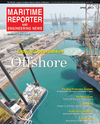
Making Flare Gas Useful
Wärtsilä has developed the GasReformer, a product which converts associated gas, which is often flared, into usable fuel for its dual-fuel engines.
When producing oil, associated gas is also released from the deposits. In many places this gas is commonly burnt off in gas flares, a waste of energy and a pollutant of the atmosphere. In addition to useful methane, this gas consists of heavier hydrocarbons including ethane, propane and butane. The composition of the gas typically also vary during the production phase of the oil field. This gas cannot directly be used as fuel in the cylinder of an engine, as it causes knocking or uncontrolled ignition. To make the gas a useful product, the Methane Number of the gas has to be raised through elimination of harmful gas components.
In December 2012 Wärtsilä delivered its first GasReformer, a new product the company is claiming can help convert associated gas into usable fuel for dual fuel engines. The size of a container, the unit will be used toconvert the associated gas on a fixed drilling and production platform, specifically one which is projected to operate in South China Sea. A Chinese operator together with Newfield Exploration of the U.S. will operate the platform under a production sharing contract. The platform is currently under construction at the COOEC shipyard in Qingdao, China, and there it will be fitted with eight-cylinder Wärtsilä 34 in-line engines, two of them as dual-fuel (DF) versions, to generate electricity for the platform.
“One main potential of the GasReformer is in offshore applications, in oil fields where the associated gas composition vary much or where the methane number is below 60,” says Mr Peik Jansson, Product manager of the GasReformer at Wärtsilä Ship Power. He explained that when the number is above this, the gas can be used but the engine has typically to be de-rated down to 75% to 80% to lower cylinder compression. This also results in lower efficiency of the process. The methane number indicates how much compression the gas can take before knocking. “With the GasReformer, we convert, through a catalytic process, the heavier hydrocarbons in the gas into methane, carbon oxide and hydrogen. This raises the methane number to approximately 100, and the gas can be used as fuel in fully rated Wärtsilä dual-fuel engines.”
When the methane number is below 60, it is cost-efficient to invest in a GasReformer. With increasing environmental regulations flaring is prohibited and the associated gas has to be disposed of by other means. “Why not use it as fuel for power production,” Jansson asks, and notes that associated gas can, as such, be used as fuel for gas or steam turbines. “A Wärtsilä GasReformer fueling a Wärtsilä power plant provides high efficiency and above all, full flexibility in power output.” With an 8 MW Wärtsilä GasReformer combined with a dual-fuel engine, utilizing associated gas, the operator can reduce the need for bunkered fuel oil by about 20 tons per day.
How does it work?
The process of the GasReformer is based on steam reforming, but is here done somewhat differently. “The goal is to produce as much methane in the process as possible. This application is entirely new,” Jansson said. All heavier hydrocarbons, and also the methane, are cracked to an intermediate product which is hydrogen and carbon monoxide. Into the catalyst is fed the gas and steam. Through a reaction in the catalyst process, which is a function of temperature, pressure, and the amount of steam injected, gas is achieved which consists of 80% or more methane, less than 11% hydrogen and some 10% or less carbon dioxide. “In the process, almost regardless of the composition of the input gas, this is the resulting composition,” he notes. The catalyst is a pressure vessel with pellets of reduced nickel.
In the process, the associated gas passes through a de-sulphurization reactor and is injected into the Reformer. The output gas is then fed into the engine. The engine controls the gas flow automatically and steam produced by the exhaust gas boiler of the engine is fed into the process based on need. The reactions of the process are very fast. “There are other technologies which filtrate the heavier hydrocarbons from the gas, but you then have to get rid of these separately,” Jansson said.
Jansson shows a real-case example (Fig. 1, previous page) where the inlet gas composition has the methane number 56 as it includes heavier hydrocarbons although as much as 78% methane. After the GasReformer, the composition is 79% methane, 10% hydrogen, 10% carbon dioxide but there are no heavier hydrocarbons. The methane number has increased to 98.
Wärtsilä started developing the GasReformer seven years ago. A prototype of the Gas Reformer was built, as a proof of concept.
