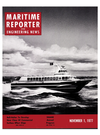
Kaiser Building Fifteen Mammoth All-Welded Aluminum LNG Tanks For Ships At Avondale
series of huge aluminum tanks nearing completion in Mobile, Ala., soon will be playing a significant role in helping the nation meet its energy requirements.
The 15 mammoth all-welded containers are being assembled by Kaiser Aluminum & Chemical Corporation on nearby Pinto Island for eventual use in three liquefied natural gas (LNG) ships under construction at Avondale Shipyards in New Orleans, La.
The 125,000-cubic-meter ships will be operated by subsidiaries of El Paso Natural Gas Company to transport natural gas at cryogenic temperatures (minus 260 degrees F) from gas fields in Algeria to East Coast markets.
The multimillion-dollar project is the largest of its type in LNG history, and the tanks are the first of their design ever built in this country.
The tank dimensions are impressive.
They are being assembled in sets of five, and vary in size and configuration depending on where they will be placed. The largest are the three that will be in the center of the ship, with each approximately 120 feet long, 120 feet wide, and 75 feet high.
More than 27 million pounds of Kaiser-developed 5083 aluminum plate, extrusions, and forgings are being used in the tank project.
Aluminum plate up to 1% inches in thickness is provided by the company's Ravenswood, W. Va., Works. Extrusions are from Kaiser Aluminum's Halethorpe, Md., plant; forgings from Erie, Pa., Works; and the total welding wire requirements of some 500,000 pounds are being supplied by the company's Newark, Ohio, Works.
The largest of the Conch-design rectangular containers weighs approximately 950 tons, while the smaller ones weigh approximately 700 tons. They are being assembled at ground level and will be lifted into place in the ships by a huge twin-boom derrick which has been specially constructed for the purpose at the Mobile site.
The first tank is scheduled for lift in approximately 30 days, according to T.H. Johnson, Kaiser Aluminum LNG project manager, and the ships are expected to be completed in 1978.
The tank fabrication itself is a two-step process. Individual component panels were assembled at a plant in Wilmington, N.C., using sophisticated processing equipment and automated welding techniques.
The subassembly panels, which weighed up to 60 tons each, then were transported to Mobile by a large oceangoing barge. The barge had a capability of carrying all 24 panels needed for one finished tank, plus the smaller brackets and parts.
Upon arrival in Mobile, the panels are assembled into a tank much the same as a ship is built, with subassembly fitting and welding into place. Workmen then complete installation of all internal tank piping and instrumentation.
Kaiser Aluminum developed special welding procedures for the project, with particular emphasis on quality control. All automatic butt welds undergo X-ray and tensile testing to insure that requirements are met, and stringent inspection is followed on all manual weld operations.
When the tanks are finished, they are transported into position for eventual placement aboard ship by specially designed crawlers.
Four of the 300-ton-capacity diesel-powered vehicles are used, one under each corner of the individual tanks.
While the aluminum containers are being fabricated in Mobile, Kaiser Aluminum also is insulating the three LNG ships at Avondale Shipyards. The company is the prime contractor for installation of a special polyurethane foam system in the holds of the carriers.
The insulation is a combination of balsa wood corners and tank support piers, nylon mesh reinforced polyurethane foam, and fiberglass. Although not in the insulation contracting business, Kaiser Aluminum developed the special cryogenic foam and perfected the procedures to install it in the LNG ships. In addition to its insulating characteristics, the system has been designed as a secondary liquefied natural gas barrier, with built-in structural support for the cargo tanks.
Quality control and testing procedures on the projects are continuous and exceedingly strict.
At Mobile, not only is there a stringent Kaiser Aluminum inspection program in operation, but one by the Coast Guard and by the American Bureau of Shipping as well. All shell welds undergo 100 percent X-ray inspection, and each finished tank is then hydrostatically tested to insure integrity of the container.
Hydrostatic testing procedures for the tanks were developed by Kaiser Aluminum, Conch, the Coast Guard, and the ABS. Each tank is more than half filled with water, which in the case of the larger tanks is approximately four million gallons, and then eight pounds of air pressure is placed on the surface of the water.
Testing and inspecting during the foaming operations at Avondale Shipyards and at the Wilmington plant are equally strict, not only by Kaiser Aluminum inspectors but also by the American Bureau of Shipping and the United States Coast Guard.
