide the vessel into the tunnel. An accurate maneuvering model of the trimaran was created in cooperation with Austal. With the use of the CFD results the HUB’s rotational capabilities and weather tight doors were exploited to the maximum to create the optimum entry condition for any given environment.
In the end, a week of extensive simulations found that the SSP HUB was indeed able to accommodate a safe entry in the harshest environments – a conclusion made possible by a unique combination of CFD analysis, real-time simulations and comprehensive simulator exercise.
The Author
Joop Helder is Project Manager of the Offshore Department of MARIN. MARIN offers simulation, model testing, full-scale measurements and training programs, to the shipbuilding and offshore industry and governments.
e. [email protected]
w. www.marin.nl
(As published in the September 2015 edition of Maritime Reporter & Engineering News - http://magazines.marinelink.com/Magazines/MaritimeReporter)
Read CFD to Assess SSP’s Crew Boat Docking Tunnel in Pdf, Flash or Html5 edition of September 2015 Maritime Reporter
Other stories from September 2015 issue
Content
- United Technologies: Joint Maritime Approach page: 12
- CFD to Assess SSP’s Crew Boat Docking Tunnel page: 14
- Sleep Apnea page: 16
- Riding Waves & Tides to a Cleaner Energy Future page: 18
- To Scrub, or Not to Scrub -That Is the Question page: 20
- 'Blue' Economy Ocean Industries & the Next 50 Years page: 24
- Keeping a Watchful Eye page: 26
- Monitoring for Efficiency, Safety page: 28
- GOST Marine Security Video Recording Device page: 28
- VOOPS: Venice Offshore Onshore Port System page: 32
- FLNG Birth of a Market page: 36
- FPSO Guide to Life Extension page: 42
- Company Profile: Offshore Inland page: 48
- Spanish Maritime Industry Prospects page: 50
- Portugal: Searching for Lost Maritime Glory page: 52
- Ulstein Verft Launches its Largest Ship to Date page: 57
- Tactical Response Vessel Delivered to NYPD page: 57
- Mega Maritime: Heavy Lift for FPSOs page: 58
- Interlake Steamship to Install More Scrubbers page: 61
- Hybrid Propulsion for New Fairplay Tugs page: 61
- EMP Renewable Energy Battery Solution for Ships page: 62
- LNG Bunker Barge Concepts page: 63