“It could, for example, turn 100% propane into methane,” Jansson said. The product was then industrialized, which included the entire process of adding safety systems, etc., and the classification and approvals. In December 2012 the first GasReformer unit was delivered, after successful factory acceptance tests at Wärtsilä’s factory in Finland. The GasReformer is classified to the Offshore regulations by Det Norske Veritas. The platform will receive four 8-cylinder Wärtsilä 34 in-line diesel-generators, two of which will run on crude oil and two DF dual-fuel engines running on both crude oil and on gas as fuel. Flaring was not allowed by the authorities. “We have a difficult gas, a difficult crude oil, but Wärtsilä could provide the solution.”
The pellets in the reactor of the GasReformer have to be renewed every three to four years. This is done through replacing the entire reactor pressure vessel with a unit served ashore. Wärtsilä handles this process as part of the contract with the client. The GasReformer has two desulphurizer reactors, with one as backup. The lifetime of one unit, using zinc-oxide as adsorbent, is approximately one year of continuous operation. The units are replaced when needed.
The first produced GasReformer is a 8MW unit.
It needs a total of 1,775kg steam per hour. Of this amount 375kg fresh water is consumed per hour, in the reformed gas. 1,400kg is recycled into the process. The amount of fresh water needed in the process is a function of the methane number of the inlet gas.
In addition some cooling water is needed, hydrogen for start-ups and blow-downs or flushing, when needed, plus some electricity for operation, start-ups and when in stand-by (Fig. 2, next page).
With the GasReformer in the product portfolio Wärtsilä is capable of providing an extensive system for handling associated gas for the oil industry. It can supply the entire power production technology and through the aquisition of Hamworthy, also inert gas systems, and systems for flare gas recovery and flare gas ignition.
Potential also for VOC recovery and in shale gas operations
VOC, or Volatile Organic Compounds, recovered in the process of crude oil handling provides another potential use of the GasReformer. In crude oil pumping and handling, the crude oil is heated to improve its viscosity. When heating, the lighter hydrocarbon fractions of the crude evaporate. These volatile organic compounds (VOCs) are traditionally vented into the atmosphere. “Now, VOCs can also be utilized by combining a VOC Recovery System with Wärtsilä GasReformer and dual-fuel engines,” Jansson said. Through Hamworthy, Wärtsilä also provides VOC Recovery Systems. Jansson presented some calculations to Maritime Reporter where a Floating Storage Unit could receive all of the fuel needed for powering the cargo pumps from VOC gas, by installing a system onboard combining these two technologies.
“There are many potential application for the GasReformer also in land-based applications. So far we have concentrated on the offshore oil industry,” Jansson said.
“A wider use of Liquefied Petroleum Gas, which is propane or butane, as fuel is now also possible. Another potential sector could be in shale gas recovery, where a power plant is easily set up using the GasReformer.”
The GasReformer is not suitable to be used for bio-gases nor gases with high amounts of sulfur, above 40ppm. Nor does it suit for processing gases with high amount of inert gases, nitrogen or carbon dioxide nor for gases including so called olefins. Wärtsilä’s GasReformer is a completely new product, now ready for the market. The size of a GasReformer for an engine shaft power of 8MW is designed to be 5.3m long, 3m wide and 3.3m high. The weight of the unit is approximately 17 tons.
(As published in the April 2013 edition of Maritime Reporter & Engineering News - www.marinelink.com)
Read Making Flare Gas Useful in Pdf, Flash or Html5 edition of April 2013 Maritime Reporter
Other stories from April 2013 issue
Content
- The Glass Half Full page: 6
- Salvage Response under OPA 90: Non-Tankers are Next page: 10
- Does Chapter 11 Work for Foreign Shipping Companies? page: 18
- Understanding the Ups and Downs of Insurance page: 22
- A Call for Transportation Management Upgrades page: 26
- Keeping Marine Projects Afloat page: 29
- Floating Production Systems to Grow 40% in Five Years page: 32
- Making Flare Gas Useful page: 34
- Underwater Robotic Championship page: 44
- 3D Body Scanning page: 46
- WSS’ Global Quest page: 48
- Dredging India page: 50
- Markey’s Mark on the Deck Machinery page: 54
- Nor Crane Powers Ahead page: 56
- Keeping Maritime and Offshore Cranes Ship Shape page: 58
- CIMAC Set for Shanghai page: 62
- Dead in the Water page: 64