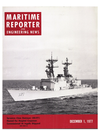
Series Production Of Aluminum LNG Spheres
In the fall of 1972 General Dynamics signed the first contracts in the United States for the construction of 125,000 cubic meter liquefied natural gas (LNG) carriers.
Subsequently, in 1973 and 1976, contracts for additional vessels were signed for a total of 12 ships.
This series of essentially duplicate vessels would require 60 identical 120-foot-diameter aluminum cargo containment spheres, five for each ship, to be manufactured at the rate of 20 spheres per year. In order to achieve this production and, at the same time, maximize the rate of ship deliveries, it was necessary to make the most efficient use of resources. A plan was t h e r e f o r e developed whereby the ships would be constructed by experienced shipbuilders while the spheres would be built simultaneously, but offsite by an experienced sphere builder, then transported by barge to the shipyard and loaded into the completed hull.
This concept required extensive modernization of the shipyard.
An automated standard parts fabrication shop, two 875 by 150-foot building basins and a 1,200-ton Goliath crane for loading of the spheres into the ships and handling ship modules were installed.
Concurrent with the modernization of the shipyard facilities, a sphere subcontractor was selected and Charleston, S.C., was chosen as the manufacturing site.
The sphere subcontractor began facility work in 1973, with production scheduled to begin in 1974.
By September 1974 it became evident that the subcontractor would be unable to meet contractural requirements.
The shipyard therefore freed itself of relationships with the subcontractor by assuming the responsibility for building the spheres.
During the last three months of 1974, the shipyard undertook an around-the-clock planning effort which also drew upon resources from other divisions of the corporation. This effort had three phases: (1) the definition and evaluation of alternative *Mr. Veliotis, president and general manager of Genera! Dynamics, Quincy (Mass.) Shipbuilding Division, at the time of writing this paper, is now general manager of the General Dynamics' Electric Boat Division. He presented the paper abstracted here before the recent Annual Meeting of The Society of Naval Architects and Marine Engineers. The complete paper may be obtained from the Society, One World Trade Center, Suite 1369, New York, N.Y. 10048 methods to obtain LNG spheres; (2) selection and concurrent development of the manufacturing process and facility requirement for those alternative methods having the highest potential for success and cost effectiveness, and (3) final selection and implementation of the optimum method to obtain LNG spheres.
Criteria for evaluation included: (1) capital investment required; (2) high confidence that the selected manufacturing plan would work; (3) flexibility in production process; (4) e a r l i e s t and most rapid rate of sphere deliveries, and (5) acceptable risk.
Against these criteria, the following possible alternatives were evaluated: (1) build spheres at the Charleston site; (2) build spheres at a new site; (3) build spheres at a new facility contiguous to the shipyard; (4) build spheres in the ship, and (5) select another subcontractor to build spheres at the Charleston site or at a new facility.
This evaluation indicated that the shipyard could build spheres either at Charleston or at a new site at a rate equal to or faster than the original sphere subcontractor with a higher confidence in obtaining scheduled deliveries.
With this knowledge in hand, various alternatives were pursued in parallel: (1) the detailed development of two different manufacturing plans — the segment concept and the rigid fixture concept, Figure 1; (2) the acquisition of alternative manufacturing sites, and (3) exploratory negotiations with other sphere subcontractors.
In parallel with exploratory negotiations with other sphere subcontractors, the shipyard developed two alternative manufacturing plans. Investigation of two different manufacturing plans, the segment concept and the rigid fixture concept, stemmed from observing problems encountered by the sphere subcontractor in attaining the required degree of sphericity and acceptable welds.
The weld problems experienced were primarily the result of poor fitup and welding in an open environment exposed to contaminating elements of nature — dust, wind, and moisture.
The basic problem of repeated poor fitup was determined to result from parts not manufactured repetitively to rigorously controlled dimensional tolerances.
When traced to the cause, poor fitup was found to result from inadequate design of tooling and fixtures.
This detailed technical evaluation established the specific criteria around which a manufacturing plan would have to be developed, namely: (1) each of the spheres must be repetitively produced to strict dimensional tolerances; (2) each fixture used in the production process must be capable of achieving and maintaining rigorous dimensional tolerances, and (3) all welding must take place in a weather-protected environment.
With these principles defined, the details of the two different manufacturing concepts were developed.
The first, a segment concept, envisioned the sphere being sliced horizontally into five or six circular sections. These sections would be fabricated from plates and welded together into 360-degree rings. Final assembly would take place by stacking and welding sections together. From the bottom of the sphere, each succeeding ring would be placed on top to the next until the sphere was complete. Alternatively, each of the two hemispheres would be assembled from three rings with one hemisphere lifted on top of the other.