Read Kaiser Building Fifteen Mammoth All-Welded Aluminum LNG Tanks For Ships At Avondale in Pdf, Flash or Html5 edition of November 1977 Maritime Reporter
Other stories from November 1977 issue
Content
- New York Harbor Containership Terminals Described In Brochure page: 4
- ARINC Awarded $117,000 MarAd Study Contract page: 4
- NASSCO Awarded $174 Million To Build Destroyer Tender page: 7
- Great Lakes Studies Awards Total $400,000 page: 7
- Second $81-Million Gulf Oil Supertanker Christened At Bethlehem Sparrows Point page: 7
- Bell Aerospace And Halter Marine To Develop New Class Of Commercial Surface Effect Ships page: 8
- Interesting Paper And Past Chairman's Night Opens Season For SNAME New York Section page: 8
- Veliotis To Manage Electric Boat Div. page: 8
- Sun Shipbuilding Consolidates All Marketing Activities —Orth, Winstead And Hunt Named Department Heads page: 10
- Samson Ocean Systems Names John Williamson Regional Manager page: 10
- SNAME 85th Annual Meeting page: 11
- Hartzman To Retire- Bossier Slated For Avondale Presidency page: 11
- American Export Lines $43.1-Million Title XI Approved By MarAd page: 13
- Douglas Oehrlein Joins Dravo SteelShip Corp. page: 13
- McAllister Brothers Names Donald Hankin VP-Engineering page: 14
- Improving Shipbuilding Productivity page: 14
- Ocean Orders Five More Ships page: 14
- British Rail Awards Ferry Contract To Harland And Wolff page: 17
- M a r i n e Boiler Reliability page: 17
- Future Opportunities And Problems Of The Barge Industry page: 18
- Navy Awards Boeing $178 Million To Build Missile Firing Boats page: 19
- Plan To Convert Three Vessels At Estimated Cost Of $12.8 Million page: 20
- Kleschick Elected To Sun Ship Board Of Directors page: 20
- ASRY Drydock Now Open To Service 500,000-DWT Vessels page: 22
- NASSCO Elects Giorgis Group Vice President page: 22
- Norshipco Adopts New Corporate Logo page: 22
- Cayman Energy Ltd. Reports On Activities page: 22
- Samson Sells Marine Survey Division To Local Management page: 22
- Ed Toale Joins Bailey Sales Staff page: 23
- Marine Firms Attend Hoffert Marine Seminar page: 23
- Small Security Vessel Symposium Set For London March 6-10 page: 24
- Bethlehem Steel San Francisco Shipyard Names William Hamilton page: 24
- $3-Million Surface Effect Ship Award To Philadelphia Gear page: 24
- Jonathan Feffer Named President SSI Navigation page: 24
- Navy Adds $4.2 Million To Tracor Contract page: 26
- C.F. Bean Corp. Names Charles R. Barron VP page: 26
- Argo International And Sealol Join Forces page: 27
- Space-Age Insulation Approved By Lloyd's page: 27
- Sperry's First Triple Flow Steering Systems Installed At NASSCO page: 28
- Raytheon Promotes A. Newell Garden page: 28
- National Steel And Shipbuilding Delivers Second Of Four 90,000-Ton Tankers To OSG page: 28
- W.A. Whitney Corp. Introduces New 28XX Tooling Catalog page: 29
- Swan Hunter To Build Vessel To Transport Spent Nuclear Fuels page: 29
- Twenty-Four Women Report For Sea Duty To U.S. Coast Guard page: 32
- GE Credit Buys Third 225,000-DWT Tanker From Seatrain Shipbuilding page: 33
- New York Port Engineers Hears Paper On Surface Preparation Of Steel page: 34
- SCR Propulsion System For Offshore Tug/Supply Vessels page: 34
- Floating Oil Storage Better Prospects For The Unemployed? page: 34
- Alaska Maritime Names William Lorch Valdez Port Manager page: 36
- No. New England Section Of ASNE Reports On Two Technical Sessions page: 36
- An Assessment Of The Market For Tankers Of 300,000-DWT And Over page: 37
- Moran-Thibodeaux Names Captain North Vice President-Sales page: 38
- Diamond Manufacturing Building Ro/Ro Dock For Port Of Tampa page: 38
- Newport News Shipyard Installs Powerful Hoists page: 39
- Kawasaki Endows M.l.T. Research Fund With Gift Of $200,000 page: 39
- Kawasaki Kobe Works Delivers World's First BORO Liner page: 40
- Todd Shipyards Corp. Holds Company Safety Conference In Chicago page: 40
- Study 56—'Sea Trade And Transportation Of Coal' page: 41
- Spanish Society And ABS Enter Agreement page: 42
- J.M. Ringelberg Joins Seaward International page: 42
- U Of California Gives Course On Deepsea Oil Structures Jan. '78 page: 43
- Slatic Named President Ameron Protective Coatings Division page: 43
- Two Management Appointments Announced At Skagit Corporation page: 44
- IMO Pump Bulletin Describes Twin Screw Pumps page: 44
- Drew Chemical Corp. Promotes Walter Smith page: 46
- Kaiser Building Fifteen Mammoth All-Welded Aluminum LNG Tanks For Ships At Avondale page: 46
- New England Company Receives U.S. Funds To Investigate Giant Sphere As Offshore Oil Terminal page: 46
- SNAME And SSC Plan Ship Vibration Symposium For Washington, D.C. October 1978 page: 47
- Electro-Nav To Market New 400-Watt SSB Transmitter/Receiver page: 48
- CIBRO Petroleum Building Super Barge At Todd Shipyards' Houston, Texas Division page: 48
- Stanley Stiansen Elected By ABS page: 49
- OMNITHRUSTER Names J. Michael Melvin VP page: 49
- Santa Fe Reenters Onshore Drilling !n The United States page: 49
- New Henschel Engine Order Telegraph Catalogs Available page: 50
- ASNE Flagship Section Holds First 1977-78 Meeting page: 50
- Wigham Poland Inc. Expands Marine Insurance Division page: 50
- Dredge Technology Corp. Formed In New York page: 53
- Port Of Hueneme Retains John J. McMullen Associates To Prepare Master Plan page: 54
- IMODCO Establishes Houston, Texas Office —M.D. Jackson Named page: 56
- Los Angeles Section's Opening Meeting page: 62
- ALCO Brochure Reports Engine Performance On Residual Fuel page: 64
- American Arabian Partnership Names John S. Hollett page: 64
- Nicholas Liberatore To Head International Activities For Genstar page: 66
- ABS Classes 127 New Vessels In September page: 67
- Belle River Sets Tonnage Record On Great Lakes page: 68
- Congressman Mario Biaggi Will Address First N.Y.C. Diving-Insurance Symposium page: 71
- Miles O'Harra Enters The Consulting Field page: 72
- Clean Venture, Inc. Formed By Spill Contractors To Cover Entire New York Harbor Area page: 73