The second plan also envisioned the sphere being sliced into five sections, but being assembled downward and then upward from the equatorial ring by loading two or four plate subassemblies in one sphere assembly fixture.
Each element of the two alternative production processes was then broken down, and the technical requirements and tooling fixtures required to manufacture the parts, subassemblies and major assemblies defined. Each element was then analyzed from an industrial engineering standpoint to determine cycle times, labor manning requirements and the number of sphere assembly stations needed to meet schedule requirements.
These requirements were then translated into facili facilities definition and lead times for construction.
The two manufacturing plans competed against each other and against proposals received from other sphere subcontractors. Proposals from sphere subcontractors ultimately were rejected because their manufacturing plans were insufficiently detailed to generate necessary confidence in the workability of their manufacturing processes or because they required excessive time to complete planning and facility construction.
The segment construction alternative also was rejected.
The single rigid-fixture equatorial ring assembly concept was selected so the entire sphere could be assembled prior to welding.
Thus, welding fits and sphericity tolerances could be verified early in production and corrected easily where necessary.
Testing Trans-lifts walk the tank from the assembly hall into the cylindrical hydropneumatic test stand, which consists of one fixed segment and two hinged segments that swing open to receive the tank. The weight of the gates during opening and closing is borne by air bearings sliding on level tracks. After the gates have been closed and bolted, the tank is landed on an elastic foundation that equalizes the reaction into the column and beam structure.
The cargo-tank transport ring is then lowered so that the tank is supported by its skirt.
Tank Insulation The final fabrication operation at the sphere manufacturing facility is insulating the spheres.
Like sphere construction, the insulating process requires a specially designed facility to apply and secure the one acre of insulation and complete the sealing cycle in 2.5 weeks to meld with the sphere production rate.
A single sphere is transported into the insulation building and placed on a uniquely designed stand where it will remain for the complete i n s u l a t i o n cycle.
The stand supports the sphere's weight and provides as well the facility for sphere rotation which minimizes access requirements during insulation installation.
Once the sphere is seated and the transport equipment is removed, the insulation process commences.
Land Transport Three different methods were evaluated for transporting the cargo tanks from the assembly building to the hydropneumatic test stand, to the insulation building and then to the barge. The Trans-lift system selected was shown to be more flexible and economical—in terms of the initial investment and the recurring costs—than crawler or rail-bogie transport.
The transport system consists of three Hydranautic's Trans-lift units, each of 335-ton capacity, and a sphere support ring of 70- foot outside diameter. The three Trans-lift units operate in unison, all receiving the same hydraulic pressure and the same electrical commands from a single operator controlling through a remote pendant control. The speed of travel is one foot-per-minute up or down a two-percent grade in 40-mph winds. Motion can be forward, backward or sideward. Each unit can be rotated independently to change direction, or all three can be made to move together in a circle, thus rotating the tank about its polar axis. The Translift units move and position the tank by "walking," using the principle of repeatedly sliding the load along a prepared surface on the center foot, and then with the load transferred to the side feet, the center foot is raised and advanced 27 inches in the direction of travel. Thus, the tanks can be moved over a variety of surfaces without a permanent track system and without external traction forces from ground-anchored members.
Barge Transportation The spherical aluminum tanks are transported from the building facility, 22 nautical miles up the Cooper River from Charleston to the shipyard at Quincy, Mass., on the special-purpose, unmanned towed barge Hercules, which was designed and constructed at Quincy.
The barge is towed on a wire hawser by a twin-screw tug of at least 4,300 hp. During the winter months the route parallels the coastline from the Charleston sea buoy to Diamond Shoals, then north to abeam Cape Henry, then north-northeast to south of Block Island, then through Vineyard and Nantucket Sounds and around Cape Cod to the shipyard.
At the time of writing, five loaded voyages have been completed during the winter months at an average speed of 9.5 knots.
According to the Moran Towing and Transportation Co., Inc. personnel, towing behavior has been excellent.
Sphere Loading Upon arrival at Quincy, Hercules is maneuvered into the outboard end of the shipyard's No. 6 basin, modified with a new watertight bulkhead to accommodate the barge in an area 297 by 132 feet. The sphere is unfastened from its support structure and the basin is drained until Hercules rests on nine concrete slabs, each measuring 14 by 12 by 8 feet.
After 55-ton tests are conducted on each of the sphere's 18 aluminum lift pads, permanently attached as part of the skirt, actual transfer from the barge to a hull under construction in an adjoining basin begins. Utilizing three hooks and specialized lifting gear consisting of trusses, equalizer bars and 18 wire-rope pendants attached to the lift pads, the Goliath crane, designed by Vevey- Mague, lifts the sphere straight up from the Hercules. Movements as minimal as Vt inch are governed by the crane operator with both computer and manual controls.
The sphere is lowered against wood-faced guide brackets and loaded into the deck opening with clearances of only 4 to 12 inches. Exact dimensional measurements of each sphere skirt are sent from Charleston to Quincy prior to sphere arrival and are used to determine circumference profile to the steel skirt in the hold to achieve proper alignment.
Transfer of the 676-metric-ton sphere from the barge to the ship takes approximately three hours.
With the sphere's aluminum skirt resting on the matching steel skirt in the ship, the wire-rope pendants are disconnected from the lift pads and the final welding process begins, lasting 24 to 36 hours. The operation is completed when a 258-metric-ton prefabricated steel cover is lowered over the sphere by the Goliath crane.
Read Series Production Of Aluminum LNG Spheres in Pdf, Flash or Html5 edition of December 1977 Maritime Reporter
Other stories from December 1977 issue
Content
- Mar Ad Approves Sale Of Tuna Boats To Foreign Companies page: 4
- Eisenbiegler And Rippy Named Presidents Of Two Sun Subsidiaries page: 6
- James S. Byrn Named President Genstar Marine page: 7
- MarAd Contract Let For Development Of Standardized Carrier page: 7
- Bethlehem Steel Sparrows Point Lays Keel For $78-Million Farrell Lines Containership page: 8
- Navy Commissions Ninth Of 30 Destroyers Being Built By Ingalls Shipbuilding page: 8
- SNAME Completes Boiler Safety Report page: 10
- Raytheon Names Millard Commercial Marine Marketing Manager page: 10
- Charles Murphy Receives Halert C. Shepheard Award For Merchant Marine Safety page: 13
- Program Outlined For Annual Conference On Marine Coatings page: 14
- State Boat Awards Contract To Blount For Offshore Supply Boats page: 15
- MarAd Releases Two-Volume Report Prepared By DeLaval page: 15
- SNAME Philadelphia Section Hears Paper On New Flexible Shipbuilding And Ship Repair Facility page: 16
- ARCTEC Canada Limited Opens Testing Facility And Ice Towing Basin page: 17
- Marine Equipment Suppliers Apply For Title XI To Build Self-Propelled Pipelay Ship page: 18
- Strict Liability And Its Impact On Marine Field Discussed By SNAME No. Calif. Section page: 18
- SNAME Pacific Northwest Section Holds Annual Meeting At Harrison Hot Springs, B.C. page: 20
- New Single Point Monitoring Salinity Control System page: 20
- Worthington Announces Management Positions In Marketing And Sales page: 21
- Rapifax Supplies U.S. Lines With Shipping Industry's First High-Speed Facsimile System page: 22
- Mississippi Marine Begins Offshore Boat Construction page: 23
- Series Production Of Aluminum LNG Spheres page: 24
- ICHCA Conference Set For Helsinki May 26-June 1, 1979 page: 26
- Comet Marine Named Marine Distributor By Crane Packing page: 26
- Oceangoing Towing Guidelines Issued By Det Norske Veritas page: 28
- Bird-Johnson Names Darby Sales Engineer For The Gulf Coast page: 28
- Perko Full Line Catalog Just Released page: 29
- Frankel Elected President Of IMODCO page: 30
- CADCOM, Inc. Appoints F. William Helming page: 30
- Seatrain Shipbuilding Appoints Hellenbrecht Chief Marine Engineer page: 31
- ASNE Reports Details Of Recent Symposium On Combat Systems page: 38
- Combustion Engineering Names Robert Fortier page: 38
- Tenneco's Newport News Industrial Corp. (NNI) Appoints M.R. Eshelman page: 41
- Southeast Shipyard Association Elects Fitzgerald President page: 41
- Belcher Tugs To Use Burmeister & Wain Slow Speed Diesels page: 42
- Three Papers Presented At SNAME California Sections Annual Joint Meeting page: 43
- UNITOR Ships Service Holds Dedication Ceremony To Mark Opening Of Facilities In New Jersey page: 44
- Magnus Maritec Names Three To Sales Posts page: 44
- Zapata In Joint Fishing Venture In Costa Rica page: 45
- Sun Ship Forms New Estimating Department —Brawner Named Manager page: 46
- Barney Evans Opens Public Relations Firm page: 47
- Thistle Field Drilling Started By Santa Fe page: 47
- IMODCO Wins Petrobras Contract To Install SPM At Record Depth page: 47
- Second Generation LNG Carriers Subject Of Paper Presented At ASNE Pascagoula Section Meeting page: 49
- Great Lakes/Great Rivers Section Hears Three Technical Papers During Fall Meeting In Ann Arbor page: 52
- Union Mechling's Application For Aid To Build 58 Barges Approved In Principle By MarAd page: 52